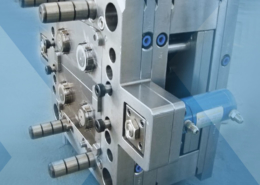
Numerical simulation of closed plastic impeller molding process and its
Author:gly Date: 2024-09-30
Tool & Plastic has been operating for 52 years and led by owners Colm Cuffe and Declan O’Rourke. The organisation specialises in offering competitive and innovative contract GMP cleanroom moulding and assembly solutions. The company operates from a number of ISO class 8 cleanroom environments in its facility in Ireland and from an IATF 16949 compliant facility in the Czech Republic. Tool & Plastic has continually invested in technology to ensure high-quality manufacturing services and a positive reputation.
The research project is also investigating possible ways to automate data matching and the adaptation of neural networks. Manufacturers not only gain the benefit of improved data quality from optical inspections, they can also design their entire process to be as rigorous and error-free as possible, even in complex production environments where a variety of different parts need to be tested.
O’Rourke added: “The acquisition by Technimark represents a strategic fit for the business in Ireland and the Czech Republic, and we look forward to developing and growing the business on the solid foundation already in place.”
Autonomous vehicles transport parts to the test cell and storage area. Image courtesy of OST – Ostschweizer Fachhochschule.
Brad Wellington, CEO of Technimark, said: “Tool & Plastic’s leadership in its core healthcare markets, combined with Technimark’s manufacturing expertise, healthcare customer relationships, and scale create a market leader with significant opportunities for future growth.
“Tool & Plastic will help us deliver even more value to our customers, and we are excited to welcome them to the Technimark family.”
Following inspection, the autonomous vehicle transports the tested parts to the warehouse and the test cell sends the analyzed data to higher-level QA or MES systems. Experts can then compare the quality data with the quality forecasts previously generated by ComoNeo PREDICT. If variances occur, the AI models are retrained using new test data.
The molded parts are serialized using individual QR codes and sorted onto trays. While production is still in progress, Kistler’s ComoNeo system monitors cavity pressures via pressure sensors. With support from appropriately trained AI, ComoNeoPREDICT software generates quality predictions for the individual parts. Driverless transport vehicles convey parts selected for spot checks to the optical test cell. This is the first time autonomous transportation has been used in this context. The parts then pass through the predefined inspection program and are checked for dimensional stability and surface defects as well as injection molding anomalies, such as black specks or moisture splay. Issues specific to plastics processing such as shrinkage due to cooling and crystallization are also taken into account.
Dr.-Ing. Oliver Schnerr is head of sales, Integrated Solutions Automation Solutions / Vision Systems / Fastening Technology at Kistler.
A research project is exploring new avenues for AI-assisted automated optical quality assurance during the injection molding process.
The partnership hopes to enhance Technimark’s healthcare manufacturing expertise, as well as its global footprint. Together the companies will have 13 facilities and over 4,400 employees across the world.
The process can be burdensome, as the samples are removed, transported, and tested manually, tying up resources. Moreover, the quality of the data depends on the skills and expertise of the personnel performing the inspections. Critical parts may have narrower tolerances and require more frequent spot checks, increasing the potential for human error. Automated, reproducible random sample testing can optimize the process.
Quality control is an essential aspect of the production process, especially when it involves parts used in automotive and medical technology applications. The entire quality control process must be designed to ensure maximum precision and reproducibility, and typically requires reams of documentation. All of this is labor-intensive and time-consuming, and is reliant on expert personnel. Automation coupled with artificial intelligence (AI) may offer an alternative.
The objective is to achieve consistently smooth and efficient part handling throughout the entire test process. Integrated safety concepts monitor the systematic progression of the individual steps in the process — as well as the “handshakes” — to guarantee process reliability while preventing data loss. The automatic system then sends the collected data via an OPC UA interface to the operator's higher-level quality assurance system and to relevant databases for analysis.
Additional injection molding machines producing different parts can be integrated into this setup and incorporated into the material flow with the use of autonomous vehicles. In other words, the concept allows for automation of quality control in complex production environments as long as the test cell is equipped with the appropriate inspection programs: The inspection system recognizes the different parts and triggers the relevant test program.
“Tool & Plastic and Technimark share a common culture for technical excellence, safety, innovation and customer partnership, and we look forward to building lasting value together.”
“By enhancing our ability to serve customers across Western and Eastern Europe, these acquisitions bolster our long-term growth strategy in the global healthcare market. Technimark is well-positioned to help our clients apply advanced and innovative technology-based solutions from design and engineering through production, including assembly and packaging of the final product", Wellington concluded.
Switzerland-based Kistler, a developer of measurement systems and sensors, is collaborating with the Eastern Switzerland University of Applied Sciences (OST) in researching advanced quality-control technologies. In particular, Kistler is involved in a project with the university’s IWK Institute for Materials Technology and Plastics that fully automates the inspection of injection molded parts while harnessing the power of AI to hone quality predictions while injection molding.
When starting to design an inspection concept of this sort, the focus initially is on the requirements for the part being tested. The project team collaborates with manufacturers to develop the required quality-relevant test parameters, mostly related to surface defects and dimensional accuracy. They also identity the appropriate test methods. Kistler-developed sensors make it possible to integrate mechanical pressure and force and torque tests. Experts from the company’s competence center then design the test cell accordingly. In addition to determining the number and positioning of camera stations with lighting elements, the key factor at this stage is outlining the inspection path for the part.
The research project with the IWK Institute for Materials Technology and Plastics Processing is focused on injection molding of a medical part. The objective is to develop a system that provides medtech manufacturers with comprehensive automated random sample inspection, generating accurate AI-based quality predictions while injection molding is still in progress.
Manufacturers typically rely on statistical process control (SPC) to verify quality. The frequency and scope of sample testing is defined, enabling users to monitor the production process according to predefined quality parameters.
GETTING A QUOTE WITH LK-MOULD IS FREE AND SIMPLE.
FIND MORE OF OUR SERVICES:
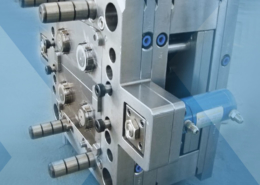
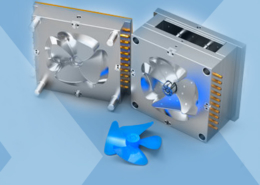
Plastic Molding

Rapid Prototyping
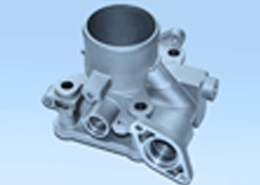
Pressure Die Casting
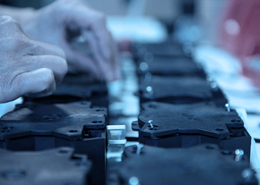
Parts Assembly
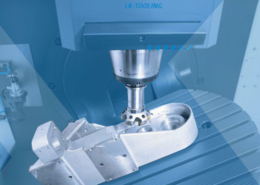