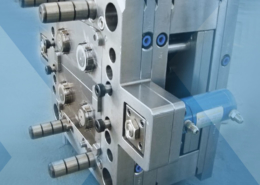
Opening the door to Metal Injection Molding parts: A case study on the
Author:gly Date: 2024-09-30
In this interview, AZoCleantech talks to Trevor Tilman and Kelly McPartland about carbon capture and storage, analysis of CO2 purity and more.
Dr. Liji Thomas is an OB-GYN, who graduated from the Government Medical College, University of Calicut, Kerala, in 2001. Liji practiced as a full-time consultant in obstetrics/gynecology in a private hospital for a few years following her graduation. She has counseled hundreds of patients facing issues from pregnancy-related problems and infertility, and has been in charge of over 2,000 deliveries, striving always to achieve a normal delivery rather than operative.
Disclaimer: The views expressed here are those of the author expressed in their private capacity and do not necessarily represent the views of AZoM.com Limited T/A AZoNetwork the owner and operator of this website. This disclaimer forms part of the Terms and conditions of use of this website.
The downside is that the use of unlike materials in the same print cycle reduces recyclable potential. A potential green solution is to use more complex parts, avoiding the need for assembly and disassembly, as well as using one or a very few tunable materials to create a whole object.
A third option is using only biodegradable materials, including compostable wiring and incinerable plastics. The environmental impact depends on the consumption of energy and material, which varies with technology, material and frequency of use.
At present, injection molding is the most efficient production method for large runs covering hundreds of thousands of parts. Inkjet printing is the 3D printing method with the lowest operating costs due to its use of inexpensive open-source recipes, requiring only operator expertise.
Lean production is a huge advantage of 3D printing, since it eliminates warehousing and work-in-progress costs, and reduces any financial incentive to overproduce, unlike injection molding.
Resource utilization is practically the same with 3D printing or injection molding. Transportation costs may be only marginally reduced, even with on-site printing, since feedstock shipping is still required. If a single producer were to offer multiple types of 3D printed parts of a single material on demand, only warehousing and shipping costs apply. Even so, this impacts manufacturing costs only slightly.
Bonding to the polypropylene (PP) core layer is possible in the same or separate injection molding step. The strong chemical bonding between all layers eliminates the need for additional adhesive layers. Asahi Kasei's new SEBS contributes to reducing the total number of materials, simplifying the manufacturing process, and improving the recyclability of interior components.
This process is capable of using multiple liquid polymers, with batch printing associated with high energy-efficiency. It uses more toxic raw materials (but with higher reusability value), often produces less waste, and requires minimal support material. The solidified polymer cannot be recycled.
Thomas, Liji. "Is 3D Printing Really a Clean Technology?". AZoCleantech. 28 September 2024.
This uses a lot of energy except when batch printing. It is adapted to a wide range of materials including metals, ceramics, thermoplastics, and glass, though slightly less with batch printing. Residual powder can be reused, and support metals recycled, though the support plastic goes to landfill.
Thomas, Liji. (2020, February 17). Is 3D Printing Really a Clean Technology?. AZoCleantech. Retrieved on September 28, 2024 from https://www.azocleantech.com/article.aspx?ArticleID=908.
Giampiero Frisio of ABB discusses AI's impact on data center sustainability and the integration of renewable energy for efficiency.
Asahi Kasei will also showcase a bio-based and biodegradable cellulose nano fiber (CNF) at Fakuma. This material is made from cotton linter and features high heat resistance and a network-forming capability. CNF-reinforced PA exhibits thixotropic behavior, making it highly suitable for 3D-printing applications requiring dimensional accuracy, a smooth appearance, and mechanical performance. Furthermore, CNF exhibits superior material recyclability compared to glass fibers.
From automotive head-up displays to head-mounted displays and smart glasses, requirements related to the weight and design of optical devices have become increasingly demanding. Asahi Kasei’s transparent AZP polymer features almost zero birefringence, overcoming the challenges of conventional transparent polymers in applications with polarizing light. Its superior processability compared to glass enables the large-scale production of injection-molded optical components that fulfill demanding customer requirements.
