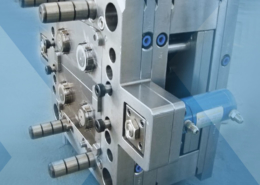
Overmolding Overhaul - plastic injection overmolding
Author:gly Date: 2024-09-30
Additive technology creates air pockets in film during orientation, cutting down on the amount of resin needed while boosting opacity, mechanical properties and recyclability.
Plastics Technology covers technical and business Information for Plastics Processors in Injection Molding, Extrusion, Blow Molding, Plastic Additives, Compounding, Plastic Materials, and Resin Pricing. About Us
Sodick by Plustech’s MS G2 Series electric injection molding machines feature new controls and displays. Source: Sodick by Plustech
Mostafa Tantawi is a senior pipeline engineer at Xodus Subsea. He has over four years’ experience in subsea engineering and pipelines mechanical design. He has an MSc in Subsea Engineering.
technotrans says climate protection, energy efficiency and customization will be key discussion topics at PTXPO as it displays its protemp flow 6 ultrasonic eco and the teco cs 90t 9.1 TCUs.
Join this webinar to explore the transformative benefits of retrofitting your existing injection molding machines (IMMs). Engel will guide you through upgrading your equipment to enhance monitoring, control and adaptability — all while integrating digital technologies. You'll learn about the latest trends in IMM retrofitting (including Euromap interfaces and plasticizing retrofits) and discover how to future-proof your machines for a competitive edge. With insights from industry experts, it'll walk you through the decision-making process, ensuring you make informed choices that drive your business forward. Agenda: Maximize the value of your current IMMs through strategic retrofitting Learn how to integrate digital technologies to enhance monitoring and control Explore the benefits of Euromap interfaces and plasticizing retrofits Understand how retrofitting can help meet new product demands and improve adaptability Discover how Engel can support your retrofitting needs, from free consultations to execution
Say “manufacturing automation” and thoughts immediately go to the shop floor and specialized production equipment, robotics and material handling systems. But there is another realm of possible automation — the front office.
Plastics Technology’s Tech Days is back! Every Tuesday in October, a series of five online presentations will be given by industry supplier around the following topics: Injection Molding — New Technologies, Efficiencies Film Extrusion — New Technologies, Efficiencies Upstream/Downstream Operations Injection Molding — Sustainability Extrusion — Compounding Coming out of NPE2024, PT identified a variety of topics, technologies and trends that are driving and shaping the evolution of plastic products manufacturing — from recycling/recyclability and energy optimization to AI-based process control and automation implementation. PT Tech Days is designed to provide a robust, curated, accessible platform through which plastics professionals can explore these trends, have direct access to subject-matter experts and develop strategies for applying solutions in their operations.
The company has upgraded to a 19" screen, enabling clear graphical representation of machine-state data and real-time cycle chart displays. The new control maintains the screen switch layout of the previous model for continuity, with smartphone-like functionalities such as pinch-in/out and swiping.
Pipelines typically form a major proportion of the development cost of a subsea project, particularly for long subsea tie-backs. The costs, which include procurement, fabrication and installation, are mainly driven by the pipeline material selected and method of installation.
A typical procurement and fabrication cost comparison between polymer liners and alternative corrosion resistant methods (includes indicative pipeline insulation). Graphs from Xodus.
Across the show, sustainability ruled in new materials technology, from polyolefins and engineering resins to biobased materials.
Multiple speakers at Molding 2023 will address the ways simulation can impact material substitution decisions, process profitability and simplification of mold design.
Mike Sepe has authored more than 25 ANTEC papers and more than 250 articles illustrating the importance of this interdisciplanary approach. In this collection, we present some of his best work during the years he has been contributing for Plastics Technology Magazine.
While prices moved up for three of the five commodity resins, there was potential for a flat trajectory for the rest of the third quarter.
