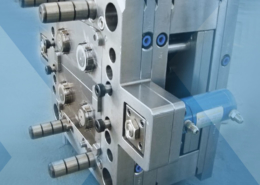
News in Hot Runners & Tooling At Fakuma 2014 - prototype and plastic mold
Author:gly Date: 2024-09-30
Prolonging tooling service life is of paramount importance for any moulding project since downtime for repairs jeopardises profit margins. According to estimates, around EUR 10 billion are spent each year for maintenance operations worldwide. During the moulding process, the friction forces developed between the closing surface and those contacting the injected plastic largely account for the damage caused to the surfaces. Ultimately, the mould needs to be scrapped. Put together, these significantly affect the mould’s service life. The EU-funded cleanMOULD project demonstrated novel coatings based on a multilayer diamond-like carbon formulation that prolong the life of injection moulding tools, offering corrosion protection, reduced wear and resistance to friction. “Importantly, our novel coating solutions increase mould performance and extend its operation before the need to take it out of service for preventive maintenance,” reports project coordinator Michael Hvam.
New owner Haartz Family Holdings is the investment branch of the Haartz family, which owns Haartz Corp., a global supplier of convertible toppings and interior surface materials for the automotive sector. It is based in Acton, MA, with additional manufacturing operations in Mannheim, Germany, and offices in Japan, China, and Mexico. The investment arm also has holdings in Peak Performance Compounding.
This is a machine translation provided by the European Commission’s eTranslation service to help you understand this page. Please read the conditions of use.
The transition to Moldgenix is supported by a substantial investment in three primary areas — processes, talent, and technology, said the press release. The Moldgenix brand will be rolled out across all company materials and communication channels.
A key attribute of the diamond-like carbon coatings is the ability to resist wear by lowering the friction between sliding surfaces. This largely eliminates the need for surface lubrication and post-finishing, which are deemed primary sources of pollutant releases to the atmosphere for certain industries such as pharmaceutical and food. The coatings are applied using a physical vapour deposition process called magnetron sputtering at temperatures as low as 180 °C. Due to this advanced deposition process, the diamond-like carbon coatings can maintain a very thin, uniform finish (1-5 μm) over the entire mould independently of its geometry. “cleanMOULD’s novel coatings optimise both surface hardness and lubricity to minimise the impact of fretting,” notes Hvam. The high hardness of the newly demonstrated diamond-like carbon coatings, which are 8 times harder compared to other coatings, allows the surfaces to become more resistant to scratches that occur during operation. It goes without saying that the absence of oil lubricants makes mould cleaning much easier: it only requires applying ethanol to a cloth for less than 10 minutes. cleanMOULD’s ‘mould breaking’ has the potential to become a key enabling technology for the entire plastics industry. Overall, the return on investment for cleanMOULD users is expected to be over 20 times the expected coating costs, thus providing a compelling value proposition. Pilot-test results demonstrated a sixfold decrease in the maintenance interval compared to state-of-the-art coatings. No fretting corrosion has been observed on any coated moulds. What’s more, “cleanMOULD’s coating demonstrated a decrease in the moulding cycle time of screw lids from 40 to 36 seconds, which is equivalent to an 11 % increase in productivity,” concludes Hvam.
The Informa Markets Engineering network of B2B media sites includes Design News, Battery Technology, Medical Device & Diagnostic Industry (MD+DI), Packaging Digest, PlasticsToday, and Powder & Bulk Solids.
A new low-friction, high-hardness coating is poised to expand the range of surface treatments to help tooling stand up to tough moulding challenges. The new diamond-like coating can increase the mould service life by up to 10 times compared to the state of the art.
Logging out of EU Login will log you out of any other services that use your EU Login account. Use the CORDIS log out button to remain logged in on other services.
Moldgenix adheres to scientific injection molding principles in producing tight-tolerance plastic parts for medical, dental, industrial, electronics, and consumer applications.
A change in ownership at Total Molding Services, a contract manufacturer supplying injection molding, tooling, and assembly services, has spawned a new name for the Quakertown, PA–based company. The new name, Moldgenix, implies via the Latin-derived word “genix,” the creation of molded products and better reflects the company’s innovative spirt and future-forward vision, it said in making the announcement today.
Permalink: https://cordis.europa.eu/article/id/418344-diamond-like-carbon-coating-offers-relief-to-plastic-injection-moulds
Telephones, PC parts, toys, electrical plugs, and other everyday products like shoes and pens are made with plastics using a process called injection moulding. The technology can produce identical parts at high volumes at a low cost per part. However, its start-up cost is relatively high, mainly because custom tooling is needed. An injection mould can cost anywhere between EUR 100 000 and EUR 300 000, depending on its complexity, material and accuracy.
GETTING A QUOTE WITH LK-MOULD IS FREE AND SIMPLE.
FIND MORE OF OUR SERVICES:
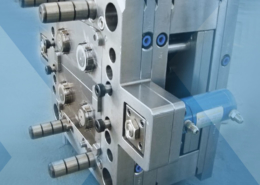
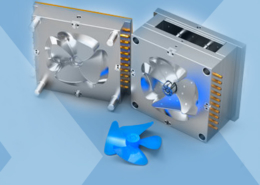
Plastic Molding

Rapid Prototyping
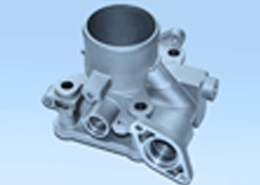
Pressure Die Casting
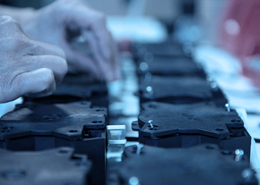
Parts Assembly
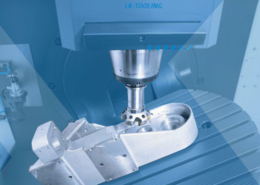