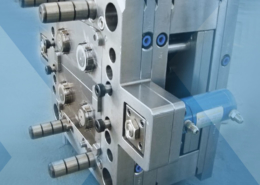
ORBIS Corporation Offers New Reusable Plastic Pallet for Food and Beverage
Author:gly Date: 2024-09-30
One supplier to major aircraft manufacturers has developed a process for joining segments of an aerospace structural component that’s been injection molded using a carbon-fiberfilled PEEK. Due to the part’s complexity and thin cross section, it must be injection molded in foot-long sections. The molder then simultaneously welds four segments into a continuous piece while holding strict dimensional and geometric tolerances for the overall assembly.
Two-shot molding combines molding and overmolding into a single process and can improve productivity and performance. Special machines and molds are required, but combining the processes can reduce variability, enhance aesthetics, and raise part quality. Technology has continued to advance with new manufacturing- process developments. One example is plasma treatment at atmospheric pressure. During molding of the second piece, the mold is momentarily opened, a precisely directed plasma is applied to the still warm surface, and then the mold reclosed. This expands the multimaterial combinations for potential cost savings, and opens the door to new design possibilities. Another proven example is using the residual heat in the just-molded PEEK part to initiate curing of a liquid silicone rubber as the second component.
Schnipke has tooling and plastic injection molding operations at its headquarters in Ottoville, OH, and operates a second manufacturing facility in Tucson, AZ. The company is FDA registered and is certified to ISO 13485:2016.
Plastics injection molder Atalys LLC announced yesterday that it has acquired Schnipke Engraving Co. LLC. Both companies provide injection molding and related services to medical device OEMs. Atalys, based in Rochester, NY, said the acquisition will enhance its manufacturing capabilities, technology, and geographical footprint.
The welding process passes infrared radiation through one transparent part that lies on top of a second lightabsorbent part. Natural PEEK grades are transparent, and black or dark grades are absorptive. A robot or motion system controls the laser path. Heat generated by absorption at the interface melts both surfaces, welding the two components together. Current laser-welding technology limits the thickness of the top transparent piece to <1 mm (0.039 in.). Anything greater will compromise weld strength. Designers can overcome this limitation by adding progressive layers of PEEK film.
Laser welding is unique in that it produces extremely precise and uniform bonds without generating particulates or contaminants. The process does not mar the part surface, as is common with ultrasonic welding. And because the laser focuses energy only into the weld area, this minimizes thermal stresses on adjacent components. It also creates gas-tight hermetic seals and joints without weak spots that ensure a cohesive failure mode.
Polymer films are more commonly used as insulators or barrier materials because they have the added benefit of being their own adhesive. They offer advantages over adhesively bonded structures because they eliminate the cost of the adhesive, the processing time required to apply it, and the possibility of adhesive deterioration or delamination that leads to premature product failure. Eliminating adhesives can also reduce emissions of volatile organic compounds (VOCs).
Ultrasonic welding Ultrasonic welding is a well-established process that uses vibration energy to bond components. Parts are sandwiched between an anvil and horn that emits low-amplitude acoustic vibrations. Vibrations of 15 to 70 kHz concentrated on the surface cause friction and heat, making the two components soften and join together. PEEK polymers lend themselves to ultrasonic joining techniques mainly due to their thermal stability during the welding process.
Without adhesives, thin PEEK-based film can continuously operate at temperatures to 200°C (392°F). This makes PEEK well suited for applications that must withstand lead-free solder-processing temperatures that can sometimes reach 280°C (536°F) for short periods. PEEKfilm laminates also have proven reliability in areas like under-the-hood automotive, down-hole oil and gas exploration, and aerospace applications.
PEEK basics PEEK (polyetheretherketone) is a semicrystalline thermoplastic with a melting point of 343°C (649°F). In addition to a high-operating temperature, PEEK’s molecular structure gives it inherent strength and stiffness, as well as wear, creep, chemical, and flame resistance. Thus, it can improve component durability and reduce weight and maintenance requirements for OEMs. Available unfilled or filled (typically with carbon, glass, or fluoropolymers), the thermoplastic can in many cases match the mechanical properties of metal while requiring less energy to manufacture a part.
