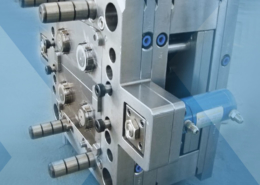
Oxford Nanopore Technologies set for up to £60M injection from investment
Author:gly Date: 2024-09-30
That the question that [Precious Plastic] asks, and by providing a centralized resource for individuals and communities looking to get into the plastic recycling game, they hope to put a dent in the worldwide plastic crisis. One of their latest projects is showing how plastic trash can be turned into functional iPhone cases with small-scale injection molding.
Tool and mould making in China is benefiting from the positive development of its customer industries. Here we provide an overview of the most important players in the market.
How many factories are in the developed world and have these high standards. I live in China and work in the area of plastics recycling and I can tell you right now that many factories are not meeting standards and there is no “formal” recycling system in place. Since the plastic import ban (which btw makes localised solutions even more important) this is beginning to change in more economically thriving areas of the country e.g. Shanghai, Shenzhen etc. but there is a lot of work to do. Note: Very good and highly developed factories do exist in China and if navigated correctly it is a wonderful place to produce.
I hereby consent to Vogel Communications Group GmbH & Co. KG, Max-Planck-Str. 7/9, 97082 Würzburg, Germany, including any affiliated companies according to §§ 15 et seq. AktG (hereafter: Vogel Communications Group) using my e-mail address to send editorial newsletters. A list of all affiliated companies can be found here
I understand that I can revoke my consent at will. My revocation does not change the lawfulness of data processing that was conducted based on my consent leading up to my revocation. One option to declare my revocation is to use the contact form found at https://contact.vogel.de. In case I no longer wish to receive certain newsletters, I have subscribed to, I can also click on the unsubscribe link included at the end of a newsletter. Further information regarding my right of revocation and the implementation of it as well as the consequences of my revocation can be found in the data protection declaration, section editorial newsletter.
In case I access protected data on Internet portals of Vogel Communications Group including any affiliated companies according to §§ 15 et seq. AktG, I need to provide further data in order to register for the access to such content. In return for this free access to editorial content, my data may be used in accordance with this consent for the purposes stated here.
Listed on the Shenzhen Stock Exchange since 2010, CHT supplies customers in China, Germany, the USA, Japan, England, Brazil, Switzerland and many other countries around the world.
The video after the break goes into intricate detail about the process involved in creating the 3D CAD files necessary to make the injection molds. Even if you don’t plan on recycling milk jugs at home, the information and tips covered in the video are extremely helpful if you’ve ever contemplated having something injection molded. The video even demonstrates a neat feature in SolidWorks that lets you simulate how molten plastic will move through your mold to help check for problem areas.
So again, I am all for encouraging people to do this. I just don’t think selling the idea as ‘saving the environment’ is necessarily honest or correct.
There are also similarities to Europe in the tool and product categories. The three most important fields of tool and mould making in China are:
https://hackaday.com/2016/06/11/new-cnc-machine-diy-machinable-wax/ , https://hackaday.com/2017/12/30/fresh-baked-plastic-tiles-for-all/ , https://hackaday.com/2015/02/21/turning-plastic-milk-jugs-into-a-useful-tool/ , https://hackaday.com/2010/08/05/recyclebot-digests-milk-jugs-to-feed-makerbot/
Naturally, we always handle your personal data responsibly. Any personal data we receive from you is processed in accordance with applicable data protection legislation. For detailed information please see our privacy policy.
That’s because, you need to make money to cover the time and upkeep of yourself and the tools. You make that money through the economy. Since the economy is services-based (>80%) it means your efforts are largely not producing new value but consuming it, because the way you make money is by helping other people consume resources.
FAW Tooling's customers from the automotive industry include more than ten renowned manufacturers from Germany and abroad, including
etc etc etc. the jist of most of the articles I’ve seen posted around here is that what you’ll end up with is some pretty inferior stock. if you where concerned about upcycling the materials you’d be doing so at a loss because you’d have to mix in higher quality stock and properly mix it in with the mulch so it blended adequately. with all the inks pigments and general discrepancies between any two shopping bag though you’ll end up with densities that wouldn’t be very good for much of anything- well aside from a plastic mallet made of milk jugs but that’s already covered.
The group itself is again divided into a number of subsidiary companies and spread over several locations in China. It dominates various sectors of the market with its offshoots FAW Mold Tianjin, FAW Mold Qingdao or Huaxiang Lightweight Technology Co., Ltd. among others, with state-of-the-art equipment and production methods.
Those bags don’t seem very UV stable (tend to go brittle and crumble when left out in the sun), but maybe useful indoors or if kept in a dark area.
