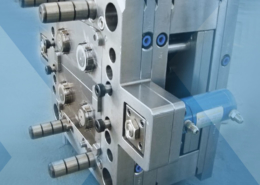
Plastic molding company brings new jobs to Lebanon - plastic molding company
Author:gly Date: 2024-09-30
Other design teams responding to the PPE shortage include MIT in the US, where researchers have invented a flat-pack face shield that can be assembled from a single piece of plastic.
3D printing services at WayKen are primarily laser-powered, offering a high level of speed and accuracy. WayKen stereolithography (SLA) is a UV based curing process, and selective laser sintering (SLS) uses a carbon dioxide laser.
These face shields protect the wearer from infectious droplets spattering on them and help keep their face masks dry. Medical-grade N95 or FFP2 masks must be replaced if they get wet, but are in short supply all over the world.
Approximations of the general parameters of each process are detailed on WayKen.com in the company’s Technology Selection Guide, and a supporting Materials Selection Guide.
Their injection moulding machines can manufacture personal protective equipment (PPE) 75 times faster than a 3D printer explained Dickens, who co-founded UK nonprofit Recycle Rebuild.
"The workspaces follow strict guidelines on how to maintain a clean working environment suitable for making the masks and storing them to avoid contamination," he added.
CNC machined parts at WayKen on the other hand can be used to make functional prototypes which are suitable for engineering evaluation and testing. In contrast to the SLA and SLS services offered, CNC machining requires specially trained engineers to pre-program the processing parameters and toolpaths, then machine according to the programs. Manufacturing costs are therefore quoted taking the extra labor into account. CNC’s advantage is for machining parts with special requirements such as dimensional tolerances and surface qualities.
We will only use your email address to send you the newsletters you have requested. We will never give your details to anyone else without your consent. You can unsubscribe at any time by clicking on the unsubscribe link at the bottom of every email, or by emailing us at [email protected].
Sent every Thursday and containing a selection of the most important news highlights. Plus occasional updates on Dezeen’s services and invitations to Dezeen events.
Shredder machines take sorted plastic waste and turn it back into useable flakes of plastic. Separate machines, including an injection moulder, an extruder or a rotation moulder, turn the flakes back into useful objects.
Infection control guidelines mean PPE must be disposed of after use, Dickens said Precious Plastic could offer a way to recycle any discarded plastic.
The rapid production time of 3D printing means it is finding increased uses throughout the medical industry. WayKen SLA & SLS 3D printing for medicine can be used to make hand held appliances, concept models, and new devices in low volume, e.g. diagnostic equipment, surgical instruments, electronic apparatus and ultrasonic systems. These devices are valuable for surgical planning, simulation and also to map dental correction procedures.
Precious Plastic La Safor and Precious Plastic Gran Canaria have been making and sharing designs for visors that sit on the forehead and hold plastic shields over the wearer's face.
The competitive price point for all services, according to the company’s website, is “normally 30%-50% less than the US/European prices, due to lower labor costs. Moreover allowing a quick project start compares to other rapid prototype companies.”
SLS and SLA 3D printing are useful for fast response solutions. With digital operational tools like slicer software, the process does not require as much specialized training as CNC machining. With little labour involved, the manufacturing cost of 3D printing is priced based on the amount of materials. As larger parts cost more 3D printing is advantageous for small volumes and lightweight parts. Realtively simple structures, wth less demand for surface quality and precision parts, also benefit the most from WayKen’s 3D printing services. The technology is ideal for protoyping small medical devices, industrial tooling, and outer covering of electrical tools.
In China, 3D printer company Creality 3D has designed and donated thousands of buckles that hold a face mask in place without hurting the wearer's ears.
News from Dezeen Events Guide, a listings guide covering the leading design-related events taking place around the world. Plus occasional updates and invitations to Dezeen events.
Established in Hong Kong and located in Shenzhen, WayKen is a contender for China’s most experienced prototype manufacturer. The WayKen Prototype shop operates across two sites, one for plastic and one for metal. In total, the facilities span 20,000 square feet, employing over 60 dedicated personnel. WayKen’s specialist prototyping services include 3D printing (particularly SLA and SLS), CNC milling and rapid tooling technology.As a service bureau operating within high value automotive, medical, and aerospace industries, WayKen Rapid’s expertise is in selecting the right technology for the specific application, and delivering results at a cost competitive with the west.
Recycling initiative Precious Plastic's open-source machines are being used to recycle plastic and turn it into face shields, respirator masks and hands-free door handles to fight coronavirus.
The coronavirus can live on surfaces for days, and people can catch it by touching a door handle and then touching their mouth or eyes. Opening doors without hands helps prevent the spread of infection.
The primary SLA material used by WayKen is an ABS-like photopolymer, suitable for use in the lost-wax method of casting favoured in jewelry making and dental industries. SLS uses powdered Nylon feedstock, which acts like a support material throughout 3D printing, cutting down post-processing times. Parts made using SLS also benefit from the potential of nesting meaning that more designs can be 3D printed within the same build.
In some cases, it may even be beneficial to combine both additive and subtractive manufacturing process to complete an end goal. As an example, SLA and SLS could be used as a preliminary stage before moving the CNC machining.
Founded in 2014 by Dave Jakkens, Precious Plastic shares designs for its machines as open source, so anyone can design and build a recycling system.
A quarterly newsletter rounding up a selection of recently launched products by designers and studios, published on Dezeen Showroom.
