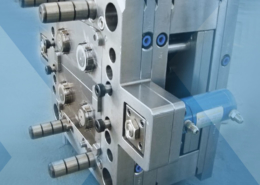
Plastic Recycling At Home Promises A Revolution In Local Plastic Production - lo
Author:gly Date: 2024-09-30
Discover how artifical intelligence is revolutionizing plastics processing. Hear from industry experts on the future impact of AI on your operations and envision a fully interconnected plant.
Successfully starting or restarting an injection molding machine is less about ticking boxes on a rote checklist and more about individually assessing each processing scenario and its unique variables.
The custom molder has secured multiple projects in health care and will be adding cleanroom and white-room spaces, as well as injection molding machines, in support.
The aim of this presentation is to guide you through the factors and the numbers that will help you determine if a robot is a smart investment for your application. Agenda: Why are you considering automation? What problems are you trying to solve? How and why automation can help Crunch the numbers and determine the ROI
Say “manufacturing automation” and thoughts immediately go to the shop floor and specialized production equipment, robotics and material handling systems. But there is another realm of possible automation — the front office.
But there are limitations here, too. Schuler has noticed that CT scanners are becoming more common among custom molders—despite price tags in the mid-six figures. But in the last year he has seen a trend among other users to packing in more and more parts per scan to save time and cost, though this means greater differences between individual parts’ distances from the emitter source, which affects accuracy. “Others may be willing to sacrifice microns for dollars, but we won’t. Others will give you scan data but won’t show you how they scanned your part. We do, as part of our metrology review.”
Which is catering to different industry such as financial sectors, industrial sectors, government organizations, universities, non-profits and corporations. The company's mission is to work with businesses to achieve business objectives and maintain strategic improvements.
After successfully introducing a combined conference for moldmakers and injection molders in 2022, Plastics Technology and MoldMaking Technology are once again joining forces for a tooling/molding two-for-one.
The importance of that dedication and that background of plastics knowledge, Schuler says, is “we’re not just about data on part dimensions, but about the Why? Why are we seeing what we’re seeing? Is a measurement different from spec a tooling issue, or can a shift in process window fix it without expensive tool rework?”
The Octex molding business and Omnia Scientific occupy a 70,000-ft2 main building, with Choice Tool & Mold housed in 10,000-ft2 next door. The main building has a 5500-ft2 Class 8 clean room with five injection presses, while the rest of the 30,000-ft2 manufacturing area is an ISO Class 6 white room with 24/7 particulate monitoring throughout. The plant operates 15 to 25 injection presses from 15 to 400 tons. “We bring in and release presses according to the programs we have running,” says Brett Wigton, chief technology officer. “When we don’t need a press anymore, we sell it.”
“With Omnia, what is most paramount is the team,” says Wigton. “TJ and his engineers are not only metrologists, they are experts in every aspect of injection molding from tool design to the finished product. Their experience in plastics manufacturing and materials, and their understanding of how molding truly works, gives them an edge our competitors simply don’t have. In fact, to my knowledge, there is not a single metrology house that operates as we do. Competitors provide the dimensional geometry of your part, where we provide a full metrology review, which includes everything from dimensional analysis to troubleshooting the tool, troubleshooting the component, and understanding the application and material. We’re able to make suggestions on how issues can be fixed at the tooling, design and manufacturing stages. That helps explain why we have customers who are high-level molders with their own in-house CT scanning, but they still come to Omnia because they are so confident in our ability to provide the most comprehensive analysis.”
While the melting process does not provide perfect mixing, this study shows that mixing is indeed initiated during melting.
Multiple speakers at Molding 2023 will address the ways simulation can impact material substitution decisions, process profitability and simplification of mold design.
Global Sustainable Aluminum Market Size, Share, and COVID-19 Impact Analysis, By Product (Sheet, Plate, Cast Products, Extrusion, and Others), By Processing Method (Rolling, Extruding, Casting, Forging, Drawn, and Others), By End-Use (Construction, Transportation (Aerospace, Automotive, and Marine), Packaging (Food & Beverages, Cosmetics, and Others), Electrical, Consumer Durables, Machinery & Equipment, and Others), and By Region (North America, Europe, Asia-Pacific, Latin America, Middle East, and Africa), Analysis and Forecast 2023 - 2033
Processors with sustainability goals or mandates have a number of ways to reach their goals. Biopolymers are among them.
