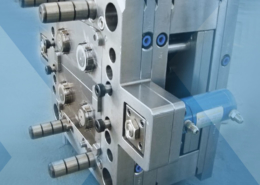
Natech Plastics Installs New Robot-Assisted Presses to Meet Medical OEM
Author:gly Date: 2024-09-30
Let’s take a closer look here at the machines and what we can create with them. The machines, which include an extruder, injection molding machine, compressor and shredder, are “made from basic materials, affordable, and easy to build.” Build all four, and you can have a veritable factory. After grinding plastic objects up into chips with something that emulates a high-power blender, you can blend different materials to create new textures, blend colors together and create weird patterns, or make a small production out of a solid mold. Most importantly for us, the extrusion machine can also make raw materials (think filament!) that you can use and share with others.
If you are as excited as I am about a set of machines that shred, compress, inject, and extrude recycled plastic, you can help spread the word by making a machine yourself, sharing your experience, and telling your maker friends about Precious Plastic’s grand vision to merge plastic recycling with 3D printing in inexpensive, easy-to-build machines. Here’s a video of the machines at work that you can also share. Discuss in the Precious Plastic 3D Printing & Recycling forum over at 3DPB.com.
One of our greatest ecological challenges, in my estimate, is tackling the problem of plastic waste. The Earth simply can not sustain the levels of pollution generated by a material that can take anywhere from 80 (plastic cup) to one million (plastic jug) years to decompose. The stats are so grim for plastic waste that whenever I refresh on my numbers, I fall into a deep depression as I try to imagine the world just 50 or 100 years from now. According to the Institute for Sustainable Communication, plastic garbage in the ocean alone kills one million sea creatures a year; Americans use 2.5 million plastic bottles every hour; and Americans only recycle 1-2% of the 10.5 million tons of plastic waste generated annually.
Precious Plastic’s plan, as outlined on its website, is to make it easy for people to establish their own plastic recycling workshops. Developing the recycling machines, sharing the open source machine blueprints online, spreading this information, creating new products — including 3D printer filament — using the recycled plastic, holding clean-ups, and building recycling communities are all part of the company’s grand vision to tackle some of this overwhelming plastic pollution problem.
The global 3D printing market continued its upward trajectory in the second quarter of 2024, totaling $3.45 billion—a year-over-year increase of 8.4%. Despite a slight sequential decline from $3.47 billion...
A recent Reddit thread on the subject seems to be in agreement that the Precious Plastic machines are a great contribution to 3D printing. One user expressed concern that the filament size made by the extrusion machine looks bigger than 2.85 mm, to which the original poster, “engineerd3d,” responded: “It may be bigger. But they are open-sourcing the plans and they work hard to show people how to reuse plastics as well as being generally caring people.” Another user added to the issue of filament size: “You can choose your nozzle size very easily. Only thing you need is a drill bit that’s the same diameter as the filament you want to produce.”
Portugal has a storied moldmaking tradition that dates back to the beginning of the 20th century, when companies in the town of Marinha Grande, about 95 miles north of Lisbon, started manufacturing molds for glassware rather than importing them. After World War II, plastic injection molds gained a foothold and, with the inevitable ups and downs, that has continued ever since. Automotive OEMs have been reliable customers; medical device manufacturers, not so much. Muroplás, located in Muro-Trofa, about 130 miles north of Marinha Grande, is the exception that proves the rule.
Stay up-to-date on all the latest news from the 3D printing industry and receive information and offers from third party vendors.
Founded in 1989, Muroplás initially produced precision parts for the automotive industry. Shortly after setting up shop, however, "domestic companies that needed components for infusion systems challenged us to produce parts," says Dinis Baptista, International Sales/Information Systems. The company never looked back, and has been a national pioneer in plastic injection molding for medical device OEMs since the 1990s. Medical technology applications now represent 90% of the company's business, and it has cemented its reputation by investing in R&D and new technologies, and embracing change.
Stay up-to-date on all the latest news from the 3D printing industry and receive information and offers from third party vendors.
Muroplás is always attuned to the needs of its customers and continues to invest in the necessary resources to produce complex molds and optimize production, says Baptista, and that is the simple secret of its ongoing success. "R&D is an obsession at Muroplás," says Baptista. "We exist for our customers, and we are proud to have forged a relationship based on quality."
In 3D Printing News Briefs today, four graduate students received $10,000 scholarships from ASTM International, and 3DPRINTUK announced the first commercial launch of the Stratasys SAF printer in the UK....