Second quarter started with price hikes in PE and the four volume engineering resins, but relatively stable pricing was largely expected by the quarter’s end.
Corrosion is a critical problem that can lead to major pipeline failure, and in some cases total shutdown, if not monitored and managed properly. This impacts the operator’s business with down time, loss of supply and the significant cost of remedial work.
The MS G2 Series second-generation electric injection molding machines feature the eV-Line servo-motor-driven injection and plasticizing injection units, which control the measurement values and injection position in a closed loop. Sodick Plustech says the system provides positional accuracy and repeatability in plasticizing, metering and injection, while running quieter and on less energy than other machines. Sodick says the new series achieves up to a 28% reduction in power consumption compared to its hybrid models.
The insulating impact of the inner polymer liner on the inside of the pipe will also result in a reduced steel temperature, which will also enhance the mechanical behavior of the pipeline, minimizing thermal expansion and propensity for global buckling. An indicative example of the reduction in steel temperature when utilizing a PVDF polymer liner is presented in the figure below.
This Knowledge Center provides an overview of the considerations needed to understand the purchase, operation, and maintenance of a process cooling system.
Following the completion of this insertion process, bespoke flangeless connector technology is used to join together lined pipe sections at the field joints.
Polymer lining can also allow for potential unprocessed (production) water re-injection service, which saves on the requirement for topside de-aeration equipment. With an increased need for hotter water injection temperatures, different types of higher performing polymer materials are now available to fulfil varying service requirements.
The VR G Series expands on the VREs’ mold size capacities with up to a 50% increase to accommodate larger and more complex molds. For reference, mold installation area expansion multiples range from 1 to 1.5 times.
The technology’s internal pipeline corrosion protection has great potential for usage in hydrocarbon pipelines using engineered polymers. It is recognized that the use of polymer liners in subsea production pipelines has yet to be fully developed and that there are challenges in this arena, which must be resolved before polymer lining can be considered in every service application, but these are now being seriously considered by operators worldwide.
Successfully starting or restarting an injection molding machine is less about ticking boxes on a rote checklist and more about individually assessing each processing scenario and its unique variables.
Operators are being challenged to investigate new ways of implementing cost reductions to oil and gas producing assets. Key to addressing these challenges is innovation, and investment into research and development must continue to help maximize the recovery of remaining hydrocarbon reserves.
Further opex reductions will be achieved by negating the need for corrosion inhibitors, frequent pigging and energy (pumping) costs. These savings are measured across the total life of a pipeline, and adopting at the early stages of a project means that IRM costs can be drastically reduced throughout the average life span of a pipeline.
Mold maintenance is critical, and with this collection of content we’ve bundled some of the very best advice we’ve published on repairing, maintaining, evaluating and even hanging molds on injection molding machines.
A significant part of the cost of maintaining a subsea pipeline is incurred attempting to combat internal corrosion. Carbon steel is traditionally selected for the fabrication of risers and flowlines, with protection from corrosion and erosion afforded by the “thickening” of the pipe, through the addition of a corrosion allowance and introduction of a corrosion inhibitor into the product.
This month’s resin pricing report includes PT’s quarterly check-in on select engineering resins, including nylon 6 and 66.
The MS G2 Series facilitates setting conditions for a wide range of molding methods, such as pressure filling control (pressure priority control), injection link clamping function and clamping during injection for effective venting measures.
Join Wittmann for an engaging webinar on the transformative impact of manufacturing execution systems (MES) in the plastic injection molding industry. Discover how MES enhances production efficiency, quality control and real-time monitoring while also reducing downtime. It will explore the integration of MES with existing systems, emphasizing compliance and traceability for automotive and medical sectors. Learn about the latest advancements in IoT and AI technologies and how they drive innovation and continuous improvement in MES. Agenda: Overview of MES benefits What is MES? Definition, role and brief history Historical perspective and evolution Longevity and analytics Connectivity: importance, standards and integration Advantages of MES: efficiency, real-time data, traceability and cost savings Emerging technologies: IoT and AI in MES
The ongoing work being undertaken by operators, and the interest being shown by the industry indicates that the message is getting across and polymer lining is being considered as a serious alternative.
