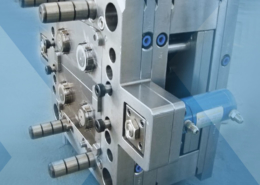
New Pendulum acquires Bardot Plastics to expand plastics portfolio - plastic inj
Author:gly Date: 2024-09-30
IME South comes to the Charlotte Convention Center in Charlotte, NC, on June 4 to 6, 2024. In addition to more than 300 exhibitors on the show floor, the event features more than 40 educational sessions led by experts in 3D printing, medical technology, packaging, and smart manufacturing. A welcome reception is scheduled at the NASCAR Hall of Fame on June 4. Tickets are available for purchase when you register to attend.
To avoid operating errors, the drums can be changed fully automatically from the drum rim from three sides within two minutes. Intuitive operation of the system, the use of simple clamp connections, a guided drum change procedure and an integrated cooling system mean even relatively low-skilled personnel can operate it without any problem. Fully automatic venting as standard completes the system’s many and varied safety and convenience features.
Due to the optimised design of the follower plates, just 40 ml of residues are left behind when the 20 litre drums have to be changed, resulting in material utilisation of up to 99.8%. With a design service life of 20 years or more for all its mechanical components, a modular structure and particular ease of servicing which keeps maintenance costs low, the TOP 700 is synonymous with cost-efficiency. Its low energy consumption of less than 50 Wh and minimal compressed air consumption also help to keep costs down.
Vertical integration enables the company to operate as a one-stop partner in the development and manufacture of medical devices and components, added Runyan. “Under one roof, Accumold offers design and material assistance, micro tool fabrication, proprietary micro-molding services, cutting-edge metrology, assembly, and automation, and this facilitates the streamlining of customer’s medical product development process, and the attainment of optimal outcomes in terms of timeliness, cost, and accuracy.”
In booth 1911, Accumold will be showcasing some of the tiny titans it has produced to exacting specifications for medical device OEMs over its nearly 40-year history. A highlight are thin-walled cannulas that the company can now micro injection mold at volume.
The company routinely molds cannulas at volume with outside diameters of 0.035 in. (0.889 mm), inner diameters of 0.027 in. (0.6858 mm), and wall thicknesses measuring 0.004 in.(0.1016 mm). “We have achieved this through attention to material choice, several critical design for manufacturing operations, assembly considerations, maintaining a balanced aspect ratio to avoid challenges associated with flow dynamics, cooling, structural integrity, and importantly through the use of our proprietary micro-molding presses,” explained Runyan. “Micro molding thin-walled cannulas is a game changer for medical device manufacturers, overcoming the labor-intensive, time-consuming, and expensive traditional thin-wall cannula manufacturing processes such as extrusion, tipping, and gluing to a metal hub.”
The TOP 700 can achieve delivery rates of over five litres/minute at a maximum pump pressure of 210 bar, so enabling short cycle times both when filling larger parts and with large numbers of small cavities. Additives and colours can be dispensed from 1, 4 and 20 litre containers. In order to achieve the dosing precision that is particularly vital for very small parts, the volumetric meter for colours has a resolution of below 0.1 μl/l. Depending on requirements, dosing can be carried out simultaneously or in a freely selectable mixing ratio.
Now that NPE2024 is history, there are some admittedly smaller but still worthy trade shows on the horizon for sourcing suppliers of plastics processing services. One that you may want to consider attending is Plastec South, co-located with Medical Design & Manufacturing (MD&M) alongside packaging, automation, design and manufacturing, and Powder Bulk Solids trade shows under the IME South umbrella in Charlotte, NC. In particular, a pioneer of medical micro molding will be exhibiting at the event in June.
The ISO 13485–certified company is sufficiently large to offer affordable pricing and the capacity and infrastructure to ramp up to full mass-volume manufacturing, he added.
TOP 700 provides the same high precision dosing of silicones and additives as Elmet’s flagship TOP 7000 Pro dosing system with its 200 or 20 litre drum size which was launched back in 2021.
Thorsten Häuser, development manager, explains: “We developed our TOP 700 dosing pump to meet customer demand for a space- and material-saving solution from ELMET. We’ve achieved this with a footprint of less than 0.5 m² (799 mm × 600 mm) and our new pump design. As a result, this new dosing system is particularly suitable not only for customers processing high-value, shear-sensitive or abrasive materials but also for R&D, prototyping and small-batch applications. The TOP 700 rounds out our product range while setting new standards in compact dosing technology.”
Editor in chief of PlasticsToday since 2015, Norbert Sparrow has more than 30 years of editorial experience in business-to-business media. He studied journalism at the Centre Universitaire d'Etudes du Journalisme in Strasbourg, France, where he earned a master's degree.
Designed to be FDA- and EMA-compliant, the new TOP 700 dosing system is used for applications requiring the highest levels of cleanliness such as medical technology, personal care, foodstuffs and optics. Virtually abrasion-free pumping also prevents metal particle contamination of the LSR which would impair its functionality. There are also no limits to the consistency of the processed LSR under real-world conditions because Elmet’s new system can dose any commercially available product with the same precision thanks to its ability to handle viscosities of between 0.001 Pas and 2000 Pas (shear rate 10/s) or 16,000 Pas (1/s). Its optionally OPC UA- and Euromap 82.3-compliant control system can be seamlessly integrated into the injection moulding machine’s own control system.
Exhibitor Accumold will explain how micro molding thin-walled cannulas reduces labor requirements and cost compared with conventional production methods.
“Accumold is rightly today acknowledged as the world leader when it comes to the manufacture of extraordinarily small plastic parts that require extreme precision — typically measured in microns,” said Paul Runyan, VP of sales and marketing. “The company is adept at the production of small-sized parts with micro features from 5 cm to less than 1 mm, and has specific expertise in insert molding, two-shot molding, and cleanroom molding using an array of materials including PEEK, liquid crystal polymers, and most engineering thermoplastics.”
The medical device industry demands absolute precision, totally repeatable manufacturing processes, and zero failure rates for products that are frequently used in safety-critical applications, notes Accumold in its announcement.
GETTING A QUOTE WITH LK-MOULD IS FREE AND SIMPLE.
FIND MORE OF OUR SERVICES:
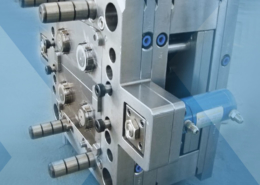
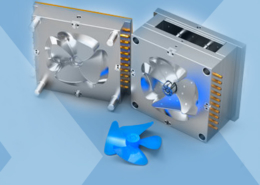
Plastic Molding

Rapid Prototyping
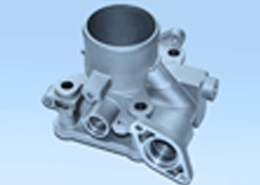
Pressure Die Casting
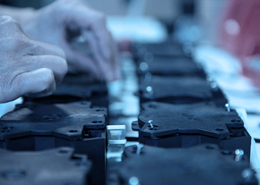
Parts Assembly
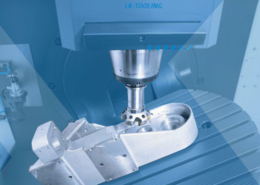