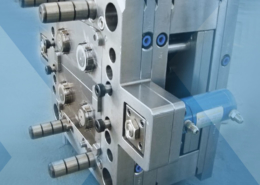
Plastic Injection Molding Company Builds Class 8 Cleanroom for
Author:gly Date: 2024-09-30
Tanzi, M. C., Farè, S., Candiani, G. Foundations of Biomaterials Engineering, 1.4.4.1 Graphite. (Academic Press, 2019). https://doi.org/10.1016/B978-0-08-101034-1.00001-3.
The Force-to-Weight Ratio is a metric used to determine the maximum force that specimens can withstand relative to their weight. This ratio is calculated using data obtained from the results of a tensile test and the weight of the specimens. PGP has a FWR almost 3.3 times higher than the graphite, and (PG)2P exceeds graphite's results by three times (Table 4). These findings indicates that the composite materials are stronger than graphite alone, and with the same weight, they can withstand a higher force before experiencing breaking.
The volume percentages of PEEK in PGP and (PG)2P composites were determined by considering the thickness of graphite and PEEK sheets in the fabricated composites. (PG)2P and PGP showed approximately 154.7% and 172% increases in UTS regarding graphite (Table 3). This increase can be attributed to the volume ratio of PEEK, 39% and 32.5% for PGP and (PG)2P, respectively. Based on our tensile testing results, the ultimate tensile strength (UTS) of graphite was determined to be 16.8 MPa, while pure PEEK exhibited a UTS of 71.2 MPa. Therefore, it can be concluded that the UTS of the composite cannot exceed that of PEEK and should not be lower than the UTS of graphite.
Start by picking a target melt temperature, and double-check data sheets for the resin supplier’s recommendations. Now for the rest...
Nevertheless, in 1915, Röhm secured a German patent for the use of polymerized acrylic acid esters as paint binders and for use in drying oils in industrial paints and lacquers. During this time period, Röhm came up with about 20 different proposed routes for creating useful products based on acrylic acid chemistry. By 1918 he had brought on six chemists to work through these ideas. One of these chemists was Dr. Walter Bauer, who became Röhm’s point man for all things acrylic. Bauer dutifully worked through Röhm’s proposals, but had a much better fundamental understanding of organic chemistry. After going through Röhm’s laundry list without success, he began to work on his own ideas for synthesizing acrylic esters.
The aim of this presentation is to guide you through the factors and the numbers that will help you determine if a robot is a smart investment for your application. Agenda: Why are you considering automation? What problems are you trying to solve? How and why automation can help Crunch the numbers and determine the ROI
Ultradent's entry of its Umbrella cheek retractor took home the awards for Technical Sophistication and Achievement in Economics and Efficiency at PTXPO.
Díez-Pascual, A. M., Naffakh, M., Marco, C., Ellis, G. & Gómez-Fatou, M. A. High-performance nanocomposites based on polyether ketones. Prog. Mater. Sci. 57(7), 1106–1190. https://doi.org/10.1016/j.pmatsci.2012.03.003 (2012).
The anisotropic nature of PEEK/graphite composites allows for a significant level of electrical conductivity facilitated by the graphite sheets. In contrast, PEEK acts as an insulator, directing the flow of current primarily across the graphite layers. Such a composite could have a vast application, for example, in an electrical bus working in a temperature range between 0 and 80 °C in space satellite antennas. In addition, a superior strength-to-weight ratio and high electrical conductivity of PEEK/graphite composites make them well-suited as structural elements in multi-layered membranes and sandwich panels, eliminating the need for aluminum structural supports. Other possible PEEK/graphite composite applications are EM and X-ray radiation shielding for space satellites. Several studies have demonstrated that PEEK exhibits excellent resistance to X-ray and gamma radiation19,20.
Fedel, M., Micheli, V., Thaler, M. & Awaja, F. Effect of nitrogen plasma treatment on the crystallinity and self-bonding of polyetheretherketone (PEEK) for biomedical applications. Polym. Adv. Technol. 31(2), 240–247. https://doi.org/10.1002/pat.4764 (2019).
This reaction, which was only the beginning of the process, became the subject of two patents issued to Rohm & Haas in 1919 and 1921. The process concluded with an innovative approach to the chemistry that was called the “one-pot process.” In doing so, Bauer exploited a chemistry that had been developed in 1913 but had problems with yield that he was able to solve, making the route to commercial application viable.
In contrast to the fillers, graphite is easier to fabricate, and the production of composites using graphite is more cost-effective and feasible. Another reason for incorporating graphite and polymers in composite materials is their high performance in aerospace and vehicle structures. High-modulus graphite is widely used in missile and space launch vehicle structures. The selection of the reinforcing material has a significant impact on the mechanical, electrical, and thermal performance of the fabricated structures. Four-direction carbon fiber composites are more resistant to chemical ablation than their polymer matrix13. Among all carbon group materials, graphite has a layered structure consisting of stacked graphene sheets that allow for a delocalized electron sea, making it a better electrical conductor than carbon nanotubes and CNT14. The layered structure of graphite contributes to its superior thermal properties15. Based on the aforementioned advantages, graphite was chosen as the appropriate material for composite preparation in this study.
Rubel, R. I., Ali, M. H., Jafor, M. A. & Alam, M. M. Carbon nanotubes agglomeration in reinforced composites: A review. AIMS Mater. Sci. 6(5), 756–780. https://doi.org/10.3934/matersci.2019.5.756 (2019).
Across all process types, sustainability was a big theme at NPE2024. But there was plenty to see in automation and artificial intelligence as well.
Second quarter started with price hikes in PE and the four volume engineering resins, but relatively stable pricing was largely expected by the quarter’s end.
In a time where sustainability is no longer just a buzzword, the food and beverage packaging industry is required to be at the forefront of this innovation. By adopting circular packaging processes and solutions, producers can meet regulatory requirements while also satisfying consumer demand and enhancing brand reputation. Join Husky to learn more about the broader implications of the circular economy — as well as how leading brands are leveraging this opportunity to reduce costs, increase design flexibility and boost product differentiation. Agenda: The cost and operational benefits of embracing circularity Key materials in circular packaging — including rPET and emerging bioplastics How to design a circular food and beverage package Strategies for selecting sustainable closures to future-proof packaging solutions Optimization and streamlining of production processes for enhanced efficiency How Husky Technologies can enable your sustainable success
Formnext Chicago is an industrial additive manufacturing expo taking place April 8-10, 2025 at McCormick Place in Chicago, Illinois. Formnext Chicago is the second in a series of Formnext events in the U.S. being produced by Mesago Messe Frankfurt, AMT – The Association For Manufacturing Technology, and Gardner Business Media (our publisher).
