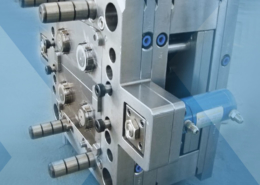
Plastic fuel injector wins SPE award - automotive plastic mold
Author:gly Date: 2024-09-30
Dr. Stefan Gräter (left) and Dr. Andreas Kicherer (right) showing a sample of pyrolysis oil and plastic produced from it in front of the steam cracker.
“The pilot projects with customers from various industries show that products made with chemically recycled raw materials exhibit the same high quality and performance as products made from primary materials. ChemCycling, which uses a mass balance approach to mathematically allocate a share of the recycled material to the final product, can help our customers to achieve their sustainability goals,” said Jürgen Becky, Senior Vice President Performance Materials. The certified products are indicated with the addition of “Ccycled” to their name. The prototypes presented at the press conference are part of the ongoing pilot phase of the ChemCycling project.
To move from the pilot phase to market roll-out, however, various issues will need to be resolved. The existing technologies for transforming waste plastics into recycled raw materials must be advanced and adapted for the use at industrial scale, in order to ensure the consistently high quality of the pyrolysis oil. BASF is currently investigating various options for supplying the company’s Production Verbund with commercial volumes of pyrolysis oil in the long term. Besides the technical issues, economic aspects also play a role. For chemical recycling to find acceptance in the market, regulators must also recognize the process officially as recycling. Within this framework, they have to define how chemical recycling and mass balance approaches can be included in the calculation of recycling rates required by law.
BASF’s partners in the ChemCycling project: Jaguar Land Rover, Storopack, Südpack, and Schneider Electric; Promising pilot phase, but continued technological and economic challenges as well as the need for regulatory development.
The process, which utilizes molding equipment designed and developed by Piper Plastics, allows the company to mold filled or unfilled high-performance thermoplastics with isotropic mechanical properties. “This capability is especially beneficial for large CNC machined parts that were historically limited to extruded or compression molded stock shapes,” explained Dave Wilkinson, Materials Engineering Manager, in a prepared statement. “In comparison to extrusion and compression molding, this new process yields parts that have higher strength—typically 15 to 20% stronger than extruded shapes and 50% stronger than compression molded shapes—with more consistent mechanical properties.”
The significant potential of chemical recycling was confirmed by the consulting firm McKinsey in a December 2018 study: If established recycling processes are combined with new ones such as chemical recycling, the experts believe that a 50% reuse and recycling rate for plastics worldwide can be reached by 2030 (today: 16%). The share of chemical recycling could then rise from 1% currently to around 17%, which is equivalent to the recycling of around 74 million metric tons of plastic waste.
Jaguar Land Rover (JLR), a leading automotive manufacturer, developed a plastic front-end carrier prototype for its first electric SUV, the I-Pace, out of Ultramid B3WG6 Ccycled Black 00564. “As part of our commitment to accelerate closed-loop manufacturing across our operations, we are always looking for advances in technology that will help to reduce waste,” said Craig Woodburn, Global Environmental Compliance Manager at JLR. “The ability to convert consumer waste into safe, quality parts for premium products through the ChemCycling process is an important step in advancing our ambition to deliver a zero-waste future.”
An increasing number of companies in the plastics industry are working on improving the recyclability of plastics and thus helping to create a circular economy. One way that BASF is contributing is the ChemCycling project: At the end of 2018, the company first used pilot volumes of pyrolysis oil derived from plastic waste as a feedstock in its own production. At a press conference in advance of K 2019, four partners have showcased the first prototypes that were created during the pilot phase of the project.
The technology also allows Piper to offer small batch runs for mating the right polymer or blend for an application. “Distributors typically only carry about 50 types of engineering plastics, but with this technology we can mold custom blanks from more than 3,000 polymers and compounds, or develop a compound specifically for an application,” said White.
“With the ChemCycling project, BASF is aiming to process pyrolysis oil derived from plastic waste that currently cannot be recycled, such as mixed or contaminated plastics. If we are successful in developing the project to market readiness, ChemCycling will be an innovative complement to existing processes for recycling and recovery to solve the plastic waste problem,” said Stefan Gräter, head of the ChemCycling project at BASF.
Piper Plastics (Chandler, AZ) reports that it has developed a proprietary high-pressure molding technology that yields near-net-shape polymers up to 2 inches thick without porosity, voids or sinks.
