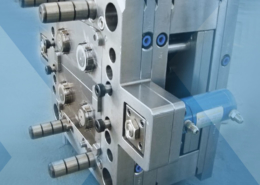
New LSR Cold Deck - cold injection molding
Author:gly Date: 2024-09-30
Absolute Haitian is exhibiting at Plastec West this week at booth 3955. The show runs Aug. 10 to 12 at the Anaheim Convention Center in Anaheim, CA.
XLPE foam ducts boast several advantages compared to blow-molded, rigid PP ducts that are commonly used at present according to Illig. For example, ducts molded using XLPE foam (density of approximately 70 to 80 kg/m³ depending on the application) are not only substantially more lightweight than ducts made of solid PP (density of 900 kg/m³); among other properties they also possesses substantially lower heat conductivity and superior acoustic dampening behavior thanks to their foamed structure.
A leading Spanish automotive supplier has put its third twin-sheet thermoforming line into operation for the manufacture of ducts for automobile air conditioning. The UAR 155g machine was supplied by Illig of Germany.
Improvements to the injection unit include up to a 19% increase in speed, depending on tonnage; newly designed plasticizing components; and more accurate and energy-efficient injection carriage and injection movement with a lower friction co-efficient. The clamp unit features a platen designed for centralized force transmission to the mold; graphite/steel bushings that provide better lubrication and extend the life of the unit; and improved repeatability of mold opening and closing.
A further benefit provided by thermoforming with twin-sheet technology versus extrusion blow molding is that multiple parts of differing dimensions and geometries can be manufactured simultaneously by utilizing a large-area tool (the UAR 155g features a forming area of up to 1450 x 1200 mm). This capability also has implication in terms of cycle time per air duct, which is naturally shorter. On these accounts, air ducts made of foam are cost competitive when compared with rigid PP blow-molded ducts– manufacturing costs per duct are in fact comparable.
Connectivity Plus enables open connection to and easy integration with the automated processes, cells, and production lines of the customers’ integration partners.
Absolute Haitian also is introducing a fast-cycling version of the machine, the Mars III F. Suited for molding thin-wall parts, the Mars III F is available with injection speeds up to 500 mm/sec, achieving up to 19% in cycle time reductions.
In twin-sheet thermoforming of cross-linked polyethylene (XLPE) foam, two sheets heated up to processing temperature are formed into half shells in the mold, supported by vacuum, and at the same time they are welded together on the outer contour. With the system developed by Illig; the formed parts are punched directly in the mold after the end of the cooling time. The upper mold half is equipped with extendible serrated knives. The lower mold half is equipped with grooves in which the knives interlock during punching. The punched out parts are secured by “holding bridges” and removed from the forming station. Upon removal from the thermoforming machine, only the joint areas of the air ducts have to be cut – just like blow-molded rigid ducts.
Worcester, MA–based Absolute Haitian is the exclusive sales and service partner in the United States and Canada for Ningbo Haitian Machinery Co., Ltd., the world’s largest supplier of plastics injection molding machinery. It is headquartered in Ningbo, China.
Absolute Haitian is bringing the third generation of its best-selling Haitian Mars servo-hydraulic injection molding machines to North America in fall 2021. The line was first presented to plastics processors in the United States and Canada at a virtual event held by Absolute Haitian in June.
The third generation of Absolute Haitian's best-selling Mars servo-hydraulic injection molding machines, with significant end-to-end upgrades, will be available in the United States and Canada this fall.
In the thermoforming process, XLPE sheet (thickness 3 to 4 mm) is supplied by two material roll stands and each material is heated up in the forming station to a surface temperature of up to 200 C. Subsequently the heater is rapidly removed from the forming station– in less than 3 seconds – in order to minimize cooling of the material prior to commencement of the forming process. Further, the servo drives for the upper and lower mold table are especially designed for rapid movement speeds of up to 500 mm/s, even for tools with a weight of up to 1 t per mold table.
In this way the foam’s lower heat conductivity minimizes condensation of water in the air duct after switching off the air conditioning system. High elasticity and good resilience of the ducts reportedly provide further benefits, such as ease of assembly and reduction of squeaking and rattling sounds even within a compact installation space.
Lightweight and moreover flexible automotive air ducts are molded in sophisticated 3D geometries using XLPE foam and the thermoforming process on this Illig unit.
Since its introduction, the Mars line of injection molding machines has sold a record-setting 300,000 units. Absolute Haitian claims that the third-generation Haitian Mars III is more powerful and economical than its predecessors. Equipped with mechanical, hardware, and software upgrades, the Mars III series includes a new generation of servo-hydraulic drives that ensure precision and reliability in an energy-efficient package, according to the manufacturer. The machines are available in clamping forces from 67 to 3,709 US tons (600 to 33,000 kN).
GETTING A QUOTE WITH LK-MOULD IS FREE AND SIMPLE.
FIND MORE OF OUR SERVICES:
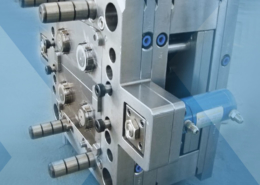
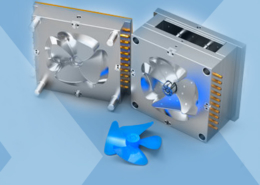
Plastic Molding

Rapid Prototyping
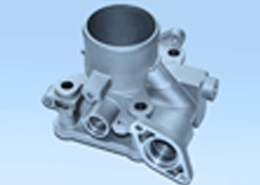
Pressure Die Casting
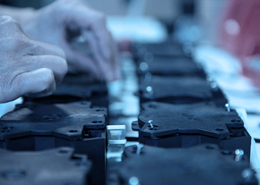
Parts Assembly
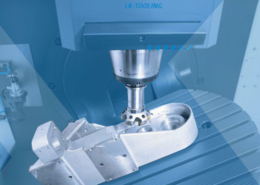