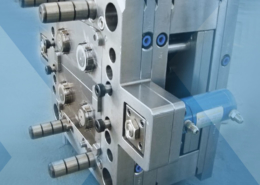
Point of Pivot: 3D Printing vs. Injection Molding - low cost plastic injection m
Author:gly Date: 2024-09-30
CompositesWorld’s CW Tech Days: Infrastructure event offers a series of expert presentations on composite materials, processes and applications that should and will be considered for use in the infrastructure and construction markets.
A report on the demand for hydrogen as an energy source and the role composites might play in the transport and storage of hydrogen.
The composite tubes white paper explores some of the considerations for specifying composite tubes, such as mechanical properties, maintenance requirements and more.
Thomas, B. P., Pillai, S. A., and Narayanamurthy, C. S. (2019). Photoelastic digital holographic polariscope. J. Mod. Opt. 66 (8), 817–828. doi:10.1080/09500340.2019.1575484
CW Tech Days are virtual events dedicated to the topics impacting the composites industry today. Access past event recordings and register for upcoming Tech Days.
Over the last 8 months, Archer Aviation has completed a total of 402 test flights with its composites-intensive aircraft, adding to key milestones.
FIGURE 3. The photoelastic image of one sample with the lines and fram for data collection (A), the gray value changing along the oblique line (B), the frequency of the gray values from 0 to 255 in the specific area of the blue frame (C), the gray value changing along the weft line (D) and the warp line (E).
An electrohydraulic hybrid injection molding machine (Model ZE1200, Ningbo Changfeiya Plastic Machinery Manufacturing Co., Ltd.) was utilized for the production of the PC goggles. Figure 1G shows the injection molding machine. To support the molding process, the following equipment was employed: a mold temperature controller (Model STM-910W) and a robot arm (Model ST3-700-1400-S) provided by Xinyi Electric Heating Machinery Co., Ltd., along with a dehumidifying dryer (Model SCD-40U/30H-OP).
This sidebar to CW’s August 2024 feature article reviews this technology for more efficient composites manufacturing and why it aligns with Koridion active core molding.
Initial demonstration in furniture shows properties two to nine times higher than plywood, OOA molding for uniquely shaped components.
However, photoelasticity has certain limitations, such as the requirement for relatively simple and plate-like part geometries for accurate stress analysis (Ajovalasit et al., 2015), and its applicability in manufacturing processes is challenging due to the need for specialized equipment, including a polarimeter with a rotation analyzer, circular scale apparatus, and compensator (Ajovalasit et al., 2015). The imperative to enhance product quality has compelled manufacturers to elevate the control level applied to both finished and semi-finished components, encompassing both qualitative and quantitative aspects. The adoption of digital image processing (DIP) emerges as an efficacious technique, not only augmenting the consistency and dependability of inspections but also enabling the extraction of valuable insights through DIP algorithms (Sasso et al., 2011). Furthermore, the utilization of DIP technology has the potential to substantially reduce the overall duration required for quality control, while simultaneously expanding the scope of inspected components. In instances where image acquisition and post-processing occur in real time, it becomes conceivable to exercise comprehensive control over the entire production process. Additionally, to address the limitations of traditional photoelasticity, the digital image correlation (DIC) technique offers a real-time, online experimental analysis method for stress analysis of transparent products (Zuo et al., 2022). By combining traditional holographic photoelasticity methods with DIC technology and rotating the polarization direction of the reference light, a digital holographic photoelasticity non-destructive testing method has been proposed for measuring residual stress in transparent regions (Thomas et al., 2019). However, the rotational process for measurements still incurs time costs, and accurately determining the residual stress in transparent parts with complex geometries using digital photoelasticity remains challenging. If the focus is shifted from precise residual stress measurement to quality assessment, a quick DIP method can be employed to verify part quality using a single photo without rotation. In this case, the complex stress optical law can be ignored, and data such as gray values and their variations can be directly utilized to determine part quality. This technique, termed digital photoelastic image correlation (PDIP), enables real-time monitoring of transparent parts with complex geometries.
Fig. 5: Proof of concept prototypes to test moldability of the RELAXED unit were made with CNC machined EPS foam tooling. Source: Cal Poly SLO
Thousands of people visit our Supplier Guide every day to source equipment and materials. Get in front of them with a free company profile.
Ajovalasit, A., Petrucci, G., and Scafidi, M. (2015). Photoelastic analysis of edge residual stresses in glass by the automated tint plate method. Exp. Tech. 39, 11–18. doi:10.1111/ext.12017
Cevotec, a tank manufacturer, Roth Composite Machinery and Cikoni, have undertaken a comprehensive project to explore and demonstrate the impact of dome reinforcements using FPP technology for composite tanks.
Table 2 displays the chosen outcomes from the numerical simulation for stress and warpage. The influence order of the five injection molding factors on the maximum residual stress of goggles was determined to be cooling time > melt temperature > packing time > injection velocity > mold temperature. Similarly, the order of influence on maximum warpage deformation of goggles was found to be melt temperature > injection velocity > cooling time > packing time > mold temperature. The order of influence of the factors on residual stress and warpage provides a valuable reference, but it is not an exact determinant due to variations in local residual stress and warpage, which are intricately linked to the cavity structure. Furthermore, the range of factor variations has a direct impact on the outcomes. The disparity in the influence order between residual stress and warpage suggests that the relationship between these two variables is non-linear. As the melt temperature increased, both residual stress and warpage deformation also increased. Conversely, increasing the injection velocity, packing time, and cooling time led to a decrease in residual stress and warpage deformation. The impact of mold temperature on these factors was not clearly discernible. This consistent trend in the influence of process parameter changes on residual stress and warpage deformation is attributed to the fact that warpage deformation is primarily caused by the release of internal residual stress within the product (Guevara-Morales and Figueroa-López, 2014).
Cabrinha also sees that RELAXED opens an expanse of new design opportunities via “the incredible aesthetic it achieves through complex geometry, and yet it is cost-effective, thanks to prefabrication and simple installation of one basic unit, repeated across the facade.”
FIGURE 12. Average gray values of the 64 samples in the specific area and along the weft and warp lines (A), correlation between the average gray values in the specific area and the average values along the weft line (B), correlation between the average gray values in the specific area and the average values along the warp line (C), DOE result of the average gray values in the specific area (D), DOE result of the average gray values along the weft line (E), and DOE result of the average gray values along the warp line (F).
Performing regular maintenance of the layup tool for successful sealing and release is required to reduce the risk of part adherence.
CompositesWorld's Carbon Fiber conference offers you cutting-edge information and access to industry experts in streamlining manufacturing costs, market outlooks and forecasting, and more. You will make invaluable contacts as you meet and network with the industry's most innovative and influential leaders at Carbon Fiber. __PRESENT
CompositesWorld’s Tech Days: Design, Simulation and Testing Technologies for Next-Gen Composite Structures is designed to provide a multi-perspective view of the state of the art in design, simulation, failure analysis, digital twins, virtual testing and virtual inspection.
Knowing the fundamentals for reading drawings — including master ply tables, ply definition diagrams and more — lays a foundation for proper composite design evaluation.
Increasingly, prototype and production-ready smart devices featuring thermoplastic composite cases and other components provide lightweight, optimized sustainable alternatives to metal.
Program will focus on sustainable, next-gen wing solutions, including in wing design and manufacturing and advancements in carbon fiber-reinforced composite materials.
CompositesWorld is the source for reliable news and information on what’s happening in fiber-reinforced composites manufacturing. About Us
Powered by an 85% air/15% pure polyimide aerogel, Blueshift’s novel material system protects structures during transient thermal events from -200°C to beyond 2400°C for rockets, battery boxes and more.