The future seems bright for the usage of polymer linings for affordable internal corrosion protection. With the average cost of installation and maintaining a pipeline accounting for around 35% of a typical subsea tie-back project, it is little wonder that such efforts are going into research and development activity and cost saving measures.
However, for ambient water injection service, the application of a polymer lining system is now becoming the benchmark. Where water injection service requirements are more extreme and in hot sour hydrocarbon service environments, corrosion resistant allow (CRA) lining and cladding, or even a solid CRA, is commonly specified to handle the corrosive nature of the transported product. This method, however, has significant implications on the procurement, scheduling and installation costs of a subsea pipeline.
Discover how artifical intelligence is revolutionizing plastics processing. Hear from industry experts on the future impact of AI on your operations and envision a fully interconnected plant.
Across all process types, sustainability was a big theme at NPE2024. But there was plenty to see in automation and artificial intelligence as well.
Core Technology Molding turned to Mold-Masters E-Multi auxiliary injection unit to help it win a job and dramatically change its process.
Exhibitors and presenters at the plastics show emphasized 3D printing as a complement and aid to more traditional production processes.
Ultradent's entry of its Umbrella cheek retractor took home the awards for Technical Sophistication and Achievement in Economics and Efficiency at PTXPO.
The VR G combines the V-Line injection unit of separate plasticizing and injection units, with Sodick’s proprietary hydraulic servo control technology. The vertical line has also adopted the new controller with large 19" screen and smartphone-like touch functionalities as well as Industry 4.0 connectivity via adoption of Euromap and OPC UA protocols.
Sustainability continues to dominate new additives technology, but upping performance is also evident. Most of the new additives have been targeted to commodity resins and particularly polyolefins.
Formnext Chicago is an industrial additive manufacturing expo taking place April 8-10, 2025 at McCormick Place in Chicago, Illinois. Formnext Chicago is the second in a series of Formnext events in the U.S. being produced by Mesago Messe Frankfurt, AMT – The Association For Manufacturing Technology, and Gardner Business Media (our publisher).
In this collection, which is part one of a series representing some of John’s finest work, we present you with five articles that we think you will refer to time and again as you look to solve problems, cut cycle times and improve the quality of the parts you mold.
At higher temperatures, up to 85°C, and where an option for produced water re-injection may be required, a more chemically resistant polyethylene such as PE-RT (polyethylene of raised temperature resistance) can be used. Polyethylene materials may be considered for hydrocarbon applications but as service environments change as temperature increases, above 50°C the properties of ‘engineered polymers’ such as polyamides and polyvinylidene difluoride (PVDF) may be preferential.
Polymer lining technology performs to the stringent health and safety standards that the oil and gas industry demands, allowing pipelines to be constructed and installed within a low risk environment and affording lifetime protection.
In this three-part collection, veteran molder and moldmaker Jim Fattori brings to bear his 40+ years of on-the-job experience and provides molders his “from the trenches” perspective on on the why, where and how of venting injection molds. Take the trial-and-error out of the molding venting process.
Sodick Plustech’s VR-G and MS-G2 Series both utilize the company’s proprietary V-Line technology, separating plasticizing and injection functions, and have upgraded displays, energy efficiency, response time and more.
Start by picking a target melt temperature, and double-check data sheets for the resin supplier’s recommendations. Now for the rest...
Gifted with extraordinary technical know how and an authoritative yet plain English writing style, in this collection of articles Fattori offers his insights on a variety of molding-related topics that are bound to make your days on the production floor go a little bit better.
Take a deep dive into all of the various aspects of part quoting to ensure you’ve got all the bases—as in costs—covered before preparing your customer’s quote for services.
