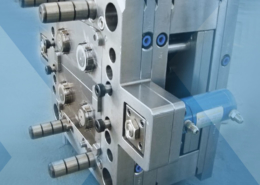
Novoloop and Aether Break Ground on Pilot Plant for PE Upcycling - polyethylene
Author:gly Date: 2024-09-30
"The recent Corona pandemic, the war in Ukraine and high inflation have clearly shown us that we need to develop constantly in order to remain competitive.
Wolf concluded: "Automated manufacturing and digital processes are essential, given the current challenges in the global marketplace.
They are then processed with a ZE 28 BluePower twin-screw extruder and, following the mixing and blending of adhesive and liquid color additives, the compound is sent to an all-electric PX 81-180 press, where the bottle opener is molded. The PX 81-180 is equipped with APCplus, which compensates for process fluctuations that may result from recyclates with different viscosities.
Five-axis simultaneous machining of workpieces up to 1,100 mm in diameter by 1,600 mm and weighing 2,200 kg had already been carried out on a DMU 100 P duoBLOCK in the factory. Euroform's experience with the machining centre was consistently good, leading to the purchase in 2022 of a latest-generation model with a 1,000 × 1,250 × 1,000 mm working envelope.
Watch the circular economy in action at booth W600 at NPE, running through May 10 at the Orange County Convention Center in Orlando, FL.
The DMU 100 P duoBLOCK 5-axis machining centre with PH Cell 2000 pallet storage and handling system on the shop floor at Euroform, Budapest.
Stefan Wolf, Euroform's managing partner said: "We play a pivotal role in automotive supply chains and our work begins in the early development phase of a new vehicle. Technical competence is crucial for exploiting the potential of innovative manufacturing solutions and CADCAM systems."
As Euroform almost exclusively manufactures one-offs, pallet handling such as the PH Cell 2000 is the optimal solution. Operators set up jobs offline on several pallets using a zero-point clamping system while machining is in progress on another mould, so production downtime is minimal, even at night.
Another focus that accompanies business development at Euroform is digitalisation. The company has had a paperless working environment for many years, from design through to quality control. The mould maker is an enthusiastic adopter of the digital 'my DMG MORI' app when it comes to online service requests, which Zwick said significantly accelerates the process of calling in a service technician.
When Euroform ordered the new DMU 100 P duoBLOCK, DMG MORI already had a large pallet handling system in development, based on the smaller, proven, modular PH Cell 300. The bigger capacity automation system handles pallets measuring up to 1,100 mm in diameter, so is able to deploy Euroform's 1,000 × 800 mm pallets. The PH Cell 2000 has twelve pallet positions on two levels and can accept workpieces up to 1,350 mm tall. (Other variants are available with three or four racks housing up to 17 or 21 pallets respectively.)
Euroform has been using machine tools from DMG MORI since 1995, latterly in a modern factory that it moved into in 2011 and expanded in 2016. Managing Director responsible for day-to-day business at Euroform, Krisztina Zwick, mentioned the supplier's broad machine portfolio and good service: "DMG MORI was one of the first machine tool manufacturers to open a subsidiary in Hungary, which meant that response times were always quick when service was required. Our latest investment in automation was necessary to utilise the machine during unattended shifts, giving us a competitive edge.”
Blood-collection vials made from medical-grade polypropylene are injection molded on the show floor, transported via a series of what look like pneumatic tubes to a shredder, upcycled via a twin-screw extruder, processed with various additives, and injection molded anew to produce the bottle opener pictured here. The process is apparently seamless.
A system of this type in a real-world application might be a bit of a stretch, but it is quite stunning to witness the metamorphosis of a plastic vial into a bottle opener in such an all-encompassing manner.
The firm currently uses eight machining centres from DMG MORI for tool production, including DMU monoBLOCKs, an HSC 75 linear and, most recently, a DMU 100 P duoBLOCK with PH Cell 2000 automation system for pallet handling to allow unattended production at night and during the weekends.
Editor in chief of PlasticsToday since 2015, Norbert Sparrow has more than 30 years of editorial experience in business-to-business media. He studied journalism at the Centre Universitaire d'Etudes du Journalisme in Strasbourg, France, where he earned a master's degree.
Based in the Hungarian capital Budapest, Euroform was established in 1993 to provide a tool and mould making service from design to production and trialling. Approximately 70 employees fulfil innovative solutions for a range of different injection moulding processes, mainly for customers in the automotive industry.
"With targeted investment in technology and the training and further education of junior staff, we will continue to successfully meet these challenges.”
This allows components to be produced with consistently high quality and little waste, another important contribution to greater sustainability, said KraussMaffei.
The vials are first molded using ExxonMobil PP 9074 MED on an all-electric PX 251-1400 injection molder. Thirty-two vials are produced per shot. For the purposes of this demonstration, the vials are transported to a grinder via the tubes and transformed into pellets in a matter of minutes.
KraussMaffei has set up a rather remarkable example of closed-loop circularity at booth 600 in the west hall at NPE2024.
GETTING A QUOTE WITH LK-MOULD IS FREE AND SIMPLE.
FIND MORE OF OUR SERVICES:
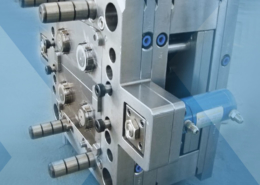
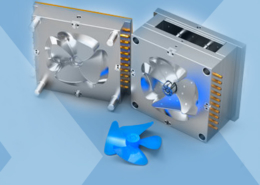
Plastic Molding

Rapid Prototyping
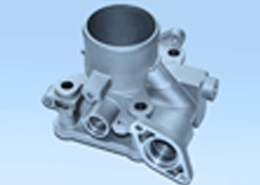
Pressure Die Casting
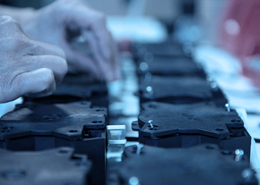
Parts Assembly
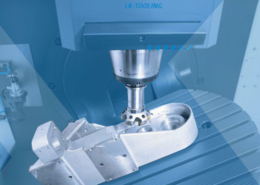