In this collection of articles, two of the industry’s foremost authorities on screw design — Jim Frankand and Mark Spalding — offer their sage advice on screw design...what works, what doesn’t, and what to look for when things start going wrong.
SEM images of (a) surface of neat PEEK, (b) surface of graphite, (c) cross-section of (PG)P, and (d) TEM image of PGP interface.
Zhang, S., Awaja, F., James, N., McKenzie, D. R. & Ruys, A. J. A comparison of the strength of autohesion of plasma treated amorphous and semi-crystalline PEEK films. Polym. Adv. Technol. 22(12), 2496–2502. https://doi.org/10.1002/pat.1791 (2011).
PEEK APTIV 1000 polymer was purchased from Goodfellow Cambridge Ltd. in the form of a thin sheet of thickness 8 μm with a density of 1.3 g/cm3. The graphite sheets 8″ × 8″ with a thickness of 25 μm and a density of 2 g/cm3 were purchased from Graphene Supermarket (USA). Table 1 compares the physical properties of PEEK and graphite, utilizing data provided by the manufacturer.
technotrans says climate protection, energy efficiency and customization will be key discussion topics at PTXPO as it displays its protemp flow 6 ultrasonic eco and the teco cs 90t 9.1 TCUs.
Mold maintenance is critical, and with this collection of content we’ve bundled some of the very best advice we’ve published on repairing, maintaining, evaluating and even hanging molds on injection molding machines.
The addition of graphite slightly increased the degradation temperature from 550 to 570 °C and had no significant effect on the thermal stability. Residue weight of PGP and (PG)2P at 900 °C was around 80% and 82% of the initial mass, respectively.
If von Pechmann had remained as Röhm’s advisor, Röhm would likely have transitioned smoothly into an academic position at Tübingen. But by the fall of 1901, when Röhm was concluding his work, von Pechmann left the university, having been diagnosed with “severe melancholy,” what today would be called depression, and took his own life in April of 1902. Röhm set aside his doctorate, but appeared to have an instinctive appreciation of the potential for these materials, and in 1907 he teamed up with banker Otto Haas to form the Rohm & Haas chemical company, a name which became synonymous with acrylic polymers.
Kim, H., Thomas, H. H., Viculis, L. M., Gilje, S. & Kaner, R. B. Electrical conductivity of graphite/polystyrene composites made from potassium intercalated graphite. Carbon 45(7), 1578–1582. https://doi.org/10.1016/j.carbon.2007.02.035 (2007).
Figure 6 shows that the graphite residues remained on a fractured sample after hot pressing, forming a (002) peak with lower intensity. Recent literature30 confirms that the broad peaks observed are associated with the amorphous phase, while the sharp peaks correspond to the crystalline phase. Therefore, the crystallinity index, a quantitative indicator of crystallinity for PEEK, PGP, and graphite, was calculated by comparing the integrated peak areas in the 2θ angle range:
Many researchers have focused on reinforcing polymer matrices using carbon fillers by melt blending and injection molding. However, both methods used for mass production have limitations, such as the high cost of equipment and materials involved16. In contrast, the hot pressing method offers a cost-effective, viable, precise, and expeditious alternative to conventional techniques like melt blending and injection molding. By subjecting the composite materials to elevated temperatures and pressures, this approach facilitates the creation of a single, strong structure with the desired shape and dimensions. The majority of studies conducted thus far have centered around the utilization of the hot press method for fabricating powder-based PEEK/graphite composites16,17,18. However, to the best of our knowledge, no investigations have been reported regarding the production of multi-layered PEEK/graphite laminate composites using the hot press method.
Discover how artifical intelligence is revolutionizing plastics processing. Hear from industry experts on the future impact of AI on your operations and envision a fully interconnected plant.
To examine the decomposition temperature range of the PEEK material, TGA measurements were performed using a STA 6000 (Perkin Elmer) under nitrogen atmosphere at a heating rate of 10 °C/min. The sample was heated from 30 to 900 °C, followed by an isothermal stage for 90 min.
Chung, D. D. L. Electromagnetic interference shielding effectiveness of carbon materials. Carbon 39(2), 279–285. https://doi.org/10.1016/S0008-6223(00)00184-6 (2001).
Exhibitors and presenters at the plastics show emphasized 3D printing as a complement and aid to more traditional production processes.
The hardness and Young's modulus of PEEK, PGP, and (PG)2P were measured using a nanoindentation technique, which has been shown to be effective in measuring the surface mechanical properties of thin films33. Load–displacement curves were obtained from 20 nanoindentations of three samples at a maximum load of 5 mN. The mechanical properties of samples were calculated using the Oliver-Pharr method based on the nanoindentation test results21. Hardness was calculated as follows22:
In this study, high-performance PEEK/graphite thin film laminate composites were fabricated by the hot pressing method. This approach significantly improved the thermal and mechanical properties of the composites, as observed through a series of comprehensive tests and analyses. Our investigations showed a significant interfacial interaction between PEEK and graphite, indicating successful formation of the composite. SEM images provided evidence of this interaction, with a visible close contact between the graphite and PEEK layers. Thermogravimetric analysis showed an improvement in thermal stability with the introduction of graphite. The (PG)2P samples maintained an 80% weight ratio at 900 °C, nearly twice that of pristine PEEK. Furthermore, the crystallinity index of the fabricated composite, as evaluated by XRD analysis, increased from 28.83 to 35.5% compared with pristine PEEK. Mechanical tests revealed a remarkable enhancement in the UTS in the PEEK/graphite laminate, with PGP showing a 172% increase compared to neat graphite. Nanoindentation tests confirmed a notable increase in both Young's modulus and hardness, as the surface mechanical properties of (PG)2P exhibited values three times higher than those of neat PEEK. Additionally, the force-to-weight ratio of PGP and (PG)2P increased 3.3 and 3 times compared to pristine graphite, respectively.