Join Engel in exploring the future of battery molding technology. Discover advancements in thermoplastic composites for battery housings, innovative automation solutions and the latest in large-tonnage equipment designed for e-mobility — all with a focus on cost-efficient solutions. Agenda: Learn about cutting-edge thermoplastic composites for durable, sustainable and cost-efficient battery housings Explore advanced automation concepts for efficient and scalable production See the latest large-tonnage equipment and technology innovations for e-mobility solutions
Introduced by Zeiger and Spark Industries at the PTXPO, the nozzle is designed for maximum heat transfer and uniformity with a continuous taper for self cleaning.
“What we do at Omnia is special because I’m a molder, I’m a process guy, I’m a tooling guy. I know what it takes to make a good product. I’ve learned the symbiosis of tooling, manufacturing and quality departments. I don’t think there anyone else in the metrology business who does what I do. You’re not just getting a data sheet, you’re getting my experience in plastics manufacturing.
This month’s resin pricing report includes PT’s quarterly check-in on select engineering resins, including nylon 6 and 66.
Core Technology Molding turned to Mold-Masters E-Multi auxiliary injection unit to help it win a job and dramatically change its process.
Schuler is an example of what makes the Omnia “team” special. “I grew up in plastics manufacturing. Fifteen years ago, as a summer intern at Octex, I was shoveling buckets of plastic pellets into a hopper. That gives you respect for the real challenges of manufacturing.” He has RJG training in processing, materials and troubleshooting, as well as training in Scientific Molding with John Bozzelli (a columnist for this magazine). He has tooling experience, too.
Browse key industry insights spread across 240 pages with 110 Market data tables and figures & charts from the report on the "Global Medical Injection Molding Market Size, Share, and COVID-19 Impact Analysis, By Product (Medical Equipment Components, Consumables, Patient Aids, Orthopedics Instruments, Dental Products, and Others), By System (Hot Runner, Cold Runner), By Material (Plastics, Metals, and Others), and By Region (North America, Europe, Asia-Pacific, Latin America, Middle East, and Africa), Analysis and Forecast 2023 – 2033."
Wigton points out another factor in the Octex competitive strategy: “Omnia shines in its ability to compress the timeline of a product launch. Our enhanced tool qualification and pre-production process development and validation are faster than any market competitor, large or small. We accomplish this by having design validation, tooling, molding and metrology under one roof.” The accompanying infographic, supplied by Wigton, shows a 45% to 65% reduction in the overall timeline of a launch.
Second quarter started with price hikes in PE and the four volume engineering resins, but relatively stable pricing was largely expected by the quarter’s end.
When, how, what and why to automate — leading robotics suppliers and forward-thinking moldmakers will share their insights on automating manufacturing at collocated event.
Asia Pacific is expected to hold the largest share of the medical injection molding market over the forecast period.Asia Pacific is expected to hold the largest share of the medical injection molding market over the forecast period. The region's expanding population and rising healthcare demands are driving the need for cutting-edge medical devices and components, which is promoting the use of injection molding technology. The growing prevalence of chronic illnesses combined with the healthcare industry's requirement for accurate and cost-effective manufacturing procedures is fueling the market's growth. Additionally, the availability of skilled labor and advancements in injection molding technologies in countries like China and India have contributed to the region's status as the center for the manufacture of medical devices.