Luckily, the company’s quoting system quickly responds to enquiries within 24 hours by our allowing “On-time delivery — every time, no exceptions.” Request a quote from WayKen Rapid online now at WayKen.com.
Groups in Germany, Spain, Greece, Austria and Switzerland are using the open-source machines, which shred and remould old plastic, to make face shields, masks for ventilators and handles that allow the user to open a door without touching it.
In Germany, the Kunststoffschmiede plastic recycling workshop is using its machines to make 20,000 visors for the Dresden area. Plasticpreneur in Austria, which makes machines for the project, has also gone into mass production.
In automotive, WayKen applies a plethora of CNC prototyping and rapid tooling methods to the production of spare parts. The services are useful to car manufacturers running limited trials of a car/motorcycle, and allow volume customization. WayKen automotive rapid prototyping is delivered as a complete service, guiding customers through proof of concept design reviews and mechanical component engineering tests, to show car projects and exterior/interior prototypes.
Greek company Alumoulds, which make moulds for Precious Plastic machines, is working with Precious Plastic Leman in Switzerland to make hands-free door handles.
Sent every Thursday and containing a selection of the most important news highlights. Plus occasional updates on Dezeen’s services and invitations to Dezeen events.
We will only use your email address to send you the newsletters you have requested. We will never give your details to anyone else without your consent. You can unsubscribe at any time by clicking on the unsubscribe link at the bottom of every email, or by emailing us at [email protected].
One of the main advantages of this process is material availability as virtually any material can be CNC machined. For this reason, and its use in industry since the 1940s, CNC machining remains the most common means of prototyping to date
"No official body has approved our designs for medical use at this time, however, several hospitals around the world – including those in Spain – are currently using them," said Dickens.
Hospitals treating coronavirus patients need this emergency PPE to keep their staff safe, as medical workers are particularly vulnerable to being seriously infected.
Our most popular newsletter, formerly known as Dezeen Weekly, is sent every Tuesday and features a selection of the best reader comments and most talked-about stories. Plus occasional updates on Dezeen’s services and breaking news.
WayKen specializes in an ability to machine a range of plastics (opaque and optically clear) and aluminum. In the CNC process, a toolhead gradually subtracts material from a solid block. As such, molecular stability of the base material remains constant producing a part with unparalleled tensile strength.
"To make the items the plastic is heated to over 200 degrees Celsius which sterilises the plastic and it has previously been cleaned," he explained.
"A Precious Plastic workspace in Gran Canaria was requested to provide over 3,000 face visors for the government, hospitals and private sector," said Precious Plastics member Rory Dickens.
As far as resolution is concerned, the accuracy of CNC machining at WayKen is typically higher than 3D printing, between 0.02mm and 0.05mm – 0.10mm depending on geometry. Turnaround time for 3D printing is typically faster at just 2-5 days versus 3 – 8 days for CNC. This does however come at a tradeoff with the volume of products than can be produced. A typical SLA/SLS run can create 1 – 10 parts, whereas CNC has a range of 1 – 50.
CNC operation is determined by computer aided design (CAD) or computer aided manufacturing (CAM) data translated into Gcode – as used by 3D printers. The precision tool path in a CNC system creates an excellent surface finish, and parts can be sanded and finished on the same machine.
"However, as long as the items can be disinfected, I see no reason why they would need to be incinerated, and instead could be cleaned, shredded and recycled into one of Precious Plastics other opensource products."
News from Dezeen Events Guide, a listings guide covering the leading design-related events taking place around the world. Plus occasional updates and invitations to Dezeen events.
"The injected items also benefit from not being porous like 3D printed counterparts, ensuring bacteria and viruses can't hide inside the plastic."
“Traditional” processes at WayKen cover CNC plastic/metal parts machining, vacuum injection molding and rapid injection molding. In the case of CNC machining, a solid block of raw material can be used.
The question is – which technology should you choose? As a WayKen spokesperson states, “it is very difficult to get a standard answer to the cost comparison between 3D printing and CNC machining.” Instead, technology should be selected based on application.
Designers and makers that use the Precious Plastic machines are repurposing them to make items needed by local health care workers.
Our most popular newsletter, formerly known as Dezeen Weekly, is sent every Tuesday and features a selection of the best reader comments and most talked-about stories. Plus occasional updates on Dezeen’s services and breaking news.
A quarterly newsletter rounding up a selection of recently launched products by designers and studios, published on Dezeen Showroom.
GETTING A QUOTE WITH LK-MOULD IS FREE AND SIMPLE.
FIND MORE OF OUR SERVICES:
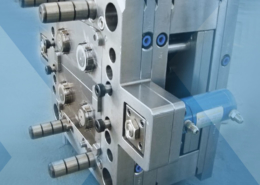
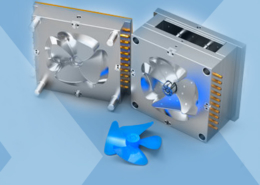
Plastic Molding

Rapid Prototyping
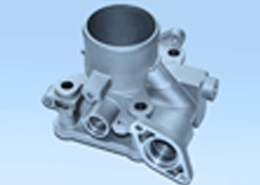
Pressure Die Casting
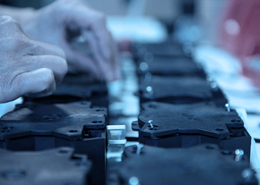
Parts Assembly
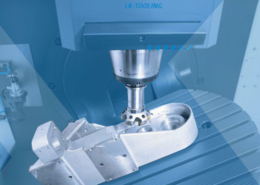