On another note, the above comments in this section prove exactly what is wrong with the sustainability community, people spend so much time talking about what’s better or worse that no one actually does anything. Emissions in X vs. emissions in Y. Frankly, no one cares about emissions and the big companies and starts ups that use these materials don’t wait around calculating if one options emits 0.00001 CO2e than another. They start, the fail, they redo, they prototype and the achieve success. That’s why I love precious plastics, they have launched a community and I guarantee the product in 10 years will be so much more advanced than the current MVP. If he had sat around having conversations like the above he would probably still be calculating the lifecycle analysis and debating the difference between boat vs. truck logistics costs to the environment….. but I guess a lot of people are paid to chat and not to do.
The greater cost to produce the item then translates into greater energy and resource use as translated through the economy, which means by recycling the object you actually consume more than you save.
The beginnings of this tool and mould maker in Shenzhen, southern China, whose factory halls look just as sparkling clean and ultra-modern as those of any competitor in Germany or Japan, date back to 1993. That was when Hu Zuohan, a graduate of Beijing's prestigious Qinghua University, and his partner Ryan Huang founded the Shenzhen Brother Mold Factory.
Newsletter content may include all products and services of any companies mentioned above, including for example specialist journals and books, events and fairs as well as event-related products and services, print and digital media offers and services such as additional (editorial) newsletters, raffles, lead campaigns, market research both online and offline, specialist webportals and e-learning offers. In case my personal telephone number has also been collected, it may be used for offers of aforementioned products, for services of the companies mentioned above, and market research purposes.
Main reason is, the labor and other expenses going to make an iphone case from scrap are greater than the value of the product.
This emerging Chinese company builds stamping and forming tools for the automotive industry. These are in turn used to produce chassis, seats, roofs and other vehicle body parts.
Also, lets not forget the duality of sustainable vs durable. On the one hand you have biodegradable plastics, which wont last hundreds of years if left in the environment, but these are also much more prone to falling appart during heating. And on the other hand you have the plastics that you can recycle, but which will last forever in the scrapheap.
Imprint Cookie-Manager About Media Subscription cancellation Privacy General Terms and Conditions Help AI-Guidelines
Fully automated milling lines, foreign professionals such as the German manager Marcus Schlundt as division manager, an IPO in Shenzhen in 2015, and ever more investments in state-of-the-art machines and software solutions have ensured that Silver Basis now exports a large part of its products abroad, especially moulds for the automotive industry.
In order to reclaim the value of the plastic, it’s often not even useful to collect it, because the collection costs resources. That’s a good way to gauge whether the recycling is worth it: if they pay you money, the material must be worth more than the money. If they demand you to sort/collect/return the items for nothing, it’s probably not worth recycling and should be burned with regular trash.
The fast-growing company employs more than 200 engineers and 220 highly specialised toolmakers, who have 129 of their own CNC machines and 17 different presses up to a load of 2,000 tonnes at their disposal. The company's main foreign markets are in Europe and North America.
The company's origins in tool and mould making date back to 1958, the first decade of the People's Republic proclaimed by Mao Zedong on Tiananmen Square on 1 October 1949. From the beginning, then called "State Owned Factory No. 132", Chengfei Group specialised in the construction of military and civil aircraft.
Best bet is to gather a bunch of them and drop them off in the entryway of your nearest Wal-mart. They have a collection bin.
In recent years, the Chinese government has published a number of strategy papers and set in motion support programmes to promote toolmaking and mechanical engineering. At the same time, the titles of these papers and programmes reveal that the aim is still to catch up with the technologically superior foreign competition.
This large Chinese manufacturer of tools and plastic and injection moulds started in 1997 as a three-man operation with the company name Changhua Wire-Cutting Processing Shop, but has since experienced a growth story that is probably unique in the industry.
The largest private company in the Chinese tool and mould industry has only existed under this specific name since 1996, but the company already has a history of more than 40 years under other names and in other constellations.
The use of virtual twins with the aid of CAE simulations is just as much a part of the offering here as advanced cold stamping tools for steel or aluminium, thermoforming and complete tryout and "one-stop" production solutions for customers from the automotive industry and other areas of the manufacturing industry.
With the mold completed, all that’s left is to bolt the two sides together and inject the liquid plastic. Here [Precious Plastic] shows off a rather interesting approach where they attach the mold to a contraption that allows them to inject plastic with human power. Probably not something you’d want to do if you’re trying to make thousands of these cases, but it does show that you don’t necessarily need a high tech production facility to make good-looking injection molded parts.
Below we present six of the currently most successful of these emerging "national champions" in China's tool and mould industry.
This portal is a brand of Vogel Communications Group. You will find our complete range of products and services on www.vogel.com
In addition to tools and moulds for building cars (including Toyota, Volvo, Geely and Lotus) and lithium batteries, it also produces those for energy storage and CNC machine parts.