Market SegmentThis study forecasts revenue at global, regional, and country levels from 2020 to 2033. Spherical Insights has segmented the medical injection molding market based on the below-mentioned segments:
The report offers the appropriate analysis of the key organizations/companies involved within the global market along with a comparative evaluation primarily based on their product offering, business overviews, geographic presence, enterprise strategies, segment market share, and SWOT analysis. The report also provides an elaborative analysis focusing on the current news and developments of the companies, which includes product development, innovations, joint ventures, partnerships, mergers & acquisitions, strategic alliances, and others. This allows for the evaluation of the overall competition within the market. Major vendors in the medical injection molding market include the Rodon Group, Currier Plastics, Inc., D&M Plastics, LLC, Molded Rubber & Plastic Corporation, Metro Mold & Design, ARBURG GmbH, BOLE Machinery, Biomerics, Rutland Plastic, Sumitomo Chemical Co., Ltd., Evco Plastics, C&J Industries, Hillenbrand Inc., Tessy Plastics., and Others.
The plastics segment is anticipated to hold the largest market share of the medical injection molding market during the projected timeframe. Based on the material, the medical injection molding market is divided into plastics, metals, and others. Among these, the plastics segment is anticipated to hold the largest market share of the medical injection molding market during the projected timeframe. Plastic injection molding is currently used to build complex designs for medical devices. Plastic medical injection molding is an essential component of the healthcare industry due to its unparalleled precision, versatility, and affordability in producing a broad range of medical devices and components.
Gifted with extraordinary technical know how and an authoritative yet plain English writing style, in this collection of articles Fattori offers his insights on a variety of molding-related topics that are bound to make your days on the production floor go a little bit better.
Omnia Scientific has been a separate operating company since 2016, and its revenue is up 400% since then. Every molding project at Octex utilizes Omnia’s metrology services, though 85% of Omnia’s revenue comes from outside business. Its growth has been largely through word of mouth. “People mail parts to my house on weekends for me to look at,” says Schuler, shaking his head.
Octex is more than a molder. The Octex Group in Sarasota, Fla., comprises three companies: Octex custom injection molding division, which has a growing emphasis on value-added secondary operations like decorating and assembly; Choice Tool & Mold, the moldmaking arm; and Omnia Scientific, the metrology business. The latter two units serve primarily outside customers. Omnia, one of the faster-growing parts of the Group, has become a major focus in differentiating Octex from its competitors.
Across the show, sustainability ruled in new materials technology, from polyolefins and engineering resins to biobased materials.
The Plastics Industry Association (PLASTICS) has released final figures for NPE2024: The Plastics Show (May 6-10; Orlando) that officially make it the largest ever NPE in several key metrics.
Global Carpet Tape Market Size, Share, and COVID-19 Impact Analysis, By Adhesive Type (Rubber-based Carpet Tape and Acrylic-based Carpet Tape), By Application (Carpet Installation, Rug Binding, Temporary Floor Covering, and Others), By End-Users (Residential and Commercial), and By Region (North America, Europe, Asia-Pacific, Latin America, Middle East, and Africa), Analysis and Forecast 2023 – 2033
technotrans says climate protection, energy efficiency and customization will be key discussion topics at PTXPO as it displays its protemp flow 6 ultrasonic eco and the teco cs 90t 9.1 TCUs.
Plastics Technology’s Tech Days is back! Every Tuesday in October, a series of five online presentations will be given by industry supplier around the following topics: Injection Molding — New Technologies, Efficiencies Film Extrusion — New Technologies, Efficiencies Upstream/Downstream Operations Injection Molding — Sustainability Extrusion — Compounding Coming out of NPE2024, PT identified a variety of topics, technologies and trends that are driving and shaping the evolution of plastic products manufacturing — from recycling/recyclability and energy optimization to AI-based process control and automation implementation. PT Tech Days is designed to provide a robust, curated, accessible platform through which plastics professionals can explore these trends, have direct access to subject-matter experts and develop strategies for applying solutions in their operations.
Formnext Chicago is an industrial additive manufacturing expo taking place April 8-10, 2025 at McCormick Place in Chicago, Illinois. Formnext Chicago is the second in a series of Formnext events in the U.S. being produced by Mesago Messe Frankfurt, AMT – The Association For Manufacturing Technology, and Gardner Business Media (our publisher).
Sustainability continues to dominate new additives technology, but upping performance is also evident. Most of the new additives have been targeted to commodity resins and particularly polyolefins.
