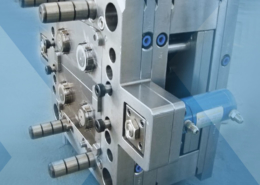
OEP’s Clayens agrees on two transformative North American acquisitions -
Author:gly Date: 2024-09-30
Innovations throughout the plastics supply chain will be featured at PLASTEC West, which comes to the Anaheim Convention Center in Anaheim, CA, on Feb. 7 to 9, 2017. For more information and to register to attend, go to the PLASTEC West website.
Fusible-core injection molding technology has been employed to mold a fuel housing for an aircraft using PEEK (polyetheretherketone) resin supplied by Victrex (West Conshohocken, PA). The solution reportedly delivers a 30% cost saving and up to 50% weight reduction versus existing metal designs.Processor Egmond Plastic was able to consolidate the number of parts using a carbon fiber reinforced grade of Victrex PEEK polymer. A separate bearing, for example, was eliminated since it is now integrated into the overall design of the housing.
MD&M West and PLASTEC West attendees can visit Carclo Technical Plastics in booth 1515 and Precision Tool & Die in booth 1495. The events come to Anaheim, CA, on Feb. 7 to 9, 2017.
Until she retired in September 2021, Clare Goldsberry reported on the plastics industry for more than 30 years. In addition to the 10,000+ articles she has written, by her own estimation, she is the author of several books, including The Business of Injection Molding: How to succeed as a custom molder and Purchasing Injection Molds: A buyers guide. Goldsberry is a member of the Plastics Pioneers Association. She reflected on her long career in "Time to Say Good-Bye."
Carclo Technical Plastics specializes in injection molding and contract manufacturing services for medical and optics applications. Its largest segment served is diagnostic disposables with significant offerings in respiratory, blood management, ostomy, ophthalmic, women’s healthcare, and surgical products. Carclo employs more than 1,000 employees at eight plants across the United States, United Kingdom, Czech Republic, India and China.
President and Division Chief Executive Mark Charbonneau said, “The acquisition of Precision Tool & Die will not only bring synergy to both PTD and Carclo’s customers in expanded capabilities marrying prototyping, tool making and volume manufacturing, but it will also enable Carclo to grow in the region close to its customers.”
“We’ve seen significant new business and opportunities from major OEMs in the region. It was only natural that to continue our growth and follow our philosophy of being close to our customers we target the Northeast as our next logical step,” Charonneau added.
PTD operates 14 injection molding presses ranging from 28 to 400 tons in a 34,000-square-foot facility, which also has Class 10,000 cleanrooms. The company offers precision mold manufacturing as well as a variety of secondary operations, such as ultrasonic welding, automation, assembly and packaging for medical, optical, automotive and electrical applications.
Carclo plc, an injection molder headquartered in Ossett, UK, recently purchased Precision Tool & Die (PTD; Derry, NH) through its Carclo Technical Plastics division. The deal, worth more than $6 million, expands Carclo’s U.S. footprint, adding a base of operations in the northeast to continue its growth in the region.
Carclo plc (Ossett, UK) recently purchased Precision Tool & Die (Derry, NH) through its Carclo Technical Plastics division. The deal, worth more than $6 million, expands Carclo’s U.S. footprint, adding a base of operations in the northeast to continue its growth in the region.
Fusible-core injection molding technology has been employed to mold a fuel housing for an aircraft using PEEK (polyetheretherketone) resin supplied by Victrex (West Conshohocken, PA). The solution reportedly delivers a 30% cost saving and up to 50% weight reduction versus existing metal designs.Processor Egmond Plastic was able to consolidate the number of parts using a carbon fiber reinforced grade of Victrex PEEK polymer. A separate bearing, for example, was eliminated since it is now integrated into the overall design of the housing.Fuel housing molded for CF-PEEK compound using fusible core process.Fuel housings for aerospace applications have very complex inner geometries which are not moldable using conventional injection molding technology. Egmond Plastic's fusible-core technology enables moldings of complex hollow housings, manifolds, and pipes. Richard Brandwijk, Managing Director at Egmond Plastic, explains: "Our technology, in combination with carbon fiber reinforced Victrex PEEK polymer, delivers numerous benefits. These include cost reduction, enhanced manufacturing speed, and weight reduction leading to improved fuel efficiency and reduced CO2 emissions. Along with part consolidation, this exceptional technology and material combination enables the design of very complex parts, beyond the capabilities of standard injection molding and metal processes."Utilizing a near net-shape manufacturing process for the fusible core allows for an 80% time saving versus machined parts. Further, secondary treatments for corrosion protection, such as anodizing, can be eliminated. Lead times can be reduced by 50%. These factors combine to deliver part cost savings of more than 30% versus metal equivalents."The global aerospace industry stands to gain enormously by persistently replacing metals in key applications, in which Egmond has demonstrated tremendous leadership," said Uwe Marburger, Aerospace Business Development Manager at Victrex. "Clearly, our PEEK knowledge and material solutions help enable the use of a technology that addresses some of the toughest challenges in complex aerospace part design and productions."Previously, the end-user had generally specified aluminum for the production of fuel containing parts, but a carbon fiber reinforced PEEK polymer demonstrated superior fatigue performance when compared to aluminum. It does this while meeting all the engineering requirements for this application, including stiffness, effective flame, smoke and toxicity (FST) performance, and resistance to aggressive chemicals, including notably, for this aerospace application, resistance to jet fuel and Skydrol hydraulic fluid. Parts can range in size all the way up to 30 cm x 30 cm x 40 cm (11.8 in x 11.8 in x 15.8 in), and typically the process is used for production runs of up to 2,000 parts.Egmond's unique fusible-core technology has already established a proven track record using Victrex PEEK in a fuel pump for the Eurofighter Typhoon, a jet fighter in use in several European countries. This pump has been in successful operational use for more than 20 years.
GETTING A QUOTE WITH LK-MOULD IS FREE AND SIMPLE.
FIND MORE OF OUR SERVICES:
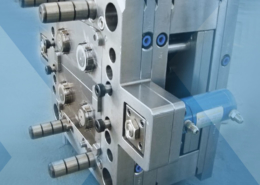
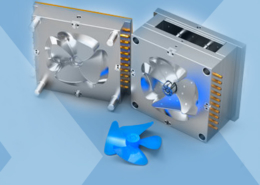
Plastic Molding

Rapid Prototyping
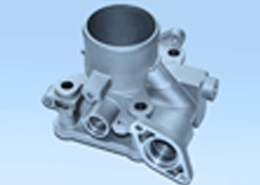
Pressure Die Casting
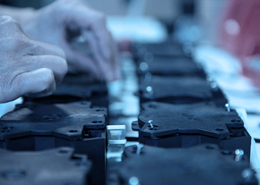
Parts Assembly
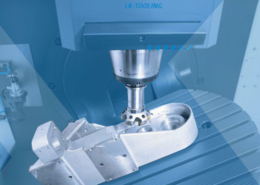