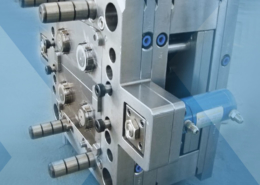
Neste Announces Agreement to Produce Bottles Using Renewable & Recycled
Author:gly Date: 2024-09-30
“For decades, glass has often been the second choice when it comes to materials in manufacturing processes because its formation is too complicated, energy-intensive and unsuitable for producing high-resolution structures,” explains Rapp. “Polymers, on the other hand, have allowed all of this, but their physical, optical, chemical and thermal properties are inferior to glass. As a result, we have combined polymer and glass processing to quickly and cost-effectively replace both mass-produced products and complex polymer components with glass.”
Sabic has announced projects in Asia and the Netherlands designed to increase global capacity for two of its high-performance engineering thermoplastic materials, Ultem polyetherimide (PEI) and Noryl polyphenylene ether (PPE) resins. To increase capacity for Ultem resins, Sabic plans to expand its existing footprint in Singapore where it currently has compounding operations. The planned new production facility in Singapore is expected to go online in the first half of 2021. The company also plans to recommission operations at its Bergen op Zoom PPE resin plant in the Netherlands by the end of 2019 to produce (PPE, the base resin for its line of Noryl resins and oligomers.
Further details of the study can be found in the paper titled ’High-throughput injection molding of transparent fused silica glass’. It is co-authored by Bastian Rapp, Frederik Kotz, Markus Mader et al.
Dr. Frederik Kotz, group leader at the Laboratory of Process Technology and Chief Scientific Officer at Glassomer, states, “We see great potential, especially for small high-tech glass components with complicated geometries. In addition to transparency, the very low coefficient of expansion of the glass also makes the technology interesting. Sensors and optics work reliably at any temperature if the key components are made of glass.”
Subscribe to the 3D Printing Industry newsletter for the latest news in additive manufacturing. You can also stay connected by following us on Twitter and liking us on Facebook.Looking for a career in additive manufacturing? Visit 3D Printing Jobs for a selection of roles in the industry.Featured image shows glass gears injection molded using the new Glassomer material. Photo via Glassomer.
The combination of 3D printing and glass tends to be an eyebrow-raising topic, but there are a number of research institutions looking to advance the field. Scientists from the King Abdullah University of Science and Technology (KAUST) recently developed a new method of 3D printing photonic crystal fibers – a special type of optical fiber. The team constructed a purpose-built SLA-based 3D printer for the project, one that enabled the scientists to customize their optical fibers with previously impossible internal geometries.
Kubi Sertoglu holds a degree in Mechanical Engineering, combining an affinity for writing with a technical background to deliver the latest news and reviews in additive manufacturing.
When used in conjunction with 3D printed molds, the composite material enables the high-throughput production of complex glass components with previously impossible geometries. The team, led by Prof. Dr. Bastian Rapp from the university’s Laboratory of Process Technology, expects potential applications in everything from optical devices to solar technology and lab-on-a-chip medical devices.
The decision to recommission the Bergen op Zoom Noryl resins facility provides customers with a second source of PPE resins globally, and affirms Sabic’s commitment to the European market and global customers who specify their material solution needs from Europe. When operational, the Bergen op Zoom facility is expected to add more than 40% global capacity over a 2017 baseline.
Kotz adds, “We have also been able to show that micro-optical glass coatings can increase the efficiency of solar cells. This technology can now be used to produce cost-effective high-tech coatings with high thermal stability. There are a number of commercial opportunities for it.”
When injected into a 3D printed mold, the material is initially a milky-white color, but can be converted into pure quartz glass via a heat treatment process. This can be done using far less energy than conventional glass melting, and the formed glass parts have a high surface quality so the need for further polishing is eliminated altogether.
The newly developed material is a special composite granulate designed in-house by the researchers, and it is moldable at a low temperature of just 130°C. There is also a liquid resin version of the material that is compatible with SLA-based 3D printing.
