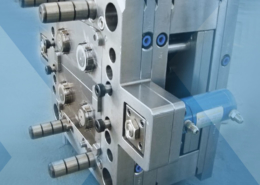
Nepal suspends sale of injection made by Indian company citing ‘serious
Author:gly Date: 2024-09-30
US PP contracts are typically formula-based and are set at polymer grade propylene (PGP) values plus an adder.
The price-conscious nature of the population and high mileage demand are further compelling auto manufacturers to use plastic parts in vehicles, which will significantly drive the demand for plastic injection molding machines within the region.
Some PP applications such as food packaging saw steady demand in the initial weeks after the lockdown measures were put in place. Demand for non-woven and fibre grades increased as demand for surgical masks and gowns rose significantly.
Export activity picked up from April as slower domestic demand caused suppliers to direct more material into the export channel.
US PP demand showed a promising start to 2020 after a experiencing a down year in 2019. Initial hopes for higher consumption levels were undone by the end of the first quarter as the coronavirus spread to the US, inspiring widespread lockdown measures beginning from mid-March.
Additionally, the segment is anticipated to showcase promising growth during the forecast timeline. The growth trend of plastic IMMs is underpinned by the packaging and automotive industries coupled with bolstering demand from the manufacturing sector, which is expected to further drive the injection molding machine market size.
Adders declined over the course of 2019 as supply expanded while overall consumption levels fell.
Export activity is expected to remain elevated into the second half of 2020 as domestic consumption is expected to remain low throughout the rest of the year while additional capacity is expected to come online.
The injection molding machine market report includes in-depth coverage of the industry with estimates & forecast in terms of volume in Units and revenue in USD Million from 2017 to 2027 for the following segments:
Work is underway to develop the use of metallocene catalysts in PP production to improve resin properties. Borealis’ Borstar bimodal polyethylene (PE) process developed in the mid-1990s has also been adapted for the production of PP.
The largest outlet is injection moulding applications, which include packaging, parts for electronic and electrical appliances, caps and closures, toys, luggage and a variety of household goods. The second largest outlet is in fibres, where carpet face yarn for carpet backing has been a growth market for PP.
According to the ICIS Supply and Demand Database, average utilisation rates are expected to decline over the next two years to around 81% by 2021 before rising in 2022.
An injection molding machine is used to produce parts by injecting molten materials into a mold. Injection molding is a suitable method to mass manufacture complex shapes and plays an important role in the plastic processing industry.
Supply length is expected to remain in place in the US PP market until demand begins to recover from the coronavirus crisis.
One of the major advantages of horizontal machines over vertical machines is that they can attain automatic production to save both labor & time and improves production efficiency along the way. It is estimated that horizontal injection molding machines will become conventional, and many manufacturers will prefer them over vertical machines.
According to data from the ICIS Supply and Demand Database, US PP consumption declined 1.7% in 2019 compared with 2018. Consumption is expected to decline by another 1% in 2020 before rebounding in 2021.
Home > Industrial Machinery > Industrial Equipment > Tools > Injection Molding Machine Market
Based on data from the ICIS Supply and Demand Database, US PP consumption is expected to rise above 2018 levels by 2021 after declining in both 2019 and 2020.
Proliferating machine demand from the packaging, medical, and electronics sectors along with the rising need for replacements in the automotive industry will drive the injection molding machine market share in the coming years. The packaging industry has been witnessing tremendous growth in recent years, especially in Asia Pacific. The sector has been ordering an increasing number of machines, especially for low and medium-injection speed applications.
In 2020, Europe accounted for 50% of the company’s revenue in small & medium-sized machines. Moreover, manufacturers are introducing new generations of injection molding machines to coup up more market share from different industry verticals. For instance, Sumitomo (SHI) Demag expanded its portfolio by including modern multi-component machinery designed to suit specific applications of each industry.
The automotive end-use sector contributed significant revenue to the injection molding market and acquired over a 10% portion of the industry share. Injection molding machines offer a feasible solution for producing large and high-quality auto parts in abundance. The automotive sector where quality, consistency, and safety are of the utmost importance considers injection molding machines a preferred choice. This machine is highly adopted in the industry owing to its ability to produce identical parts in mass quantity with relatively low operating costs. Many metal auto parts have been transitioned into plastics and are significantly driving the requirement for injection molding machines to achieve production targets.
Looking for more? Our expert team of researchers can create market analysis reports for any of your needs.
Current bulk technologies such as the Spheripol process developed in 1982 by Himont (later Basell, now LyondellBasell) replaced the solvent in an older process with liquid propylene.
Rising production within the US and Canada over the coming years may lead to greater export activity out of the US in the coming years.
Injection molding machine industry manufacturers are adopting strategic initiatives, such as product launches, production capacity expansion, mergers, and acquisitions, to siphon more market share and increase their business profitability. For instance, Sumitomo (SHI) Demag is focused on the production of all-electric machines tailored to the needs of the end-use industry. Additionally, the company is expanding its production capacity in Germany to manufacture an increasing number of electric injection molding machines.
Data from the American Chemistry Council (ACC) and Vault Consulting showed US PP inventories declining in January and February before picking back up in March and April. PP inventories reached multi-year highs in the summer of 2019 and remain below those figures through April.
The long-term growth prospects for PP remain positive as the polymer is very versatile and able to substitute for other plastics in a number of applications.
Changing regional demographics, such as shrinking houses, in conjunction with the adoption of a fast-paced life by millennials are significantly influencing the packaging trend in the region and stimulating the demand for lighter, portable, small & on-the-go consumption pack types. Moreover, in 2020, the market witnessed a more than 50% increase in demand for injection molding machines from the medical sector. This can be attributed to the sudden rise in the requirement for medical equipment due to the ongoing coronavirus pandemic.
