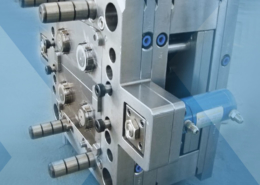
NexGenSolutions, CAE Services Combine on Molding Simulation - injection molding
Author:gly Date: 2024-09-30
Using fibre-reinforced systems and materials, the tools are said to function better than traditional 3D printed injection mould tools and eliminate the need to wait weeks for an aluminium tool.
So far, dental, automotive and electrical connector manufacturers have shown great interest in the scalable additive system and Schultz believes this appeal will only continue to grow. “We are just getting started,” he says. “The technology itself has so much potential, it’s going to be a game-changer for the entire additive industry.”
“I believe the growing use [in] tooling and moulding is due to the buying market maturing and the awareness of additive manufacturing increasing. Many companies are in the early phases of adopting additive manufacturing. Additive tooling wins are much lower risk than full adoption of additive manufacturing. Tooling in many ways is a perfect “gateway” application to customers’ transition to the new technology platforms of AM.”
For low-volume production, the Figure 4 affords the opportunity to save on part production costs. For instance, while an expensive tool will pay itself off with the manufacturing of hundreds of thousands or even millions of parts, the part cost goes up significantly if a smaller volume is required. With its easy scalability, digital molding is much more suited to producing Low-rate Initial Production (LRIP) small-batch runs. This, of course, is conducive to part customization, replacement part production and fast design iteration. For medium-volume production of certain small-scale parts such as dental fittings or automotive clamps, the Figure 4 system’s costs and turnaround times are comparable to injection molding.
The benchmark tests also show that the estimated costs for CAD, tooling design and tooling labor for the automotive vent were only $121 with the Figure 4 system compared to $4,315 for injection molding. Additionally, by eliminating the need for tooling altogether, digital molding also did away with a $4,850 internal tooling cost necessitated by injection molding.
By eliminating tooling requirements and speeding up the time to market, 3D Systems’ digital molding system also offers cost advantages to manufacturers. Notably, by eliminating various manufacturing steps associated with traditional manufacturing, digital molding delivers reduced labor, machining, iteration and testing costs.
By reinforcing the resin with engineering-grade ceramic microparticles, Fortify achieved optimum mechanics compared to other additive techniques, which suggests that Digital Tooling can offer comparable performance to aluminium soft tooling with shorter lead times and lower costs.
As an industry, additive manufacturing (AM) is seeking to disrupt industrial production practices that have been dominated by injection molding for over a century. Today, we are closer than ever to that reality: sophisticated 3D printing technologies are proving to be a viable means for fulfilling new manufacturing philosophies centered on quick turnarounds and smaller-volume production.
It is worth noting that injection molding process could catch up to the production rate eventually, with each part taking 55 seconds on average to fabricate.
The Fortify Digital Tooling material is the first launched by Fortify and believed to be the industry’s first microparticle filled DLP/SLA resin. By reinforcing this material with microparticle-sized engineering-grade ceramics, the company is able to produce additively manufactured tools that are stronger, stiffer, exhibit a higher heat deflection temperature, and an increased wear resistance compared to other 3D printed tooling. These are crucial metrics to maximise when designing a 3D printed tool due to the repeated exposure to high temperature polymers at high pressures.
Digital molding, on the other hand, does away with the tooling process altogether, going from CAD design straight to manufacturing. This means that manufacturers can iterate part designs, test them and adjust them for optimal performance without having to add significant tooling costs and, crucially, without adding time to the production process.
“We are currently focused on short run injection mould tooling - an application that has been attempted for years with limited success and adoption with other 3D print technologies,” Josh Martin, CEO and Co- Founder at Fortify, explained. “The primary reasons for this come down to a lack of performance of available polymer materials or challenging workflows with metals. Fortify Digital Tooling is different because we are reinforcing high-temperature thermoset systems with specialised ceramics to improve strength, stiffness, wear resistance and performance at temperature. When we couple this material system with DLP technology, we are able to achieve a surface finish that does not need secondary machining. So the complete package [offers] both higher performance and less processing. We are excited to explore other tooling applications where we can add value.”
3D Systems’ Figure 4 is one AM technology that has the potential to radically change how plastic parts are produced. Recently displayed at AMUG and RAPID + TCT 2018, the Figure 4 Production system enables digital molding for low- and medium-volume plastic parts. Unlike traditional injection molding, Figure 4 digital molding doesn’t require time-consuming, costly tooling processes.
No matter how advanced injection molding processes have become over the years, they are still encumbered by lengthy and costly tooling processes. Taking anywhere from weeks to months, the need to produce molds and other tooling equipment has presented limitations for the manufacturing sector. Most significantly, tooling processes have discouraged anything less than mass production, inhibited customization and limited design and design iteration flexibility.
Groups like Catalysis Additive Tooling specialise in creating injection moulded prototype parts that allow designers and engineers to run tests on a product and gather customer feedback before going into full scale production, de-risking investment in production tooling costs. Because of this need, it is invaluable for their customers to prototype their parts in their end-use plastic as soon as possible.
1,346 polymer and metal AM companies and 143 end-users. Consumer products AM generated $2.6 billion in 2023. Segment expected to grow to $28 billion by 2033 at 26.8% CAGR. This new market study fro...
Accelerating time-to-market when launching a new product is invaluable in enabling R&D teams to stay competitive. The need to produce agile prototypes faster and accurately evaluate the geometry, design, performance and feel of plastic injection moulded parts is necessary before creation of the final mould. However, the cost and lead time associated with machining aluminium soft tooling can make many iterations impractical for most organisations.