To make the current work possible, the research team had to solve existing problems relating to material porosity and particle abrasion. In a bid to make the technology more environmentally-friendly, Rapp’s team also used water as a base material.
In the meantime, Sabic expects incremental manufacturing process improvements at the Selkirk, New York, and Mt. Vernon plants to provide increases in Noryl PPE resin and Ultem PEI resin production by the end of 2018. The resulting supply gains will be used to meet growing demand and improve lead times for customers.
“Increased customer demand, especially in Asia, prompted the further capacity expansion plans,”, said Ernesto Occhiello, Executive Vice President, Specialties, Sabic. “While interim capacity gains for both Ultem and Noryl resins have been achieved, global demand for both product lines has increased significantly, and Sabic is planning to expand its capacity to support our customers’ growth aspirations. We will continue to focus efforts to deliver the right capacity, in the right global locations, at the right time to support our customers’ needs.”
Injection molding, on the other hand, is the leading technology in the polymer industry. It is both rapid and cost-effective, making it well suited to series production with a wide variety of part types. According to the Freiburg team, transparent glass has not been compatible with high-speed injection molding technology until now.
Elsewhere, at Lawrence Livermore National Laboratory (LLNL), researchers have previously used multi-material 3D printing, namely direct ink writing (DIW), to fabricate highly customized gradient refractive index (GRIN) glass optics. The technique allows for a number of optical functions to be programmed directly into flat glass components – functions that would otherwise require curved lenses.
Stephen has been with PlasticsToday and its preceding publications Modern Plastics and Injection Molding since 1992, throughout this time based in the Asia Pacific region, including stints in Japan, Australia, and his current location Singapore. His current beat focuses on automotive. Stephen is an avid folding bicycle rider, often taking his bike on overseas business trips, and is a proud dachshund owner.
Expansion of footprint in Singapore will localize Ultem resin production in Asia, increasing global production by 50%; recommissioning of Noryl resin manufacturing operations in Bergen op Zoom expected to increase global production more than 40%.
A team of researchers from the University of Freiburg, together with materials startup Glassomer, have developed a new polymer-based silica glass material compatible with injection molding technology.
Ultem resins are currently produced in two locations, Mt. Vernon, Indiana, and Cartagena, Spain. The planned operations in Singapore will localize supply for customers in Asia, reducing lead times, especially for shorter qualification cycle applications. When fully operational, the Singapore facility is expected to increase capacity by 50% over a 2018 baseline. “With the addition of Singapore, Sabic will be the only petrochemical company with the ability to produce the high heat resin in Asia, the Americas and Europe, a significant advantage for the company’s customers,” Occhiello noted.
For millennia, glass has been the go-to material for aesthetic, see-through parts. Today, the material is used in everything from bottles and windows to high-tech telecommunication devices. The shaping of glass components is predominantly based on processes such as melting, grinding, etching, and kiln casting – all of which are slow, energy-intensive, and severely limited in terms of geometric freedom.
GETTING A QUOTE WITH LK-MOULD IS FREE AND SIMPLE.
FIND MORE OF OUR SERVICES:
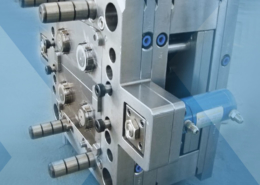
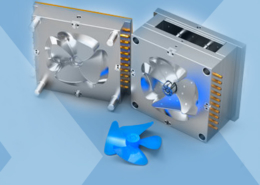
Plastic Molding

Rapid Prototyping
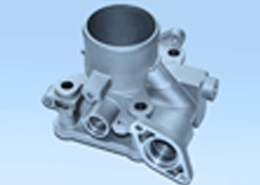
Pressure Die Casting
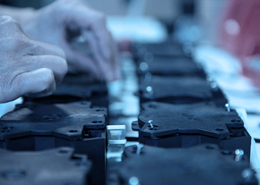
Parts Assembly
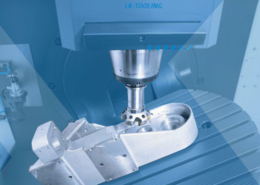