Unlike in Europe, however, business is now developing very positively in several downstream industries of tool and mould making in China, especially in the areas of e-mobility, energy storage and car batteries as well as in the communications industry. So the outlook has brightened again for the "mother of all industries" in China, without which, as we know, nothing works. At least not in the manufacturing industry.
At the end of last year, the Qichacha database already counted 221,141 Chinese companies active in tool and mould making. The vast majority of these, however, are smaller companies with only a few hundred employees, which are only active in the lower to medium price segment of products and are by no means eligible for orders in the premium sector, for example in the automotive industry.
But… before I can be convinced that home plastic recycling can be a useful tool for helping the environment I would need to have a couple of questions answered. First, how does the energy efficiency of some guy in his garage recycling plastic compare to that of a high volume factory? I suspect it’s pretty poor. Second, how about emissions? Factories (in the developed world) are regulated, regularly inspected and usually employ high tech scrubbing technologies on their emissions. The garage maker who blows air through a box of aquarium charcoal is probably ahead of the curve when it comes to non-professionals.
“Factories (in the developed world) are regulated, regularly inspected and usually employ high tech scrubbing technologies on their emissions.”
Specialising in tools for the electronics industry, just six years later CHT's more than 2,000 employees were supplying internationally renowned customers such as Konica Minolta Inc, Brother Industries, Thermo Fisher and the Chinese mobile phone and electronics giant Xiaomi.
We imagine you’ve heard this already, but waste plastic is a problem for the environment. We wrap nearly everything we buy, eat, or drink in plastic packaging, and yet very little of it ends up getting recycled. Worse, it doesn’t take a huge industrial process to melt down a lot of this plastic and reuse it, you can do it at home if you were so inclined. So why aren’t there more localized projects to turn all this plastic trash into usable items?
A current example of this is the new "Action Plan for the Further Improvement of Product, Engineering and Service Quality in the Moulding Industry (2022 - 2025)". Where something needs to be "improved" with such calls from the central planners in Beijing, there is still a lot of work to be done.
This giant among the Chinese state-owned companies in the tool and machine building sector is a wholly owned subsidiary of the FAW Group. The FAW Group is known in Germany as one of Volkswagen's joint venture partners in China. The company has been around for more than 70 years, but was last restructured and renamed in 1997.
We regularly buy H2O2 for the pool and several other stuff in blue ones (we had also acetone and HCl in blue ones). I have uncolored for water, one also contained H2O2 before. I also have black and orange ones for gasoline. So there seems no color code.
One more thing – you can identify the aluminium alloy with an XRF machine (expensive, but labs have them), good luck IDing what the composition of a plastic polymer is :P
Today, TQM supplies customers in China and worldwide. An important focus here is also the automotive industry. Tools for the production of inner and outer skin parts of car bodies and complete equipment groups and processes are offered.
One of the 33 subsidiaries, Shenyang TQM Aviation Parts Co., Ltd. is significantly involved in the construction of the first airliner C919 manufactured in China and researches, develops, produces and assembles components for all kinds of aircraft.
That’s why for a backyard aluminum foundry melting cans you need something to crush many cans together into blocks. That way the metal inside the block will heat and melt with minimal air to oxidize it. Adding to the problem is any leftovers of the contents, especially if still wet. Cleaning and drying lots of pop or beer cans takes lots of time and effort.
Arguably small scale aluminum recycling has similar drawbacks to plastic recycling w/o virgin material added. Cans/thin sheet are notoriously bad since they have all that surface area to oxidize without some process controls most backyard foundries ignore. It’s just that aluminum impurities are insoluble in the melt making it easier to retain material properties if you’re willing to accept comparatively high waste losses.
According to its own information, the company is now the "number 1 tool exporter in China", although it is left open whether this is a question of the quality or quantity of exports. What is certain, however, is that Vision Tool & Mould has developed an impressive product range. It ranges from hot and cold forming tools to welding fixtures of all kinds to tandem and compound injection moulds.
First, let me say, this does not in any way mean I am against the idea. I love the concept of encouraging individuals to make more stuff themselves. I very much think that encouraging making over consumerism will give us a much more creative, knowledgeable and self sufficient population that ultimately will do greater things and make a better world.
In 2003, CHT won the "Shenzhen High-Tech Enterprise Award", in 2009 the "National High-Tech Award" of the People's Republic of China. A complete product line for medical consumables, offered by a subsidiary in Hong Kong, is also part of the toolmaker's range.
There are many problems with plastic recycling. I wanted to make 3D filament from recycling and that is when the problems hit you in the face. 1)Our current system for identifying the type of plastic is totally inadequate. #5 plastic is a wide variety of plastics 2)Unlike Consumer food grade Aluminum, most plastics are blends. The same additives that give plastics some very beneficial properties also cause problems when you try to recycle them. 3)The plastic degrades when you heat it. The additives cause problems when you heat them and as a result you don’t always end up with what you start out with. 4)Outgassing from the heated plastic is a real crap shoot. What chemicals are you subjecting yourself to when you heat these up?