Injection Molding Machine Market size was valued at USD 4.4 billion in 2020 and is estimated to exhibit a CAGR of over 4.8% from 2021 to 2027. Packaging and medical technology sectors to proliferate the demand will fuel the business growth during the forecast period.
Materials that are mainly used include metals (which is also referred to as die-casting), glasses, elastomers & confections and the most commonly used are thermoplastic and thermosetting polymers. An injection molding machine is capable of fabricating the sizes of different products from the smallest part to the entire body of the car. Additionally, injection molding is the most common modern method of manufacturing plastic parts.
Catalyst activity from the older process was also improved, allowing for the introduction of gas phase technology.
Global Market Insights Inc. 4 North Main Street, Selbyville, Delaware 19975 USA Toll Free: +1-888-689-0688 USA: +1-302-846-7766 Europe: +44-742-759-8484 APAC: +65-3129-7718 Email: sales@gminsights.com
In 2020, electrical segment generated around USD 1.5 billion in injection molding machine market and is expected to observe substantial demand in the coming years. The increasing demand from the packaging, electronics, and medical sectors is backing up the market growth. Compared to hydraulics, all-electric IMMs are controlled with servo motors that allow a repeatable, faster, energy-efficient, and more precise operation.
The plastic injection molding machine accounted for over 70% market share in 2020 as these are used to manufacture plastic parts for multiple industries. In recent times, plastic injection molding machines are essential to every manufacturing sector including automotive, electronics, housewares, and home appliances, among others. Plastic provides durable, high-quality production runs, affordable, and corrosion-resistant products; hence, has emerged as one of the most crucial materials in modern manufacturing.
PP has been successfully competing against polystyrene (PS) in a number of applications over the past several months. PP has been competitively priced relative to polystyrene (PS) rand PS has also experienced some negative publicity recently over concerns that the polymer is not very recyclable. ■
Polypropylene (PP) is used in a wide range of consumer and industrial products. Three forms of PP can be produced: isotactic, syndiotactic and atactic. Isotatic PP is the main form manufactured.
PP supply lengthened during 2019 as several producers completed debottlenecking projects. Further capacity growth is anticipated in 2020 as Braskem is planning to start up a new 450,000 tonne/year PP plant in La Porte, Texas in the summer.
PP prices declined to the lowest levels seen in a decade in the early months of 2020 as the coronavirus crisis caused a significant drop-off in demand while also pulling upstream costs lower.
Horizontal injection molding machines held over 80% share in 2020. Horizontally-oriented machines are easy to maintain, offer simple operation, and are more easily favored by the public. This type of machine is generally chosen to manufacture pure plastic products, in addition to parts with larger surface areas. Horizontal machines are suitable to manufacture cylindrical products, such as silicone baby nipples, silicone baby bottles, and LSR breast pumps, among others.
On the other hand, the COVID-19 health crisis has catalyzed the product demand from the medical sector. Nevertheless, the world has now entered a phase of recovery and is likely to create a positive outlook for the injection molding machine market growth.
Asia Pacific is the leading revenue-generating region and will witness around 5% CAGR in the injection molding machine market by 2027. The robust product demand can be attributed to the growing end-use industries. The automotive industry is one of the verticals substantially contributing to this growth. The region has the least number of cars per thousand people. Therefore, the demand for cars is improving in Asia Pacific with the improving economic condition. Since many Asian countries have low car penetration, the automotive industry is yet to grasp the full potential of the market in the region.
The digital control of electric injection molding machines allows them to be operated virtually unattended, boosting profits by lowering labor costs. Due to their high precision, these types of machinery are suitable for manufacturing small to medium products and medical parts such as syringes and Petri dishes.
Furthermore, manufacturers are focused on the development and production of all-electric injection molding machines. Key industry players are taking several efficiency measures to improve their production capabilities for this forward-looking technology. Companies are benefitting from the shifting preference to all-electric machinery. For instance, Sumitomo (SHI) Demag Plastics Machinery GmbH, a major market player, has been witnessing substantial demand from this machinery segment.
PP demand is likely to experience the sharpest decline during the second quarter before economic activity begins returning to more normal levels in third and fourth quarters as the lockdowns in different US states are graudally lifted in phases.
However, emerging technologies, such as 3D printing, may pose a threat to market development in the coming years. Besides, the COVID-19 outbreak has been a major barrier to market growth. The disrupted industry value chain, raw material shortage, and plummeted demand have negatively influenced the nosiness profitability and restricted market expansion. The demand for injection molding machines observed a severe downfall from the automotive and construction industries.
GETTING A QUOTE WITH LK-MOULD IS FREE AND SIMPLE.
FIND MORE OF OUR SERVICES:
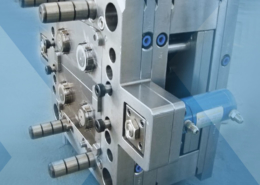
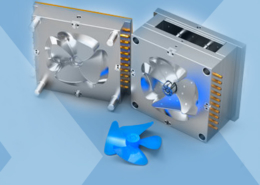
Plastic Molding

Rapid Prototyping
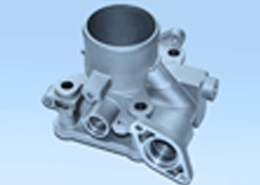
Pressure Die Casting
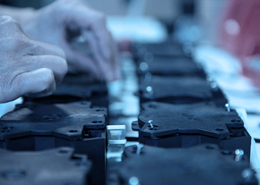
Parts Assembly
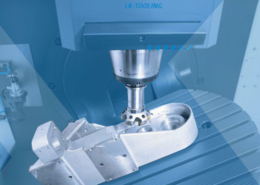