In North America, Europe, the Middle East and Down Under, architects and engineers are finding composites are a good fit in groundbreaking applications.
By comparing Figures 5, 12, it is evident that the change in residual stress follows a consistent pattern with the gray values observed within the specific area. Among the studied factors, melt temperature was found to have the most significant influence on both residual stress and the average gray value. To quantify the strength of the relationship between these variables, Pearson’s correlation coefficients were calculated and presented in Table 5. The correlation coefficient ranges from −1 to 1, indicating the strength and direction of the relationship between two variables. The correlation coefficients between the average gray value in the specific area and the average gray value along the weft and warp lines were consistently high. Similarly, the correlation coefficients between the maximum stress and the stress at the two probe positions were also significantly high. Moreover, the correlation coefficients between the photoelastic gray value and the simulated stress ranged from 0.676 to 0.785. These high correlation coefficients indicate a strong relationship between the photoelastic image analysis and the simulated residual stress of the samples. Furthermore, the experimental results align with the numerical simulation results, providing further validation. Consequently, this validates the use of instant shooting with a polarizer for real-time online monitoring of part quality. The gray value obtained within the specific area using the DIP technique can be employed to verify the residual stress of transparent parts. To simplify the process or reduce time, the gray value along a short line within the specific area can also be utilized for identification purposes.
Analyzing structural resonance of the aircraft under various loads becomes a critical step in obtaining flight certification.
While destructive methods like the hole drilling method have been employed for residual stress measurement, they are expensive, limit the reusability of parts, and are not suitable for small and complex components. The indentation method, a commonly used non-destructive testing method, has shown effectiveness in measuring residual stress in small-sized and complex geometries (Pak et al., 2013; Akahori et al., 2018). In comparison, the photoelasticity technique offers significant advantages for measuring residual stress in transparent polymer parts for practical applications. This non-destructive testing method enables the analysis of transparent or translucent plastic materials without altering their properties (Macías et al., 2015; Prasath et al., 2018). The ASTM D4093-95 standard describes photoelasticity as a method to determine residual stress by utilizing the effect of double refraction and measuring the direction of principal strains using a compensator (Macías et al., 2015). Transparent polymer materials exhibit photoelastic behavior, wherein the refractive index changes under load, resulting in stress birefringence. By employing a polarizer and subjecting the product to polarized light, an optical path difference is generated at points where residual stress is present. The magnitude and distribution of stress can be calculated using the stress optical law (Ghali et al., 2003; Ramesh and Sasikumar, 2020). Photoelasticity allows for the visualization and quantification of full-field residual stress distribution in injection-molded samples, enabling process monitoring, stress reduction, and improvement of part quality. Lu and Khim (2001) conducted experimental research to explore the impact of molding conditions on the surface contours of injection molded PC lenses. They employed a specialized polarimeter for measuring birefringence to assess residual stress within the lenses. The research approach incorporated statistical methods to systematically investigate how various process parameters influenced errors in lens contour. These contour errors were then correlated to both mold shrinkage and the presence of residual stress within the molded lenses. Macías et al. (2015) analyzed the residual stresses in PC cover lenses used in automotive. Their analysis utilized both photoelasticity and chemical attack methods considering the multiple characteristics of the plastic cover lenses, such as complex geometry, size and wall thickness. The findings contributed to the development of a technique aimed at alleviating stress in these PC cover lenses. Vargas-Isaza et al. (2023) delved into a comprehensive assessment of residual stress distribution in PC components manufactured under different molding conditions. They harnessed digital photoelasticity along with sophisticated computational algorithms to attain quantitative results. This approach allowed for a detailed understanding of how various molding conditions influenced the overall distribution of residual stress in PC parts.
Led by global and industry-wide sustainability goals, commercial interest in flax and hemp fiber-reinforced composites grows into higher-performance, higher-volume applications.
In these sessions, experts will discuss the emerging hydrogen economy and the opportunities for composites in this lucrative space.
Kim, B., and Min, J. (2017). Residual stress distributions and their influence on post-manufacturing deformation of injection-molded plastic parts. J. Mater. Process. Technol. 245, 215–226. doi:10.1016/j.jmatprotec.2017.02.015
Disclaimer: All claims expressed in this article are solely those of the authors and do not necessarily represent those of their affiliated organizations, or those of the publisher, the editors and the reviewers. Any product that may be evaluated in this article or claim that may be made by its manufacturer is not guaranteed or endorsed by the publisher.
FIGURE 4. Injection filling process of the numerical simulation (A) and the comparison of warpage values, distributions, and the experimental parts prepared by the processing conditions without and with DOE optimization (B).
Figure 1E showcases the CAD model of the cavity. Two probe positions were selected for analysis: one at the surface of the lenses and another near the gate, as depicted in Figure 1E. The stress and warpage values at these two probe positions were utilized for further analysis and discussion. Figure 1F illustrates the mesh model of the goggles. The process conditions outlined in Table 1 were implemented in the simulation. Through the DOE analysis, an optimized condition was identified for subsequent simulations, ultimately leading to the achievement of the final optimized result.
We acknowledge the software Moldex 3D 2022 support from CoreTech System Co., Ltd. The company was not involved in the study design, collection, analysis, interpretation of data, the writing of this article or the decision to submit it for publication.
Tasked by Kreysler & Associates (American Canyon, CA, US), Enclos (Eagan, MN, US), and Gensler Los Angeles (Los Angeles, CA, US) with rethinking conventional curtainwalll design, the Cal Poly San Luis Obispo Material Innovation Lab’s student design team developed the RELAXED concept with windows mounted perpendicular to the wall plane, to avoid heavy daytime solar exposure (see next image). Source: Cal Poly San Luis Obispo
Lu, X., and Khim, L. S. (2001). A statistical experimental study of the injection molding of optical lenses. J. Mater. Process. Technol. 113 (1-3), 189–195. doi:10.1016/s0924-0136(01)00606-9
Figure 8 presents the data obtained along the oblique line. Each group of the DOE samples consisted of four products, and the results demonstrate excellent repeatability. The observed wave patterns are associated with the photoelastic fringes, and the number of fringes can be easily determined by counting the peaks within each wave. The average fringe number was utilized for the DOE analysis. However, since the peak numbers were similar across the samples, the resulting DOE analysis did not reveal a clear pattern.
Peixoto, C., Valentim, P. T., Sousa, P. C., Dias, D., Araújo, C., Pereira, D., et al. (2022). Injection molding of high-precision optical lenses: a review. Precis. Eng. 76, 29–51. doi:10.1016/j.precisioneng.2022.02.002
Theoretically, the data collected from each set of process parameters designed for the experiment (1–16 sets) should be consistent. However, variations in overall brightness may occur due to lighting or focusing issues during stress fringe capture, leading to an overall increase or decrease in the average value. Additionally, there may be cropping defects during image processing, resulting in unconventional changes in data acquisition, which can lead to analysis errors. When the mean and variance values fall within a reasonable range, the sample data collection is considered acceptable. If the mean value experiences sudden jumps while the variance remains stable, it indicates an issue with the lighting during the capture process. In such cases, the capture can be repeated or replaced with data from a backup sample. When both the mean and variance fluctuate significantly, it suggests a problem with the specific sample, potentially caused by experimental equipment or other interference factors. In such instances, the problematic sample is discarded, and a backup sample is selected for data collection. Following the data acquisition, anti-interference measures, and data extraction, the mean and variance of the gray values are employed for analysis.
Polycarbonate (PC) pellets (model number: LEXANTM PC LS2-111, SABIC) with a density of 1.2 kg/m³ at room temperature and a melt flow index (MFI) of 11 g/10 min were selected for this study. The PC material exhibits a shrinkage of 0.5% in the machine direction (MD) and 0.7% in the transverse direction (TD). The PC material has a high transmittance of 88% and a refractive index of 1.581.
