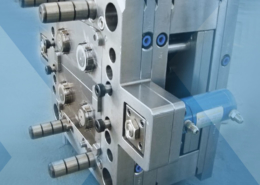
Overmolding Overhaul - overmolding injection molding
Author:gly Date: 2024-09-30
Your email address is used only to let the recipient know who sent the email. Neither your address nor the recipient's address will be used for any other purpose. The information you enter will appear in your e-mail message and is not retained by Phys.org in any form.
“We can set the melting depth by means of various parameters: the laser output, the speed at which the laser beam travels along the surface and the length of the laser pulses,” states Willenborg. Laser polishing does not achieve the same surface smoothness as perfect hand polishing - hand polishers can achieve a roughness Ra of 5 nanometers, the laser at present can only manage 50 nanometers - but Willenborg still sees considerable market potential for the system. “We will concentrate on automating the medium grades: a roughness of 50 nanometers is adequate for many applications, including the molds used for making standard plastic parts.” The high-end levels of smoothness will therefore remain the domain of skilled hand polishers.
Headquartered in York, PA, GEC is committed to supporting customers’ evolving needs through a one-stop-shop approach, commented Schroeder on the rationale for purchasing Kennedy Tool & Die. “A critical step in achieving this goal is putting the right organization together to meet those needs. The Kennedy team brings a deep understanding of precision molds and tooling, and we are thrilled to have them join our company. Bringing together two industry leaders will significantly improve our ability to provide superior customer service and the highest quality products,” said Schroeder.
We keep our content available to everyone. Consider supporting Science X's mission by getting a premium account.
Researchers at the Fraunhofer Institute for Laser Technology ILT in Aachen have developed a way of automating the polishing work: “We do not polish the surface by hand with grinding and polishing media. Instead we use a laser,” explains Dr.-Ing. Edgar Willenborg, group leader at the ILT. “The laser beam melts the surface to a depth of about 50 to 100 micrometers. Surface tension ensures that the liquid metal flows evenly and solidifies smoothly.” Like in conventional grinding and polishing, the process is repeated with increasing degrees of fineness. In the first stage the researchers melt the surface to a depth of about 100 micrometers, in further steps they gradually reduce the depth.
“Bridging the gap” between extrusion and tooling and mold design, the acquisition will allow Graham Engineering to expand its life-cycle management portfolio.
“This is just a logical step toward helping to meet the needs of an ever-changing marketplace,” commented Kroll. “Together, we can provide more value to customers and simplify the extrusion machinery and tooling process.”
The time gained by laser polishing and the cost saving achieved are enormous. Whereas a skilled polisher needs about 10 to 30 minutes for each square centimeter, the laser polishes the same area in about a minute. A prototype of the laser polishing machine developed by the scientists in cooperation with mechanical engineering firm Maschinenfabrik Arnold has already been built. Willenborg estimates that the system will be ready for industrial use in one to two years’ time. At the Euromold trade show, to be held from December 2 to 5 in Frankfurt, the researchers will be presenting examples of three-dimensional surfaces polished by laser.
Get weekly and/or daily updates delivered to your inbox. You can unsubscribe at any time and we'll never share your details to third parties.
The Kennedy operation, now a GEC brand, will remain in Birdsboro, PA, where it was founded in 1960. Reporting directly to David Schroeder, Kennedy co-owners Steve Kennedy and Scott Kroll will continue with the company as Director of Operations and Director of Business Development, respectively.
Use this form if you have come across a typo, inaccuracy or would like to send an edit request for the content on this page. For general inquiries, please use our contact form. For general feedback, use the public comments section below (please adhere to guidelines).
“There are good mold and tooling suppliers and good extrusion machinery companies,” observed David Schroeder, President and CEO of GEC. “Until now, however, we don’t believe that anyone has bridged the gap between extrusion and the tooling and mold design required to make the finished product, nor the services required to maintain system performance over time.”
Jobs are in short supply, and yet some sectors have difficulty in finding suitable trainees for specialist tasks, such as polishing injection molds. The work is time-consuming and monotonous but requires highest levels of concentration, because any blemish in the mold can render it useless. A skilled worker may often need a whole week to polish a single metal mold. Up to now it has not been possible to use machines for this dreary work because they cannot get into the curved shapes.
(PhysOrg.com) -- Polishing metal surfaces is a demanding but monotonous task, and it is difficult to find qualified young specialists. Polishing machines do not represent an adequate alternative because they cannot get to difficult parts of the surface. A new solution is provided by laser polishers.
A single-screw extrusion specialist, Graham Engineering offers standard and custom extrusion products spanning blow molding, feed screws, and turnkey systems for various end markets.
Extrusion technology company Graham Engineering Co. LLC (GEC) announced today that it has acquired Kennedy Tool & Die Inc., a manufacturer of molds and tooling used in blow molding, reaction-injection molding, thermoforming, and structural-foam molding.
GETTING A QUOTE WITH LK-MOULD IS FREE AND SIMPLE.
FIND MORE OF OUR SERVICES:
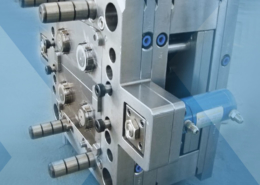
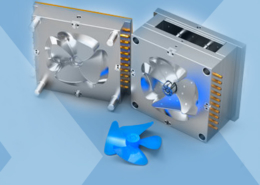
Plastic Molding

Rapid Prototyping
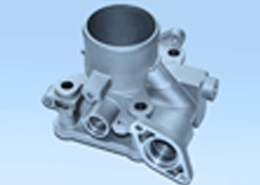
Pressure Die Casting
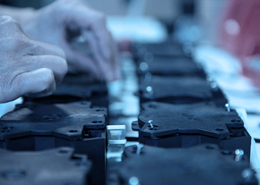
Parts Assembly
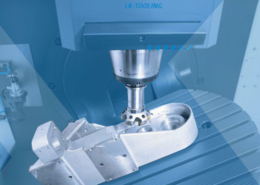