Despite price increase nominations going into second quarter, it appeared there was potential for generally flat pricing with the exception of a major downward correction for PP.
While prices moved up for three of the five commodity resins, there was potential for a flat trajectory for the rest of the third quarter.
This work studies high-performance laminate composite materials made of graphite and poly(ether-ether-ketone) (PEEK). The main objective was to enhance graphite's inherent properties by the addition of PEEK to produce materials with improved thermal and mechanical stability for high-performance applications. The composites were fabricated using a hot press method at a temperature below 310 °C. The newly formed materials were then subjected to various tests, including Scanning Electron Microscopy, Thermogravimetric Analysis, mechanical properties tests, nanoindentation tests, and X-Ray Diffraction to assess their structural, thermal, and mechanical properties. Our findings showed a substantial interfacial interaction between PEEK and graphite, indicating successful composite formation. Both three-layered PEEK/graphite/PEEK (PGP) and five-layered PEEK/graphite/PEEK/graphite/PEEK (PG)2P composites exhibited superior thermal stability at high temperatures compared to neat PEEK. Moreover, our mechanical tests demonstrated a 172% increase in ultimate tensile strength of PGP compared to neat graphite. Additionally, nanoindentation tests confirmed an increase in both Young's modulus and hardness of composites. Furthermore, XRD analysis revealed a 35.5% increase in crystallinity in the fabricated composites compared to pristine PEEK. These findings significantly contribute to the field of high-performance composite materials, confirming that the hot pressing of PEEK and graphite sheets results in enhanced thermal and mechanical properties.
Join this webinar to explore the transformative benefits of retrofitting your existing injection molding machines (IMMs). Engel will guide you through upgrading your equipment to enhance monitoring, control and adaptability — all while integrating digital technologies. You'll learn about the latest trends in IMM retrofitting (including Euromap interfaces and plasticizing retrofits) and discover how to future-proof your machines for a competitive edge. With insights from industry experts, it'll walk you through the decision-making process, ensuring you make informed choices that drive your business forward. Agenda: Maximize the value of your current IMMs through strategic retrofitting Learn how to integrate digital technologies to enhance monitoring and control Explore the benefits of Euromap interfaces and plasticizing retrofits Understand how retrofitting can help meet new product demands and improve adaptability Discover how Engel can support your retrofitting needs, from free consultations to execution
This month’s resin pricing report includes PT’s quarterly check-in on select engineering resins, including nylon 6 and 66.
This Knowledge Center provides an overview of the considerations needed to understand the purchase, operation, and maintenance of a process cooling system.
Oliver, W. C. & Pharr, G. M. Measurement of hardness and elastic modulus by instrumented indentation: Advances in understanding and refinements to methodology. J. Mater. Res. 19(1), 3–20. https://doi.org/10.1557/jmr.2004.19.1.3 (2004).
In this collection of content, we provide expert advice on welding from some of the leading authorities in the field, with tips on such matters as controls, as well as insights on how to solve common problems in welding.
Sariyev, B., Abdikadyr, A., Baitikenov, T. et al. Thermal properties and mechanical behavior of hot pressed PEEK/graphite thin film laminate composites. Sci Rep 13, 12785 (2023). https://doi.org/10.1038/s41598-023-39905-w
Tavlet, M., Van der Burgt, H. Radiation resistance and other safety aspects of high-performance plastics. https://doi.org/10.5170/CERN-1994-007.157.
Batakliev, T. et al. Effects of graphene nanoplatelets and multiwall carbon nanotubes on the structure and mechanical properties of poly (lactic acid) composites: A comparative study. Appl. Sci. 9(3), 469. https://doi.org/10.3390/app9030469 (2019).
When, how, what and why to automate — leading robotics suppliers and forward-thinking moldmakers will share their insights on automating manufacturing at collocated event.
From the calculated data, initially, graphite was 67.72% crystalline, while neat PEEK was 28.83% crystalline. After the hot pressing, the crystallinity index of PGP composite accounted for 35.53%.
Introduced by Zeiger and Spark Industries at the PTXPO, the nozzle is designed for maximum heat transfer and uniformity with a continuous taper for self cleaning.
Tatsuno, D., Yoneyama, T., Kawamoto, K. & Okamoto, M. Hot press forming of thermoplastic CFRP sheets. Proc. Manuf. 15, 1730–1737. https://doi.org/10.1016/j.promfg.2018.07.254 (2018).
Vicario, A. A., Ramanan, S. S. & Arun, S. Composites in missiles and launch vehicles. Compr. Compos. Mater. II(3), 131–152. https://doi.org/10.1016/B978-0-12-803581-8.03960-6 (2018).
SEM is employed to investigate the surface topography of PEEK and graphite, as well as to observe the cross-sectional interface at a relatively high resolution. This technique helps in understanding the bonding behavior between graphite and PEEK layers, as well as identifying any evidence of cracks or voids. Furthermore, TEM was used to conduct a detailed investigation of the interface. Cross-section analysis revealed a close interfacial adhesion along the whole joint due to the high joining load and polymer melting (Fig. 4). Notably, a solid bond was achieved without the need for material surface functionalization23,24,25,26.
One of the big challenges was developing an efficient method for manufacturing the acrylic acid esters to be used as monomers. Many experimenters had started with organic acids, aldehydes or ketones that had chemical structures similar to acrylic acid. These various approaches were plagued by poor yields. Bauer developed a complex multi-step process dubbed the ethylene approach. Because ethylene was difficult to obtain at the time, Bauer started with acetylene, reacting it with hydrogen bromide to form ethylene bromide. This was a route that most chemists felt was fruitless, but Bauer showed that in the presence of the appropriate catalysts, it worked.
Semicrystalline and amorphous XRD diffraction patterns of neat PEEK, graphite, and PGP over the 2θ range from 5 to 45 °C are illustrated in Fig. 6. Graphite exhibits a (002) sharp peak at 2θ = 24°, indicating its graphitic structure28. In addition, the neat PEEK displays peaks at 2θ = 18.82°, 2θ = 20.56°, 2θ = 22.29°, and 2θ = 28.68° belonging to the 110, 111, 200, and 211 planes of the orthorhombic PEEK structure, respectively. The XRD pattern of the hot pressed sample also exhibits a sharp peak at the same angle of 2θ = 26.55° as graphite, indicating the onset of crystallization29.