“Metrology geared specifically to plastics injection molding is special to us. There isn’t a single other metrology house out there that’s dedicated to that.” He adds, “We can accelerate data reporting because we work 24/5 or 24/7, unlike most metrology houses.”
Additive technology creates air pockets in film during orientation, cutting down on the amount of resin needed while boosting opacity, mechanical properties and recyclability.
“Our philosophy is that wherever you are in the manufacturing process, we can make it better,”says Wigton. “We ask the important questions up front: How are we going to make this? How will we deal with the tooling challenges? How will we deal with the metrology challenges? How will it be cost-effective to measure this part in production?”
Krones adds PET preform injection molding to its bottle blowing and filling capabilities, as well as cap molding and expansion into medical, food and other markets.
Another medical device, for administering intravenous fluids, uses Eastman’s Tritan copolyester, which is recommended by the supplier for molding no thinner than 60 to 80 mils. But Octex engineers gambled that the part could be run at 8-10 mil wall thickness, thanks to the firm’s ample experience with the material, its in-house tooling capability, and its ability to measure and maintain precise tool tolerances. According to Thomas “TJ” Schuler, director of Omnia Scientific, “We had run Tritan for years—we knew about its outgassing and the importance of good venting. We knew what kind of injection pressure we’d need, and what kind of screw and barrel. The cores had to be almost perfectly straight across 16 cavities, because any core wobble would take up 15-20% of the total part thickness. So we CT scanned the tool—including vents, core pins and even cavity-pressure sensors—which helped us modify the tolerance stack-up to less than 16 millionths of an inch (0.016 mils).”
Thomas “TJ” Schuler, director of Omnia Scientific, brings experience in molding, tooling and quality assurance to his firm’s metrology services.
Despite price increase nominations going into second quarter, it appeared there was potential for generally flat pricing with the exception of a major downward correction for PP.
X-ray based CT scanners have gained a reputation as the ultimate metrology tool. Systems like Omnia’s Zeiss Metrotom 800 can generate a “point cloud” of millions of measurements in 1 hr. No fixturing is needed, and the scanner can measure internal features and even entire assemblies. “If you want to measure a critical hole with ±1 mil tolerance in an invisible location inside the part—you need a CT scan,” states Schuler.
At other companies, where tooling, manufacturing and metrology are often dispersed among different providers, the “blame game” is all too common: The tool is bad! You can’t process this part! You can’t measure this dimension!
An integral supplier in the effort to fast-track COVID-19 vaccine deployment, Retractable Technologies turned to Arburg and its PressurePilot technology to help deliver more than 500 million syringes during the pandemic.
This Knowledge Center provides an overview of the considerations needed to understand the purchase, operation, and maintenance of a process cooling system.
By having design validation, tooling, molding and metrology under one roof, Octex Group says it can cut project launch time by 45-65%.
New York, United States , July 10, 2024 (GLOBE NEWSWIRE) -- The Global Medical Injection Molding Market Size is to Grow from USD 21.54 Billion in 2023 to USD 36.43 Billion by 2033, at a Compound Annual Growth Rate (CAGR) of 5.40% during the projected period.
Join Wittmann for an engaging webinar on the transformative impact of manufacturing execution systems (MES) in the plastic injection molding industry. Discover how MES enhances production efficiency, quality control and real-time monitoring while also reducing downtime. It will explore the integration of MES with existing systems, emphasizing compliance and traceability for automotive and medical sectors. Learn about the latest advancements in IoT and AI technologies and how they drive innovation and continuous improvement in MES. Agenda: Overview of MES benefits What is MES? Definition, role and brief history Historical perspective and evolution Longevity and analytics Connectivity: importance, standards and integration Advantages of MES: efficiency, real-time data, traceability and cost savings Emerging technologies: IoT and AI in MES
In this three-part collection, veteran molder and moldmaker Jim Fattori brings to bear his 40+ years of on-the-job experience and provides molders his “from the trenches” perspective on on the why, where and how of venting injection molds. Take the trial-and-error out of the molding venting process.
