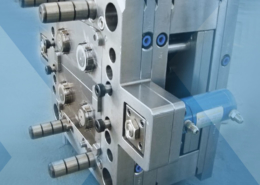
Overmolding Overhaul - two shot molding
Author:gly Date: 2024-09-30
So far, Unilever and Serioplast have tested about 15 bottle designs produced with the molds. Serioplast first created a standard mold design and print preparation and then modified the mold cavity for each unique bottle design.
Kate Bertrand Connolly has been covering innovations, trends, and technologies in packaging, branding, and business since 1981.
“Our strategic and ambitious expansion plans in the medical field start in Singapore, with future plans to extend our reach into the greater Asean region. We have plants located in Singapore, Malaysia and China, and are actively exploring opportunities in emerging markets like Indonesia, Thailand, Cambodia and Vietnam to meet the growing demand for manufacturing in those regions,” Seow said.
From automated robot doctors to water filters, performance drills to medical endoscopes, the engineering and manufacturing of these items involve the inception of ideas, rigorous testing and the relentless pursuit of engineering perfection. Singapore-based company Fu Yu embodies this philosophy through its cutting-edge, one-stop-shop services, which include design and tool fabrication, precision injection moulding, metal injection moulding, product assembly and secondary processes.
“We are talking about up to 30-bar pressure. It’s absolutely good and reliable on that. We are also talking about 100 °C heating for the [bottle] preform without any wearing on the cavity of the 3D printer mold,” says Flavio Migliarelli, R&D design manager at Serioplast, in a Formlabs video interview.
The SLA 3D printing process enabled Serioplast to build resin molds in two days, a significant time savings vs. traditional machined metal molds (typically outsourced to a vendor), which take four to eight weeks to produce.
The ability to rapidly iterate bottle designs and molds speed pilot evaluations by enabling testing of multiple designs at the same time.
The pilot included not only consumer testing but also primary validation of the bottle designs on Unilever’s filling line. This included bottle movement and how the containers functioned during filling, capping, and robotic case packing.
With a presence in Singapore, China and Malaysia, Fu Yu’s comprehensive services cater to various industries, manufacturing precision plastic components for sectors such as medical, automotive, printing, industrial and consumer goods. Its subsidiary, Fu Yu Biomedical, aims to innovate and manufacture medical diagnostics equipment, envisioning a future where simple medical tasks, like blood tests, can be conveniently conducted at home. Fu Yu also offers product design services, rapid prototyping, and full product assembly to meet the ever-evolving needs of the medical sector.
Fu Yu is looking to form alliances with complementary service providers in the electronics, batteries, metals, coating, and sterilisation sectors, enabling it to offer an all-in-one solution suite to its customers.
Working together in Italy, Unilever and Serioplast used 3D printing to rapidly create molds and produce pre-production sample bottles made of PET. The molds were built using Formlabs’ Rigid 10K Resin and Form 3L large-format, stereolithography (SLA) 3D printer.
“We are focused on scaling up and upgrading our capabilities, transitioning from traditional case parts manufacturing to a niche specialisation in high-precision products,” said David Seow, group CEO and board member of Fu Yu. “Our exceptional capabilities in precision tooling and precision moulding and unique ability to engage with our customers at the early product development stage are what truly set us apart.”
The printed molds also reduced lead time for pilot testing of blow-molded PET bottles. Lead time to produce 200 bottle samples using the printed molds was only two weeks, vs. the six to eight weeks required with conventional molds.
Additionally, Serioplast uses the printed molds to validate the stretch blow-molding process for the bottle designs. The company also performed dimensional analysis on the bottles and conducted performance evaluations, including bulge, cupping, and drop testing.
Printing the molds reduced tooling cost by up to 90% vs. metal molds. Specifically, the printed molds cost $500 to $1,000 to make vs. $2,500 to $10,000 for machined metal molds.
To produce bottles with the printed molds, Serioplast used the same blow-molding process window as for a metal pilot mold.
“The Formlabs machine plus the [Rigid] 10K Resin together offer the real possibility to have very good details on the bottles, [including logos or something] like a lemon detail, which requires a lot of precision,” says Stefano Cademartiri, CAD and prototyping owner at Unilever.
Formlabs describes the resin as an industrial-grade, highly glass-filled material with a tensile modulus of 10,000 MPa. Molds printed from the resin exhibit good dimensional stability and tolerate hundreds of blow-molding cycles, with repeatability.
Unilever and plastic-packaging manufacturer Serioplast Global Services are transforming stretch blowmolded bottle prototyping using 3D printing technology from Formlabs. The result is much faster, less expensive mold making and prototype production and testing.
To create the plastic molds, the team needed a resin that could endure the temperature and internal pressure of stretch blow molding and deliver dimensional accuracy and stability in the finished tooling. Formlabs’ Rigid 10K Resin provided the required strength, stiffness, and thermal resistance.
Produced using the same resin and on the same blow-molding equipment as production bottles, the samples were ideal for pilot testing.
Through the art and science of 3D printing, “Something is on your screen, [and] in a short time is in your hands,” Cademartiri explains. “A real product with a real bottle, with a real cap, and the real label.”
GETTING A QUOTE WITH LK-MOULD IS FREE AND SIMPLE.
FIND MORE OF OUR SERVICES:
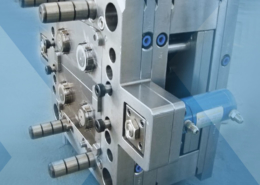
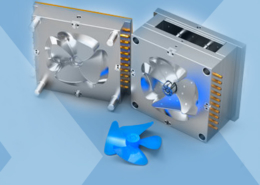
Plastic Molding

Rapid Prototyping
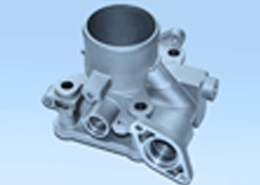
Pressure Die Casting
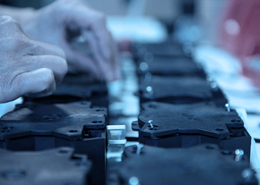
Parts Assembly
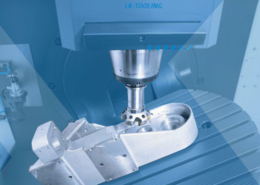