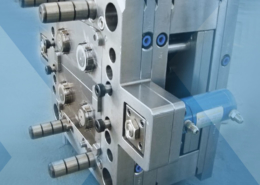
New HDPE a ‘Paradigm Shift’ for Blow-Molded Bottles and Containers, Says
Author:gly Date: 2024-09-30
In the area of micro molding, it is all about heritage. Since 1985, Accumold has been pioneering the art and science of micro molding, and is rightly today acknowledged as the world leader when it comes to the manufacture of extraordinarily small plastic parts that require extreme precision — typically measured in microns. The company is adept at the production of small-sized parts with micro features from 5 cm to less than 1 mm, and has specific expertise in insert molding, two-shot molding, and cleanroom molding using an array of materials including PEEK, LCP, and most engineering thermoplastics.
Geoff Giordano is a tech journalist with more than 30 years’ experience in all facets of publishing. He has reported extensively on the gamut of plastics manufacturing technologies and issues, including 3D printing materials and methods; injection, blow, micro and rotomolding; additives, colorants and nanomodifiers; blown and cast films; packaging; thermoforming; tooling; ancillary equipment; and the circular economy. Contact him at [email protected].
Runyan continues, “On stand 47, we will be showing a number of micro molded parts and components, and prominent among these are examples of our micro molded thin-walled cannulas. Our innovation in this area significantly improves the functionality and reliability of wearable diabetes devices by reducing overall costs and minimizing potential issues associated with traditional production methods. By eliminating the need for glued components, which can come loose and compromise the device's integrity, the new micro molding process ensures a more secure and durable assembly. This advancement leads to fewer failures in the field, enhancing the user experience and trust in the device's reliability.”
Nissei touts its NEX-V series and its “N-Constellation” IoT technology as turning the injection molding machine into a network hub that connects auxiliary equipment and collects real-time operation data.
Paul Runyan, VP of Sales & Marketing at Accumold says, “At Accumold, we believe that cost-effective, timely, and innovative products can be manufactured when we work with customers in a truly collaborative manner, and we insist upon transparency at every stage of product development. We have a solutions-oriented focus that when coupled with our unparalleled expertise ensures that we can manufacture end-use medical devices and components others may say are impossible. We are proud to be working at the cutting-edge of medical innovation, and invite all visitors at the Medical Technology Ireland Expo to come and see us, look at the parts that we have made, and we will discuss your specific applications and how Accumold can help realise your product development goals.”
Central to the event, Accumold will be showcasing examples of its micro molded thin-walled cannulas which will be displayed on the booth. It will also be demonstrating its commitment to the Irish medical device sector through its collaboration with Avem (stands 53A, 53B, and 53C) which will be representing Accumold’s micro molding capabilities and micro solutions to the medical technology, microelectronics, wearable, and micro-optics sectors in Ireland and United Kingdom markets.
“This system represents a significant leap forward in injection molding technology,” said Plasdan CEO Paulo Silva. “It delivers efficiency gains and productivity improvements, crucial for manufacturers aiming to optimize their operations and minimize environmental impact. The single-machine approach not only cuts operational costs but also supports the industry's move toward more sustainable practices.”
Accumold announced it collaboration with Avem back in June 2024, and the Medical Technology Ireland Expo marks the first event that the companies will be at together. The Avem team is well established in the medical OEM sector based in Galway, Ireland and has the skillset and experience in representing Accumold micro molding solutions with existing and newer customers who are working on new projects where micro in size, micro tolerances, or micro features (or all three) are needed in their next generation product designs.
See Plasdan’s equipment at Nissei America’s booth, W2401, at NPE2024 at Orlando’s Orange County Convention Center from May 6 to 10.
A three-material molding system from Plasdan will demonstrate the production of complex assemblies with two add-on injection units and in-mold robotics at NPE2024.
The plastic injection molding system from Plasdan with an integrated Nissei press reduces cycle times and labor and energy requirements.
Plasdan’s end-to-end automated cycle moves products quickly through the cycle, eliminating the cost of unfinished work-in-process inventory. The company’s multi-injection molding solutions ultimately save operating costs and reduce environmental impact.
Accumold brings nearly 40-years’ experience enabling innovation through micro molding to the Medical Technology Ireland Expo, 25-26 September 2024 in Galway, and will be showcasing examples of the impossibly small and intricate parts that it has developed for medical device OEMs on stand 47.
Plasdan’s equipment will be integrated with a Nissei NEX360V-100LE all-electric molding machine to function in a single cycle — without the need for multiple machines or manual assembly. The setup reduces machine time, labor and energy requirements, and uses less floor space.
During live demos at Nissei America’s booth at NPE2024, Plasdan will discuss with attendees how they can integrate the company’s solutions into existing manufacturing setups. The demo will feature two add-on Ergoline injection units, which Plasdan designed in a slim footprint to overcome assembly constraints. These units can be mounted angular on tool, vertical on a fixed platen, or horizontal on the non-operator side.
Accumold’s representatives look forward to meeting Medical Technology Ireland show visitors, and discussing the specifics of the medical applications that they have under development.
Accumold's ability to produce high volumes, in the tens of millions, with consistent quality means that manufacturers can rely on a steady supply of uniform thin-walled cannulas. This consistency is crucial for the final device's performance, as it ensures that each unit operates as intended, reducing variability and increasing the overall reliability of wearable diabetes devices.
Runyan comments, “Avem’s technical sales experience and knowledge in a variety of medical applications, materials and manufacturing processes effectively connects the right solutions with R&D and commercial teams that are miniaturizing their devices. Accumold is very excited about our relationship with such a talented team.”
GETTING A QUOTE WITH LK-MOULD IS FREE AND SIMPLE.
FIND MORE OF OUR SERVICES:
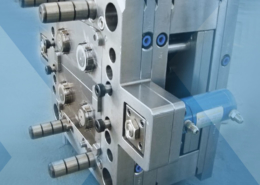
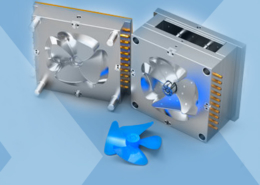
Plastic Molding

Rapid Prototyping
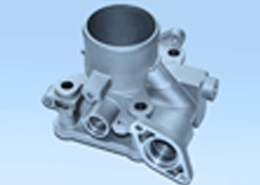
Pressure Die Casting
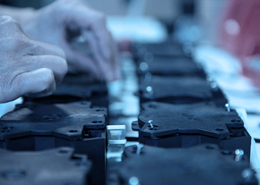
Parts Assembly
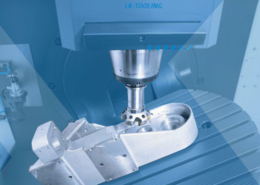