A device that uses the injection molding process to make plastic products is called an injection molding machine, additionally referred to as an injection press. The primary components are the clamping unit and the injection unit. During the injection molding manufacturing process, molten material is injected into a mold to form a product. Although a wide variety of materials can be injected, the most common ones are elastomers, glass, confections, metals (die casting is the process utilized for this), thermoplastic, and thermoset polymers. One of the primary factors driving the market for medical injection molding machines is material selection. Wearable technology and prosthetic surfaces help with the usage of polyethylene due to its high molecular weight, robustness, attractiveness, and relative smoothness. Furthermore, the high initial tooling and machinery costs related to medical injection molding machines may prevent the organization from expanding. Developing a plastic injection facility requires substantial initial expenses, which can keep small and medium-sized companies from entering the market.
Learn about sustainable scrap reprocessing—this resource offers a deep dive into everything from granulator types and options, to service tips, videos and technical articles.
Metrology services dedicated to plastics injection molding is an important factor differentiating Octex from its competition.
North America is predicted to grow at the fastest pace in the medical injection molding market during the projected timeframe. There is a well-established healthcare infrastructure and an enormous demand for medical devices and equipment. Furthermore, the growing prevalence of chronic illnesses and an aging population are driving the growth of the medical injection molding market in this area. One of the key factors affecting the North American sector is the rising per capita healthcare spending in the US on health insurance. This is expected to contribute to an increase in the demand for generic medications and medical supplies.
Global Precious Metals E-Waste Recovery Market Size, Share, and COVID-19 Impact Analysis, By Metal (Gold, Silver, and Others), By Source (Household Appliances, IT & Telecommunication, Consumer Electronics, and Others), and By Region (North America, Europe, Asia-Pacific, Latin America, Middle East, and Africa), Analysis and Forecast 2023 – 2033
Mike Sepe has authored more than 25 ANTEC papers and more than 250 articles illustrating the importance of this interdisciplanary approach. In this collection, we present some of his best work during the years he has been contributing for Plastics Technology Magazine.
In a time where sustainability is no longer just a buzzword, the food and beverage packaging industry is required to be at the forefront of this innovation. By adopting circular packaging processes and solutions, producers can meet regulatory requirements while also satisfying consumer demand and enhancing brand reputation. Join Husky to learn more about the broader implications of the circular economy — as well as how leading brands are leveraging this opportunity to reduce costs, increase design flexibility and boost product differentiation. Agenda: The cost and operational benefits of embracing circularity Key materials in circular packaging — including rPET and emerging bioplastics How to design a circular food and beverage package Strategies for selecting sustainable closures to future-proof packaging solutions Optimization and streamlining of production processes for enhanced efficiency How Husky Technologies can enable your sustainable success
In this collection, which is part one of a series representing some of John’s finest work, we present you with five articles that we think you will refer to time and again as you look to solve problems, cut cycle times and improve the quality of the parts you mold.
In this collection of content, we provide expert advice on welding from some of the leading authorities in the field, with tips on such matters as controls, as well as insights on how to solve common problems in welding.
Mixed in among thought leaders from leading suppliers to injection molders and mold makers at the 2023 Molding and MoldMaking conferences will be molders and toolmakers themselves.
With advocacy, communication and sustainability as three main pillars, Seaholm leads a trade association to NPE that ‘is more active today than we have ever been.’
Exhibitors and presenters at the plastics show emphasized 3D printing as a complement and aid to more traditional production processes.
Mold maintenance is critical, and with this collection of content we’ve bundled some of the very best advice we’ve published on repairing, maintaining, evaluating and even hanging molds on injection molding machines.
Metrology is still poorly understood by a large part of the industry, in Schuler’s view. “Customers say, ‘These dimensions, these tolerances, are what I need to make my part work.’ But no one thinks about what’s needed to make the part manufacturable, the tool maintainable (what’s going to wear out first), and quality measurable. We can be that bridge.”
Extrusion simulations can be useful in anticipating issues and running “what-if” scenarios to size extruders and design dies for extrusion projects. It should be used at early stages of any project to avoid trial and error and remaking tooling.