Alvaredo-Atienza, A., Fernández-Blázquez, J. P., Castell, P. & de Villoria, R. G. Production of graphene nanoplate/polyetheretherketone composites by semi-industrial melt-compounding. Heliyon 6(4), e03740. https://doi.org/10.1016/j.heliyon.2020.e03740 (2020).
Wright, W. Polymers in aerospace applications. Mater. Des. 12(4), 222–227. https://doi.org/10.1016/0261-3069(91)90169-5 (1991).
The monomer that Bauer succeeded in synthesizing was ethyl acrylate. While the breakthrough was made in the very early 1920s, a combination of technical challenges related to polymerization, economic difficulties in Germany during the 1920s, and a healthy dose of paranoia regarding the intellectual property associated with the one-pot process, delayed the development of useful commercial products for about a decade. And that part of the story will be told in our next installment.
Sustainability continues to dominate new additives technology, but upping performance is also evident. Most of the new additives have been targeted to commodity resins and particularly polyolefins.
Crystallinity in polymer composites like PEEK plays a vital role, particularly in mechanical and thermal applications. In mechanical applications, such as aerospace and automotive components, as well as biomedical devices, a higher degree of crystallinity tends to result in improved tensile strength, stiffness, and dimensional stability. Moreover, in thermal applications like electronics and energy storage devices, the degree of crystallinity has a significant impact on the material's thermal conductivity and thermal expansion behavior.
In many respects, nylons and polyesters appear to be interchangeable. But there are interesting differences in the properties of these two families that arise from their chemical structures.
Based on the results of the nanoindentation test, it was observed that (PG)2P possesses superior surface mechanical properties compared to PEEK. Specifically, (PG)2P exhibited a modulus of elasticity three times higher than that of PEEK.
The initial focus for the use of these materials was in textiles and leather goods. Röhm used the proceeds from the sales of these products to resume his acrylic chemistry research. But the history of the development of modern acrylic polymers was characterized by Röhm’s approach as a businessman rather than a chemist. This led to long periods of attempts to develop products that reflected a poor understanding of the acrylic chemistry because the focus was on developing a product that was marketable. Röhm observed that the acrylic polymers he was creating had a rubber-like set of properties.
Moosa, A. & Abed, M. Graphene preparation and graphite exfoliation. Turk. J. Chem. 45(3), 493–519. https://doi.org/10.3906/kim-2101-19 (2021).
The residual material on PEEK was determined by examining the microstructures of fracture surfaces after tensile tests using SEM and EDS (Fig. 11). Through the combined use of SEM and EDS, we were able to observe and confirm the presence of graphite flakes on the fractured surface. The results of the EDS analysis revealed that there was no oxygen and a high carbon content, indicating presence of graphite flakes from bond formation between two different materials during the hot press process. Graphite, being more brittle than PEEK, exhibits fracture characteristics that involve brittle fracture with angular edges and flat surfaces. The observation of such features in the SEM images suggests the fracture process partially occurred within the graphite flakes. The formed flakes are likely responsible for strengthening the composites and improving their mechanical properties. The exact bonding mechanism between PEEK and graphite will be a topic for further investigation in future research.
In 1901 Otto Röhm published his doctoral dissertation on polymerization products of acrylic acid. Röhm’s thesis advisor at the beginning of his doctoral studies was Hans von Pechmann, also a Professor of Chemistry at Tübingen University and the person who had first created polyethylene in 1898 while studying diazomethane. Von Pechmann was persuaded that acrylic-based materials had the same potential as other notable successes of the time such as rubber, celluloid, and casein. He asked Röhm to conduct his doctorate research on esters of acrylic acid. Röhm quickly figured out that methyl acrylate polymerized more easily than ethyl acrylate and focused on creating a solid material using a combination of light, heat, and a chemical initiator. He produced a colorless, transparent material that had characteristics “between tough, flexible glass and stiff rubber.”
Thousands of people visit our Supplier Guide every day to source equipment and materials. Get in front of them with a free company profile.
The tensile tests of the fabricated specimens, PGP and (PG)2P, were performed using a standard universal test machine (Tinius Olsen 10ST). The samples were clamped with grips at both ends and pulled out with a test speed of 0.1 mm/s, as shown in Fig. 3. A displacement was applied to each test piece until the sample failed. The tensile strength, elongation at break, and Young's modulus were obtained directly from the stress–strain curves. Five samples with gauge dimensions of 80 mm in length and 10 mm in width were tested following ASTM D822 standard for each graphite, PEEK, PGP, (PG)2P sample.
PEEK is a thermoplastic material already recommended for use in the aerospace industry. Its great thermal resistance, excellent mechanical performance, and low density compared to metals make it a prospective aerospace material3. In the production of PEEK/carbon composites, various sintering processes can be employed, with hot pressing, hot isostatic pressing and sinter forging being the most commonly used methods. Alternatively, the melt blending approach involves melting PEEK particles and subsequently mixing the molten PEEK with fillers. Injection molding is another technique where the molten PEEK/carbon composite is injected into a mold to achieve the desired shape4,5,6,7,8. However, nanofillers like CNTs and GNPs have a tendency to form agglomerates, making the homogeneous dispersion of carbon a challenging task9,10. Moreover, nanocomposites with GNP and CNT tend to suffer stress defects due to the sharp edges of nanoplatelets and void regions in the microstructure10,11. In addition, GNP and CNT have low-cost efficiency in mass production, while inexpensive nanoclays cannot conduct electricity5. Furthermore, as many researchers mentioned, cost-effective GNP and GO have sophisticated preparation methods compared with graphite due to additional synthesis steps11,12.
Wang, Q. B. et al. Mechanical performance of graphenex/poly(ether ketone ketone) composite sheets by hot pressing. Sci. Rep. https://doi.org/10.1038/s41598-022-08221-0 (2022).
Learn about sustainable scrap reprocessing—this resource offers a deep dive into everything from granulator types and options, to service tips, videos and technical articles.
While the major correction in PP prices was finally underway, generally stable pricing was anticipated for the other four commodity resins.
Additive technology creates air pockets in film during orientation, cutting down on the amount of resin needed while boosting opacity, mechanical properties and recyclability.
