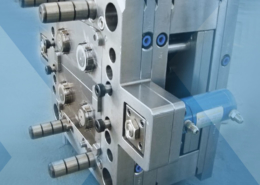
Exploring the Innovations in Injection Molding of Medical Plastics
Author:gly Date: 2024-06-08
Injection molding of medical plastics represents a groundbreaking advancement in the field of healthcare manufacturing, offering unparalleled precision, efficiency, and customization. This article aims to delve into the intricacies of this transformative technology, shedding light on its applications, advantages, challenges, and future prospects.
Introduction to Injection Molding of Medical Plastics
Injection molding is a manufacturing process wherein molten material is injected into a mold cavity under high pressure, allowing it to cool and solidify into the desired shape. In the realm of healthcare, this technique finds extensive use in producing a wide array of medical devices, equipment, and components, ranging from syringes and catheters to implants and surgical instruments.
Advantages of Injection Molding in Medical Plastics
1. Precision and Consistency
One of the primary advantages of injection molding in medical plastics lies in its ability to achieve unparalleled precision and consistency. The controlled injection of molten material into precise mold cavities ensures the production of components with tight tolerances, critical for medical applications where accuracy is paramount.
2. Complex Geometry
Injection molding enables the fabrication of medical devices with complex geometries and intricate features that may be challenging or impossible to achieve through traditional manufacturing methods. This capability allows for the design and production of innovative medical devices tailored to specific patient needs, enhancing treatment outcomes.
3. Material Selection
The versatility of injection molding extends to the wide range of medical-grade plastics available for use. Manufacturers can select materials with properties tailored to the requirements of specific applications, such as biocompatibility, sterilizability, and chemical resistance, ensuring the safety and efficacy of medical devices.
Applications of Injection Molding in Medical Plastics
1. Implantable Devices
Injection molding plays a crucial role in the production of implantable medical devices, including orthopedic implants, dental prosthetics, and cardiovascular stents. The ability to fabricate precise, biocompatible components enables the development of implants that integrate seamlessly with the human body, promoting healing and restoring function.
2. Disposable Medical Products
The manufacturing of disposable medical products such as syringes, IV components, and diagnostic consumables heavily relies on injection molding. Mass production of these items with consistent quality and cost-effectiveness is made possible by the high throughput and repeatability of injection molding processes.
3. Drug Delivery Systems
Injection molding is instrumental in the production of drug delivery systems, including inhalers, insulin pens, and transdermal patches. The ability to precisely control the size, shape, and surface properties of these devices ensures accurate dosage delivery and patient compliance, enhancing the efficacy of pharmaceutical treatments.
Challenges and Future Directions
While injection molding of medical plastics offers numerous benefits, it is not without challenges. Issues such as material selection, regulatory compliance, and manufacturing validation require careful consideration to ensure the safety and reliability of medical devices. Additionally, ongoing research is focused on advancing materials, process optimization, and integrating emerging technologies such as additive manufacturing to further enhance the capabilities of injection molding in healthcare.
Conclusion
Injection molding of medical plastics stands at the forefront of healthcare manufacturing, driving innovation and improving patient care. Its ability to produce precise, customized components for a wide range of medical applications underscores its significance in modern healthcare. By addressing challenges and embracing advancements, the future of injection molding in medical plastics holds immense promise, paving the way for continued advancements in healthcare technology and patient outcomes.
GETTING A QUOTE WITH LK-MOULD IS FREE AND SIMPLE.
FIND MORE OF OUR SERVICES:
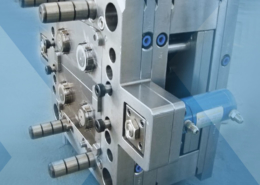
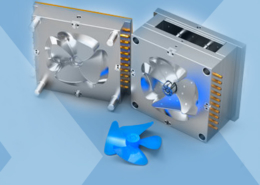
Plastic Molding

Rapid Prototyping
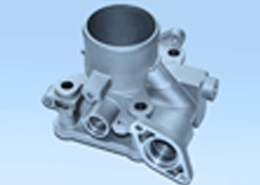
Pressure Die Casting
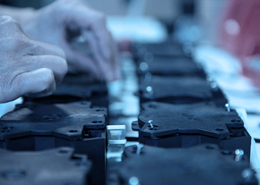
Parts Assembly
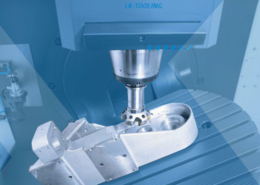