He explains further, “We do a metrology review with customers at the start of a project. “How exactly do you want this measured in production? The circularity on this diameter is not called out on the print—how do you want it measured?”
The hot runner segment dominated the market with the largest market share of the medical injection molding market during the projected timeframe. Based on the system, the medical injection molding market is divided into hot runner and cold runner. Among these, the hot runner segment dominated the market with the largest market share of the medical injection molding market during the projected timeframe. Hot runner systems are becoming increasingly essential due to their many advantages, including reduced pressure and a shorter cycle time. As the molten mixture must be forced into the mold cavity, waste can be eliminated because runners are not needed, larger parts can be produced at a higher volume, and part consistency and quality are all enhanced.
It’s all part of process validation, Schuler says—“Putting all the systems in place to control and analyze the quality of parts. We develop calibration and control plans. We use Scientific Molding for process development—testing high and low threshholds, finding out what the machine and tool can handle. It’s always a delicate balance between tooling, manufacturing and quality assurance. We fight over 10 thou.”
The medical equipment components segment is expected to grow at the highest CAGR growth of the medical injection molding market during the projected timeframe. Based on the product, the medical injection molding market is divided into medical equipment components, consumables, patient aids, orthopedics instruments, dental products, and others. Among these, the medical equipment components segment is expected to grow at the highest CAGR growth of the medical injection molding market during the projected timeframe. The medical equipment manufacturing business is experiencing a growing demand for medical injection molding due to several significant factors. Recently, complicated medical devices have grown increasingly essential as the healthcare industry develops, and injection molding offers a highly accurate and efficient manufacturing method for fulfilling these needs.
While prices moved up for three of the five commodity resins, there was potential for a flat trajectory for the rest of the third quarter.
Spherical Insights & Consulting is a market research and consulting firm which provides actionable market research study, quantitative forecasting and trends analysis provides forward-looking insight especially designed for decision makers and aids ROI.
While the major correction in PP prices was finally underway, generally stable pricing was anticipated for the other four commodity resins.
Two examples illustrate how Octex is challenging its equipment and its people to achieve higher levels of quality and productivity. One application is a surgical device that involves a metal rod and spring overmolded with PP on both ends. Four housing parts are molded and assembled around the overmolded metal parts. The assembly receives three sonic welds and pad printing.
Thousands of people visit our Supplier Guide every day to source equipment and materials. Get in front of them with a free company profile.
Take a deep dive into all of the various aspects of part quoting to ensure you’ve got all the bases—as in costs—covered before preparing your customer’s quote for services.
There are also optical 2D vision systems. “This is fast, measuring 200 points in 2 sec,” says Schuler, “but it has multiple sources of bias—illumination intensity, use of backlighting or not, distance of the workpiece from the light source. These factors can all give different measurements of the same dimension. This technology is very repeatable, but not necessarily accurate.” To make it accurate, he recommends starting from a “known true standard”—a CT scan.
Resin drying is a crucial, but often-misunderstood area. This collection includes details on why and what you need to dry, how to specify a dryer, and best practices.
One factor contributing to this compressed timeline is a fiber-optic data superhighway, installed by Wigton to handle the massive load generated by CT scans. Where other metrology firms might require weeks to provide usable data from scans of parts from 32 cavities in a single mold, Omnia can do it minutes.
Global PFAS Filtration Market Size, Share, and COVID-19 Impact Analysis, By Technology (Reverse Osmosis, Ion Exchange Resins, Granular Activated Carbon Filters, and Others), By End-User (Commercial, Industrial, Municipal, and Others), and By Region (North America, Europe, Asia-Pacific, Latin America, Middle East, and Africa), Analysis and Forecast 2023 – 2033
Nowadays, Octex Group pursues mainly medical business, which accounts for 65-70% of its revenue. The remainder is a mix of high-end electronics, aerospace/defense R&D projects, and some consumer and industrial jobs. (For an overall company profile, see Feb. ’18 On-Site feature.)
In this collection of articles, two of the industry’s foremost authorities on screw design — Jim Frankand and Mark Spalding — offer their sage advice on screw design...what works, what doesn’t, and what to look for when things start going wrong.