The cleanest processes sometimes produce the lowest quality, however, and green materials for 3D printing like wood, sawdust and salt are often unavailable or unviable.
The Thermo Scientific™ MAX-iAQ™ is a fully automated ambient air monitoring solution with 20 detection points, specifically designed for the accurate detection of trace compounds in environments with high humidity.
Asahi Kasei will present its materials and solutions in three different areas: Compact & Safe EV Batteries, Improved Connectivity & Lightweighting, and Sustainable Material Life Cycle at its location in hall B5, booth 5319.
The company will also present its comprehensive solutions for establishing a sustainable life cycle for PA 66. In the field of chemical recycling, the company works with Japanese partner company Microwave Chemical, utilizing a microwave process to depolymerize automotive airbags and other PA 66–based parts and directly obtain the monomers hexamethylenediamine (HMD) and adipic acid (ADA). Currently undergoing trials, the process is expected to achieve high yields with low energy consumption. The monomers obtained can then be used to manufacture new PA 66.
This application uses a wide range of energy, but through proper designs it can produce self-supporting part designs with low waste. It uses easily recycled plastics like polyethylene terephthalate (PET), poorly recycled plastics like acrylonitrile butadiene styrene (ABS), and polylactic acid (PLA), which is biodegradable but requires special composting.
The Japanese resin supplier will highlight polymers that support sustainability, comfort and performance in automobiles at the plastics-focused trade show in southern Germany.
Balancing sustainability and functionality without sacrificing cost-competitiveness is a major issue for car manufacturers. To tackle this challenge, Asahi Kasei is currently developing a thermoplastic styrene block copolymer (SEBS) grade for automotive interior surfaces, which require good haptics and soft touch. Conventional approaches use different materials and production technologies for the skin, foam, and core layers in automotive instrument panels, door panels, armrests, or center consoles. The new SEBS material is suitable for both skin and foam layers, which can be molded in one step by utilizing a core back injection molding process.
Your questions, but not your email details will be shared with OpenAI and retained for 30 days in accordance with their privacy principles.
At present most 3D printing is carried out on a small scale. However, it is expanding quickly as tools and materials become more affordable, process quality improves, and innovative techniques emerge.
Any new technology, however promising, must be assessed for its environmental sustainability. This applies to 3D printing, also called additive manufacturing (AM), which is being developed as an alternative manufacturing technology in many fields of production. Clean technology is defined in terms of the lifecycle, greenhouse gas emissions, air pollution, toxic materials, and the use of non-renewable resources.
Optimal printer design, with minimal support material, could also reduce waste generation markedly with certain technologies, but not all. For instance, inkjet and fused deposition modelling (FDM) are very low-waste processes.
Greenhouse gas emissions are likely to drop steadily if 3D printing replaces injection molding technology globally. However, with current technology, whether 3D printing could replace injection molding technology globally remains a question.
Stephen has been with PlasticsToday and its preceding publications Modern Plastics and Injection Molding since 1992, throughout this time based in the Asia Pacific region, including stints in Japan, Australia, and his current location Singapore. His current beat focuses on automotive. Stephen is an avid folding bicycle rider, often taking his bike on overseas business trips, and a proud dachshund owner.
Japanese technology company Asahi Kasei will exhibit its range of diversified material solutions at Fakuma 2024 from Oct. 15 to 19 in Friedrichshafen, Germany. Highlights include polymers for thermal management applications in EVs, a novel thermoplastic elastomer for improved recyclability of automotive interior parts, and a cellulose nanofiber composite for high-performance 3D printing.
Thomas, Liji. "Is 3D Printing Really a Clean Technology?". AZoCleantech. https://www.azocleantech.com/article.aspx?ArticleID=908. (accessed September 28, 2024).
A novel transparent polymer reportedly outperforms incumbents such as polycarbonate and acrylic in automotive head-mounted displays. Image courtesy of Asahi Kasei/Business Wire.
A dual-layer polyamide/mPPE cooling pipe for EV battery thermal management offers excellent bending properties, hydrolysis resistance, and low ion elution properties. Image courtesy of Asahi Kasei/Business Wire.
