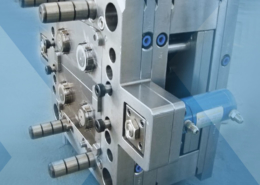
Plastic Camshaft Module Reduces CO2 Emissions - aluminum molds for plastic
Author:gly Date: 2024-09-30
Moldgenix adheres to scientific injection molding principles in producing tight-tolerance plastic parts for medical, dental, industrial, electronics, and consumer applications.
“In the real world, I’m not going to be designing my own mold and I’m not going to be cutting my own mold. But I am going to be designing my own parts, and if I don’t know what constraints there are around it, I’m not going to end up designing a very good part,” Stavisky said.
We want to provide announcements, events, leadership messages and resources that are relevant to you. Your selection is stored in a browser cookie which you can remove at any time using “Clear all personalization” below.
While other classes tend to focus on the manufacturing process itself, this course is about designing to fit the manufacturing process, Huynh said. It’s a set of lessons fraught with complications that foster flexibility. The payoff, however, has more impact than the physical products suggest.
“Having the chance to actually try it, to go beyond the theory and make something, is really critical to understanding what it takes to manufacture these parts,” said Marlo Kohn, lecturer in mechanical engineering and instructor for the course.
In an advanced design and manufacturing course, students learn that the ubiquitous plastic objects made by injection molding are deceptively hard to make.
Each student devises a product that is interesting or useful enough to benefit from being highly reproducible. The results in winter quarter were diverse: an insulin vial protector, a screwdriver with interchangeable magnetic heads, a portable spring that makes it easier to use chopsticks, a necklace organizer and a shoe tag that a person can slide onto laces to add some flair to footwear.
Those products are ubiquitous, but deceptively hard to make, students learn in the engineering class ME325: Making Multiples: Scaled Manufacturing Tooling. In it, students design and make molds for their own mass-produced parts.
Huynh’s own work tested the line between parts that could be copied a few times and those that could be duplicated in the dozens. His original plan was to make a fountain pen, decorated with intricate ribs. After designing the fragile and delicate mold components this piece would require, he realized making many wasn’t feasible. He changed course, instead creating a screwdriver with a design inspired by his original project.
Once students in ME325 have completed the design and manufacture of their molds, each individual part might take only 30 seconds to mold. This speed of production belies the challenges and amount of the time that went into designing the part and creating the tooling.
New owner Haartz Family Holdings is the investment branch of the Haartz family, which owns Haartz Corp., a global supplier of convertible toppings and interior surface materials for the automotive sector. It is based in Acton, MA, with additional manufacturing operations in Mannheim, Germany, and offices in Japan, China, and Mexico. The investment arm also has holdings in Peak Performance Compounding.
The Informa Markets Engineering network of B2B media sites includes Design News, Battery Technology, Medical Device & Diagnostic Industry (MD+DI), Packaging Digest, PlasticsToday, and Powder & Bulk Solids.
In the design classes that students take before Making Multiples, they are free to make just about anything they want, exploring many media and a wide range of techniques. Making Multiples focuses on a single medium and technique while urging students to give their projects the utmost forethought in order to experience what it’s like to mass-produce an object they created from start to finish.
A change in ownership at Total Molding Services, a contract manufacturer supplying injection molding, tooling, and assembly services, has spawned a new name for the Quakertown, PA–based company. The new name, Moldgenix, implies via the Latin-derived word “genix,” the creation of molded products and better reflects the company’s innovative spirt and future-forward vision, it said in making the announcement today.
The transition to Moldgenix is supported by a substantial investment in three primary areas — processes, talent, and technology, said the press release. The Moldgenix brand will be rolled out across all company materials and communication channels.
Given the prevalence of injection molding, knowledge about this process could give these students a clear advantage in a wide variety of design careers. But the most satisfying outcome of this class, for both students and instructors, is probably the hard-won success can be shared directly with classmates, friends and family.
In each case, students sketched prototypes, printed them with a 3-D printer, machined the aluminum molds and injected the molds with molten plastic of their chosen flexibility and color to create final products.
“When my first parts came out, I said, ‘Man, this looks so simple!’ But so much work and thought went into the mold and it was quite complicated to make,” said Katya Stavisky, a master’s student in mechanical engineering who made the shoelace tags last quarter. “Now, looking around at things, like the tools we use, I think, ‘Wow, the tooling for this must have been really difficult.’”
“Having the chance to make more than one of something gives students experience that might be useful to them in their career but also is really incredible to create one of something – one mold – and then get to share your design with all of your friends,” Kohn said. “I think that’s a very empowering experience for students because they realize that they can make something that can be out in the world as a real object.”
Plastic objects made by injection molding are abundant and, for many of us, a constant presence in our everyday lives. Your phone case, toothbrush and the keys on your computer are all probably the result of mass production, which involves injecting molten plastic into molds.
“In other classes at the Product Realization Lab, you only make one part and you could polish it for hours,” said Brian Huynh, a master’s student in mechanical engineering. “But in the real world you’re going to be making hundreds of thousands or millions. So there’s debugging that goes with making your mold, and then there’s the injection-molding process, which makes you realize, I have to make it look good enough – just good enough – where, if I make a hundred of them, most of them look great.”
GETTING A QUOTE WITH LK-MOULD IS FREE AND SIMPLE.
FIND MORE OF OUR SERVICES:
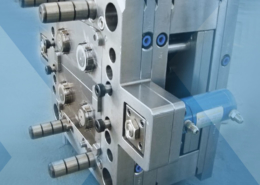
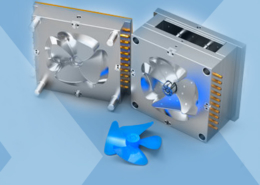
Plastic Molding

Rapid Prototyping
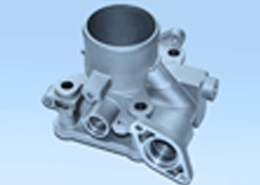
Pressure Die Casting
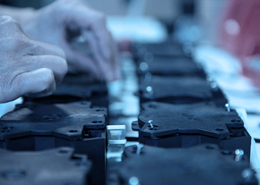
Parts Assembly
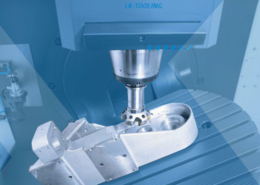