Molding good parts is not enough. Better and faster metrology services for tool qualification and process validation make the difference for Octex Group.
To illustrate the importance of those choices, Schuler cites various measuring technologies available at Omnia. One is touch CMM, very common throughout industry. “It’s very accurate, but limited by how many points it is cost-effective to measure. Do you want to measure four points or 4000? On how many cavities? Time is cost.”
Plastics Technology covers technical and business Information for Plastics Processors in Injection Molding, Extrusion, Blow Molding, Plastic Additives, Compounding, Plastic Materials, and Resin Pricing. About Us
Join this webinar to explore the transformative benefits of retrofitting your existing injection molding machines (IMMs). Engel will guide you through upgrading your equipment to enhance monitoring, control and adaptability — all while integrating digital technologies. You'll learn about the latest trends in IMM retrofitting (including Euromap interfaces and plasticizing retrofits) and discover how to future-proof your machines for a competitive edge. With insights from industry experts, it'll walk you through the decision-making process, ensuring you make informed choices that drive your business forward. Agenda: Maximize the value of your current IMMs through strategic retrofitting Learn how to integrate digital technologies to enhance monitoring and control Explore the benefits of Euromap interfaces and plasticizing retrofits Understand how retrofitting can help meet new product demands and improve adaptability Discover how Engel can support your retrofitting needs, from free consultations to execution
He adds, “Our equipment is becoming specialized for difficult molding.” That means high cavitation (up to 32 with full cavity separation); tight tolerances, such as ±8 mils across 16 cavities for parts “smaller than your pinky tip”; complex geometries, including parts with 1.5-2 mil walls; and micromolding, with a Wittmann Battenfeld 15-ton MicroPower machine.
August 29-30 in Minneapolis all things injection molding and moldmaking will be happening at the Hyatt Regency — check out who’s speaking on what topics today.
While prices moved up for three of the five commodity resins, there was potential for a flat trajectory for the rest of the third quarter.
Across all process types, sustainability was a big theme at NPE2024. But there was plenty to see in automation and artificial intelligence as well.
Join KraussMaffei for an insightful webinar designed for industry professionals, engineers and anyone interested in the manufacturing processes of PVC pipes. This session will provide a comprehensive understanding of the technology behind the production of high-quality PVC pipes: from raw material preparation to final product testing. Agenda: Introduction to PVC extrusion: overview of the basic principles of PVC pipe extrusion — including the process of melting and shaping PVC resin into pipe forms Equipment and machinery: detailed explanation of the key equipment involved — such as extruders, dies and cooling systems — and their roles in the extrusion process Process parameters: insight into the critical process parameters like temperature, pressure and cooling rates that influence the quality and consistency of the final PVC pipes Energy efficiency: examination of ways to save material and energy use when extruding PVC pipe products
Ultradent's entry of its Umbrella cheek retractor took home the awards for Technical Sophistication and Achievement in Economics and Efficiency at PTXPO.
GETTING A QUOTE WITH LK-MOULD IS FREE AND SIMPLE.
FIND MORE OF OUR SERVICES:
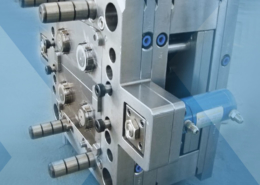
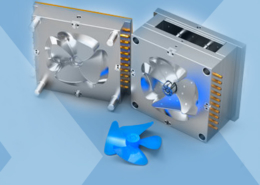
Plastic Molding

Rapid Prototyping
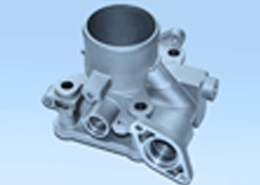
Pressure Die Casting
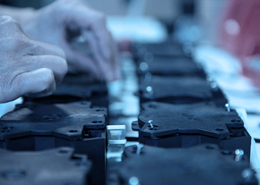
Parts Assembly
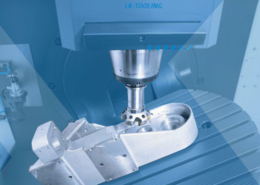