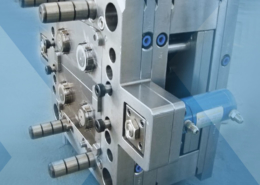
New technique for injection-molding glass - scientific plastic injection molding
Author:gly Date: 2024-09-30
“One of the biggest areas mould makers look at is the most efficient way to remove bulk material to near-net shape. Advances in ‘smart’ roughing toolpaths continue to dramatically drive down machining time. Of course, the precision and quality of the final mould is what matters most, and here shops are looking more closely at not just new toolpath motion, but new tools, all of which need to be supported by their programming software. Here we utilise four seats of the Edgecam CAM software.”
“We now have over 100 machines at our disposal. These include 3, 4 and 5-axis turning and milling machines from SNK, Mazak, Kitamura, Awea, Kaoming, Makino and Breton. On the grinding side we have machines from Studer, Kellenberger, Bahmuller, Okamoto, Perfect, SNK and Estarta. They cover our requirements of external and cylindrical grinding, centerless cylindrical grinding and horizontal plate grinding.”
Rakez offers entrepreneurs, startups, SMEs, and manufacturers a wide range of solutions, including free zone and non-free zone licenses, customizable facilities, and first-class services provided in a one-stop-shop. Furthermore, Rakez has six specialized zones that are tailored to specific needs of investors: a Business Zone for commercial and service companies; Al Ghail, Al Hamra and Al Hulailah Industrial Zones for manufacturers and industrialists; a Media Zone for creative firms; and an Academic Zone for educational providers.
Rakez is a business and industrial hub established by the Government of Ras Al Khaimah in the United Arab Emirates. It currently hosts over 14,500 companies coming from over 100+ countries and operating in more than 50 industries.
“With faster metalcutting through high-speed machining (HSM) and improved EDM techniques, mould and die shops are finding innovative ways to compete with manufacturing operations in traditionally low-cost labour markets. We at UTP Mould & Die are helping them to achieve their goals.”
“Currently being installed is our new Mitsubishi MV-4800S WEDM, which is the biggest WEDM that WD Hearn has supplied to a client in South Africa. The dimensions of the workpiece for this machine are XYZ of 1 250 x 1 020 x 550mm and a weight of 3 000kg. This is a big machine that can handle big workpieces for us on a table size of 1 080 x 780mm.”
Adapting to the changing times is imperative for these manufacturers of a tool that will ultimately produce a product that will end up being critically examined by the consumer – whether it be on your supermarket shelf or on some form of transport.
As a result, tool makers can’t rely on old business models but must instead focus on targeting niche markets and developing specialised products, materials, processes and customer knowledge in order to survive in today’s market. In other words, they must try to compete on value instead of cost.
“We therefore need to invest in our equipment. We have purchased a Kitamura MyBridgeCenter 8G 3-axis bridge type machining center with linear scale feedback in all axis. The machine has XYZ travels of 2 000 x 1 200 x 800mm and can accommodate a workpiece mass of 3 500kg. Rapid feed rates are 24m/min and the spindle motor is 22kW.”
Ras Al Khaimah Economic Zone (Rakez) has recently added another giant Indian conglomerate to its client portfolio — Motherson Sumi Systems Ltd (MSSL), one of the global leaders in the field of automotive wiring harnesses. MSSL is set to produce a broad portfolio of products including wiring harnesses, rearview mirrors for passenger cars, injection-molded parts and many more from its Rakez manufacturing unit.
“Additionally, we realised that to remain competitive while offering quality we had to start importing our own plate. Five years ago we were appointed the exclusive distributor in South Africa for Toolox 33 and Toolox 44, both manufactured by SSAB Sweden and used as the general standard of material used in the industry. The 60 tons that we hold in stock come in plate thickness from 14mm to 165mm and sheet sizes of 1 250 x 2 050mm. This material is a modern and improved equivalent of 2312 and 2311 pre-hardened tool steel available in 33HRc and 44HRc.”
The second Kitamura machine is a Mycenter 4XiD with travels of 1 000 x 600 x 600mm and a maximum workpiece load of 2 000kg
“This is not the maximum size plate that we process. We are capable of processing plate from 156 x 156mm up to 1 200mm x 2 000mm.”
Mould base and press tool die sets preparation “There are a number of steps that go into delivering someone’s idea of a new design for the packaging of your favourite sauce or beverage, for example, before it is delivered to you the consumer. Many of us have no idea of the amount of processes, checks and inspections that have to be completed first and that is even before the product is labelled. The advent of additive manufacturing and 3D printing is also skewing the reality. The uninformed are expecting the same high volume results as achieved by the traditional engineering methods.
