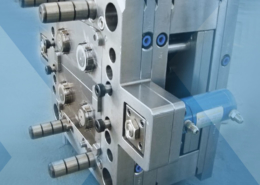
Low Volume Injection Molding: Revolutionizing Production Dynamics
Author:gly Date: 2024-06-08
Low volume injection molding stands as a pivotal innovation in manufacturing, offering versatility and efficiency in producing small to medium batches of intricate plastic components. As the demand for customized products and rapid prototyping surges across industries, understanding the nuances and potentials of low volume injection molding becomes imperative. This article aims to delve into the intricacies of this technology, unraveling its principles, applications, advantages, and future prospects.
The Essence
Low volume injection molding epitomizes precision engineering, leveraging advanced machinery to fabricate intricate plastic parts with unparalleled accuracy and efficiency. Unlike traditional molding processes, it caters to the production needs of small to medium-scale enterprises, offering a cost-effective solution without compromising quality or lead times.
Technical Insights
At its core, low volume injection molding harnesses the principles of thermoplastic injection, wherein molten plastic is injected into a mold cavity under high pressure, cooled, and solidified to form the desired component. The process entails meticulous control over temperature, pressure, and cooling rates to ensure uniformity and consistency in the final product.
Applications Across Industries
The versatility of low volume injection molding transcends industry barriers, finding applications in automotive, medical, consumer electronics, and aerospace sectors, among others. From intricate medical device components to custom automotive prototypes, this technology empowers manufacturers to translate complex designs into tangible products with unprecedented precision and speed.
Advantages and Challenges
The adoption of low volume injection molding brings forth a myriad of benefits, including reduced tooling costs, faster time-to-market, and enhanced design flexibility. However, challenges such as material selection, tooling complexity, and process optimization necessitate a nuanced approach to ensure optimal outcomes.
Environmental Implications
While low volume injection molding offers substantial advantages in terms of efficiency and resource utilization, its environmental footprint warrants scrutiny. By optimizing material usage, implementing sustainable practices, and exploring biodegradable alternatives, manufacturers can mitigate the ecological impact of this technology, paving the way for a greener future.
Innovations and Future Trends
The evolution of low volume injection molding is intrinsically tied to technological advancements and market demands. From the integration of additive manufacturing techniques to the emergence of smart materials, ongoing research and innovation hold the promise of further enhancing the capabilities and sustainability of this transformative manufacturing process.
Conclusion: Pioneering a New Era in Manufacturing
In essence, low volume injection molding emerges as a cornerstone of modern manufacturing, revolutionizing production dynamics and fostering innovation across industries. By unraveling its intricacies, exploring its applications, and addressing associated challenges, this article endeavors to shed light on the transformative potential of this technology. As we navigate towards a future marked by customization, agility, and sustainability, embracing the principles of low volume injection molding will undoubtedly pave the path towards a more efficient, adaptive, and environmentally conscious manufacturing landscape.
GETTING A QUOTE WITH LK-MOULD IS FREE AND SIMPLE.
FIND MORE OF OUR SERVICES:
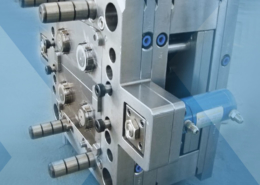
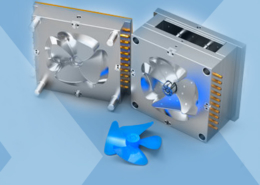
Plastic Molding

Rapid Prototyping
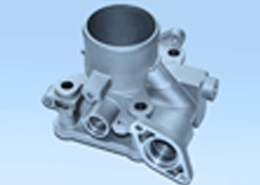
Pressure Die Casting
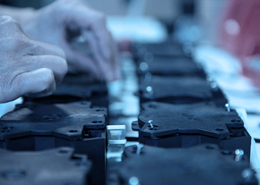
Parts Assembly
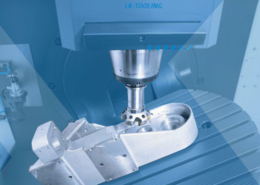