The process from the first synthesis of acrylic acid, the base from which the monomer is derived, to introduction of the commercial polymer, was an 85-year journey. Even after commercialization of the first compounds, the process of getting to the acrylic materials that we are familiar with today was fraught with a number of technical and economic hurdles, as well as battles involving intellectual property and professional pride. The process was driven almost exclusively by German chemists; even when contributions were made by scientists from other countries like England, they were working in or had been educated in Germany.
While the melting process does not provide perfect mixing, this study shows that mixing is indeed initiated during melting.
Bauer, in commenting on his experiences in investigating new approaches to chemistries that were thought to be useless, delivered a quote that should resonate with all innovators: “Doubts about the accuracy of existing thinking prove to be justified again and again. Research scientists frequently need to act in a way that appears irrational.”
Plastics Technology covers technical and business Information for Plastics Processors in Injection Molding, Extrusion, Blow Molding, Plastic Additives, Compounding, Plastic Materials, and Resin Pricing. About Us
Across the show, sustainability ruled in new materials technology, from polyolefins and engineering resins to biobased materials.
Furthermore, the morphology of fabricated samples was examined using SEM with integrated EDS (Crossbeam 540, Zeiss). It was operated at 15 kV in the secondary electron mode. A thin gold coating was applied to the specimens to obtain a conductive surface for further SEM and EDS investigations.
Puértolas, J. A., Castro, M., Morris, J. A., Ríos, R. & Ansón-Casaos, A. Tribological and mechanical properties of graphene nanoplatelet/PEEK composites. Carbon 141, 107–122. https://doi.org/10.1016/j.carbon.2018.09.036 (2019).
Thank you for visiting nature.com. You are using a browser version with limited support for CSS. To obtain the best experience, we recommend you use a more up to date browser (or turn off compatibility mode in Internet Explorer). In the meantime, to ensure continued support, we are displaying the site without styles and JavaScript.
XRD tests were conducted at room temperature using a SmartLab SE X-ray diffractometer (Rigaku) with CuKλ radiation (λ = 0.154 nm). XRD data were obtained from the fractured samples of PGP, PEEK, and graphite film samples. The total scanning time was 90 min, the X-ray tube voltage was 45 kV, and the current was 40 mA.
Devaraju, S., Alagar, M. Polymer matrix composite materials for aerospace applications. In Encyclopedia of Materials: Composites 947–969 (2021). https://doi.org/10.3390/polym13213721.
Open Access This article is licensed under a Creative Commons Attribution 4.0 International License, which permits use, sharing, adaptation, distribution and reproduction in any medium or format, as long as you give appropriate credit to the original author(s) and the source, provide a link to the Creative Commons licence, and indicate if changes were made. The images or other third party material in this article are included in the article's Creative Commons licence, unless indicated otherwise in a credit line to the material. If material is not included in the article's Creative Commons licence and your intended use is not permitted by statutory regulation or exceeds the permitted use, you will need to obtain permission directly from the copyright holder. To view a copy of this licence, visit http://creativecommons.org/licenses/by/4.0/.
The Plastics Industry Association (PLASTICS) has released final figures for NPE2024: The Plastics Show (May 6-10; Orlando) that officially make it the largest ever NPE in several key metrics.
Aliphatic polyketone is a material that gets little attention but is similar in chemistry to nylons, polyesters and acetals.
Take a deep dive into all of the various aspects of part quoting to ensure you’ve got all the bases—as in costs—covered before preparing your customer’s quote for services.
The obtained results strongly indicate an enhancement of crystallinity of the fabricated samples with the addition of graphite into the PEEK, and similar results were reported by Batakliev et al.31. In addition, Harris et al.32 investigated the crystallization behavior of neat PEEK with carbon-containing filler added to the polymer matrix. As a result, graphite acts as a stress initiator for nucleation and increases crystallization within the polymer at temperatures close to the melting temperature of PEEK32.
The road from discovery in the lab to commercial viability can be long, and this was certainly the case for acetal polymers.
Join KraussMaffei for an insightful webinar designed for industry professionals, engineers and anyone interested in the manufacturing processes of PVC pipes. This session will provide a comprehensive understanding of the technology behind the production of high-quality PVC pipes: from raw material preparation to final product testing. Agenda: Introduction to PVC extrusion: overview of the basic principles of PVC pipe extrusion — including the process of melting and shaping PVC resin into pipe forms Equipment and machinery: detailed explanation of the key equipment involved — such as extruders, dies and cooling systems — and their roles in the extrusion process Process parameters: insight into the critical process parameters like temperature, pressure and cooling rates that influence the quality and consistency of the final PVC pipes Energy efficiency: examination of ways to save material and energy use when extruding PVC pipe products
Patel, P. et al. Mechanism of thermal decomposition of poly (ether ether ketone)(PEEK) from a review of decomposition studies. Polym. Degrad. Stab. 95(5), 709–718. https://doi.org/10.1016/j.polymdegradstab.2010.01.024 (2010).
Lynch-Branzoi, J. K. et al. Shear exfoliation of graphite into graphene nanoflakes directly within polyetheretherketone and a spectroscopic study of this high modulus, lightweight nanocomposite. Compos. Part B Eng. 188, 107842. https://doi.org/10.1016/j.compositesb.2020.107842 (2020).
Resin drying is a crucial, but often-misunderstood area. This collection includes details on why and what you need to dry, how to specify a dryer, and best practices.
Li, T. & Hsu, S. L. Enhanced thermal conductivity of polyimide films via a hybrid of micro- and nano-sized boron nitride. J. Phys. Chem. B 114(20), 6825–6829. https://doi.org/10.1021/jp101857w (2010).
Nowadays, carbon-polymer composites find applications in various industries due to their outstanding strength-to-weight ratio. One application of this type of material lies within the aerospace industry, where composites are required to demonstrate exceptional performance in terms of high stress, fracture resistance, and damage tolerance, all while maintaining a significantly reduced weight to enable efficient transport of payloads1,2. The usage of carbon-polymer composites can save up to 20% and 40% of weight for primary and secondary structures, respectively. Polymer composites are also versatile in manufacturing, as they can be molded into complex shapes.