UTP Mould & Die invests in imported high quality steel from Sweden, 5-axis machining and WEDM to help keep you ahead of the competition.
“What impresses me with this machine is that the positioning accuracy is 0.002mm and the repeatability is 0.001mm – accuracies that we need in our type of work.”
“We realised that mould and die manufacturers, as was the case of our own company, were wasting many hours on their plate and base preparation, as well as the sourcing and machining of associated componentry such as pins and bushes.”
UTP Mould & Die has three SNK 5-axis machines that have a maximum travel of 1 500 x 1 200 x 1 000mm and a maximum workpiece mass of 7 000kg
“For example plate roughing for all complex cavity and core plates can be pre-machined leaving 0.3mm for final machining. We also offer stress relieving after machining and regrinding of bottom surface before delivery. What is important is that we are not in competition to the 1 200 odd clients that we have on our books. Our services are precision components for plastic injection moulds, foundry locating components, machine parts and production assembly lines. Typical components include mould bases, mould inserts, extrusion dies, press tools, pillars and bushes, moulding box bushes, pattern pins and machine spares.”
“Recently, the globe-shrinking effects of advanced transportation and communication technologies, as well as the cheap material and labour costs associated with the Asian countries, have put these companies under even more pressure.”
Welcoming MSSL to the Rakez family, Ramy Jallad, Group CEO of Rakez, said: "We consider the coming of Motherson to our thriving industrial ecosystem as another significant milestone in our commitment to underpinning the industrial growth in the emirate. This very industry is among the leading contributors to the emirate's stability and strength in tackling economic headwinds. I'm sure that Motherson is one of the great additions we are going to have this year."
“In a mould shop, the model of the customer’s part gets used in two parallel processes. One of these is core and cavity machining, in which CAM software generates complex tool paths to let CNC machining cut the shape of the part in metal.”
Kitamura MyBridgeCenter 8G 3-axis bridge type machining center with linear scale feedback in all axis. The machine has XYZ travels of 2 000 x 1 200 x 800mm and can accommodate a workpiece mass of 3 500kg. Rapid feed rates are 24m/min and the spindle motor is 22kW. A NC-4 non-contact toolsetting/toolbreakage detection/ tool wear detection system and an OMP40 work piece measuring probes kit has also been installed on both machines
“Our previous investment in equipment, which was about the same time we purchased the Behringer in 2017, was for two surface grinders from Taiwanese manufacturer Perfect. The bigger of the two accommodates plate up to 1 200 x 2 000mm, which fits our profile perfectly and we believe it is the biggest surface grinder in South Africa.”
Custom component machining “Another area that we found we could specialise in and save our clients time and money in was the manufacture and supply of the custom components associated with the moulds, components such as pins and bushes. Mould manufacturers have the equipment to manufacture these types of components but do they have the time? They certainly don’t have the volume.”
“There was a niche in the market that nobody was really exploring and still today they do not. We understood that if we could specialise in this area of the process we would become the friend of many mould, tool and die manufacturers. By adding the complementary press tool die set machining as well as the associated componentry machining capabilities it enabled us to refer to ourselves as the specialists in the industry.”
Adding value is not just a matter of offering more services. There are many processors who have grown their businesses in recent years by providing additional services such as finishing, decorating, assembly, packaging and cataloguing products for their OEM (original equipment manufacturer) customers. It is, however, becoming increasingly difficult for processors to receive a fair profit for these added services unless they are tied to a specialty. Such a specialty could be an in-house painting line, or a vacuum metalising or electroplating capability. In short, the key is to combine added services with specialisation.
“Milling critical mould surfaces to final size literally leaves no margin for error. This takes absolute confidence in every aspect of the machining process, as well as absolute confidence that the results are worthwhile. Both a small mould for a toaster and a large mould for an automobile bumper must produce parts that are mechanically and cosmetically correct.”
Tool making has undergone a cultural shift, moving away from being considered a craft demanding high degrees of skill to being increasingly viewed as a commodity – something that anyone can perform with the right technological tool at hand, such as 3D parametric solid modelling, rapid tooling and high-speed machining.
Two new Kitamura CNC high-speed milling machines, a Mitsubishi MV-4800S WEDM and a Behringer LPS 60 plate saw UTP Mould & Die have recently invested in two new Kitamura CNC high-speed milling machines and a Mitsubishi MV-4800S WEDM, which were supplied by WD Hearn Machine Tools. The Behringer LPS 60 plate saw was supplied by Elquip Solutions.