Six U.S. companies have proven their recycling technologies for composites and rare earth elements, and will be supported for relevant scale demonstration and validation.
Foundational research discusses the current carbon fiber recycling landscape in Utah, and evaluates potential strategies and policies that could enhance this sustainable practice in the region.
Curtainwalls are typically thin and made from aluminum frames called mullions, which support glass, metal and/or thin stone panels. Aluminum-framed curtainwalls are coming under fire, today, because aluminum, although lightweight, is highly conductive. It radiates summer heat into air-conditioned interiors and out of heated interior spaces in cold weather, significantly increasing energy costs. Further, aluminum itself is produced in an energy-intense process, and that affects a building’s overall LEED rating, a voluntary third-party certification that evaluates a building’s construction and operational sustainability (LEED ratings are awarded by the Leadership in Energy and Environmental Design (LEED) certification program. Read more about it here). “Now we start talking about significant improvement in thermal performance and CO2 footprint because aluminum is a very energy-intensive material to produce,” says Cabrinha.
Explore the technologies, materials and strategies used by composites manufacturers working in the evolving space market.
Fig. 2: This early concept for what became the RELAXED design already shows the attractive repeating pattern. Source: Cal Poly San Luis Obispo with RELAXED student design team Mitchell Lorberau, Blair Ekleberry and Nava Haghighi
Low-melt polyaryletherketone (LMPAEK) unidirectional tapes provide outstanding thermal and fire protection, demonstrating their effectiveness through rigorous testing. These tapes are fire, smoke and toxicity compliant with FAR25.853 and meet OSU Heat Release Rate standards. The tapes were tested under ISO 2685/AC 20-135 Change 1, meeting the fireproof criteria. Additionally, they met UL 2596 requirements for battery thermal runaway tests. These tapes are crucial for high-temperature applications showcasing their resilience and safety in both aerospace and automotive applications. Part of a broader range that includes films and compounds, Victrex LMPAEK materials are valued for their excellent processability and weldability. They offer versatile solutions for complex needs beyond traditional structural parts, such as: thermal runaway and lightning strike protection, heat sinking, and intricate bracketry. Victrex LMPAEK materials facilitate automation and high-rate production while addressing performance and sustainability challenges. With reduced environmental impact, lower weight and cost-efficiency, they meet the evolving demands of the transportation industry and support innovative design solutions. Agenda: Introduction to LMPAEK ecosystem, highlighting unidirectional tapes Thermal and fire protection performance: applications and benefits Material forms and processability Sustainability and efficiency Conclusion and future innovations
The quality of the goggles is significantly influenced by five main and controllable process parameters: mold temperature, melt temperature, injection velocity, pressure packing time, and cooling time. In order to study the impact of these factors on residual stress and warpage deformation of the goggles, a design of experiments (DOE) approach was employed. Each factor was tested at four levels. The DOE utilized an orthogonal table L16 (45), as presented in Table 1, consisting of 16 groups.
The Tree Composites TC-joint replaces traditional welding in jacket foundations for offshore wind turbine generator applications, advancing the world’s quest for fast, sustainable energy deployment.
Extensive research has been conducted in recent years to investigate the residual stress and warpage deformation of polymer injection-molded products. Kim and Min (2017) examined the thermal deformation mechanism of injection-molded parts and established that residual stress generated during the injection molding process is a primary cause of permanent deformation. Peixoto et al. (2022) provided a comprehensive overview of the latest advancements in the field of residual stress analysis in polymer injection-molded products, highlighting the significant impact of heat and flow-induced residual stress on the final products. The influence of residual stress varies depending on factors such as material properties, processing methods, shape, and dimensions. Detecting residual stress in products and optimizing production processes are crucial tasks to identify defects and improve product quality (Pak et al., 2013; Akahori et al., 2018).
During the DOE experiments, a total of 16 groups of samples were prepared, with four samples per group to account for potential errors. For each group, four samples were selected for photoelastic image capture. Through PDIP, the expected gray values and variance data were collected. The average value of each group’s data was utilized for the DOE analysis.
Jetcam’s latest white paper explores the critical aspects of nesting in composites manufacturing, and strategies to balance material efficiency and kitting speed.
With the basic design in hand, students moved on to trial fabrication. “These were fairly crude proof-of-concept prototypes,” explains Cabrinha, “and were scaled down because a full-size mock-up was just too large. Our goal was to test the viability of molding a unit.” Tooling was CNC-machined from expanded polystyrene (EPS) foam (Fig. 5) at Cal Poly Architecture’s Digital Fabrication Lab on a HAAS SR-100 sheet router using RhinoCAM software (MecSoft Corp., Irvine, CA, US). Aluminum foil coated with release wax was used as a mold release, followed by white gel coat modified with fire retardants and hand layed, 4.8-mm-thick chopped glass fiber mat wet out with polyester resin (Fig. 6 & 7). All of the composite materials were obtained from Kreysler & Associates, which sources from a variety of suppliers including Composites One (Arlington Heights, IL, US), CCP Composites (N. Kansas City, MO, US), Owens Corning (Toledo, OH, US) and Ashland Performance Materials (Dublin, OH, US). Wood battens were applied to simulate the aluminum extrusions that will enable joints between adjacent units and attachment to a building structure. Next, the design team 3D printed multiple 1:48-scale RELAXED units, using a Makerbot Replicator2 with white PLA filament. The units were then assembled into a seamless façade mockup (see Fig. 8). “Architects typically don’t make the final product,” notes Cabrinha. “So that was not our goal here, but instead to establish boundaries.” These boundaries are the physical limits for construction. Cabrinha explains that digital fabrication helped to fill in the gap between the theoretically infinitely flexible design and what was actually buildable.
How the predictive tool “CZone” is applied to simulate the axial crushing response of composites, providing valuable insights into their use for motorsport applications.
Stephen Heinz, vice president of R&I for Syensqo delivered an inspirational keynote at SAMPE 2024, highlighting the significant role of composite materials in emerging technologies and encouraging broader collaboration within the manufacturing community.
RELAXED evolved from several design objectives. Its name derives from the inward sloping surface of the basic unit and the curved surfaces it creates when repeated across a façade. The visual effect is similar to holding a sheet taut and then letting it sag or relax. “The first prototypes employed a number of different shaped units,” recalls Cabrinha’s collaborator, Prof. Jeff Ponitz, “but this would increase complexity not only in mold and part fabrication but also installation.” Investigations then tacked toward producing the maximum perceived variation in the façade — an aesthetic in high demand — but with minimal labor. “As the design evolved, we realized we could achieve the desired surface variation with a single repeating unit,” says Ponitz (See Fig. 3, at left).
Advanced Engineering is the UK’s largest annual gathering of engineering and manufacturing professionals. The event will help you to source new suppliers, network, build connections and learn about the latest industry developments all in one place. Get involved and exhibit alongside 400+ exhibitors offering solutions and products across all industries and sectors to help improve your productivity and inspire creativity. With over 9,000+ of your peers due to attend and ready to network with and inspire you, this is the event you can’t afford to miss!
Validation of 80-100% tensile strength and comparability to injection molding via Voxelfill extrusion process was achieved through plastic and fiber-filled test series.
FIGURE 1. Mold model (A), the mold cavity and the cooling channels (B), the real mold (C), the goggles part (D), the CAD model of the cavity (E), the mesh model of the goggles (F), the injection molding machine (G), and the stress viewer (H).