Stephen has been with PlasticsToday and its preceding publications Modern Plastics and Injection Molding since 1992, throughout this time based in the Asia Pacific region, including stints in Japan, Australia, and his current location Singapore. His current beat focuses on automotive. Stephen is an avid folding bicycle rider, often taking his bike on overseas business trips, and is a proud dachshund owner.
Schneider Electric, a leader in the digital transformation of energy management and automation, manufactured a circuit breaker from chemically recycled Ultramid. “We actively assess the ability of secondary raw materials, such as recycled plastics, to meet our demanding quality standards, and stringent industry regulations and norms. We rely on BASF expertise to demonstrate the end-to-end sustainability benefits while offering an appealing cost. We are hopeful this experimentation with BASF will open room for more circular innovations in Energy Management and Distribution,” said Xavier Houot, Schneider Electric’s Senior Vice President Group Environment, Safety, Real Estate.
The process is suitable for large parts and weights up to 6 pounds per blank, with large and varying wall thicknesses and complex geometries. “Near-net shape is effective for parts that cannot be produced using standard injection molding because the cross sectional area is too thick,” said Wilkinson. “This new technology has opened up exciting opportunities in the semiconductor, oil and gas, medical equipment and aerospace markets.”
Packaging innovations made of Styropor P Ccycled from Storopack: Temperature-controlled 96h-box for medical applications.
“Our ChemCycling project is a good example of how BASF is working with partners on solutions to the key challenges of the 21st century,” said Dr. Andreas Kicherer, sustainability expert at BASF. Besides ChemCycling, BASF is involved in many other projects and initiatives that strengthen the idea of the circular economy and prevent plastics from entering the environment. For example, BASF’s product portfolio includes ecovio, a certified compostable plastic partly based on renewable raw materials.
Storopack, a globally active supplier of protective packaging and technical molded parts, used Styropor P Ccycled to make insulation packaging for temperature-sensitive pharmaceutical products as well as boxes for transporting fresh fish and protective packaging for electronic devices. “We were particularly impressed by the fact that Styropor P Ccycled can be used in food packaging. There are already various recycling options for Styropor, and ChemCycling helps raise the recycling share even further,” said Storopack’s Chairman of the Management Board, Hermann Reichenecker. Storopack and BASF are thus forging a new path in the circular economy.
Südpack, a leading producer of film packaging in Europe, produced a polyamide film and a polyethylene film that were processed into specially sealed packaging for mozzarella. Until now, multi-layer packaging has usually been considered to be only recyclable to a limited extent. “Film packaging must fulfill important roles: product protection, hygiene, and shelf life while using a minimum amount of plastics. That is why it is made up of several materials and layers with various properties and barriers. Through innovations such as ChemCycling we come closer to solving the problems associated with recycling of flexible packaging,” said Johannes Remmele, Managing Partner of Südpack.
A subsidiary of Quadrant Engineering Plastic Products, Piper Plastics supplies high-performance polymer materials and precision machined plastic components and assemblies to a range of industries.
A major reason for developing the new technology was to save costs when machining finished parts from expensive, high-performance materials such as PEEK, PAI or TPI, said the company. “The molds are inexpensive, since we are only molding a near-net shape that will be machined after molding,” said Bruce White, Vice President, Piper Plastics. “Because it’s close to the final part, a near-net shape requires less machining. Less machining means less waste, which is an important consideration for green and sustainable programs.”
GETTING A QUOTE WITH LK-MOULD IS FREE AND SIMPLE.
FIND MORE OF OUR SERVICES:
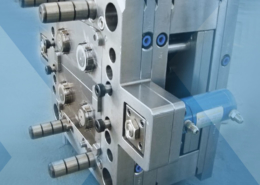
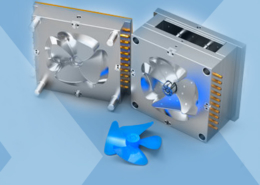
Plastic Molding

Rapid Prototyping
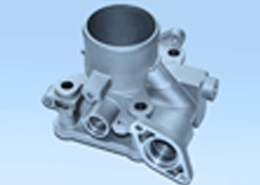
Pressure Die Casting
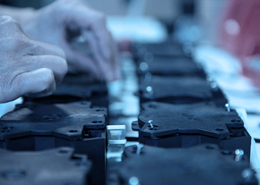
Parts Assembly
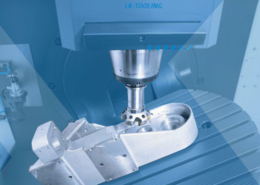