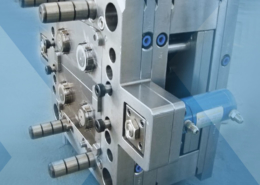
New Winbro machine speeds-up EDM drilling on large components - edm injection mo
Author:gly Date: 2024-09-30
“As part of our global vision, we believe it is critical to have a presence in Europe to better serve our medical and pharmaceutical customers, many of whom have global reach,” said Comar CEO Mike Ruggieri in a prepared statement. “APL has superb quality, best-in-class manufacturing, and a spectacular management team that can carry our strategic initiatives forward. We look forward to a successful partnership and continuing our growth journey together.”
Another area where Sumitomo Bakelite and Nissei Plastic are propelling innovation is in the encapsulation of circuit boards, which is conventionally carried out using the more costly and lower precision transfer molding process. Precision control of injection pressure at low levels is critical in this application to prevent damage to the circuit boards. “Typically, you need to limit injection pressure to less than 13 MPa and we have demonstrated on our FNX110III-18AK press that we can control pressure in the range of 6 to 10 MPa,” said Yoda.
At its in-house event, Nissei Plastic exhibited the 180-tonne clamping force NEX180III-5ELM all-electric press outfitted with a dosing system from Elmet and its own spiral plunger system that combines the first-in/first-out benefits of an inline screw with the dosing accuracy of a plunger system.
Speaking to PlasticsToday at the event in Japan, Nissei Plastic CEO Hozumi Yoda highlighted the fact that the “760” in the machine’s model name refers to the tie-bar clearance of 760 x 760 mm, rather than the clamping force of 3,540 kN (360 tons). “In general, we feel injection machines tend to be over-specified for the application at hand, with molders tending to ram the resin through the injection cylinder at high pressure and compensating for this with a higher clamping force in the case of thermoplastic molding,” he explained. “Our approach is to optimize injection pressure using our N-SAPLI low-pressure molding system and apply the minimal clamping force.”
Ireland is one of the world’s major medtech and pharmaceutical industry hubs — 14 of the world’s top 15 medical device manufacturers have a presence on the island and the manufacturing base exports €13 billion worth of goods to more than 100 countries annually, according to Enterprise Ireland. Comar said that the acquisition provides an exceptional foundation for supplying its multinational customers and grow in European healthcare markets. The combined company will have 11 manufacturing facilities and more than 1200 employees worldwide.
Comar, a supplier of custom medical devices and assemblies and specialty packaging, announced today it has acquired Automatic Plastics Ltd. (APL), a contract manufacturer of injection molded products primarily for the medical device and pharmaceutical sectors headquartered in Wicklow, Ireland. The deal represents Comar’s first step in a global expansion strategy.
The N-SAPLI control system can also be applied to thermoset molding to precisely control the flow of the liquid polymer into the mold, thereby raising the precision of the final part to a tolerance of 0.3 mm compared with the 0.7 mm typically achievable. “We are targeting a precision of 0.2 mm by applying N-SAPLI to the injection-compression molding of a thermoset resin,” added Yoda.
In business for more than 70 years, Comar provides injection molding, injection blow molding, injection stretch blow molding, and extrusion blow molding along with a full suite of value-added services. Headquartered in Voorhees, NJ, Comar is majority owned by Morgan Stanley Capital Partners.
Traditionally, thermoset injection molding has been utilized in Japan to mold relatively small components for the electrical sector, typically weighing in at 150 g or less. Nissei Plastic and Sumitomo Bakelite, however, have their sights set on components tipping the scales at 1 kg or more for applications such as e-axle invertor covers. Prototype parts molded on a Nissei FWX760III-130BK thermoset injection molding press using biomass-derived phenolic resin tip the scales at 1.4 kg but nevertheless are reportedly 50 to 70% lighter than conventional steel covers and 20 to 50% lighter than aluminum versions.
In operation for 50 years and led by owner and managing director Al Lawless and commercial director Andrea Cawley, APL specializes in custom design, development, molding, and assembly of medical devices and rigid pharmaceutical packaging. Its production facility, certified to ISO 13485, houses 30 injection molding machines ranging from 25 to 485 tons. The company has expertise in design and development, overmolding, two-shot molding, automation, packaging, and custom printing.
Aware that someday in the future the emergence of solid-state batteries might transform the material requirements of EV drive systems, this writer suggested a potential alternative application for the battery cell spacers being molded in Nagoya. He duly accepted two samples to take back to his base in Singapore and currently uses them as heat-resistant placemats.
Stephen has been with PlasticsToday and its preceding publications Modern Plastics and Injection Molding since 1992, throughout this time based in the Asia Pacific region, including stints in Japan, Australia, and his current location Singapore. His current beat focuses on automotive. Stephen is an avid folding bicycle rider, often taking his bike on overseas business trips, and is a proud dachshund owner.
Long perceived to be in decline, thermoset resin molding is being revived by two Japanese companies as a process with ample potential to contribute to lightweighting in electric vehicles (EVs). Injection machine builder Nissei Plastic and development partner Sumitomo Bakelite, a supplier of thermoset resins, held an in-house event at the Nagoya Congress Center on Aug. 2 to 4, 2023, in Aichi Prefecture, showcasing multiple thermoset molding solutions and more to 230 companies from the automotive industry, including OEMs and tiers. Home to Toyota Motor and Honda plants, Aichi is considered the capital of automobile manufacturing in Japan.
A third thermoset resin in Nissei Plastic’s liquid silicone rubber (LSR) has potential for applications in battery cell spacers as well as high-voltage EV battery connectors that are water-resistant, to boot. The current material of choice for battery cell spacers, which compensate for cell expansion and contraction during charging and discharge, is EPDM rubber.
Injection machine builder Nissei Plastic teams up with materials supplier Sumitomo Bakelite to expand adoption of EV components molded from phenolic and epoxy resins.
GETTING A QUOTE WITH LK-MOULD IS FREE AND SIMPLE.
FIND MORE OF OUR SERVICES:
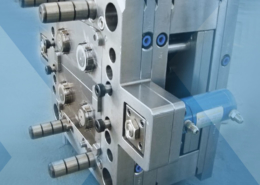
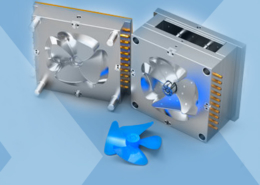
Plastic Molding

Rapid Prototyping
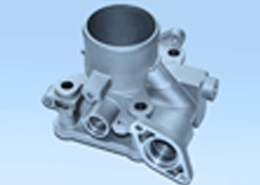
Pressure Die Casting
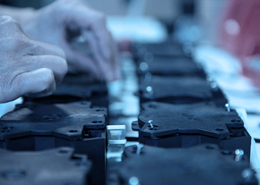
Parts Assembly
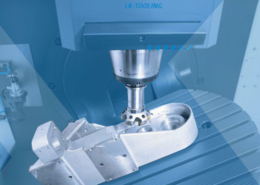