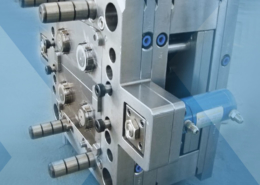
Plastics Processing Activity Contracted in July - plastic molding business
Author:gly Date: 2024-09-30
Brad Scott has had to be up front with companies about what he can realistically produce. (ABC South East SA: Bec Whetham)
"We can actually start small-scale manufacturing, we can de-centralise a lot of our industries out of cities and make them into small country towns and provide small businesses for country towns, revive the whole place," Mr Scott said.
"Currently we can't really say exactly where the plastic is coming from, so we can't make a new product and say that it's food safe," Mr Butler said.
Mr Hakkens started the open-source project in 2012 with the mission of giving people around the world the tools and resources to reduce plastic on a local scale.
This service may include material from Agence France-Presse (AFP), APTN, Reuters, AAP, CNN and the BBC World Service which is copyright and cannot be reproduced.
That he knew of, he said, he was the first to build a machine in Australia, and the first to make a business out of one.
The original space Brad Scott worked out of when he started the business in 2018 was a third the size of his new workspace (pictured). (ABC South East SA: Bec Whetham)
New York, Aug. 02, 2023 (GLOBE NEWSWIRE) -- Reportlinker.com announces the release of the report "Injection Molding Machine Global Market Report 2023" - https://www.reportlinker.com/p06479940/?utm_source=GNW Ltd., Husky Injection Molding Systems Ltd., Japan Steel Works Limited, KraussMaffei Group, UBE Machinery, Shibaura Machine Co. Ltd., Wittmann Battenfeld, and Nissei America Inc.The global injection molding machine market is expected to grow from $12.38 billion in 2022 to $13.14 billion in 2023 at a compound annual growth rate (CAGR) of 6.2%. The Russia-Ukraine war disrupted the chances of global economic recovery from the COVID-19 pandemic, at least in the short term. The war between these two countries has led to economic sanctions on multiple countries, a surge in commodity prices, and supply chain disruptions, causing inflation across goods and services and affecting many markets across the globe. The injection molding machine market is expected to reach $16.12 billion in 2027 at a CAGR of 5.2%.The injection molding machine market consists of sales of horizontal injection molding machines and vertical injection molding machines.Values in this market are ‘factory gate’ values, that is the value of goods sold by the manufacturers or creators of the goods, whether to other entities (including downstream manufacturers, wholesalers, distributors, and retailers) or directly to end customers.The value of goods in this market includes related services sold by the creators of the goods.An injection molding machine refers to a machine used for manufacturing of plastic products and consists of a hopper, an injection unit, a clamping unit, and a control unit. It works by heating plastic pellets until they are molten and then injecting the molten plastic into a mold cavity to create the desired shape.Asia-Pacific was the largest region in the injection molding machine market in 2022.Asia-Pacific is expected to be the fastest-growing region in the forecast period.The regions covered in the injection molding machine report are Asia-Pacific, Western Europe, Eastern Europe, North America, South America, Middle East and Africa.The main technologies of injection molding machines are hydraulic, electric, and hybrid.Hydraulic technology refers to a branch of engineering that deals with the study, design, and application of hydraulic systems, which use liquids, usually oils or water, to transmit power, which is used in injection molding machines to power the machine and control the movements of the various components of the machine during the injection molding process.The clamping force applied includes less than 200 tons force, 200-500 tons force, and more than 200-500 tons by using plastic, rubber, metal, ceramic, and others, with low and high pressure. It is applied in automotive, packaging, healthcare, consumer goods, toy making, building and construction, home appliances, and others.The growing electronics industry is expected to propel the growth of the injection molding machine market going forward.The electronics industry refers to the sector of the economy that produces electronic components, devices, and systems such as semiconductors, integrated circuits, computer hardware, telecommunications equipment, consumer electronics, and other electronic products.Injection molding machines are used in the electronics industry to provide protection for electronic products, produce less waste than other manufacturing processes, have versatility in material selection, and produce high volumes of parts quickly and efficiently.For