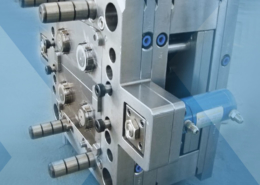
NPE 2024: Additive Manufacturing Assisting, Advancing Plastics Processing - inje
Author:gly Date: 2024-09-30
According to Arnaud Nomblot, business development manager of packaging at Sumitomo (SHI) Demag, "Total's know-how in the field of materials for caps has greatly contributed to this success. The material provides a vital common goal of Sumitomo Demag, Total and partners was to achieve highest product quality with significantly reduced cycle times. The technical breakthrough was made possible thanks to the excellent flow characteristics of the HD6081 material. A cycle time of 1.9 second and perfect injection point quality are the result of optimum combined material, machine and mold performance."
The 96-cavity hot-runner mold was designed and built by Plastisud in Castelnaudary, France with U.S. manufacturing in Kentucky, specializing in high-volume precision molds for the packaging, closures and medical markets.
"Expertise in tool design is fundamental to our core competences within Trelleborg Sealing Solutions," emphasizes Jarno. "Developing the two-color process required additional considerations during the design and construction of the tool to make sure the flow of the clear and the colored material portions must be kept strictly separated.
"Looking actively to improve this result, Sumitomo (SHI) Demag tested several HDPE resins from the market dedicated to caps and closures, and this is where Total made the difference with HDPE HD6081, resins that provided the best results in terms of part quality at lower cycle time (1.9 sec)," the spokesperson said. "So given the fact of sharing the same commercial strategy and objectives, providing excellent technology and know-how from each parties, and achieving results in the right direction, it was very natural to collaborate all together."
The two-color injection molding process has been simplified through a development at Trelleborg Sealing Solutions (Stuttgart, Germany) that employs a single shot and a single tool to manufacture partially colored liquid silicone rubber (LSR) components. Utilizing an innovative and proprietary tool construction, the process has the capability to add color pigment to part of the transparent silicone material stream just prior to its injection into the tool cavity.
Until she retired in September 2021, Clare Goldsberry reported on the plastics industry for more than 30 years. In addition to the 10,000+ articles she has written, by her own estimation, she is the author of several books, including The Business of Injection Molding: How to succeed as a custom molder and Purchasing Injection Molds: A buyers guide. Goldsberry is a member of the Plastics Pioneers Association. She reflected on her long career in "Time to Say Good-Bye."
"This collaboration with Sumitomo Demag is one additional example of Total competitiveness and commitment to the Caps & Closures market, where total as the new challenger, brings to the industry optimized resins fulfilling the highest requirements providing benefits to the complete value chain," said Gabriela Quevedo Silvetti, market development engineer rigid packaging at Total.
This newest system can produce 190,000 caps per hour and 1.5 billion per year. The El-Exis SP 420-3000 packaging machine produces 1.3g HDPE screw caps on a 96-cavity hot runner mold (29/25 design) with a production cycle of only 1.9 seconds. This machine is equipped with a 25:1 L/D ratio barrier screw and has been designed with a special backflow barrier to improve reproducibility.
Total HDPE HD 6081 (d = 0.960 g/cm3, M12 = 8 g/10 min), dedicated to still (non-carbonated) water application, has proved at Sumitomo Demag to be the best HDPE resin capable of achieving the fastest crystallization, thus reducing demolding time between shots while giving optimized mechanical parts.
A Total spokesperson told PlasticsToday that Sumitomo (SHI) Demag and Plastisud had previously worked together during the K show, achieving 2.1 sec of cycle time, which was the fastest production until Chinaplas 2014, where Sumitomo (SHI) Demag set the new world record at 1.9 sec.
Multi-cavitation molds for running high-volume cap and closure production can be very fast systems. Now, Sumitomo (SHI) Demag together with its partners, Total and Plastisud, has set a new world record in the production of HDPE caps with tamper-evident band without post-molding operations, according to information from Total, headquartered in France, with more than 150 locations for specialty chemicals worldwide. Total's refining & chemicals division produces and commercializes a wide range of products from petroleum products to commodity polymers including base chemicals and intermediates.
Multi-cavitation molds for running high-volume cap and closure production can be very fast systems. Now, Sumitomo (SHI) Demag together with its partners, Total and Plastisud, has set a new world record in the production of HDPE caps with tamper-evident band without post-molding operations, according to information from Total, headquartered in France, with more than 150 locations for specialty chemicals worldwide.
Ursula Nollenberger, Product Line Director for LSR Components at Trelleborg Sealing Solutions, says: "Our first application of this revolutionary technology is for a leading automotive tier-one supplier. The company was looking for a solution to visually differentiate geometrically identical parts that Trelleborg produces off a single tool for various vehicle platforms, without impacting the overall aesthetics of the finished product. This new process offered an ideal solution that was both practical and cost-effective."
The two-color injection molding process has been simplified through a development at Trelleborg Sealing Solutions (Stuttgart, Germany) that employs a single shot and a single tool to manufacture partially colored liquid silicone rubber (LSR) components. Utilizing an innovative and proprietary tool construction, the process has the capability to add color pigment to part of the transparent silicone material stream just prior to its injection into the tool cavity.
Jarno Burkhardt, General Manager of the Trelleborg Sealing Solutions European center of excellence for LSR component solutions in Stein am Rhein, Switzerland, comments: "The advantage of the two-colored LSR components to our customer, as well as to the OEM they supply, is that it gives, without adding significant extra cost, product traceability. The beauty of the novel tool design is that it will allow an unlimited number of color combinations from a single machine, in a single tool and in one single shot."
"This novel technology can be applied to any size and number of cavities per tool. Depending on part geometry and size as well as production capacity needed, we construct tools anywhere between 1 and 128 cavities with possibilities even beyond," adds Nollenberger.
The fast cycle time results on one hand, from the combination of optimized mold dynamics by Sumitomo Demag's unique independent hybrid clamp system and optimized injection and plasticizing performance. On the other hand, this achievement has been made possible through the close co-operation between packaging partners, including Total, who has contributed their expertise in polyolefin resins for the caps & closures industry.
The process involves the two components of LSR raw material being mixed in a ratio of 1:1. On the way into the injection tool, this homogenous mass is then divided. Color is added via an additional mixing unit to one part of the volume stream and injected into the tool cavity via a proprietary valve design. Simultaneously, the colorless material is being injected via a second stream.
GETTING A QUOTE WITH LK-MOULD IS FREE AND SIMPLE.
FIND MORE OF OUR SERVICES:
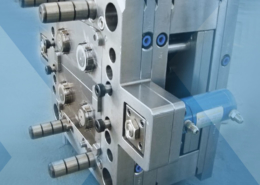
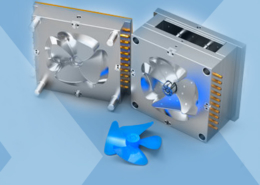
Plastic Molding

Rapid Prototyping
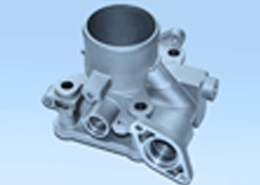
Pressure Die Casting
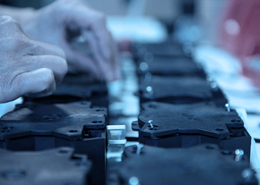
Parts Assembly
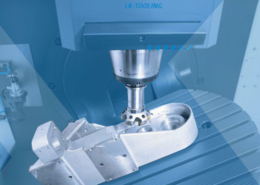