In addition to its headquarters in Rochester, Atalys has manufacturing facilities in Asheboro, NC, and the Dominican Republic. The New York and North Carolina plants have multiple Class 8 cleanrooms for molding and assembly on site; the Santo Domingo site in the Dominican Republic offers cleanroom assembly and automation. The company said it adheres to scientific molding principles and is equipped with presses ranging in size from “near micro molding” to 1,400 tons.
Editor in chief of PlasticsToday since 2015, Norbert Sparrow has more than 30 years of editorial experience in business-to-business media. He studied journalism at the Centre Universitaire d'Etudes du Journalisme in Strasbourg, France, where he earned a master's degree.
Changing market demands increasingly have engineers replacing metals and other traditional materials with thermoplastics like PEEK. Reasons include weight reduction in aerospace and automotive applications, to improve fuel economy and cut emissions; and eliminating material-related failures, downtime, and maintenance, such as in oil-field operations as rigs drill deeper wells and encounter higher temperatures and pressures.
It can also lower overall costs. Conventional injection molding, extrusion, and other thermoplastic conversion processes let manufacturers make parts with complex 3D geometries and close tolerances in a fraction of the time it would take to produce the same part in a machined metal, and it usually eliminates secondary finishing operations. Plastic parts are much lighter than their metal predecessors and, therefore, are easier to ship, handle, and assemble.
Process developments now permit direct lamination of roll-to-roll and flat-panel laminate structures. This lets engineers combine film with metal foils like copper, brass, and aluminum, as well as other materials like aramid and glass fibers. Each laminate can be tailor-made with the required materials along with PEEK film to meet specific application requirements.
Founded in 1967, Schnipke has established a reputation for building tools in-house and designing and engineering molds that meet the medical device industry's stringent requirements for precision at extremely tight tolerances, said the news release. The company claims on its website that it can mold within tolerances of +/-0.001 inches and as small as 0.02 grams in weight. Even smaller dimensions can be accommodated upon customer request.
As with other types of welding, the bond is only as strong as the base materials. Metals would seem to offer stronger bonds than PEEK, but that’s not always the case. For instance, chemical reactions such as oxidation or nitriding may occur with metals such as aluminum and subsequently release unwanted gases that compromise joint strength. And if excessive energy absorption at the surface causing the metal to bubble, it can lead to critical failure at the weld seam.
Eliminating the insulating adhesive layer also increases laminate thermal conductivity and can reduce laminate thickness. This leads to smaller, thinner devices. Adhesives can add up to 50% to the overall thickness and weight of a laminate structure, raising fuel costs for operators of aircraft and automobiles and adding to loads and stresses on other components.
Overmolding is a two-step process. First, the rigid PEEK part is injection molded. Then after cooling, the part is loaded into a second cavity where the elastomer is overmolded. Note that mechanical interlock designs are typically unacceptable, as they can add unnecessary weight or create uneven loading conditions that can premature break down the elastomeric layer. A simple flat interface is recommended for even compression forces. Macromechanical interlocking provides good bond strength, so part design is crucial to the success of a finished overmolded part.
Earlier this week, another medical injection molder made news when Total Molding Services announced that it has been acquired by Haartz Family Holdings, changing its name to Moldgenix in the process.
Design-for-assembly (DFA) techniques help reduce the overall number of assembly steps by consolidating components into more integrated designs. Snap-fits often eliminate metal fasteners, and one-piece composite chassis with integral locating pins can accept molded subassembly modules and replace stamped, spot-welded steel frames.
Authored by: Patrick Clemensen Technical Manager - Americas Victrex Polymer Solutions West Conshohocken, Pa. Edited by Kenneth J. Korane [email protected] Key points: • Engineers are replacing metals with highperformance plastics to cut weight and eliminate material-related failures. • Designers should reconsider conventional mechanical joining techniques and look to thermal bonding as a better way to assemble parts. Resources: Victrex Polymer Solutions
Today’s laser-welding equipment readily handles varying surfaces and geometries. Simultaneous welding, for example, uses one or more lasers to simultaneously heat the entire weld path, helping ensure even and continuous bonds. More-precise welds are possible by welding the entire joint at once, or mask welding, which is well suited for large parts and proven effective with PEEK.
As a result, conventional joining techniques — for instance using mechanical fasteners — are now being revisited as manufacturers look for new and better ways to assemble equipment.