Zhang, Q. et al. Microstructure and nanoindentation behavior of Cu composites reinforced with graphene nanoplatelets by electroless co-deposition technique. Sci. Rep. 7(1), 1–12. https://doi.org/10.1038/s41598-017-01439-3 (2017).
In this work, we focused on the fabrication of PEEK/graphite composites using the hot press method. We examined the mechanical and thermal properties by tensile test, nanoindentation, and TGA. In addition, the crystallinity behavior of the PGP composite was studied.
Plastics Technology’s Tech Days is back! Every Tuesday in October, a series of five online presentations will be given by industry supplier around the following topics: Injection Molding — New Technologies, Efficiencies Film Extrusion — New Technologies, Efficiencies Upstream/Downstream Operations Injection Molding — Sustainability Extrusion — Compounding Coming out of NPE2024, PT identified a variety of topics, technologies and trends that are driving and shaping the evolution of plastic products manufacturing — from recycling/recyclability and energy optimization to AI-based process control and automation implementation. PT Tech Days is designed to provide a robust, curated, accessible platform through which plastics professionals can explore these trends, have direct access to subject-matter experts and develop strategies for applying solutions in their operations.
Conceptualization, B.S.; methodology, B.S.; synthetic materials and performance characterization, B.S., A.A., T.B. and Y.A.; investigation, B.S. and A.A.; resources, T.B. and Y.A.; data curation, B.S. and A.A.; writing of the original draft preparation, B.S., A.A. and Y.A.; writing of review and editing, B.S., A.A., T.B. and B.G.; visualization, T.B.; supervision, B.G. and C.S.; project administration, B.G. and C.S.; funding acquisition, B.G. and C.S.; all authors have read and agreed to the published version of the manuscript.
These findings underline the promise of our fabrication approach for creating highly thermally stable and mechanically robust composites. The strategy of preparing PEEK/graphite laminates through hot pressing offers a viable pathway for the production of advanced materials for high-performance applications. The substantial improvements in both thermal and mechanical properties observed in this study underscore the potential of these composites for wide-ranging applications.
Fracture toughness is assessed by evaluating the area under the stress–strain curve. The extent of this area directly correlates with the ductility of the composite. Among the four composites analyzed, the graphite composite exhibits the smallest area, indicating greater brittleness. On the other hand, (PG)2P composite displays a larger area, suggesting improved ductility and reduced brittleness. Thus, PEEK makes the composite more ductile26. The results demonstrated a six-fold increase in elongation prior to fracture, progressing from graphite to PGP. The inclusion of PEEK results in a reduction in the stiffness of composites (Table 3). To calculate the Young's modulus of the composites from the stress–strain graph, specific points were chosen on each curve that corresponded to strain values of 0.011% and 0.021%. The slopes of the lines passing through these points were then utilized to determine the stiffness of the composites.
In summary, the moderate difference in results between the tensile test and nanoindentation technique can be attributed to the different measurement approaches. The tensile test measures the overall effective modulus under dynamic conditions reflecting the bulk mechanical properties of the sample, while nanoindentation measures the surface mechanical properties. The results obtained by nanoindentation are generally higher in modulus of elasticity and hardness compared to the tensile test due to the influence of surface tension as well as factors such as size effect, non-linear viscoelasticity, particle density, strain exceeding the elastic limit, and imposed hydrostatic stress values34.
Mike Sepe has authored more than 25 ANTEC papers and more than 250 articles illustrating the importance of this interdisciplanary approach. In this collection, we present some of his best work during the years he has been contributing for Plastics Technology Magazine.
Core Technology Molding turned to Mold-Masters E-Multi auxiliary injection unit to help it win a job and dramatically change its process.
Bassett, D. C., Olley, R. H. & Al Raheil, I. A. M. On crystallization phenomena in PEEK. Polymer 29(10), 1745–1754. https://doi.org/10.1016/0032-3861(88)90386-2 (1988).
Successfully starting or restarting an injection molding machine is less about ticking boxes on a rote checklist and more about individually assessing each processing scenario and its unique variables.
While prices moved up for three of the five commodity resins, there was potential for a flat trajectory for the rest of the third quarter.
Hsissou, R. et al. Polymer composite materials: A comprehensive review. Compos. Struct. 262, 113640. https://doi.org/10.1016/j.compositesb.2019.107625 (2021).
Join Engel in exploring the future of battery molding technology. Discover advancements in thermoplastic composites for battery housings, innovative automation solutions and the latest in large-tonnage equipment designed for e-mobility — all with a focus on cost-efficient solutions. Agenda: Learn about cutting-edge thermoplastic composites for durable, sustainable and cost-efficient battery housings Explore advanced automation concepts for efficient and scalable production See the latest large-tonnage equipment and technology innovations for e-mobility solutions
Mixed in among thought leaders from leading suppliers to injection molders and mold makers at the 2023 Molding and MoldMaking conferences will be molders and toolmakers themselves.
Volz, T., Schwaiger, R., Wang, J., Weygand, S. M. Comparison of three approaches to determine the projected area in contact from finite element Berkovich nanoindentation simulations in tungsten. In IOP Conference Series: Materials Science and Engineering (257) (2017). https://doi.org/10.1088/1757-899X/257/1/012013.
Department of Mechanical and Aerospace Engineering, School of Engineering and Digital Sciences, Nazarbayev University, 010000, Astana, Kazakhstan
The tensile tests examined the effect of PEEK on the mechanical properties of graphite, and the resultant graphs for neat graphite, PEEK, PGP, and (PG)2P are shown in Fig. 7.
Mokhtari, M., Archer, E., Bloomfield, N., Harkin-Jones, E. & Mcilhagger, A. Melt-blended multifunctional PEEK/expanded graphite composites. Front. Mater. https://doi.org/10.3389/fmats.2021.724958 (2021).
Acrylic acid was first synthesized in the laboratory in 1843. Methacrylic acid was derived from acrylic acid in 1865 and shortly thereafter it was reacted with methanol to produce the compound known as methyl methacrylate. This is the monomer that is the primary ingredient in what would eventually become the acrylic polymer. The accompanying figure shows the chemical structure of these three compounds. Both methacrylic acid and methyl methacrylate contain the double bond that is crucial in promoting polymerization. In 1877, the German chemist Wilhelm Rudolph Fittig, Professor of Chemistry at Tübingen University, discovered the process for polymerizing methacrylic acid.