Whittle joined Swagelining in 2009 at the inception of the company as business development director. He works with new and existing clients to determine future industry requirements for polymer lining technology across a range of projects in subsea and onshore pipeline systems.
David Whittle has over 40 years’ experience in the pipeline industry, in various engineering capacities in the UK and internationally for organizations including British Gas and Subsea 7.
Theoretically, in hydrocarbon service, the threat of liner collapse exists, due to the permeated pressure gas build-up in the annular gap between the polymer liner and the inner wall of the carbon steel pipeline. Additionally, the issue of potential liner swelling when in contact with hydrocarbons needs to be considered.
When, how, what and why to automate — leading robotics suppliers and forward-thinking moldmakers will share their insights on automating manufacturing at collocated event.
The aim of this presentation is to guide you through the factors and the numbers that will help you determine if a robot is a smart investment for your application. Agenda: Why are you considering automation? What problems are you trying to solve? How and why automation can help Crunch the numbers and determine the ROI
Indicative example of steel temperature for external 5LPP system vs. 15mm PVDF internal liner (based on case study conducted by Xodus Group Ltd. Inlet fluid temperature = 60°C) Graphs from Xodus.
Work to address this is currently being carried out by Swagelining (a UK-based specialist in the design and installation of polymer linings), which has recently embarked upon a joint industry project (JIP) with The Welding Institute (TWI) and Saudi Aramco. This JIP will examine the extent of corrosion incurred in a variety of polymer lined pipelines when subjected to a hot sour hydrocarbon environment.
While the major correction in PP prices was finally underway, generally stable pricing was anticipated for the other four commodity resins.
Swagelining is also currently carrying out technical qualification programs with operators, identifying how polyethylene performs with higher temperature injection water and considering the effects of chemicals used for enhanced oil recovery (EOR).
While the melting process does not provide perfect mixing, this study shows that mixing is indeed initiated during melting.
Polymer-lined pipe has been around since the 1990s, but its potential has yet to be fully tapped, according to those behind JIPs to extend use of this technology. Mostafa Tantawi and David Whittle explain.
After successfully introducing a combined conference for moldmakers and injection molders in 2022, Plastics Technology and MoldMaking Technology are once again joining forces for a tooling/molding two-for-one.
Join KraussMaffei for an insightful webinar designed for industry professionals, engineers and anyone interested in the manufacturing processes of PVC pipes. This session will provide a comprehensive understanding of the technology behind the production of high-quality PVC pipes: from raw material preparation to final product testing. Agenda: Introduction to PVC extrusion: overview of the basic principles of PVC pipe extrusion — including the process of melting and shaping PVC resin into pipe forms Equipment and machinery: detailed explanation of the key equipment involved — such as extruders, dies and cooling systems — and their roles in the extrusion process Process parameters: insight into the critical process parameters like temperature, pressure and cooling rates that influence the quality and consistency of the final PVC pipes Energy efficiency: examination of ways to save material and energy use when extruding PVC pipe products
In this collection of articles, two of the industry’s foremost authorities on screw design — Jim Frankand and Mark Spalding — offer their sage advice on screw design...what works, what doesn’t, and what to look for when things start going wrong.
Until now, high performance grades of polyethylene, predominantly polyethylene (PE) 100 have been used for the vast majority of lining applications. PE 100 is suitable for use in water injection service up to 60°C, where long lifetimes can be expected in the relatively benign conditions of treated seawater for example.
In this collection of content, we provide expert advice on welding from some of the leading authorities in the field, with tips on such matters as controls, as well as insights on how to solve common problems in welding.
Performing fundamental maintenance inspections frequently assures press longevity and process stability. Here’s a checklist to help you stay on top of seven key systems.
Despite price increase nominations going into second quarter, it appeared there was potential for generally flat pricing with the exception of a major downward correction for PP.
