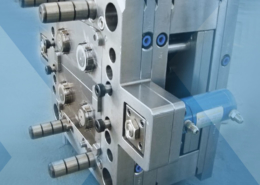
Nissei gearing up to open injection molding machine assembly plant in Texas - ni
Author:gly Date: 2024-09-30
The indelible imprint of injection moulding in medical manufacturing underscores its pivotal role in delivering efficient, high-quality, and cost-effective solutions to the industry. As the medical field continues to evolve, the synergy between injection moulding and emerging technologies like 3D printing is poised to drive innovation further, ensuring the continual enhancement of patient care and medical advancements.
Alpha Rho (Fitchburg, MA), an injection molder of rigid plastic boxes of various sizes and shapes, has decided to go solar. The company will produce more than 80% of its power requirements to run the company’s manufacturing, warehousing and administrative operations, according to President David Tall, who discussed this decision with PlasticsToday.
The solar energy system will be installed by New England Clean Energy on the roof of Alpha Rho’s 36,000-square-foot facility in April. It will have 745 Canadian Solar 320-watt panels, SolarEdge inverters with optimizers under each panel and Sollega racking and mounting hardware. The system is projected to deliver electricity savings of more than $1.6 million over 25 years (factoring in inflation). In addition, Alpha Rho will benefit from a new revenue stream created by the sale of solar renewable energy certificates (SRECs), arranged by New England Clean Energy.
Tall did his homework before deciding to put in solar. “I called around and talked to people in this business park who have solar and no one had anything negative to say. Everybody ran the numbers; on paper, it’s supposed to really save me a lot of money.”
“The return on investment with solar is phenomenal,” commented Tall. “The low cost of ownership thanks to the LFC lease, plus the SREC income and electricity savings, add up to a significant impact on our bottom line profitability, while we do something good for the planet at the same time.”
Tall figures he’ll save about $64,000 annually if the numbers work. “There’s definite savings to be had, but until you get up and running, you never really know,” he said.
Well-suited for products with straightforward shapes, injection moulding delivers unrivalled precision and finish quality. For medical applications such as moving machine parts or implantable devices, the procedure gives a vital smoother finish.
Luke Smoothy, founder and director, Get It Made, delves into why injection moulding still holds the sceptre in the medical industry and highlights the key benefits it brings.
Perhaps intriguingly is the fact that 3D printing and injection moulding are not exclusive of one another. Injection moulding is frequently preceded by 3D printing, which assists with prototyping and even helps create moulds for the injection moulding process.
In the realm of medical device manufacturing, the tussle between traditional injection moulding and modern 3D printing technologies continues. However, injection moulding has held its ground firmly, especially when high-volume production, cost-effectiveness, and precision are all paramount.
The environmental benefits of installing solar are “as appealing as the financial benefit.” Tall added, “the solar energy system will reduce the amount of carbon dioxide in the air by 412,800 pounds per year, which is equivalent to taking 39 cars off the road, or planting almost 150 acres of trees.”
To finance the solar, Alpha Rho opted for a seven-year traditional lease from LFC Capital Inc., which eliminated any upfront capital investment. Instead, Alpha Rho will make 100% tax-deductible fixed monthly payments, creating a low-cost path to ownership at a substantially reduced price.
Liquid silicone injection moulding: This produces pliable, durable parts in high volume, and is used in fabricating tubes and respiratory masks requiring high levels of hygiene and chemical resistance.
“I generate what I need for the plant and whatever I generate and don’t use goes back into the grid,” Tall said. “However there is some controversy currently in the legislature. Some want to increase the cap on the amount of unused electricity that goes back into the grid. Others, primarily the utility companies, are in opposition to raising the cap. That’s an issue. We’re on a waiting list for the net metering program, and I don’t know whether I’ll get it, but I’ll probably use most of what I generate, which will still give me a reduced electric bill through credits.”
An expansive range of materials are available with injection moulding, making it easier to produce medical equipment that adheres to the strict biosafety and chemical stability criteria of the medical sector. Techniques such as thin wall moulding and gas-assisted injection moulding enable the production of both practical and aesthetically appealing parts.
Thin wall moulding: A specialised form of conventional injection moulding that focuses on the mass production of ultra-thin (less than 1mm) and light plastic parts to make material cost savings. This is used to create portable medical devices enabling clinicians and patients to transport and operate them more easily - such as wearable devices, micro surgical tools, and invasive equipment like catheter ablation tools and endoscopes.
There will be some maintenance costs for the solar panels. The converters that turn the sunlight into energy tend to fail like any piece of equipment, which will require replacing them from time to time, Tall explained.
Until she retired in September 2021, Clare Goldsberry reported on the plastics industry for more than 30 years. In addition to the 10,000+ articles she has written, by her own estimation, she is the author of several books, including The Business of Injection Molding: How to succeed as a custom molder and Purchasing Injection Molds: A buyers guide. Goldsberry is a member of the Plastics Pioneers Association. She reflected on her long career in "Time to Say Good-Bye."
Because of the rebates and SREC, Massachusetts is a solar-friendly state to be in, even though it’s one of the more costly states for energy in the country. And while it’s not exactly the “sunshine state,” Tall said there are on average enough sunny days to make solar energy worthwhile.
Since the need for devices and components in the medical sector is always increasing, injection moulding stands out for its effectiveness and capacity to handle large-scale orders. The method is best suited for high-volume production, making it the preferred method for mass-producing medical components. That said, even though 3D printing is hailed for having cheaper initial costs in small-scale production, its cost advantage diminishes as production volume rises.
Gas-assisted injection moulding: In certain medical device applications, gas-assist moulding can provide solutions that conventional injection moulding can’t. The process consists of injecting a pressurised gas into the mould cavity after the initial plastic injection, expelling the molten plastic and forming hollow areas within the final product. It is suited to the manufacturing of complex parts without visual blemishes, for instance, tube- or rod-shaped parts which typically include handles and foot pedals, as well as large, cover-shaped structural parts e.g. side panels and covers for medical devices.
Tall explained that he has looked at solar a couple of times as a way to save money on his energy bills for the 12-press company. “Two previous times we looked at it, and it’s always seemed too good to be true,” said Tall. “This time we looked seriously at solar and decided that it is that good to be true. We’re a small business, so I wear a lot of hats and there are always so many things to think about other than solar power. On the third pitch, we looked more closely at what we can save and decided that financially it makes sense.”
GETTING A QUOTE WITH LK-MOULD IS FREE AND SIMPLE.
FIND MORE OF OUR SERVICES:
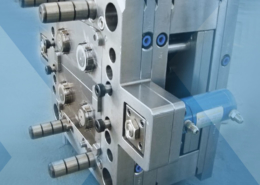
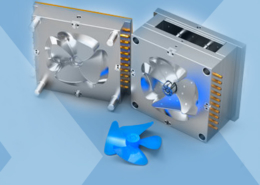
Plastic Molding

Rapid Prototyping
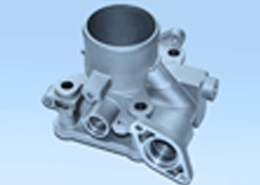
Pressure Die Casting
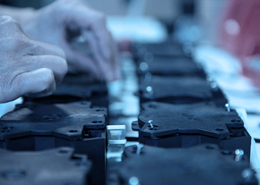
Parts Assembly
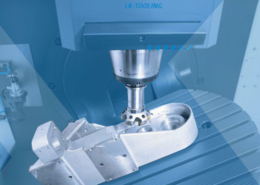