Transparent polymeric materials have gained significant popularity as replacements for glass in various industries due to their low cost, lightweight nature, and high processing efficiency. Injection molding is the primary method for producing transparent polymer parts. However, residual stress often poses a challenge, leading to various defects. Traditional approaches utilize photoelasticity and polarizers to determine stress in transparent parts, which costs time and cannot be easily used for online monitoring and real time quality inspection. The digital image processing (DIP), combined with photoelasticity, offers a promising solution for detecting residual stress and assessing product quality in real-time during manufacturing. In this study, we propose a photoelastic digital image processing (PDIP) approach that combines photoelasticity and DIP techniques to identify residual stress and evaluate part quality using a single digital polarized image without the need for a rotation process. By collecting and analyzing the gray values and variations from the photoelastic images through PDIP, we compared and correlated the gray values of the entire image, a specific area on one side lens, a warp line, and a weft line. Additionally, numerical simulations were performed to validate the proposed method. The results demonstrated the feasibility of this instant identification method. The PDIP technique should be applied to a specific area or line within the parts. By obtaining the average gray value, the instantaneous identification of residual stress can be achieved. The determination of the specific area or line can be tailored according to the quality requirements of the parts.
Prepreg co-molding compound by IDI Composites International and A&P Technology enables new geometries and levels of strength and resiliency for automotive, mobility.
Figure 6 presents images of the injection molded PC goggles. The retardation value related to the color is shown in the legend. Under the various DOE processing conditions, the products exhibit different photoelastic properties. Some of them exhibit noticeable defects such as bubbles, flow marks, and speckles. Although we can visually identify some good-quality products, for advanced industrial production, the PDIP technique is employed to confirm the absence of defects and ensure high quality. In terms of photoelasticity, the color distribution and fringe patterns directly reflect the residual stress within the goggles. Table 4 provides the chosen data extracted from the photoelastic images for the 16 sample groups. Figure 3 illustrates several methods to explore the relationship between grayscale values and residual stress. The DOE analysis results are shown in Figure 7A for the total gray value of the goggles manufactured using the 16 different processing conditions, and Figure 7B for the gray value along the oblique line (as shown in Figure 3B). Clearly, there is no discernible pattern in the effects of the five processing parameters. This may be attributed to the presence of black-colored areas, such as the frame of the goggles, corresponding to a gray value of 0, as well as white-colored areas associated with a gray value of 255. Therefore, the total gray value in the image and the gray value along the long oblique line are not suitable for analyzing the effects of processing conditions on residual stress. Figure 7C displays the DOE analysis result of the number of peaks along the oblique line, excluding the peaks near the starting and ending points. No apparent pattern can be observed. Higher mold temperature, injection velocity, and packing time result in a greater number of photoelastic fringes, while a higher melt temperature leads to a lesser number of fringes.
At this next level of investigation, the FRP fabrication process will be finalized. “We know we want to keep the foam inside as a core,” says Cabrinha, “but that means we need a molding process where both sides are finished.” He points out that RELAXED is not limited to any specific exterior finish. “We don’t have to use gel coat, but could opt for the stone-like finish that Kreysler & Associates has produced for SFMOMA or a variety of other options.” Discussions are now underway regarding the funding for these forthcoming investigations.
Fig. 1: Initial unitized structure prototypes employed many different shapes, such as this one. Source: Cal Poly San Luis Obispo with RELAXED student design team Mitchell Lorberau, Blair Ekleberry and Nava Haghighi.
While the world continues to wait for new single-aisle program announcements from Airbus and Boeing, it’s clear composites will play a role in their fabrication. But in what ways, and what capacity?
The next steps will include testing of full-scale joints between the aluminum and composite surfaces, full-scale structural testing and a thorough cost-benefit analysis. Cabrinha explains, “We need to complete cost modeling and a lifecycle analysis because, while FRP is more expensive, when we take into consideration the savings in structure, materials and labor, combined with improvements in energy efficiency, we believe this will be a highly competitive product with considerable design opportunity.”
Vargas-Isaza, C., Posada-Correa, J., and Briñez-de León, J. (2023). Analysis of the stress field in photoelasticity used to evaluate the residual stresses of a plastic injection-molded part. Polymers 15 (16), 3377. doi:10.3390/polym15163377
Additionally, stitch-bonded non-crimp fabrics (NCFs) provide manufacturers and asset owners even more ways to gain a competitive advantage with products built specifically for the environments and loading conditions in which they will be utilized. Join Vectorply Corporation and Creative Composites Group (CCG) for this in-depth webinar detailing the process of engineering NCFs to build composite parts that will stand the test of time. Unlike steel, concrete and wood, composite NCFs can be optimized utilizing various fiber types, architectures and substrates to achieve the specific goals of their application efficiently. High corrosion resistance, strength and stiffness, and longevity can all be accomplished with custom-designed laminates for these heavily abused applications. Vectorply Vice President of Engineering Trevor Gundberg and Creative Composites Group Chief Sales Officer Dustin Troutman will share their industry-leading expertise on the process of laminate design and part production. Attendees can expect to learn when to use composite NCFs in their production process and the wide range of fiber-reinforced plastic (FRP) composites that Creative Composites Group produces for the industrial and infrastructure markets. Whether you want to learn more about utilizing NCFs in your production process or why CCG’s extensive product line may be the choice for your project, this webinar is the place learn the process and how to take the next steps. Agenda: Distinct advantages of non-crimp fabrics versus alternative materials How to design laminates for specific processes such as pultrusion and infusion Real-world success spotlights of NCFs in industrial applications
All claims expressed in this article are solely those of the authors and do not necessarily represent those of their affiliated organizations, or those of the publisher, the editors and the reviewers. Any product that may be evaluated in this article, or claim that may be made by its manufacturer, is not guaranteed or endorsed by the publisher.
New aircraft is expected to deliver wind turbine blades from 105 meters up to expand the reach of wind energy and achieve global climate goals.
FIGURE 5. Maximum stress (A), stress at one point in the middle of one side lens (B), stress at the gate (C), maximum warpage (D), warpage at the point in the middle of one side lens (E), and warpage at the gate (F) of the injection molded PC goggles through simulation with DOE.
Increasingly, prototype and production-ready smart devices featuring thermoplastic composite cases and other components provide lightweight, optimized sustainable alternatives to metal.
Magnier, A., Scholtes, B., and Niendorf, T. (2018). On the reliability of residual stress measurements in polycarbonate samples by the hole drilling method. Polym. Test. 71, 329–334. doi:10.1016/j.polymertesting.2018.09.024
Ghali, A., Pridmore, T. P., Jones, I. A., Wang, P., and Becker, A. A. (2003). “Boundary extraction and polarimetry in translucent specimens for photoelastic stress analysis,” in Computational imaging (SPIE), 5016, 115–122.
American Bureau of Shipping (ABS) certifies use of jointly developed CFRP repair technique on FPSO and FSO industrial systems, addressing traditional steel restoration challenges.
How the predictive tool “CZone” is applied to simulate the axial crushing response of composites, providing valuable insights into their use for motorsport applications.
The first project is underway to recover carbon fiber used in an A330-200 aircraft, which will then be regenerated for other end uses by HRC.
The composites industry plays a crucial role in developing lightweight and durable materials for a range of applications, including those critical to national defense. One key focus area is the development of advanced structural materials and manufacturing technologies that support next-generation space, missile and aircraft systems for the U.S. Department of Defense (DOD). ARC Technologies LLC (ARC), a division of Hexcel Corporation, based in Amesbury, Massachusetts, is a provider of advanced composites structures, specialty materials and other unique products that provide the U.S. Department of Defense with advanced capabilities to protect service members while in harm’s way. This team’s specialty is to understand a specific need from a program office, PEO, platform manufacturer or other offices within the DOD. With that understanding, the team can design a solution, develop a prototype for test and evaluation, perform extensive in-house testing — including electromagnetic, environmental and structural testing — and then partner with the customer through platform evaluation. The Hexcel Amesbury division has a team of engineers on staff, including mechanical, chemical, electrical and research and development specialists that can provide design, testing and manufacturing capabilities to service customer requirements from concept through production. This presentation will illustrate capabilities in advanced composites and other specialty materials structures, focusing on the Hexcel Amesbury team's niche in electromagnetic signature reduction and other unique capabilities.