“With traditional methods, you need to make a temporary tool and then a hard tool and so on, and each one of those phases carries with it another qualification step. In the case of digital molding, we are able to go seamlessly into production,” commented Schultz.
To demonstrate the Figure 4’s competency compared to traditional injection molding processes, 3D Systems conducted a thorough benchmarking study using an automotive vent as the test part. The tests—overseen by a team of experienced engineers and executed by companies specializing in CAD/CAM, machining, injection molding and AM—ultimately showed significant differences in cost and time in favor of digital molding.
For this reason, injection molding is still largely beneficial for mass production runs. But for low rate initial production (LRIP) or low- to medium-volume manufacturing, digital molding has the benefit of drastically reducing the time to market for products.
More than that, by integrating multi-mode polymerization, 3D System’s Figure 4 technology is one of the few photopolymer-based printing platforms capable of producing hybrid-material parts. These hybrid materials offer properties such as toughness, durability, biocompatibility, temperature resistance and elasticity that are similar to injection molded materials.
“The modularity of the system is wonderful,” explains Phil Schultz, Senior Vice President of On Demand Solutions at 3D Systems. “It enables 3D Systems to configure the exact right solution for the customer’s needs. For example, the Figure 4 Modular version contains the main control unit and at least one print engine module; the main unit can control up to 24 print engines (there are four print engines in each module). The customized configuration can also include integrated cells for post-processing functions such as curing and washing.”
Overall, digital molding and 3D Systems’ Figure 4 system offer the means to produce plastic parts at astonishing rates and low costs for low to moderate volumes. In doing away with tooling stages, this modular additive manufacturing system is in a position to disrupt the machining-based manufacturing field, offering a beneficial complementary solution to injection molding.
The Figure 4 core technology, patented by 3D Systems’ co-founder Chuck Hull 30 years ago, is non-contact membrane Digital Light Printing (DLP). In the Figure 4 Production solution, the DLP technology is used in a series of connected print engine modules integrated with an automated robotics system to continuously produce plastic parts quickly and efficiently – enabling tool-less digital molding. The modular system is highly scalable and is built for easy integration into automated production lines.
The curing modules in Figure 4 Production are also notable. As Schultz explains, Figure 4 integrates a non-invasive light-based UV curing system which ensures a high level of repeatability and accuracy—especially when compared to thermal curing processes. Further ensuring accuracy and dimensional stability is the configuration’s previously mentioned non-contact membrane DLP technology which alleviates the printed part from all contact and potentially compromising forces (except gravity, of course!).
3D Systems’ digital molding technology also addresses another challenge commonly faced by the additive manufacturing industry: material diversity. Thanks to its fast print speeds (measured in millimeters per minute), the Figure 4 digital molding system is compatible with reactive plastic resins with short vat lives. That is because the Figure 4 printers turn out parts at impressive rates; resins are thus not required to sit in the vat for as long, significantly opening up the range of materials suitable for manufacturing. This increased range of materials edges digital molding closer to traditional injection molding by offering manufacturers the material properties they require for a range of applications.
At this speed, an eight-module Figure 4 machine is capable of producing 10,000 units of the textured automotive vent in just 11 days. Injection molding, for comparison, would still be in the tooling design stage at this point. For example, once conventional injection molding starts and has produced 10,000 units, Figure 4 will have produced 4,000 more units for a total of 14,000
When you visit any web site, it may store or retrieve information on your browser, mostly in the form of cookies. Control your personal Cookie Services here.
In one case, this led to a 35% reduction in cost compared to CNC machining and a 3 to 5 day lead time for over 200 parts produced using a tool measuring 100 x 95 x 150 mm. According to Fortify data, the same tool produced on a laser sintering system would have cost more than three times the amount for the same number of parts, while polymer material jetting would have been slightly cheaper but would only have provided 25 parts.
Figure 4 Production adds automation enabled by a system of robotic arms that carry the printed parts through the manufacturing process, pulling them from the resin vat to the washing, drying and curing modules.
Let’s take a closer look at the benchmarking results. Using an eight-engine Figure 4 configuration, the first automotive vent reportedly took 92 minutes to manufacture (the time from inputting the digital file) compared to a 15-day time-to-first-part for injection molding. Subsequent parts were turned out at a rate of one recurring unit every 95 seconds.
Traditionally, injection mould tools made for prototyping are produced by machining a large block of aluminium, which can cost thousands of dollars and is subject to long lead times, often upwards of six weeks. Boston-based composite 3D printing company Fortify has created a digital tooling process that gave Catalysis Additive Tooling the ability to create quick-turn injection mould tools at a fraction of the cost and time.
GETTING A QUOTE WITH LK-MOULD IS FREE AND SIMPLE.
FIND MORE OF OUR SERVICES:
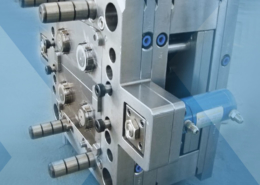
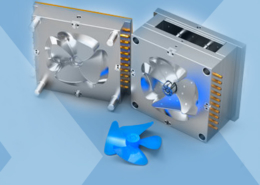
Plastic Molding

Rapid Prototyping
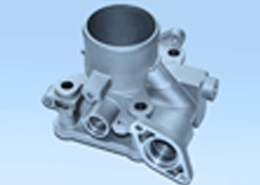
Pressure Die Casting
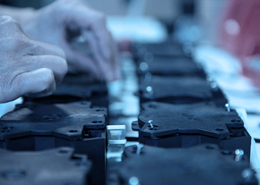
Parts Assembly
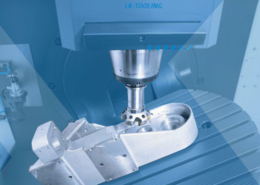