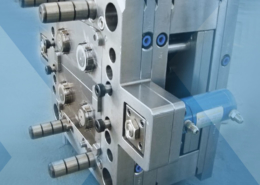
Exploring the Potential of Injection Moulding Aluminium
Author:gly Date: 2024-06-08
Injection moulding aluminium is a fascinating process that combines the versatility of injection moulding with the strength and lightweight properties of aluminium. This article aims to delve into the realm of injection moulding aluminium, providing readers with an insight into its capabilities, applications, and significance in the manufacturing industry.
Introduction: Unveiling the Advantages of Injection Moulding Aluminium
Injection moulding aluminium is a process wherein molten aluminium is injected into a mould cavity under high pressure, resulting in the production of intricate and lightweight components. This process offers numerous advantages over traditional manufacturing methods, including reduced material waste, faster production cycles, and enhanced design flexibility.
Strength and Lightweight Properties
Strength-to-Weight Ratio
Aluminium boasts an excellent strength-to-weight ratio, making it an ideal choice for applications where weight reduction is critical without compromising structural integrity. Injection moulding aluminium allows for the production of lightweight components that offer exceptional strength and durability, making it suitable for aerospace, automotive, and consumer electronics industries.
Complex Geometries
The injection moulding process enables the production of complex geometries with tight tolerances, allowing manufacturers to create intricate designs and features that would be difficult or impossible to achieve using conventional machining methods. This capability opens up new possibilities for product innovation and differentiation in various industries.
Heat Dissipation
Aluminium's excellent thermal conductivity facilitates efficient heat dissipation, making it an ideal choice for components subjected to high temperatures or thermal cycling. Injection moulding aluminium allows for the integration of cooling channels and heat sinks directly into the component design, enhancing thermal management and overall performance.
Applications and Industries
Automotive
In the automotive industry, injection moulding aluminium is used to produce lightweight yet durable components such as engine blocks, transmission housings, and structural components. These lightweight components contribute to fuel efficiency and performance while reducing vehicle emissions.
Aerospace
In aerospace applications, injection moulding aluminium is employed to manufacture lightweight structural components, aircraft interiors, and engine parts. The combination of strength, lightweight properties, and corrosion resistance makes aluminium an indispensable material for aerospace applications where weight savings are crucial.
Consumer Electronics
In the consumer electronics industry, injection moulding aluminium is utilized to produce lightweight and durable housings, heat sinks, and structural components for smartphones, laptops, and other electronic devices. The use of aluminium allows for thinner and lighter designs without sacrificing performance or durability.
Challenges and Future Directions
Material Selection
Despite its numerous advantages, injection moulding aluminium presents challenges related to material selection, process optimization, and tooling design. Future research efforts should focus on developing advanced aluminium alloys tailored to the injection moulding process, as well as optimizing process parameters to enhance productivity and component quality.
Surface Finish and Aesthetics
Achieving desired surface finish and aesthetics is another challenge in injection moulding aluminium, particularly for applications requiring decorative or cosmetic finishes. Innovations in surface treatment technologies and tooling design are essential for meeting aesthetic requirements while maintaining the efficiency and cost-effectiveness of the process.
Sustainability and Recycling
As sustainability becomes increasingly important, efforts to improve the sustainability of injection moulding aluminium processes and promote recycling of aluminium scrap are imperative. Developing closed-loop recycling systems and exploring alternative sources of aluminium will be crucial for reducing environmental impact and conserving resources.
Conclusion
Injection moulding aluminium offers a compelling combination of strength, lightweight properties, and design flexibility, making it a versatile and cost-effective solution for a wide range of applications across industries. As technology advances and challenges are addressed, injection moulding aluminium is poised to play an increasingly significant role in the manufacturing landscape, driving innovation and shaping the future of lightweight component production.
GETTING A QUOTE WITH LK-MOULD IS FREE AND SIMPLE.
FIND MORE OF OUR SERVICES:
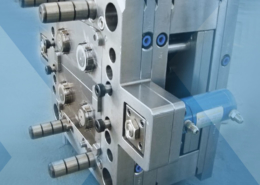
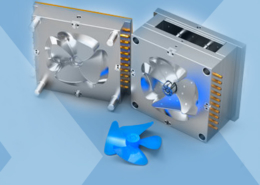
Plastic Molding

Rapid Prototyping
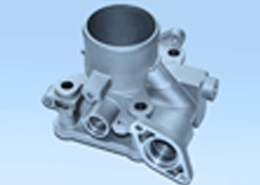
Pressure Die Casting
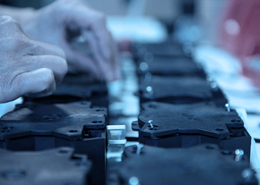
Parts Assembly
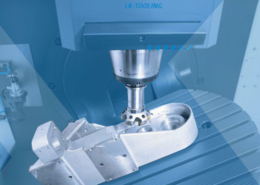