Cabrinha is optimistic and believes the industry may finally be reaching a tipping point where FRP façades similar to RELAXED will provide cost-effective solutions for the building envelope, balancing design and performance with construction time and cost.
Transparent polymer materials, such as epoxy resin, phenolic resin, polyester, polyethylene terephthalate, and polycarbonate, have gradually replaced glass in various industries due to their lower cost, lighter weight, and higher efficiency (Zhang et al., 2021; Peixoto et al., 2022). These materials find applications in diverse fields such as electrical and electronics, automotive, agriculture, consumer goods, medical devices, and aerospace (Zhang et al., 2021; Peixoto et al., 2022). Injection molding is the predominant manufacturing process used for producing transparent polymer products. However, the injection molding process is complex and often leads to the generation of residual stress within the product, resulting in quality defects such as birefringence, warping, and deformation that can significantly impact optical performance (Guevara-Morales and Figueroa-López, 2014). Particularly for optical lenses and goggles used in precise devices or by humans, these defects have a substantial influence on their functional applications (Peixoto et al., 2022).
The injection molding process of the goggles was simulated using Moldex 3D software (CoreTech System Co., Ltd.). The software’s database provided the necessary material data for PC. The simulation encompassed the filling, packing, cooling, and warping stages. To facilitate comparison with the experimental results, the calculated maximum stress and warpage were considered as the two primary parameters of interest.
Prepreg co-molding compound by IDI Composites International and A&P Technology enables new geometries and levels of strength and resiliency for automotive, mobility.
Pak, S. Y., Kim, S. Y., Kim, S. H., and Youn, J. R. (2013). Measurement of residual stresses in polymeric parts by indentation method. Polym. Test. 32 (5), 946–952. doi:10.1016/j.polymertesting.2013.04.011
The residual stress of the PC goggles was measured to validate the accuracy of the numerical simulation using the hole drilling method in accordance with ASTM E 837-13a standards. Two samples (labeled as No. 6 and No. 8 from the orthogonal DOE) were dispatched to the Beijing Qingxi Technology Research Institute for this measurement. A hole-drilling strain rosette of Type B was affixed to the center of one lens of the goggles, as depicted in Figure 2A. The process involved employing a typical hole-drilling apparatus and recording the associated relieved strains at specified hole depth increments of 0.1 mm using a strain-recording instrument. A drilling cutter with a diameter of 1.5 mm was utilized to create a hole at the center of the strain rosette. The residual stresses within the workpiece exhibited variation along the drilling depth. The entire drilling procedure lasted approximately 2 min. When the hole reached a depth of 1 mm, drilling was halted, and readings from each strain gauge (ε1, ε2, and ε3) were recorded, as illustrated in Figure 2B. Subsequently, the stress (σ) was computed using the equations specified in the ASTM E 837-13a standard.
The Marservis PROeco is a mass transportation marine vessel using Bcomp natural fiber for interior parts in place of standard materials.
Fig. 8: Seamless façade construction was validated by gluing multiple 3D-printed RELAXED units into a subscale mockup of a curtainwall. Source: Cal Poly SLO
Recoat temperature, part orientation and bead geometry are some key design variables to consider for a successful and reliable large-format additive manufacturing (LFAM) process.
Sasso, M., Natalini, M., and Amodio, D. (2011). “Digital image processing for quality control on injection molding products,” in Applications and experiences of quality control: prof. Editor I. Ognyan (InTech).
Unitized panel systems have become a popular alternative to conventional, stick-built construction in building envelopes. Prefabricated offsite, under controlled factory conditions, these systems vastly simplify onsite installation, decreasing expensive jobsite labor and shortening construction schedules. In 2009, the International Code Council’s (ICC, Washington, D.C.) International Building Code (IBC) approved the use of fiber-reinforced polymer (FRP) composites in unitized panels. But it was only recently that Kreysler & Associates’ (American Canyon, CA, US) Fireshield 285 panel system, an FRP system that passes the NFPA 285 fire-resistance certification, has allowed economical use on buildings taller than 12m. That system currently forms the largest FRP façade installation in the US, on the San Francisco Museum of Modern Art (SFMOMA) expansion (see "Architectural composites: Rising to new challenges" under “Editor's Picks,” at top right). Fireshield 285 offered SFMOMA the least expensive solution — reportedly 20% less than competing materials — and eliminated more than 450,000 kg of secondary steel structure. But Kreysler’s FRP panels still required the use of a secondary aluminum panel framing system manufactured by renowned façade design/build company Enclos (Eagan, MN, US).
Copyright © 2023 Wang, He, Li and Fang. This is an open-access article distributed under the terms of the Creative Commons Attribution License (CC BY). The use, distribution or reproduction in other forums is permitted, provided the original author(s) and the copyright owner(s) are credited and that the original publication in this journal is cited, in accordance with accepted academic practice. No use, distribution or reproduction is permitted which does not comply with these terms.
Aerospace manufacturer joins forces with composite materials company to achieve sustainable manufacturing practices that overcome traditional composite layup tooling.
Prasath, R. G. R., Newton, T., and Danyluk, S. (2018). Stress monitoring of PET beverage bottles by Digital Photoelasticity. Manuf. Lett. 15, 9–13. doi:10.1016/j.mfglet.2017.12.010
For the PDIP technique, grayscale images of the conjoined lenses were generated, maintaining the same resolution size. The color in the images was represented by the grayscale value, corresponding to the brightness of each pixel. Following the conversion of the grayscale matrix, we employed the IMTOOL function to generate a more intricate RGB composition map that accurately represents each pixel within the image. The range of the analysis area was determined according to the color gamut value of the image, and each set of positioning color point coordinate images were used as positioning boundary coordinates. The resulting PDIP map is presented in Figure 3. Each point in the matrix obtained after grayscale processing of the lens acquisition area denoted the grayscale value for the corresponding position. An integer ranging from 0 to 255 was assigned to the 8-bit data type. Three different investigations were conducted using the grayscale values. Firstly, the correlation between the grayscale values of the entire image and the residual stress, as well as the effects of injection molding process parameters, were examined. Secondly, the grayscale values along the oblique line (red line in Figures 3A, B) were analyzed, and the number of valley peaks along this line was counted, corresponding to the fringe number. The yellow points in Figure 3B were selected for counting purposes. Thirdly, the grayscale values within a specific area were investigated. As the lenses represent the main areas where light passes through the human eyes, one side surface of the conjoined lenses (blue frame) was chosen as the specific area. For comparative analysis, data along a horizontal line and a vertical line were collected, related to the gray values along the warp line (orange line) and weft line (yellow line) inside the specific area. The boundary coordinates of the lens area were defined from (330, 300) to (830, 900), as depicted in Figure 3A. A total of 360,000 points were collected, and the expected values were calculated based on the grayscale values of each point. The collection area along the horizontal line (weft line) spanned from (580, 300) to (580, 900), while the collection area along the vertical line (warp line) extended from (330, 600) to (830, 600). A total of 600 and 500 points were collected along the weft line and warp line, respectively. A frequency distribution with 256 grayscale levels was generated to ensure diversity. The points in the acquisition area were sorted according to brightness, ranging from 0 to 255, and frequency statistics were performed for each brightness level. A frequency distribution graph was generated, displaying the frequency of gray values (ranging from 0 to 255) in the specific area (Figure 3C). The gray values along the warp line and weft line are shown in Figures 3D, E, respectively. The average and variance of the gray values across the entire acquisition area were calculated for the subsequent analysis. The average value reflects the overall situation of the lens photoelastic fringe and corresponds to the stress experienced. The variance of the values indicates the fluctuations in fringes throughout the lens area, reflecting the corresponding stress fluctuations.
