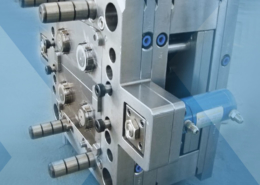
NOVA Chemicals Injection Moulding Unit, Calgary, Alberta - polyethylene molding
Author:gly Date: 2024-09-30
The exhibit uses a 4-cavity mould from Brink to produce thin-walled IML round cups from polypropylene (PP) using injection compression moulding. The flowpath/wall thickness ratio is 380:1. For process monitoring, the mould is equipped with six high-resolution inductive position measuring and embossing sensors. Four moulded parts, each weighing 10.4 grams and with a wall thickness of only 0.37 millimetres, are produced in a cycle time of 3.95 seconds. The plastic has a biomass footprint and ISCC-certified. Also integrated into the production cell is a side-entry robot from Brink that inserts the labels, removes the finished cups and stacks them on a conveyor belt.
In Metal Injection Moulding, as in all manufacturing industries, business can either be won by competing to be the lowest-cost supplier amongst fierce global competition, or by offering the most innovative technologies for the most demanding applications.
Discover suppliers of these and more in our advertisers’ index and buyer’s guide, available in the back of PIM International.
At its stand 3101 in Hall A3, ARBURG will be offering trade visitors nine exciting exhibits plus a whole host of information on sustainability, digitalisation and automation in the world of plastics. The fact that high-quality injection moulding technology can be an alternative to thermoforming will be demonstrated by an electric ALLROUNDER 720 A "Ultimate", for example, using injection compression moulding to produce thin-walled IML cups that can be easily recycled after use.
Metal Injection Moulding often has an aura of mystery around it. Whilst those in the industry understand the technology well, there are many ‘on the outside’ who are more apprehensive.
Extensive MIM, CIM industry and sinter-based AM industry news, plus the following exclusive deep-dive articles and reports:
If you were to place a bet on which country was going to take metal Binder Jetting to the highest volumes of commercial production, China would probably be high on your list. As the world’s manufacturing hub for consumer electronics, China already accounts for nearly half of global MIM sales by value. So with markets on the doorstep, and sintering capacity and metal powder supplies ready and waiting, where’s Binder Jetting in China? Here, Dr Q and Dr James report on developments, including a new Sintering Application Center at BJ–TECH Co. featuring HP’s Metal Jet technology.
Here, Dr Georg Schlieper reports from a recent visit to Germany’s Schunk Sintermetalltechnik GmbH, a company that has taken the latter path, setting itself the goal of being a leading supplier to the aerospace industry and, at the same time, offering its customers unique solutions for the next generation of MIM applications.
The 120-page Summer 2024 issue of PIM International (Vol. 18 No. 2) features over thirty pages of industry news, plus the following articles and technical reviews:
With this particularly resource-efficient application for the packaging industry, special emphasis was placed on energy efficiency and on a part design that saves materials. Thanks to the all-electric packaging machine in combination with injection compression moulding, the energy footprint is improved by 20 per cent with a significant reduction in part weight from 13 to 10.8 grams. The special "Next Cycle IML" label can be completely separated from the cup's PP during recycling, so that the product can be recycled by type after use. In contrast to thermoforming, no pre-produced foils are used and no stamping waste is produced.
For reliable performance, a slimline design and an unbeatable price, there is only one choice: the new ALLROUNDER 720 E GOLDEN ELECTRIC!
The arburgXworld customer portal gives you access to a wide range of digital apps and features that make your daily work easier.
Benefit from our expertise and lower the costs for your injection moulding production by optimising your energy requirement.
The free-to-access PIM International magazine archive offers unparalleled insight into the world of MIM, CIM and sinter-based AM from a commercial and technological perspective through:
Don't miss any new issue of PIM International, and stay up to date with the latest industry news. Sign up to our fortnightly newsletter.
For reliable performance, a slimline design, and an unbeatable price, there is only one choice: the new ALLROUNDER 720 E GOLDEN ELECTRIC!
In this article, Declan Coyle takes some of the mystery out of MIM technology in relation to tooling. Having gone through his own ‘MIM initiation’ process when tasked with developing the tooling for Apple’s Lightning connector in 2011, Coyle is well-positioned to offer some practical ‘do and don’t’ suggestions from a tooling engineer’s perspective.
Reach a truly international audience that includes component manufacturers, end-users, industry suppliers, analysts, researchers and more.
MIM2024, the International Conference on Injection Molding of Metals, Ceramics, and Carbides, was held in Raleigh, North Carolina, from February 26 to 28, 2024.
Attended by more than a hundred delegates from ten countries, this latest event in the well-established series was deemed to be an innovative success. This year was – to the relief of both attendees and the Metal Powder Industries Federation (MPIF) – an in-person only event.
GETTING A QUOTE WITH LK-MOULD IS FREE AND SIMPLE.
FIND MORE OF OUR SERVICES:
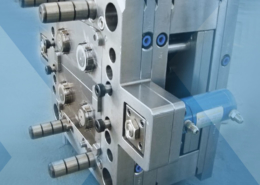
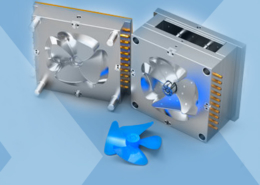
Plastic Molding

Rapid Prototyping
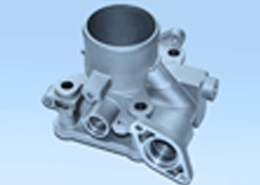
Pressure Die Casting
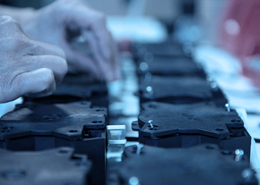
Parts Assembly
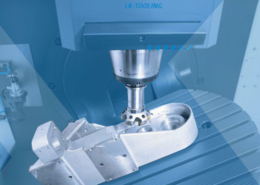