UTP Mould & Die is based in Krugersdorp Gauteng with two ultra modern factories spanning 3 600m². UTP employs 55 staff of which 30 are tool technicians. The company is also very active in employing and training technicians associated with the government’s NTIP programme. UTP Mould & Die has been awarded the ISO 9001:2015 quality certification by TUV Rheinland accreditation.
What steels can UTP supply? Exclusive importer and distributor of Toolox UTP can manufacture custom and customised bases and plates for moulds and press tooling from all locally available tool steels, aluminium and mild steels (e.g. 1.2311, 1.2312, 1.2344, 1.2067,1.2083, 1.2316 and Coroplast).
“The second Kitamura machine is a Mycenter 4XiD with travels of 1 000 x 600 x 600mm and a maximum workpiece load of 2 000kg.”
“We decided to manufacture a limited amount of the commonly known DME range and provide a service of off-the-shelf availability. At the same time we signed an exclusive import and distribution agreement with well-known Italian mould and press component manufacturer Pedrotti Mould and Press Components. They manufacture mould elements for plastic injection, die-casting and metal stamping such as springs, guiding pillars and bushes. We hold a large stockholding of these components.”
“On our gun drilling side we have three machines. The unique machine in this department is our Ixion Auerbach plate gun drilling machine. As far as we know we are the only company with this type of machine in South Africa. What sets us apart is this machine’s capabilities. The deep hole or boring machine, as it is sometimes referred to, has travels of 1 200 x 2 000 x 400mm and is capable of drilling holes up to 1 000mm deep on all four sides. No one else can do that in South Africa.”
“Furthermore, to meet the accelerating pace of product design and time-to-market, major corporations have also taken to outsourcing high-level engineering and production tasks. Subcontractors and service providers find themselves bidding not just to provide parts, but to assist their customers in executing core functions of the product development process within ever tighter time frames.”
“This is what we did when we acquired the company in 1999. UTP Mould & Die was first established in 1959 by KH Trautwein of Germany, who identified the enormous potential in developing a local mould and die making facility to European standard. For awhile we continued with this line of manufacturing but then we changed strategy.”
“Make it fast and accurate. An all too often heard demand from customers. However, those of us in this industry must realise that this is not a growing trend but a must for this industry.”
Unique plate gun drilling machine “On our gun drilling side we have three machines. The unique machine in this department is our Ixion Auerbach plate gun drilling machine. As far as we know we are the only company with this type of machine in South Africa. What sets us apart is this machine’s capabilities. The deep hole or boring machine, as it is sometimes referred to, has travels of 1 200 x 2 000 x 400mm and is capable of drilling holes up to 1 000mm deep on all four sides. No one else can do that in South Africa.”
“We even have a dedicated round parts production department. 3D CMM measurement, checking fixtures, tryout and other inspection procedures are all part of our make-up. We even offer fixture and jig manufacture as well as assembly.”
Currently being installed is a new Mitsubishi MV-4800S WEDM, which is the biggest WEDM that WD Hearn has supplied to a client in South Africa. The dimensions of the workpiece for this machine are XYZ of 1 250 x 1 020 x 550mm and a weight of 3 000kg
Many operations, many machines “However, plate and base preparation requires operations such as cut-to-size, squaring, grinding, milling and drilling, amongst others, and despite the advancement in machines, tooling and software, many hours can be spent on this area of the process.”
UTP Mould & Die imports and distributes product from well-known Italian mould and press component manufacturer Pedrotti Mould and Press Components
Vivek Chaand Sehgal, Chairman of MSSL, said: "We are very glad to have taken this important step of setting up our manufacturing facility in the fast-growing emirate of Ras Al Khaimah. This provides us great opportunities for larger exposure to the global markets. We are truly proud to be working in conjunction with Rakez, which is among the leading economic zones in the region."
“Manufacturing critical mould surfaces to final size literally leaves no margin for error. This takes absolute confidence in every aspect of the machining process, as well as absolute confidence that the results are worthwhile. It is no different for plate and base preparation. We are at the beginning of the process and need to supply product that adheres to micron specification.”
Indeed, the die and mould industry has experienced tremendous change: It’s no longer simply a craft but a multifaceted business. And to thrive in this intensely competitive environment, die and mould makers must learn to specialise, beef up services, add value to products, and seek niche markets.
Other machining services include plate roughing for all complex cavity and core plates that can be pre-machined leaving 0.3mm for final machining
Another investment has been in a Behringer LPS 60 plate saw. It is a compact vertical bandsaw that can cut plate up to 720mm and 1 260mm in length. This is not the maximum size plate that UTP Mould & Die can process. They are capable of processing plate from 156 x 156mm up to 1 200mm x 2 000mm
MSSL recently held a groundbreaking ceremony at Rakez Al Hamra Industrial Zone to mark the beginning of the construction of its factory which is presently being built on a 21,000-m2 site. The company's operations are expected to officially commence on the 2nd quarter of 2020.