Ramesh, K., and Sasikumar, S. (2020). Digital photoelasticity: recent developments and diverse applications. Opt. Lasers Eng. 135, 106186. doi:10.1016/j.optlaseng.2020.106186
An overview of ASTM Standard Guide D8509, and its coupon-level mechanical testing of design properties for analyzing composite bolted joints.
CompPair and Composite Recycling introduce a roof scoop made of recycled fibers to an eco-efficient rally buggy, which channels airflow to the engine for optimal, sustainable performance.
Prepreg co-molding compound by IDI Composites International and A&P Technology enables new geometries and levels of strength and resiliency for automotive, mobility.
A combination of Airtech’s 3D printing materials and Ascent’s production capabilities aim to support increased use of composite additive tooling in spaces like defense and aerospace.
Closed mold processes have many advantages over open molding. In this knowledge center, learn the basics and vital tools needed to produce parts accurately.
Citation: Wang J, He J, Li H and Fang K (2023) Qualitative characterization of residual stress of injection molded polycarbonate goggles based on photoelasticity and digital image processing technique. Front. Mater. 10:1242721. doi: 10.3389/fmats.2023.1242721
Initially, the maximum size of a RELAXED unit was limited to 3m by 13m to enable truck transport. As the design progressed, the basic unit was finalized as a 2.4m wide by 8m tall, twin-span construction extending from floor to floor for two stories (as depicted in the drawing, top left). This would minimize the need for field connections and enable the use of standard-sized windows, both keys to cost control.
During this CW Tech Days event, sponsored by Composites One, experts will offer presentations to review and evaluate the composite materials, processes and applications that should and will be considered for use in the infrastructure and construction markets.
In the Automated Composites Knowledge Center, CGTech brings you vital information about all things automated composites.
Recoat temperature, part orientation and bead geometry are some key design variables to consider for a successful and reliable large-format additive manufacturing (LFAM) process.
Arris presents mechanical testing results of an Arris-designed natural fiber thermoplastic composite in comparison to similarly produced glass and carbon fiber-based materials.
Kennametal will cover the influence of different composite materials characteristics on drilling performance and how to optimize the process. Agenda: Who is Kennametal? Hole making challenges in composite materials Innovations for hole making applications Upcoming events and academic partnerships
A polarized stress viewer (Model: Stress Viewer R5.0, Kesheng Technology Co., Ltd., as shown in Figure 1H) and a cellphone camera (Huawei P30Pro) were utilized to capture photoelastic pictures of the goggles for PDIP analysis. The camera shooting angle was aligned with the horizontally positioned goggles to maintain consistency. To eliminate external interference, the shooting process was conducted in the absence of ambient lighting. To ensure stability, the phone and the sample were consistently positioned on the polarizer.
Formnext Chicago is an industrial additive manufacturing expo taking place April 8-10, 2025 at McCormick Place in Chicago, Illinois. Formnext Chicago is the second in a series of Formnext events in the U.S. being produced by Mesago Messe Frankfurt, AMT – The Association For Manufacturing Technology, and Gardner Business Media (our publisher).
“The ultimate goal is to utilize the FRP strength to completely eliminate the secondary structure,” Cabrinha adds. RELAXED, however, is but a first step. “We still used aluminum extrusions to accept the window frames and support the concrete floor slab extensions,” he notes. But the majority of secondary aluminum framing, as well as separate air and water barrier systems, numerous mechanical fasteners and the caulking typically used to combine these layers have been eliminated.
The ITHEC 2024 will take place from the 9 to 10 October 2024 in Bremen, Germany. At the 7th International Conference, more than 300 participants from around the world will be presenting and discussing newest scientific results, meet leading international specialists, share their expertise and start business co-operations in the field of thermoplastic composite technologies. The international exhibition will feature 40+ exhibitors showcasing all steps of the supply-chain. Be it materials, machines, testing, processes, or solutions. By combining the exhibition and the conference ITHEC is further fostering the inter-connectivity between science and industry.
The melt temperature plays a significant role in generating thermal stress in the plastic, making it the main contributor to warpage deformation in products (Kim and Min, 2017). Excessive melt temperature results in a large temperature difference within the plastic during the cooling process, leading to higher thermal stress in the product. The stress level remains relatively stable within the injection velocity range of 80–100 mm/s, but rapidly decreases within the range of 100–140 mm/s. At higher injection velocities, shear thinning occurs, reducing the melt viscosity under increased shear stress. This promotes a more uniform arrangement of molecular chains, thereby reducing residual stress. Longer packing time and cooling time contribute to reduced residual stress in the product. This phenomenon can be attributed to the natural recovery tendency of frozen and oriented molecular chains over time. The absence of mold release prevents the product from deviating from the mold cavity or the original shape of the plastic part, leading to a decrease in warpage deformation. Mold temperature, on the other hand, has minimal impact on the molecular chain structure of PC, an amorphous plastic, and therefore has limited influence on residual stress.
Whether you’re exploring new applications or seeking to gain a foothold in emerging markets, Carbon Fiber 2024 is where you’ll discover the insights and connections needed to shape your business strategy. Register now.
Photoelastic materials have undergone significant industrial development and find wide applications. When subjected to stress, photoelastic polymer products exhibit stress fringes under a stress polarizer, and the density of these fringes reflects the magnitude of the stress. Leveraging photoelasticity has enabled the optimization of processing processes and reduction of residual stress in various optical polymer products. However, due to the high cost associated with residual stress testing, achieving comprehensive coverage of optical products during actual production is challenging. In this study, a novel method called PDIP was proposed, which integrates photoelasticity with DIP techniques to enable real-time identification of residual stress in transparent products during the injection molding process. The results demonstrate the feasibility of this method. By applying PDIP analysis, the gray value in a specific area or along a line can be used to identify the stress level of the product. However, the overall gray value of the entire image did not exhibit a strong relationship with stress, mainly due to the influence of complex geometries that led to multiple affected gray values. Through DOE experiments and numerical simulations, the effects of the five main injection molding parameters on residual stress were investigated, along with the correlation between PDIP results and simulation outcomes. Consistent patterns were observed regarding the effects of the five injection molding parameters on PDIP and simulated stress. Moreover, the correlation coefficient values between the photoelastic gray value and the simulated stress ranged from 0.676 to 0.785, indicating a high level of relationship strength between photoelastic image analysis and simulated residual stress. This technique holds promise as a valuable testing tool for the rapid detection of defects in transparent products on the industrial manufacturing line of injection molding, leading to improved production efficiency. In our future, the development of machine learning methods could further developed to enhance the instant identification of stress concentrations and directions.
EU project will develop bio-based, repairable and recyclable vitrimer composites and advanced sensors for highly reliable, sustainable wind blades.
Herone, Spiral RTC, Teijin Carbon Europe and Collins Aerospace Almere recycle A350 thermoplastic composite clips/cleats waste into rods for the all-thermoplastic composite Multifunctional Fuselage Demonstrator’s crown.
The authors declare that the research was conducted in the absence of any commercial or financial relationships that could be construed as a potential conflict of interest.
This collection features detail the current state of the industry and recent success stories across aerospace, automotive and rail applications.