3D printing is ideal for legacy repair of single components of outdated machines like washing machines or bike parts. This keeps perfectly good machines in continued use, avoiding needless discards or replacement.
Thomas, Liji. 2020. Is 3D Printing Really a Clean Technology?. AZoCleantech, viewed 28 September 2024, https://www.azocleantech.com/article.aspx?ArticleID=908.
The ARL QUANT'X is a complete energy-dispersive X-ray fluorescence spectrometer solution for all your elemental analysis needs.
Another concern is worker exposure to toxic materials with 3D printing, whether at home or in offices, largely due to the absence of safety measures that are routine in industrial situations.
AZoCleantech interviews Carbon Limit's Founder and CEO about the company's mission to reduce one billion tons of CO2 with CaptureCrete, an innovative concrete technology.
3D printing cannot typically be used to print a whole working object with multiple materials simultaneously. Instead, it produces simple components, to be assembled with other parts. However, experimental multi-material printers are already in existence, and if commercialized, could greatly increase the reach of 3D printing.
Sustainable 3D printing demands optimization of the period of operation and part geometry. In general, 3D printing is probably better for the environment compared to machining technologies, but injection molding production processes are superior at the same scale. A printer used for only a few hours each week will leave a larger footprint than when used continuously. 3D printing of hollow-core parts is cleaner than solid-block parts, but with machining, the reverse is true.
This technique uses materials like ceramics, plaster, sawdust, concrete, starch, salt and sugar. While it saves a lot of energy on batch printing and reduces waste, the large-scale printing of consumer goods is unviable.
At the battery island, the company will showcase Xyron modified polyphenylene ether (mPPE) featuring high non-halogenic flame retardance and low ion elution properties. This material is suitable for thermal management applications in EV batteries.
3D printed parts may also impart higher use-phase energy efficiency, such as by lessening the component weight in aerospace and transportation applications. Regenerative cooling and fuel efficiency could be optimized by designing complex engine parts for printing like combustion chamber walls containing fluid channels.
While we only use edited and approved content for Azthena answers, it may on occasions provide incorrect responses. Please confirm any data provided with the related suppliers or authors. We do not provide medical advice, if you search for medical information you must always consult a medical professional before acting on any information provided.
In parallel, Asahi Kasei will introduce its solvent-based recycling process for the first time in Europe. By applying dissolution recycling, high-quality PA 66 can be obtained from process scraps and post-consumer-recycled (PCR) materials such as airbags.
The Energy 11 Twin-Screw Extruder is a versatile piece of equipment designed for various applications in battery research and development.
At Fakuma, Asahi Kasei also will show multilayer cooling pipes that do not require an adhesive layer. These two-layer pipes employ the company’s Leona polyamide (PA) on the outside and Xyron mPPE on the inside. This product offers excellent bending properties, hydrolysis resistance, and low ion elution properties.
GETTING A QUOTE WITH LK-MOULD IS FREE AND SIMPLE.
FIND MORE OF OUR SERVICES:
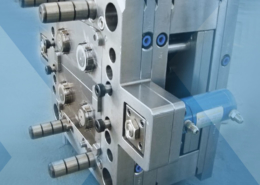
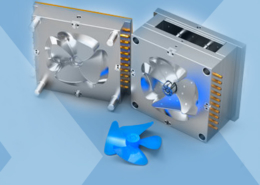
Plastic Molding

Rapid Prototyping
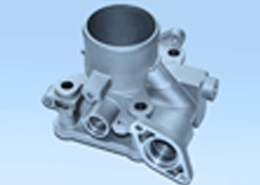
Pressure Die Casting
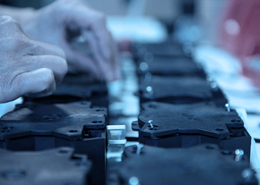
Parts Assembly
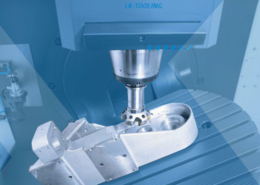