The thermal stability of the composites was studied using TGA under nitrogen atmosphere. Figure 4 shows PGP, (PG)2P, PEEK, and graphite degradation curves. The residue weight loss of neat PEEK at 900 °C varies from 40 to 45%. The decomposition of PEEK and its composites occurs in two steps. The first step takes place at 550–570 °C. Within this temperature range, degradation is attributed to the breakdown of polymer chains containing ketone and ether bonds. The resulting products include carbon dioxide, water, and phenol groups. The second degradation occurs at a temperature above 600 °C. During this step, the residue is cracked and dehydrogenated, leaving thermally stable carbonaceous char27.
Wang, P. et al. Comparative study of fullerenes and graphene nanoplatelets on the mechanical and thermomechanical properties of poly (ether ether ketone). Mater. Lett. 249, 180–184. https://doi.org/10.1016/j.matlet.2019.04.092 (2019).
Processors with sustainability goals or mandates have a number of ways to reach their goals. Biopolymers are among them.
The commercial significance of the material was not immediately recognized. At the time there was not a clear understanding of the composition of materials in this chemical family, and in particular there was poor comprehension of the difference between the organic acids and their esters. Today we know that esters of organic acids are more difficult to polymerize but produce more stable products. But the distinction between acrylic acids and their esters was not well understood at the time.
In fabricated composites, the load transfer strengthens, and the ultimate tensile stress increases due to the interfacial interaction between PEEK and graphite laminates. Although the strength of PGP and (PG)2P composites lies between that of pristine graphite and pristine PEEK, it is worth noting that the crystalline form of PEEK demonstrates a higher UTS compared to neat PEEK. When samples subjected to the tensile tension in a parallel setup, more loads will be distributed to the element with the highest stiffness. In both PGP and (PG)2P composites, the graphite sheet stiffness is higher than PEEKs; as a result, more of the load will go to the graphite. It was observed that the breaking point primarily occurred in the middle region of the specimen, away from the clamping ends. During these tests, the deviation in the thickness of the specimens was found to be almost negligible, ensuring consistent results.
Gifted with extraordinary technical know how and an authoritative yet plain English writing style, in this collection of articles Fattori offers his insights on a variety of molding-related topics that are bound to make your days on the production floor go a little bit better.
Alvaredo Atienza, Á. Effect of graphene nanoplatelets and carbon nanotubes in PEEK and PEEK/carbon fiber composites (2019). https://doi.org/10.3390/polym11010124
Marcomini, A. L., Rego, B. T. & Suman Bretas, R. E. Improvement of the short-and long-term mechanical properties of injection-molded poly (ether ether ketone) and hydroxyapatite nanocomposites. J. Appl. Polym. Sci. https://doi.org/10.1002/APP.44476 (2017).
In this three-part collection, veteran molder and moldmaker Jim Fattori brings to bear his 40+ years of on-the-job experience and provides molders his “from the trenches” perspective on on the why, where and how of venting injection molds. Take the trial-and-error out of the molding venting process.
After successfully introducing a combined conference for moldmakers and injection molders in 2022, Plastics Technology and MoldMaking Technology are once again joining forces for a tooling/molding two-for-one.
One of the big challenges was developing an efficient method for manufacturing the acrylic acid esters to be used as monomers.
Acrylic polymers were developed in Germany over the course of around 70 years, despite technical and economic hurdles and battles over intellectual property and professional pride. (Photo: Evonik)
Department of Chemical and Materials Engineering, School of Engineering and Digital Sciences, Nazarbayev University, 010000, Astana, Kazakhstan
Harris, L. A Study of the crystallization kinetics in PEEK and PEEK composites [dissertation]. Univ. Birmingham (2011). http://etheses.bham.ac.uk/id/eprint/2846.
In this collection, which is part one of a series representing some of John’s finest work, we present you with five articles that we think you will refer to time and again as you look to solve problems, cut cycle times and improve the quality of the parts you mold.
During the era when many of the polymers we have discussed previously (nylon, PET, PBT, PC, acetal) were undergoing development, another member of the family that has become a mainstay in the industry was following its own lengthy path to commercialization. This was the material that has become known generically as acrylic.
Multiple speakers at Molding 2023 will address the ways simulation can impact material substitution decisions, process profitability and simplification of mold design.
Kumar, A., Verma, V. & Sharma, M. Hot pressing: A very cost-effective process for fabrication of advanced composites. Int. J. Eng. Technol. 7(3), 431–435 (2018).
A Rule-of-Mixtures graph is plotted in Fig. 5, where the weight percentage of samples and neat materials decreases due to thermal degradation. The chart illustrates that composite performance lies between the curves for neat PEEK and graphite. For samples with higher graphite volume ratio, the weight loss is less due to the better thermal resistance of graphite under higher temperature, according to the rule-of-mixtures. Experimental data showed a higher residual weight percentage than expected, which can be explained by changes in the microstructure of the samples due to the crystallization processes.
By submitting a comment you agree to abide by our Terms and Community Guidelines. If you find something abusive or that does not comply with our terms or guidelines please flag it as inappropriate.
Bakar, M. A., Cheang, P. & Khor, K. A. Mechanical properties of injection molded hydroxyapatite-polyetheretherketone biocomposites. Compos. Sci. Technol. 63(3–4), 421–425. https://doi.org/10.1016/S0266-3538(02)00230-0 (2003).
Sengupta, R., Bhattacharya, M., Bandyopadhyay, S. & Bhowmick, A. K. A review on the mechanical and electrical properties of graphite and modified graphite reinforced polymer composites. Prog. Polym. Sci. 36(5), 638–670. https://doi.org/10.1016/j.progpolymsci.2010.11.003 (2011).
In 1892, Georg Kahlbaum, a professor at Basel University, carried out research on methyl acrylate, which he polymerized into polymethyl acrylate, the precursor to our PMMA of today. The initial polymers were not of very high molecular weight, taking the form of high-viscosity, gelatinous materials whose utility was not apparent at first. But it was noted that as the polymer formed, the clear monomers remained clear in polymerized form.