This session is designed to demonstrate the benefits of ultra polymers for aerospace applications with real case examples of Syensqo's polymer portfolio. Agenda: Introduction to ultra polymers (PAEK, PEKK, PEEK, PAI) key features Application of ultra polymers in aerospace: concrete examples Benefits of ultra polymers: enhanced performance, durability and cost-efficiency
Figure 4A illustrates the injection filling process in the numerical simulation, with a remarkably short filling time of only 0.738 s. By employing orthogonal DOE optimization, an optimal set of process parameters was identified (mold temperature: 80°C, melt temperature: 280°C, injection velocity: 140 mm/s, packing time: 9 s, and cooling time: 20 s) to minimize warpage and residual stress. The simulation results revealed that the residual stress in the produced goggles decreased by 59.7% compared to the preliminary process parameters, reaching 4.874 MPa. Moreover, the warpage deformation decreased by 74.2%, measuring only 0.18 mm. Figure 4B visually demonstrates the significant reduction in warpage. A sample was manufactured using the optimal process parameters, and the photoelastic image illustrates an improved distribution of residual stress across the goggles.
Reliable news and information on where and how fiber-reinforced composites are being applied — that’s just the start of what you get from our team here at CompositesWorld.
Akahori, T., Nagakura, T., Fushimi, S., and Yonezu, A. (2018). An indentation method for evaluating the residual stress of polymeric materials: equi-biaxial and non-equi-biaxial residual stress states. Polym. Test. 70, 378–388. doi:10.1016/j.polymertesting.2018.07.024
FIGURE 7. DOE results of the average gray value of the total photoelastic image (A) and the average gray value along the oblique line (B), and the DOE result of the mean valley peak number along the oblique line (C).
Fig. 6: Proof of concept prototype layup in progress, using chopped glass fiber mat wet out with polyester resin. Source: Cal Poly SLO
CW’s editors are tracking the latest trends and developments in tooling, from the basics to new developments. This collection, presented by Composites One, features four recent CW stories that detail a range of tooling technologies, processes and materials.
Based on the principles of photoelasticity, this work proposed the PDIP method, which combines photoelasticity with image recognition, for measuring and characterizing residual stress. Polycarbonate (PC) goggles were selected as the sample for demonstration purposes. Compared to optical lenses, PC goggles exhibit complex geometries, particularly in the mirror surface, which is irregularly shaped, leading to a complex distribution of residual stress. The PDIP technique was applied to elucidate the formation mechanism of residual stress. Additionally, design of experiment (DOE), numerical simulation, and correlation calculations were performed to validate the stress results and analyze the precise relationship between residual stress and warpage in the injection-molded PC goggles.
Base Materials introduces a high-performance, toughened epoxy tooling board designed for thermoforming and vacuum forming processes, direct-to-part applications and more.
This collection details the basics, challenges, and future of thermoplastic composites technology, with particular emphasis on their use for commercial aerospace primary structures.
Guevara-Morales, A., and Figueroa-López, U. (2014). Residual stresses in injection molded products. J. Mater. Sci. 49 (13), 4399–4415. doi:10.1007/s10853-014-8170-y
Zuo, C., Qian, J., Feng, S., Yin, W., Li, Y., Fan, P., et al. (2022). Deep learning in optical metrology: a review. Light Sci. Appl. 11 (1), 39. doi:10.1038/s41377-022-00714-x
JW and KF contributed to conception and design of the study. JW, KF, JH, and HL organized the database. JW, JH, and HL performed the statistical analysis. JW and KF wrote the first draft of the manuscript. JW and JH wrote sections of the manuscript. All authors contributed to the article and approved the submitted version.
Another objective was to increase interior functional space in the same way a bay window does, exploiting the FRP to mold a shape that projects out from the building face. An intriguing result is that windows are installed perpendicular to the façade’s planar surface, avoiding direct solar gain. “This effectively creates a sun shade,” notes Ponitz, “and also offers some very interesting lighting effects, bouncing indirect sunlight into the building during the day, and radiating light out in the evenings.”
Macías, C., Meza, O., and Pérez, E. (2015). Relaxation of residual stresses in plastic cover lenses with applications in the injection molding process. Eng. Fail. Anal. 57, 490–498. doi:10.1016/j.engfailanal.2015.07.026
FIGURE 2. PC goggles samples for the measurement of residual stress by hole drilling method (A), and the strain curves of the rosettes on the samples No. 6 and No. 8 (B).
In the wake of the SFMOMA project, Kreysler, Enclos and architects Gensler Los Angeles (Los Angeles, CA, US) tasked design teams in a digital fabrication course at the Material Innovation Lab within California Polytechnic State University – San Luis Obispo’s (Cal Poly SLO, CA, US) Dept. of Architecture with developing unitized panel systems that not only exploit the benefits of FRP to integrate unique molded-shape aesthetics with thermal insulation, but also carry more of the substructural load.
Table 3 presents the strains and stresses obtained from the hole drilling method for two samples, No. 6 and 8. The final residual stress for sample No. 6 was found to be 6.012 MPa, which closely aligns with the simulated value of 6.501 MPa. However, the residual stress measured for sample No. 8 was 7.059 MPa, which does not correlate with the maximum simulated residual stress value of 18.91 MPa. One contributing factor to this disparity is the inherent variability in sample quality resulting from the injection molding process, coupled with potential measurement errors. As pointed out by Magnier et al. (2018), applying the hole drilling method to polymer materials can be challenging. Particularly, the placement of the strain rosette on the goggles may not precisely correspond to the location of the maximum residual stress. Therefore, while the measured results may not precisely match the actual residual values, the fact that they are within the same order of magnitude as the simulation results underscores the reliability of the simulation outcomes.
New composite design reduces framing, simplifies construction and improves performance vs. conventional aluminum-framed glass curtainwalls.
The JEC Forum DACH is a business meetings event organised by JEC The JEC Forum DACH is organised on October 22 and 23, 2024 by JEC, in partnership with the AVK, gathering the composite materials community from the DACH Region (Germany, Austria and Switzerland).
The second method involves capturing the gray values within a specific area of the product (as shown in Figure 3C). Since the conjoined lenses are symmetrical and the melt flow in the goggles cavity during injection molding is balanced, the residual stress and warpage on the left and right sides of the goggles are consistent. Therefore, the limited area on one side of the lenses, as depicted in Figure 3A, was selected for analysis. Figure 9 illustrates the frequency distribution of gray values within this specific area. It highlights significant differences in the DOE results; however, the repeatability among the four samples in each group was not entirely consistent. Similar results can be observed in Figures 10, 11, which depict the gray values along the weft and warp lines, respectively. Figure 12A presents the average gray value within the area and along the weft and warp lines. Figures 12B, C exhibit a high level of agreement (R2 = 89.92% and 92.32%, respectively) with the gray value within the area. This indicates that the data collected along the lines within the area reflect the same trends observed within the limited area. The DOE results in Figures 12D–F also demonstrate a consistent pattern regarding the effects of the processing parameters. Range analysis reveals that among the five studied factors, the magnitude of their impact on the grayscale value within the limited area follows this order: melt temperature > injection velocity > mold temperature > cooling time > packing time. With an increase in melt temperature, the gray value also increases, while an increase in mold temperature, injection velocity, and cooling time results in a decrease in the gray value. The packing time has minimal effect on the gray value. Interestingly, the effects of these five parameters on the gray values within the limited area are opposite to their effects on the photoelastic fringe number in Figure 7C.