instance, in July 2022, according to the ZVEI e.V., a Germany-based electro and digital industry association, the global electric market was 4.5 trillion euros ($4.97 trillion) in 2020 and increased in 2021, accounting for 5.0 trillion euros ($5.52 trillion) respectively. Among all the regions, in 2020 Asia captured the highest market share accounting for 63%, America accounted for 19%, and Europe contributed 17% of the market share. Therefore, the growing electronics industry is driving the growth of the injection molding machine market.Technological advancements are a key trend gaining popularity in the injection molding machine market.Major companies operating in the injection molding machine market are adopting new technologies to sustain their position in the market.For instance, in April 2022, LS Mtron Ltd., a South Korea-based manufacturer of medical products launched the latest artificial intelligence (AI)-based smart injection molding system. It is equipped with two technological features ’AI Molding Assistant’ and ’Smart Weight Control’. The AI molding assistant enables a reduction in time and stabilizes the initial molding setup process whereas the smart weight control is integrated with the software of the injection molding machine that helps in the detection of weight changes in products.In February 2022, Comar LLC, a US-based manufacturer, and supplier of innovative plastic solutions acquired Automatic Plastics Ltd for an undisclosed amount.With this acquisition, Comar LLC looks forward to enhancing the manufacturing of pharmaceutical and medical device packaging solutions globally.Further, both companies aim to expand and flourish in the healthcare markets of European regions and are combinedly equipped with 1200 employees and 11 production facilities. Automatic Plastics Ltd. is an Ireland-based contract manufacturer of injection molding machines and products for the pharmaceutical and medical devices sectors.The countries covered in the injection molding machine market report are Australia, Brazil, China, France, Germany, India, Indonesia, Japan, Russia, South Korea, UK, USA.The market value is defined as the revenues that enterprises gain from the sale of goods and/or services within the specified market and geography through sales, grants, or donations in terms of the currency (in USD unless otherwise specified).The revenues for a specified geography are consumption values that are revenues generated by organizations in the specified geography within the market, irrespective of where they are produced. It does not include revenues from resales along the supply chain, either further along the supply chain or as part of other products.The injection molding machines market research report is one of a series of new reports that provides injection molding machines market statistics, including the injection molding machines industry global market size, regional shares, competitors with an injection molding machines market share, detailed injection molding machines market segments, market trends, and opportunities, and any further data you may need to thrive in the injection molding machines industry. This injection molding machines market research report delivers a complete perspective of everything you need, with an in-depth analysis of the current and future scenarios of the industry.Read the full report: https://www.reportlinker.com/p06479940/?utm_source=GNWAbout ReportlinkerReportLinker is an award-winning market research solution. Reportlinker finds and organizes the latest industry data so you get all the market research you need - instantly, in one place.__________________________
"The machines that are coming out (now) have a great capacity so that means we're able to process more of the plastic that's getting dropped off," Mr Butler said.
"If you start with a very large batch of unsorted, uncleaned plastic, then most of your work would come in at the sorting and cleaning stage," Mr Butler said.
"Instead of having to put their waste in their bins they can take it (to a hub) and kind of see a newly realised product there and then."
"We're in that space now where the customer will come to us and say, here's a shape that I would like you to make. Can you make that out of bread tags?"
"As far as people developing these machines into something that works for their business…(it's) not something we've seen an awful lot, but we have seen a lot of people express interest in wanting to implement it."
There are now 10 or so that he knows of in the country, including this Maragaret River start-up turning bottle lids into surfboard fins.
"Since then I've taken it to a different place, and that's really what (Precious Plastic) want you to do — they want you to get the general gist of your recycling and go whatever way you want," he said.