PEEK melts and recrystallizes over a relatively narrow temperature range and has excellent thermal stability, allowing for several different joining and assembly methods. These techniques are providing engineers a new set of material and process options to expand design possibilities. Here’s a closer look at some thermal joining methods that can improve part performance and lower costs.
These polymers have been used for decades in demanding applications that were previously the exclusive domain of metals and ceramics. For instance, antilock-brake poppets, compressor-valve plates, and oil-field downhole-tool bushings, seals, and connectors are just a few applications where PEEK handles extreme heat, pressure, and chemical exposure combined with long-term wear and fatigue cycling.
Ken Korane holds a B.S. Mechanical Engineering from The Ohio State University. In addition to serving as an editor at Machine Design until August 2015, his prior work experience includes product engineer at Parker Hannifin Corp. and mechanical design engineer at Euclid Inc.
"Our acquisition of Schnipke was driven by a focused strategy to deepen our capabilities, capacity, and technical superiority across the entire manufacturing process for medical device components,” said Vinc Ellerbrock, president and CEO of Atalys. “The addition of Schnipke adds two manufacturing sites for scalable growth, broadens our geographic presence and reach, enables us to serve a wider array of customers, and significantly augments our technical capabilities,” said Ellerbrock.
Clear-to-clear laser welding is an evolving area. This process has been in development over the last decade but was limited by laser capabilities. Within the last year, however, special lenses have been developed and tested that reach maximum density at the beam waist, applying the highest temperatures to a smaller area in the right wavelength, averaging around 1,700 nm. While not yet commercial, it should make it possible to weld two clear parts.
Heat laminating Heat laminating joins two or more layered materials by heating and melting each layer together without adhesives. The process involves pressing the laminate structure between heated platens or rollers in a continuous process. The material may be preheated by infrared or another noncontact method, but in the press the heat is applied by conduction from the platens or rolls.
Overmolding and two-shot molding Overmolding and two-shot molding can be used to seamlessly apply elastomers directly onto a rigid PEEK part surface, for instance, to give pressure seals tighter tolerances or serve as a tactile cushion on top of a relatively hard, slick surface.
In February, Atalys announced that it is tripling the size of its existing facility in the Dominican Republic from 15,000 to 47,000 square feet through the addition of a new 32,000-square-foot building. The company said that the new building will be dedicated to manual assembly with complementary injection molding, pad printing, tool repair, and warehousing. The existing facility will become the company's primary plastics processing site focused on cleanroom injection molding as well as secondary operations such as testing and packaging.
Laser welding Laser welding, also referred to as laser-transmission welding, offers high-speed production, pin-point accuracy, and good bond strength when joining PEEK parts. Unlike hot-melt and gluing methods, laser welding is more cost effective because no additional material is needed to create the bond. It’s environmentally safe and the tools don’t clog or wear, eliminating maintenance headaches.
The assembled part has more-precise dimensional accuracy than would be possible with a molded part of similar length. These ultrasonically welded PEEK components reduce costs and cycle times because they do not require fasteners, adhesives, or snap-fits to make the bond.
GETTING A QUOTE WITH LK-MOULD IS FREE AND SIMPLE.
FIND MORE OF OUR SERVICES:
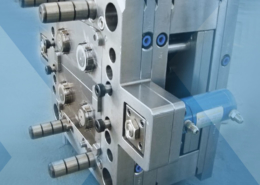
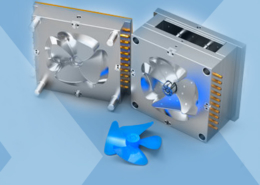
Plastic Molding

Rapid Prototyping
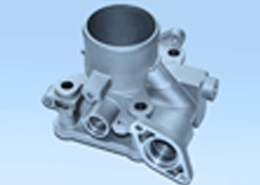
Pressure Die Casting
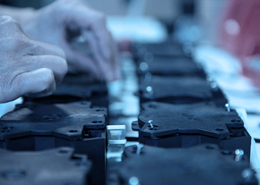
Parts Assembly
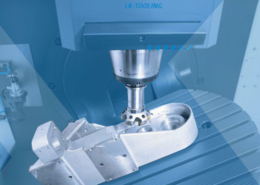