Table 5 summarizes the values of hardness and Young's modulus for three thin films: PEEK, PGP, and (PG)2P. An average value of 20 indentations with their standard deviation is depicted for each sample. The results show that (PG)2P has a higher value for both elasticity and hardness modulus than PGP and PEEK. Thus, it can be concluded that increasing the volume of graphite in the composite makes the material stiffer. Also, PEEK's lowest modulus of elasticity and hardness demonstrated that it is more ductile than composites In the previous study conducted by Puértolas et al.30, it was concluded that the addition of GNP enhances the surface hardness and tribological properties of PEEK-based materials. Their results obtained from tensile and nanoindentation tests indicated an increase in Young's Modulus, a decrease in tensile strength, and a slight increase in hardness for the GNP/PEEK composite.
ABOUT THE AUTHOR: Michael Sepe is an independent materials and processing consultant based in Sedona, Ariz., with clients throughout North America, Europe, and Asia. He has more than 45 years of experience in the plastics industry and assists clients with material selection, designing for manufacturability, process optimization, troubleshooting, and failure analysis. Contact: (928) 203-0408 • mike@thematerialanalyst.com
Aware of the success of natural and synthetic rubber, Rohm sought to produce an ester-based rubber using the mechanism of vulcanization. In 1912 Röhm received a German patent for the “process for manufacturing a product with the properties of vulcanized rubber.” A special rolling mill was installed at Rohm & Haas to carry out the vulcanization process. But the patent was not technically viable because vulcanization relies on unsaturated sites where the sulfur can attach chemically to create the crosslinked structure. Röhm did not realize that the ester-based polymers were saturated structures that could not be vulcanized.
Zak, S., Trost, C. O. W. & Kreiml, P. Accurate measurement of thin film mechanical properties using nanoindentation. J. Mater. Res. 37, 1373–1389. https://doi.org/10.1557/s43578-022-00541-1 (2022).
Join Wittmann for an engaging webinar on the transformative impact of manufacturing execution systems (MES) in the plastic injection molding industry. Discover how MES enhances production efficiency, quality control and real-time monitoring while also reducing downtime. It will explore the integration of MES with existing systems, emphasizing compliance and traceability for automotive and medical sectors. Learn about the latest advancements in IoT and AI technologies and how they drive innovation and continuous improvement in MES. Agenda: Overview of MES benefits What is MES? Definition, role and brief history Historical perspective and evolution Longevity and analytics Connectivity: importance, standards and integration Advantages of MES: efficiency, real-time data, traceability and cost savings Emerging technologies: IoT and AI in MES
The results indicated that (PG)2P exhibited a 48.5% decrease in Young's modulus, while PGP showed a 42.7% decrease compared to neat graphite. A reduction in modulus can be explained by the low modulus of PEEK and its moderate ratio in the fabricated samples, which leads to the high interface with graphite laminate. Similar trends in the modulus of PEEK graphite composites have been reported in studies involving melt-blending28. Additionally, the hot press method employed at high pressure facilitated strong adhesion between the layers of the composite. As a result, efficient load transfer was observed between the graphite and PEEK layers.
Nanomechanical analysis was performed using a Hysitron TI Premier Nanoindenter (Bruker). Flat sheet composites were tested. For each specimen, 20 nanoindentations were made with maximum applied force of 10 mN. The 100 nm diamond-tip Berkovich indenter was used to perform the tests. Specialized software was employed to calculate the hardness and modulus of elasticity of the specimens using the Oliver-Pharr method21,22. All nanoindentation tests were performed at a constant temperature of 20 °C.
Figures 8, 9 and 10 depict typical load–displacement curves of PEEK, PGP and (PG)2P respectively. A slight scatter can be observed in the measured Young's modulus profiles due to the friction between the indenter and samples. The depth values in the load-depth curves correspond to the extent of indenter penetration into the material during the nanoindentation test. The observed shift towards lower depth values in the case of (PG)2P indicates that this composite exhibit greater resistance to indentation compared to PGP and PEEK. This shift can be attributed to the increased number of graphite layers in the fabricated composites. Thus, the values above the penetration depth of 820 nm and below 520 nm were not considered to avoid an error during the indentation tests33.
(PG)nP composites were prepared by the hot pressing method, as illustrated in Fig. 1. The associated equipment setup is shown in Fig. 2. Aluminum foil was employed on both the bottom and top surfaces of the press to prevent adhesion between the heating plates and the polymer. First, the stainless-steel bulk was heated to 330 °C, close to the melting temperature of PEEK. In-situ thermocouples measured the temperature. After that, a multilayer stack of thin films (PG)nP was rapidly introduced, and 400 bar pressure was applied for 10 min to form a laminate. Then, the laminate was maintained under pressure and naturally cooled to the below-glass transition temperature of PEEK. Two different laminates, PGP and (PG)2P, of size 100 × 100 mm2 were prepared. The weight and corresponding volume fractions of graphite in (PG)nP composites are presented in Table 2. They were calculated based on the thickness of the graphite and PEEK sheets.
Say “manufacturing automation” and thoughts immediately go to the shop floor and specialized production equipment, robotics and material handling systems. But there is another realm of possible automation — the front office.
August 29-30 in Minneapolis all things injection molding and moldmaking will be happening at the Hyatt Regency — check out who’s speaking on what topics today.
GETTING A QUOTE WITH LK-MOULD IS FREE AND SIMPLE.
FIND MORE OF OUR SERVICES:
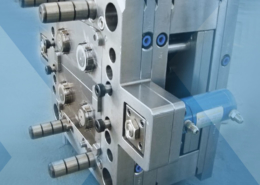
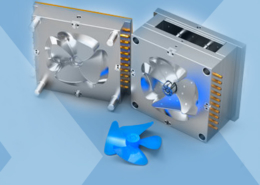
Plastic Molding

Rapid Prototyping
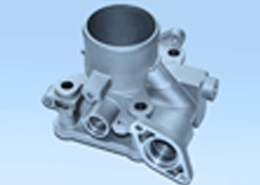
Pressure Die Casting
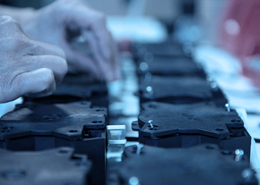
Parts Assembly
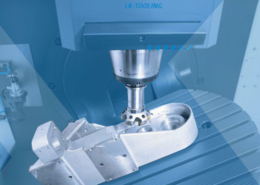