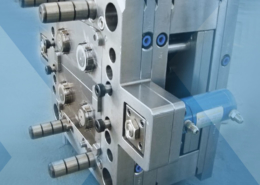
Plastic Injection Molding for Medical Device Market is - medical plastic injecti
Author:gly Date: 2024-09-30
The answer lies in considering the parts and assembly processes that IME renders unnecessary. For example, providing capacitive touch sensing by applying functional foils means that lighting and waveguides need to be produced and installed separately, whereas with IME they are integral to the component. Greater integration means that IME will require fewer parts and materials and fewer assembly processes overall. IME parts, thus, will be lighter, benefitting both electric vehicle range and sustainability.
Be.EV, the Manchester-based national EV charging network, has secured £55m in debt financing from NatWest and KfW IPEX-Bank in a landmark debt raise for the industry.
The deal between the national charge point operator, UK high street bank and German state bank will enable Be.EV to expand its charging network to more than 1,000 rapid and ultra-rapid charge points by the end of 2024.
By contrast, the manufacturing process for IME places more challenging requirements on the materials. First, conductive ink is printed onto a plastic, commonly polycarbonate, substrate. Electrically conductive adhesives (ECAs) are then used to attach electrical components such as LEDs. The substrate with conductive traces and mounted components is then thermoformed to produce the desired curvature, followed by injection molding to produce the complete part.
Because of the less stringent material requirements and lower adoption barriers relative to IME, applying functional foils to slightly curved parts to make capacitive touch switches has already reached commercialization in the automotive sector. Given that the two manufacturing methods result in parts with very similar functionalities and, hence, consumer experience, how can IME compete?
In-mold electronics (IME) is often touted as a forthcoming revolution in how automotive touch-sensitive interfaces will be manufactured. However, while smooth capacitive touch sensors are increasingly common in many recently launched vehicles, especially on steering wheels and parts of the center console, they are not currently produced by IME. Instead, other methods, such as applying functional films to existing 3D parts, are employed.
HMI components that offer backlit capacitive touch sensing are increasingly utilized in multiple applications, including automotive interiors and household appliance control panels. Relative to traditional mechanical switches, the fewer parts used in backlit capacitive touch sensors make them both lighter and simpler to assemble, while the lack of discrete buttons means that they can be wiped clean.
The hybrid thermoforming/injection-molding process has the potential to incorporate a wider range of functionalities, including haptics, energy harvesting, and heating, than current production methods.
Andreas Ufer, member of the management board of KfW IPEX-Bank said: “We are glad to have won Be.EV as a new customer and thus help advance the e-mobility infrastructure in the UK. It is our mission to support the mobility transition with our financings in Europe and worldwide and drive the change towards decarbonisation in our societies.”
Despite their visual similarity, backlit capacitive touch sensors can be produced with a range of different methods. One common approach, deployed in some recently launched cars, is to first produce a decorative, often curved part via high-pressure thermoforming and subsequent injection molding. A functional film comprising a printed conductive pattern of capacitive switches and interconnects is then attached to the back side. Conductive regions can be transparent — either via conductive polymer PEDOT:PSS (poly(3,4-ethylenedioxythiophene) polystyrene sulfonate) or metal mesh) — to enable backlighting with separately produced waveguides.
Asif Ghafoor, CEO of Be.EV, said: “This sizeable commitment from NatWest and KfW and the continued support from Octopus Energy Generation paves the way for future investments in the industry, which ultimately benefits the EV driving community and helps the Government’s zero-emission vehicles by 2035 mandate.
Be.EV said the funding was a milestone in a nascent sector for debt and served as a strong vote of confidence from the banking industry that the public charging industry is a sound investment. The support from Germany’s KfW IPEX-Bank also gives strong endorsement of the UK from abroad.
“It proves that investors, both domestic and international, are confident in the UK’s transition to EVs and its importance in transitioning to a net zero economy.”
This apparent discrepancy poses an important question: Will the capacitive human-machine interface (HMI) components of the future be produced using IME, or will the simpler, currently used manufacturing methodologies persist? This question is addressed in a recent report published by IDTechEx titled, “In-Mold Electronics 2022-2032: Technology, Market Forecasts, Players.” The market could be worth $1.5 billion by 2032, according to the report.
Crucially, as IME technology develops, a wider range of functionalities will be integrated. These include haptics, energy harvesting, heating, and even the control electronics (i.e., PCBs), removing the need for many separate parts and enhancing the IME value proposition. With functional foils, such extensive integration of electronics is challenging and slow, since components would need to be mounted on a 3D surface. By contrast, IME electronic components can be mounted before thermoforming via comparatively rapid conventional 2D pick-and-place systems.
Octopus Energy Generation has also continued its commitment to Be.EV, with further funding allocated as part of the £110m cash injection announced in 2022. Octopus’ investment was made on behalf of the Sky fund (ORI SCSp) it manages, which has a majority stake in Be.EV.
The majority of chargers supported by the new money will be ultra-rapid. There are currently only 5,336 locations in the UK that offer rapid and ultra-rapid charging.
The funds will also help Be.EV to cement its foothold in Manchester and the North West, where it’s already installed more than 600 charge points. These are accessible to all members of the public, with the 35,000 Be.EV members able to charge their EVs at discounted rates. The chargers are powered by renewable energy from Octopus Energy.
Natalie has worked as a fleet journalist for over 20 years, previously as assistant editor on the former Company Car magazine before joining Fleet World in 2006. Prior to this, she worked on a range of B2B titles, including Insurance Age and Insurance Day. Natalie edits all the Fleet World websites and newsletters, and loves to hear about any latest industry news - or gossip.
GETTING A QUOTE WITH LK-MOULD IS FREE AND SIMPLE.
FIND MORE OF OUR SERVICES:
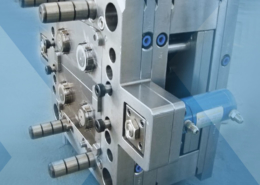
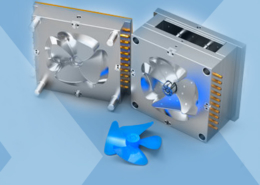
Plastic Molding

Rapid Prototyping
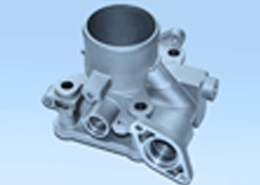
Pressure Die Casting
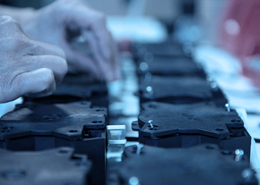
Parts Assembly
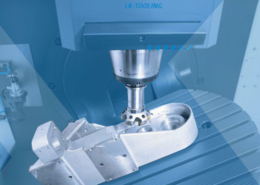