"In Australia we're pretty much picking out number one and number two type plastics and sometimes number five...all the other stuff is basically going to landfill," Mr Scott said. (ABC South East SA: Bec Whetham)
While Mr Scott built a bigger shed and hired an extra employee (his wife) last year to help keep up with business, there was only so much he could do with the technology available, he said.
We acknowledge Aboriginal and Torres Strait Islander peoples as the First Australians and Traditional Custodians of the lands where we live, learn, and work.
"If it takes so much time to produce a small product it doesn't really seem overly cost effective to use the machines for that," Mr Butler said.
"It empowers the community to use those machines and take it into their own community to act as a hub that different people can come to," Mr Butler said.
Not all the plastic goes into a mould. This "waste" creation sits outside Mr Scott's shed. (ABC South East SA: Bec Whetham)
From humble beginnings, experimenting in his studio in the South Australian seaside town of Robe, the former corporate boss from Queensland is now being targeted by major companies around the country looking to repurpose their waste.
Mr Scott said it was worth remembering he was one man in a shed operating home-modified machines made of donated kitchen ovens and car jacks.
While melting down plastic waste and recycling it into everyday items may seem like common sense, Mr Scott is one of few in the country actually doing it.
At the same time Mr Scott was getting started in his shed, Monash University was establishing its Precious Plastic program.
The products that can be made from plastic waste are endless. Precious Plastic Monash put this guitar together. (Supplied: Precious Plastic Monash)
Project leader David Butler said until recently the machines could not take the volume of plastic required to establish a sustainable business.
The machine Mr Scott uses is inspired by the Precious Plastic project, the brainchild of Dutch industrial design student Dave Hakkens.
Mr Butler can imagine a future where Australians drop off their waste at local recycling hubs, from where it is transformed into products.
"If it goes ahead the idea is that they have all the pods they've made out of plastic collected, send them to me, I recycle and make them into a box, and they send them back out to customers or cafes to put their pods in," Mr Scott said.
He said the next challenge and opportunity was creating food-safe products with the recycled plastics, finding ways to ensure the quality of the plastic.
Mount Gambier's Whitty Engineering was approached by Brad Scott late last year. Aaron Hill and Hamish Hopgood have since helped Mr Scott design and build five different product moulds. (ABC South East SA: Bec Whetham)
"That has really motivated us nationally to really think about the fact that we need to invest a bit more energy into our own recycled plastic manufacturing here," Mr Butler said.
Each mould for a Precious Plastic product takes a lot of time and effort to design and develop. Here is Brad Scott in the final stages of assembling a chopping board made with 5,500 old bread tags. (ABC South East SA: Bec Whetham)
Another thing stopping businesses from jumping onboard could be the country's dependency on offshore recycling, Mr Butler said, although he added this was changing as Australia limited the amount of plastic waste it processed overseas.
GETTING A QUOTE WITH LK-MOULD IS FREE AND SIMPLE.
FIND MORE OF OUR SERVICES:
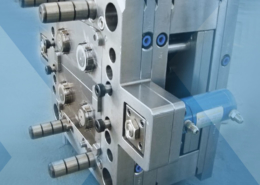
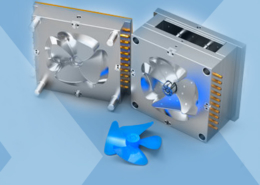
Plastic Molding

Rapid Prototyping
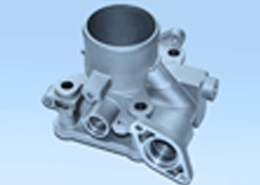
Pressure Die Casting
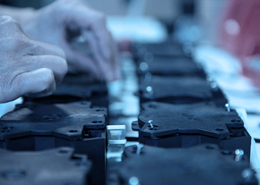
Parts Assembly
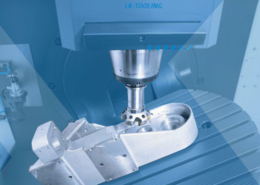