UTP Mould & Die have recently invested in two new Kitamura CNC high-speed milling machines supplied by WD Hearn Machine Tools. Renishaw probing cycles have been installed on the two Kitamura machines. Another major selling feature on the Kitamura is the Arumatik control, which is a 19” touch screen Icon based control system
“Additionally, you need many different types of machines to perform the required operations – bandsaws, surface grinders, turning, slotting, honing, broaching, wire cutting and EDM, milling and drilling, including deep hole gun drilling. Not all plates and bases require all of these operations but in most cases they do.”
Other machining and services “We are not limited to custom machining of the bases, plates and press tool die-sets. If a customer requires customised work to be done we are quite capable of doing it. We have the machinery, technicians and design staff that can carry out the specialised machining services required.”
The Emirate of Ras Al Khaimah will host the new factory for auto wire harnesses, rearview mirrors for passenger cars, injection-molded parts
“Mould, die and press tool manufacturing has always been a tough, competitive business. Additionally, mould makers and press tool manufacturers are under constant pressure to speed up the mould and press tool manufacturing process, improving their processes and product quality, while boosting productivity. To meet their goals, these companies employ the latest mould making software, leveraging new techniques in CAD/CAM and CAE, with vastly improved simulations for conformal cooling and other key features in mould and die manufacturing,” explains Markus Funk, Managing Director of UTP Mould & Die.
Stephen has been with PlasticsToday and its preceding publications Modern Plastics and Injection Molding since 1992, throughout this time based in the Asia Pacific region, including stints in Japan, Australia, and his current location Singapore. His current beat focuses on automotive. Stephen is an avid folding bicycle rider, often taking his bike on overseas business trips, and is a proud dachshund owner.
“The other process is mould base and plate machining. Here, the work is less likely to flow so smoothly. Mould design software may be used to model the bases and plates based on the core/cavity geometry, but the automation usually ends after that.”
Globalisation is making this traditionally competitive business even tougher. As a result, die, mould and press tool manufacturers must rethink both their short-term and long-term strategies. The tooling industry as a whole – which counts die makers, mould makers and press tooling manufacturers as its three most prominent groups – is not just experiencing a temporary decline but a complete restructuring with far-reaching implications. The sweeping changes in the industry are reflected in mergers and acquisitions, as well as in new cooperative and collaborative endeavors entered into by small and medium-sized tool shops.
“Cores and cavities are complex only in terms of geometry. Plates and bases are complex in a different way. While the tool paths to machine a plate may be simple indeed – just a series of hole-making plunges – the complexity comes in choosing the tools and operations. A plate with 100 or more holes might require dozens of center drills, drills, chamfers and taps in various combinations. Some holes will also call for a choice between drilling and helical milling. In other words, the complexity of a plate lies in the knowledge necessary to machine it.”
Using additive technologies to create value in manufacturing and industrial workflows, like using 3D-printed tooling to bridge from prototype to production is here to stay and will reduce lead times. By not recognising this fact you do so at your own peril. The trick is to leverage the technology to your advantage.”
The company also has a Mazak HCN6000 CNC horizontal machining center with XYZ travels 1 000 x 900 x 600mm and a maximum workpiece mass of 1 000kg
GETTING A QUOTE WITH LK-MOULD IS FREE AND SIMPLE.
FIND MORE OF OUR SERVICES:
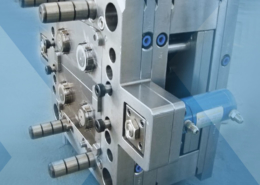
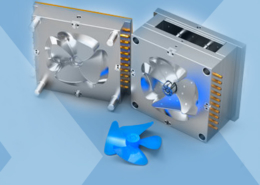
Plastic Molding

Rapid Prototyping
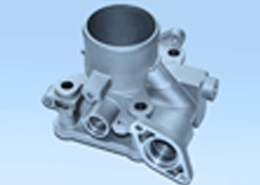
Pressure Die Casting
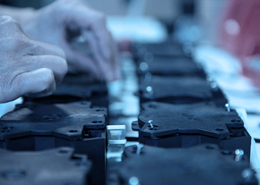
Parts Assembly
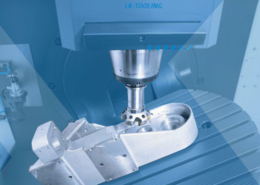