The Plastics Industry Association (PLASTICS) has released final figures for NPE2024: The Plastics Show (May 6-10; Orlando) that officially make it the largest ever NPE in several key metrics.
While prices moved up for three of the five commodity resins, there was potential for a flat trajectory for the rest of the third quarter.
Resin drying is a crucial, but often-misunderstood area. This collection includes details on why and what you need to dry, how to specify a dryer, and best practices.
Polymer-lined subsea pipelines are traditionally installed by reel lay, J-lay and in bundles. Existing connector technology restrictions have excluded the application by S-lay until now, but new developments are allowing this to be considered as an option.
August 29-30 in Minneapolis all things injection molding and moldmaking will be happening at the Hyatt Regency — check out who’s speaking on what topics today.
Polymer lining technology was introduced to the oil and gas subsea sector in the mid-1990s. Installation is achieved by pulling an extruded polymer pipe through a reduction die to temporarily reduce its diameter. While in this reduced state, the pipe continues to be pulled through the constructed carbon steel carrier (outer) pipe, before being released and reinstated to its initial size so that it fits tightly to the host. Lengths of liner up to 1500m have been installed in single operations.
The UK oil and gas industry is in the midst of some troublesome times. The new, lower price of Brent oil, averaging US$45-60/bbl during the last six months, has seen drastic measures taken to make cost savings and reduce operational spend.
Join Engel in exploring the future of battery molding technology. Discover advancements in thermoplastic composites for battery housings, innovative automation solutions and the latest in large-tonnage equipment designed for e-mobility — all with a focus on cost-efficient solutions. Agenda: Learn about cutting-edge thermoplastic composites for durable, sustainable and cost-efficient battery housings Explore advanced automation concepts for efficient and scalable production See the latest large-tonnage equipment and technology innovations for e-mobility solutions
Processors with sustainability goals or mandates have a number of ways to reach their goals. Biopolymers are among them.
The MS G2 Series includes a new controller and operation screen. Sodick says the new control’s communication system has improved the response time for each operation. It has also adopted a temperature control system for more precise regulation of heater temperature, achieving more stable, high-precision molding.
Mixed in among thought leaders from leading suppliers to injection molders and mold makers at the 2023 Molding and MoldMaking conferences will be molders and toolmakers themselves.
Further to the impact on an operator’s schedule and bottom line however, is the dramatic consequences which can result from pipeline failure. Polymer lining technology stops corrosion being incurred from the outset, which is one of its most important benefits.
The VR G Series is the successor to Sodick’s VRE Series hybrid, vertical, rotary injection molding machines. The new VR G Series inherits the accurate filling and stable plasticization of the VRE Series via the V-Line injection unit and Sodick’s hybrid direct-pressure clamping.
An additional advantage for regular hydrocarbon service is that polymers have good heat insulation properties and add significantly to the thermal performance of a pipeline system. For example, a layer of polymer between 10-15mm will have a significant effect on the pipeline overall heat transfer coefficient, greatly reducing the outer insulation requirement of the pipeline. While a 12in carbon steel buried pipeline with a 5LPP insulation system can typically have a U-value of 3 W/m2K, a 15mm PVDF liner will result in a U-value around 4 W/m2K. This can provide substantial cost saving, as the cost of outer insulation is often higher when compared to the cost of carbon steel.
Learn about sustainable scrap reprocessing—this resource offers a deep dive into everything from granulator types and options, to service tips, videos and technical articles.
Using polymer liners in hydrocarbon pipelines can deliver significant technical advantages. Not only are they fully corrosion resistant, polymer liners are also relatively smooth compared to steel and metallurgic alloys. The low roughness of polymers minimizes the pressure drop across the pipeline, which is maintained along the lifetime of the pipeline, unlike steel/CRA roughness which degrades due to erosion and corrosion.
Swagelinings enior development engineer machining thepolymer lining to accept connector technology. Photos from Swagelining.