By using our website and services, you expressly agree to the placement of our performance, functionality and advertising cookies. Learn more
None of the above is a big problem for commercial foundries because they use electric arc furnaces with inert gas and synthetic cryolite flux to keep the aluminum from oxidizing.
By clicking on „Subscribe to Newsletter“ I agree to the processing and use of my data according to the consent form (please expand for details) and accept the Terms of Use. For more information, please see our Privacy Policy.
Also the Aluminium oxides are the same as the raw material used to make it in the first place. If you just chuck all your scrap Aluminium into the smelter it goes through the process much faster using less energy. The purity doesn’t matter that much.
Chengfei Integration now combines, after a series of restructurings, not only the mould making equipment of Chengfei Group, but also many machines and technologies of carmaker Geely, as well as R&D centres and talents from Nanjng University of Aeronautics and Northwestern Polytechnical University.
This project reminds us of the tiles made of HDPE plastic with nothing more exotic than what you’d find in the average kitchen. Projects like these really drive home the idea that with the right hardware individuals can turn trash into usable products.
The plastic waste have to be sorted, PE, PET, etc. so the right temperature can be used and you don’t mix chlorated plastics in there like Nylon. Undyed PE, like used in plastic Jerry cans and the likes, is quite pure. Black plastics have usually already been recycled once. So the trick is to find the right mix of undyed higrade and lower grade plastic to grt satifactory properties. The problem with plastics, even if they are not heated to more than their recomended temperature for casting, is that some of the polymers breaks up, and the material gets a little more brittle. If a correct amount of virgin material is used and time and temperature is observed, satisfactory results can be achieved.
* Henrik Bork is Managing Director at Asia Waypoint, a Beijing-based consulting agency specialising in China. "China Market Insider" is a joint project of the Vogel Communications Group, Würzburg, and Jigong Vogel Media Advertising in Beijing.
He, that’s me! Thanks for sharing :D Feel free to ask questions here or here: https://davehakkens.nl/community/forums/topic/make-a-plastic-phone-cover-using-cnc-milling/
Nope. The UK and the rest of the EU has the same color/usage regulations as us. Red for leaded gas, green for unleaded, etc.
Once you’ve designed your mold on the computer, you need to turn it into a physical object. If you’ve got a CNC capable of milling aluminum then you’re all set, but if not, you’ll need to outsource it. [Precious Plastic] found somebody to mill the molds through 3DHubs, though they mention in the video that asking around at local machine shops isn’t a bad idea either.
At the same time, however, with the active help of the government, a number of "national champions" are emerging in this industry in China. With their high degree of automation, IT technologies such as CAD, CAE or CAM and 3D design tools, and equipped with a lot of money from IPOs, they are now very close to Western companies in terms of quality and precision in manufacturing.
Chengfei Integration had emerged in 2014 from a subsidiary of AVIC, i.e. the Aviation Industry Corporation of China, a state-owned aerospace conglomerate.
A series of investments, restructuring, as well as a strategic partnership with the NGK Group from Japan have turned it into one of China's leading competitors in tool and mould making to this day.
Now a painstaking recovery has begun, but it is not progressing nearly as fast as many had hoped. In this respect, the companies in China are not much different from the European industries in this segment.
The tool and mould industry in China had suffered greatly from the Corona measures imposed by Beijing in recent years. In 2020, the first of the three pandemic years, the total value of the industry in the People's Republic had fallen by around 34.5 billion euros, which corresponded to a decline of 11.3 percent compared to the previous year.
GETTING A QUOTE WITH LK-MOULD IS FREE AND SIMPLE.
FIND MORE OF OUR SERVICES:
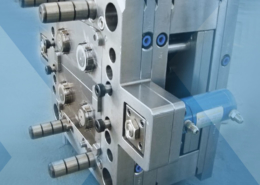
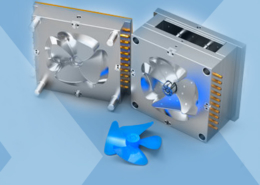
Plastic Molding

Rapid Prototyping
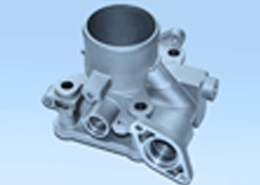
Pressure Die Casting
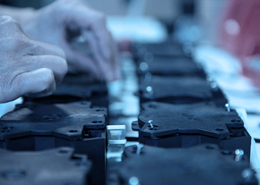
Parts Assembly
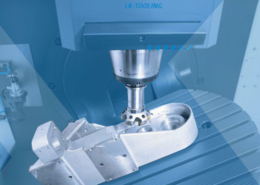