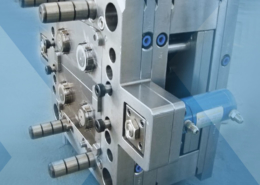
Plastic Molding Technology Invests in New Presses During Banner Year - double in
Author:gly Date: 2024-09-30
Is there still one of those machines at the Griffith Park observatory? I was there in 1986 or 1987 and it had a Space Shuttle mold.
This brings back fond memories of as a kid watching little “King Kong” model figures getting made on the commercial machines. Great stuff.
About three years ago he got the itch to build the mini-molder after learning about the Mold-A-Rama machine — a blow-molding vending machine that was popular a half century ago. A bit of his journey is documented as a molding category on his blog. For the most part it sounds like 1.5 years spent on the CAD design really paid off. He did share one element that required redesign. The initial prototype had a problem with the molds being pushed up when they came together. He tweaked the mechanism to close with a downward motion by flipping the hinge design. This seems to hold everything in place while the drinking fountain chiller and water pump cool the mold and the plastic model within.
The cell also provides flexibility, as it can also be designed with different mounting stands to allow smaller footprints, integrated conveyor systems, or other downstream equipment needed for pre or post moulding automation. The robots can be programmed to work together or can run individually, when one robot can be used when standard two plate moulds are run in the same machine.
By incorporating dual high-speed top entry robots, this type of cell allows for faster cycle times, lower payload requirements, and flexible process flow.
Ah here is the confusion. The mold-a-rama was a hybrid injection blow molder. What isn’t clear is what these guys are doing. This site better explains the process of the mold-a-rama. So you use injection molding to fill the mold, and air to make it hollow. A blending of both processes. It should read injection-blow molding. http://ashermade.com/2010/09/12/diy-mold-a-rama-how-it-works/
By using our website and services, you expressly agree to the placement of our performance, functionality and advertising cookies. Learn more
Decades of application experience, innovative developments and more than 35,000 produced units have made the WITTMANN robots what they are today – the most reliable and innovative robots for the plastics industry. Well planned detailed solutions and state-of-the art components allow highest reliability, shortest cycles and long intervals between maintenance.
“Customers often call asking for dual vertical arm robots to run stack moulds, but in most cases the high-speed top entry robot cells have proven to be more robust and quicker for those applications,” said Jason Long, national sales manager, robots and automation for WITTMANN. “A lot of moulders who are not stack mould experts do not think of this out of the box until we share it with them, as these type of dual robot cells are unique to WITTMANN.”
When looking at stack mould applications, moulders normally opt for a dual vertical arm robot to provide automated part handling. However, the issues with dual vertical arm top entry robots are the speed and payload needed for such applications.
Having been one of those makers that was not selling or crowd funding at a Maker Faire, by the end of the day I was wondering to myself what I was doing there. It was interesting talking to people about my projects for about the first hour, but after that it got really old. It does seem like a good question, why? I’m still trying to come up with a good answer.
The chances of you running into fellow hobbyist blow mold fabricators at such an event is very low. At least with the internet, fellow blow mold fabricator enthusiasts can meet up and talk, exchange ideas, etc.
Why does the title and article read blow molding when the creator says in the video & the youtube title clearly says injection molding. Injection molding is totally different than blow molding. This is his website. http://ashermade.com/category/mini-molder/
You have to set videos as private on YouTube in order to schedule them for publishing. I make a time-zone error (just got back home from CA and my brain didn’t reset, I guess). Sorry!
We caught up with [James Durand] at Maker Faire. He was one of the rare Makers (no mention of selling or future crowd funding) that had a booth at Maker Faire — he was exhibiting a blow molding machine that he built from scratch.
Also you reference the Mold-a-rama as a blow molding machine which it isn’t either. It is an injection molding machine. I know Wikipedia says it’s a blow molding machine but I’m afraid Wiki is also incorrect. There are several videos on YouTube of the mold-a-rama in action and you can see the process in action.
WITTMANN USA, a manufacturer of injection moulding machines, robots and auxiliary equipment, has developed a custom robot solution targeting stack mould applications.
The standard WITTMANN high-speed robots can be mounted to run even the most complex stack mould applications. These cells normally can offer cycle times of 7-12+ seconds, without requiring special robots or causing abnormal wear and tear on dual vertical arm robots, which is the case for robots not designed for quicker cycles.
The fabrication process is 100% [James]. Every custom part was designed and milled by him. All of the assembly techniques were his to learn along the way. And we didn’t see anything that isn’t production ready. We’re both impressed and envious.
The title here said injection molding originally. I guess it was changed in response to a complaint that said it was blow molding.
All creative projects eventually get diluted by competitive exclusion. You are likely trying to work cooperatively to improve your understanding of things, while lower functioning individuals are primarily motivated by reward incentives. Unfortunately the ends justify the means in the real world, and success is defined by most people as having acquired notoriety or a monetary sum.
I am the Department Chair of Applied Technologies at a community college. I was a mold maker before becoming an educator. Would you consider sharing your information? I would like to see this as a departmental project. Thanks,
According to the builder’s description in the video, the molten plastic is injected then the mold is chilled long enough to create a thin shell of solidified plastic. Then the remaining molten plastic is removed from inside that shell. The removal of the remaining molten plastic is aided by air pressure, but I don’t believe that justifies calling this a blow molding process.
GETTING A QUOTE WITH LK-MOULD IS FREE AND SIMPLE.
FIND MORE OF OUR SERVICES:
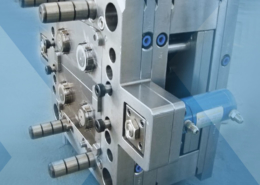
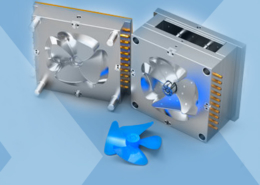
Plastic Molding

Rapid Prototyping
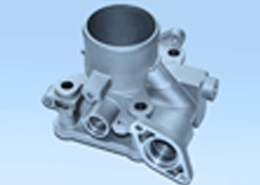
Pressure Die Casting
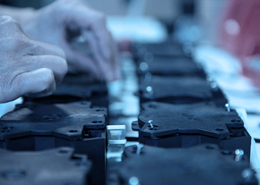
Parts Assembly
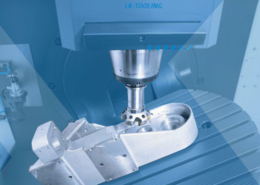