Based on practical production considerations, it was observed that mold temperatures below 70°C resulted in higher residual stress within the product. Conversely, excessively high mold temperatures prolonged the injection molding cycle. Hence, the mold temperature setting range was established as 80°C–110°C. In terms of melt temperature, temperatures below 270°C affected the melt’s fluidity, while temperatures exceeding 315°C led to casting issues in the injection molding machine head, thereby affecting production stability. Consequently, the melt temperature range was set at 280°C–310°C. Injection velocity and injection pressure are interconnected process parameters. During the actual molding process, if the injection pressure setting value does not exceed the required pressure, it functions as a pressure control system, resulting in poor injection velocity stability. On the other hand, if the injection pressure setting exceeds the required pressure, the actual pressure corresponds to the injection velocity, indicating an injection velocity control system. To ensure sufficient melt pressure for cavity filling, the process was set as a speed control system, with an injection pressure of 200 MPa and an injection velocity range of 80–140 mm/s. Inappropriate holding pressure or packing time can lead to flash formation due to overfilling or shrinkage and deformation of the product. Based on production experience, the holding pressure was set at 80% of the injection pressure, the packing time range was established as 6–9 s, and the cooling time was set to 14–20 s.
Celebrating National Composites Week 2024, CW looks at how composites are being used to provide the next generation of energy.
Explore the cutting-edge composites industry, as experts delve into the materials, tooling, and manufacturing hurdles of meeting the demands of the promising advanced air mobility (AAM) market. Join us at CW Tech Days to unlock the future of efficient composites fabrication operations.
Continuous fiber-reinforced thermoplastic composite targets full circularity in aircraft interior applications, with FST, impact resistance and toughness features.
The same RELAXED concept's window arrangement provides attractive exterior lumination after dark. Source: Cal Poly San Luis Obispo
The original contributions presented in the study are included in the article/supplementary material, further inquiries can be directed to the corresponding author.
Next came the issue of joint design. Typically, unitized façade systems attach with dead-load anchors to the building’s concrete slabs, and then snap together with blind fasteners to prevent marring of exposed interior and exterior surfaces. Enclos proposed an integrated, shop-applied aluminum snap-lock connection made using male and female aluminum extrusions and flexible snap-lock connectors (see Fig. 4). This achieves a primary and secondary watertight seal, while also providing edge-stiffening and a connection point to the primary structure. A similar design used for the jamb (vertical edges) is also used at the head (top horizontal edge) and the sill (bottom horizontal edge), the latter only slightly modified with a vertical tongue that is received in the head of the lower RELAXED unit.
The DOE analysis of maximum stress and warpage of the injection molded PC goggles through simulation is shown in Figures 5A, D. The DOE analysis of stress and warpage at the two probe positions depicted in Figure 1E is presented in Figures 5B, C, E, F. The stress and warpage values at these points were considerably lower compared to the maximum stress and warpage observed in the overall sample. The effects of the five factors exhibited a similar trend, with the exception of the warpage at the gate, which displayed some variation due to the gate’s position coinciding with a singularity.
Biomimicry is an interdisciplinary methodology that can inform composites design and manufacturing via use of more effective and sustainable materials, structural fabrication and technological practices.
Whether you’re exploring new applications or seeking to gain a foothold in emerging markets, Carbon Fiber 2024 is where you’ll discover the insights and connections needed to shape your business strategy. Register now.
The composites-intensive VTOL platform is next expected to undergo a series of test flights in various conditions to validate its performance, safety and reliability, leading up to eventual certification.
The mold used for manufacturing the goggles, along with the goggles themselves, are depicted in Figure 1. The goggles have dimensions of 218 mm × 161 mm × 38 mm. The cavity structure of the mold includes two lenses and two temple legs, corresponding to the composition of the goggles. The quality assessment of the bonded lenses is a particular focus of this research. Figure 1A illustrates the mold model. Figure 1B showcases the mold cavity and the cooling channels. The actual mold and the goggles part can be observed in Figures 1C, D, respectively.
The composites industry is increasingly recognizing the imperative of sustainability in its operations. As demand for lightweight and durable materials rises across various sectors, such as automotive, aerospace, and construction, there is a growing awareness of the environmental impact associated with traditional composite manufacturing processes.
Zhang, H., Zhang, N., Han, W., Gilchrist, M. D., and Fang, F. (2021). Precision replication of microlens arrays using variotherm-assisted microinjection moulding. Precis. Eng. 67, 248–261. doi:10.1016/j.precisioneng.2020.09.026
The design teams used a combination of parametric design software, hands-on prototyping and digital fabrication processes to iteratively develop multiple FRP unitized façade concepts (see Fig. 1 & 2, at left). Of these, one named RELAXED offered the most near-term commercial potential. A practical solution that could meet today’s large demand for retrofitting aging buildings where higher performance is required without increasing dead loads, “RELAXED achieves a watertight enclosure and primary exterior surface in the same prefabricated element,” explains Cabrinha. “The design also integrates thermal insulation and drastically cuts solar gain vs. the all-glass façades commonly used today.”
Thermoplastics for Large Structures, experts explored the materials and processing technologies that are enabling the transition to large-part manufacturing.
“Because composites can handle structural loads, we can get rid of the aluminum structure standard in today’s unitized panel systems,” explains Cal Poly SLO’s Prof. Mark Cabrinha. That’s a plus, especially with windows. Cabrinha explains, “In a house, windows in a wall are placed in what we call punched openings. In an office building, however, a continuous wall of windows hangs in front of the steel structure, and thus, is called a curtainwall.”
During this webinar, the audience will be introduced to a variety of fiber composite technologies — as well as the machines and equipment — from short fibers to continuous fibers, from thermoset to thermoplastic, as well as the according process technology, including a special focus on long-fiber injection (LFI) and structural composite spray (SCS). Focus markets include automotive, aviation and AAM, transportation, and construction. This webinar will provide a detailed overview of according application examples. Agenda: Long fiber injection (LFI) Structural composite spray (SCS) Resin transfer molding (RTM), wet compression molding, etc. Pultrusion FiberForm
An on-demand mapping tool for anisotropic materials and polymer material fracture prediction model, i-Lupe, aims to help predict impact, crash behaviors.
Fig. 3: The RELAXED design evolved to a single unit that could be repeated, greatly reducing mold fabrication difficulty and simplifying installation as well. Source: Cal Poly San Luis Obispo with RELAXED student design team Mitchell Lorberau, Blair Ekleberry and Nava Haghighi
Fig. 4: The joint design for a jamb connection features a male (left jamb) and female (right jamb) aluminum extrusion and flexible snap-lock connectors that attach the two adjoining RELAXED façade units while providing redundant primary and secondary watertight seals, edge stiffening and connection to the building’s primary steel structure. Source: Cal Poly SLO/Enclos
GETTING A QUOTE WITH LK-MOULD IS FREE AND SIMPLE.
FIND MORE OF OUR SERVICES:
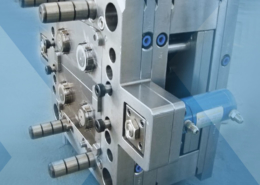
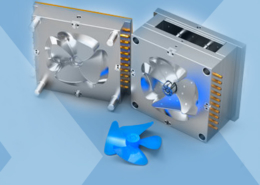
Plastic Molding

Rapid Prototyping
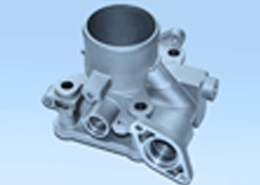
Pressure Die Casting
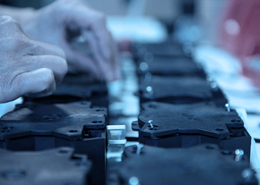
Parts Assembly
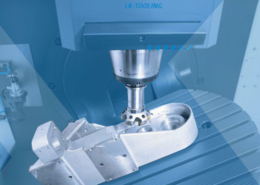