The good news here — information that keeps me from falling into that seemingly-inevitable deep depression — is that more opportunities for recycling are on the horizon. Precious Plastic wants to spread the word about their plastic recycling machines that can also inject and extrude so you can make filament from recycled plastic and 3D print new creations. Now we’re talking!
Another commenter wondered how the machine would work with filament made from HDPE — one of the most common household plastics — to which engineerd3d responded by linking to RepRap’s HDPE page and stating that settings would likely have to be tweaked to use HDPE filament, but that it is possible.
Carbon and Keystone Industries just hit a milestone with the successful production of one million dental parts, highlighting the steady progress in 3D printing for dental manufacturing. In just 314,000...
Adidas has teased a new 3D-printed shoe, sending it to shoe photographer Tyler Mansour, also known as Arab Lincoln, who showcased it on his Instagram. Tyler introduced the shoes by...
Unlike many molding companies in Portugal, which historically have tended to specialize in specific activities—tooling design, polishing, the fabrication of precision molds, and so forth—Muroplás chose to invest in its own machining department and build molds as well as provide injection molding services.
The company operates Class 7 cleanrooms on site for the production of infusion, transfusion, and hemodialysis kits. It runs Krauss Maffei and Negri Bossi molding systems in its 4500-sq-m production space. Muroplás also has developed an IT system to help maximize the production of precision parts for medical applications. One investment that has contributed to its success is the purchase early on of PowerMILL CAM software from Delcam plc (Birmingham, UK), which it has used to develop its own range of medical devices. Muroplás carries on a tradition, in fact: Back in 1983, a Portuguese company was the first European moldmaker to install CAD/CAM technology, according to industry association Cefamol.
Register to view and download proprietary industry data from AM Research and 3DPrint.com Questions? Contact info@3dprint.com
Contrary to common belief, the major reason suppliers of injection molding services incorporate moldmaking and mold repair into their portfolio typically is not a matter of economics but delivery time, according to Delcam. Time and reputation is lost when a company has to wait for a mold to be repaired or parts shipment is delayed because molds have not been delivered within the planned timeframe. Being able to implement small changes or improvements to the mold on site also improves customer service, and intellectual property ceases to be an issue when molds are built in house, says the company.
Ingenious, right? You have the complete cycle here, from the recycling of plastic materials to the creation of new objects. I am personally convinced that there’s not a person out there who owns or is considering buying a 3D printer who wouldn’t consider this excellent alternative option for the production of their own filament.
Editor in chief of PlasticsToday since 2015, Norbert Sparrow has more than 30 years of editorial experience in business-to-business media. He studied journalism at the Centre Universitaire d'Etudes du Journalisme in Strasbourg, France, where he earned a master's degree.
Portugal has a storied moldmaking tradition that dates back to the beginning of the 20th century, when companies in the town of Marinha Grande, about 95 miles north of Lisbon, started manufacturing molds for glassware rather than importing them. After World War II, plastic injection molds gained a foothold and, with the inevitable ups and downs, that has continued ever since. Automotive OEMs have been reliable customers; medical device manufacturers, not so much. Muroplás, located in Muro-Trofa, about 130 miles north of Marinha Grande, is the exception that proves the rule.
"We believe that combining the conception and manufacture of molds with injection molding of precision plastic parts offers our customers unique benefits," Dinis Baptista, International Sales/Information Systems, told PlasticsToday. "The use of high-speed machining technology and a dedication to improving the form, function, and manufacturability of molds has allowed us to provide medical device manufacturers with the best of both worlds: accuracy and precision at less cost," adds Baptista.
GETTING A QUOTE WITH LK-MOULD IS FREE AND SIMPLE.
FIND MORE OF OUR SERVICES:
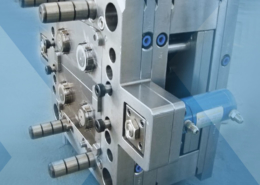
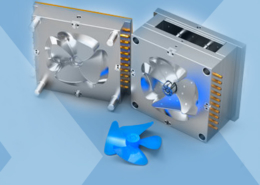
Plastic Molding

Rapid Prototyping
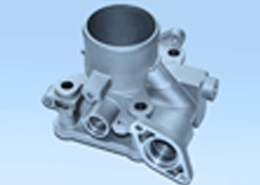
Pressure Die Casting
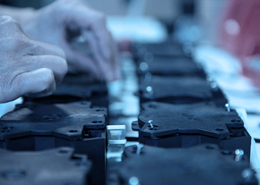
Parts Assembly
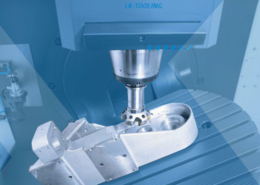