Polymer liners are currently favored in the majority of subsea water injection pipelines in the North Sea due to the cost effective corrosion resistance and reliability, with a significant increase in the number of operators recognizing the technology in recent years.
In a time where sustainability is no longer just a buzzword, the food and beverage packaging industry is required to be at the forefront of this innovation. By adopting circular packaging processes and solutions, producers can meet regulatory requirements while also satisfying consumer demand and enhancing brand reputation. Join Husky to learn more about the broader implications of the circular economy — as well as how leading brands are leveraging this opportunity to reduce costs, increase design flexibility and boost product differentiation. Agenda: The cost and operational benefits of embracing circularity Key materials in circular packaging — including rPET and emerging bioplastics How to design a circular food and beverage package Strategies for selecting sustainable closures to future-proof packaging solutions Optimization and streamlining of production processes for enhanced efficiency How Husky Technologies can enable your sustainable success
The use of polymer liners in subsea pipelines can result in substantial cost reduction for both capital expenditure (capex) and operational expenditure (opex). The cost of procurement and fabrication of a PVDF lined pipeline for service application to 130oC is about 50% cheaper compared with the equivalent CRA clad pipeline. In low temperature applications (for example <60oC), where a PE liner can be used, the cost of procurement and fabrication can be 80% cheaper than the equivalent clad pipeline and 40% cheaper than carbon steel pipeline with corrosion allowance. (Figures presented are representative of a 12im X65 pipeline and are indicative only).
Introduced by Zeiger and Spark Industries at the PTXPO, the nozzle is designed for maximum heat transfer and uniformity with a continuous taper for self cleaning.
Sodick says the machines comply with Euromap 77, Euromap 82 and OPC UA communication protocols, enabling them to network with auxiliary devices and other equipment, with standard LAN ports facilitating connections to the company’s V Connect quality and production management system.
The elastic nature of polymers is also more tolerant to both fluid and particle erosion. These fluids often contain debris and deposits, which can accumulate on the inner wall of a pipeline, causing flow restrictions and occasionally, blockages. It is envisaged that the adhesion between fluid deposits, for example wax and hydrates, and polymer material is lower than that of steel, which decreases this blockage risk and reduces pigging frequency requirements.
Extensive research and development has gone into developing pipeline polymer lining solutions, which have the potential to offer considerable cost savings as well as significant operational and technical benefits. These developments have been driven by both industry and consultancies, in an effort to achieve wider understanding of the significant benefits that polymers bring.
The technical benefits of plastic lined pipelines are vast. Polymers are corrosion resistant, which immediately negates the need for corrosion inhibitors throughout the life of the pipeline or the requirement of a CRA derived pipeline.
Thousands of people visit our Supplier Guide every day to source equipment and materials. Get in front of them with a free company profile.
GETTING A QUOTE WITH LK-MOULD IS FREE AND SIMPLE.
FIND MORE OF OUR SERVICES:
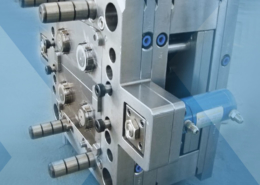
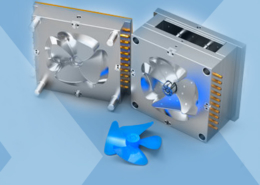
Plastic Molding

Rapid Prototyping
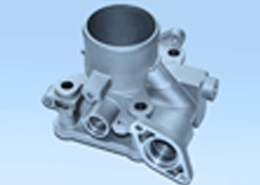
Pressure Die Casting
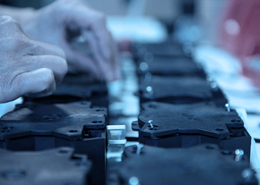
Parts Assembly
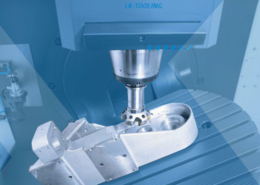