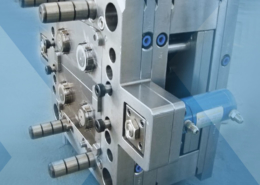
Myers Industries Bolsters Rotomolding Portfolio with Trilogy Plastics Buy - plas
Author:gly Date: 2024-09-30
TPE’s, a very wide class of Thermo PLastic Elastomers can be blow molded or injection molded. (in my experience vinyl and pvc used for blow molding is rigid and not the same low durometer “squeakable” stuff used in rotocasting). In blowmolding there is obviously no core but you have wall thickness limitations. When injection molding there is a core or mandrel suspended in the mold cavity. For minor undercuts you can use the ejection stroke to remove the mandrel if you design the tool right but in most cases of hollow parts its a manual process where the part and mandrel are removed after each shot, mounted on a fixture and either leveraged off with brute force or if there are no other openings in the part you can run an airline through the mandrel and blow compressed air through to launch the parts off like a rocket.
For anything I’ve seen rotomolded I always felt like it was larger parts, poor exterior surface quality, and usually the higher cycle time makes it not great for super cheap stuff.
Schnipke has tooling and plastic injection molding operations at its headquarters in Ottoville, OH, and operates a second manufacturing facility in Tucson, AZ. The company is FDA registered and is certified to ISO 13485:2016.
On my last trip to China i saw a pneumatic machine that i designed to help bring some automation and robot assistance to this process on the production line of every rubber supplier i visited, i only ever sent the plans to one supplier.
Plastics injection molder Atalys LLC announced yesterday that it has acquired Schnipke Engraving Co. LLC. Both companies provide injection molding and related services to medical device OEMs. Atalys, based in Rochester, NY, said the acquisition will enhance its manufacturing capabilities, technology, and geographical footprint.
If you are thinking of importing PVC products, be aware that they can contain material that is prohibited for sale in California or prohibited for sale without labeling. The law is called Prop 65. The list of materials is available here: https://oehha.ca.gov/proposition-65/proposition-65-list As a designer, you can’t really validate this in your garage, but inspection services can. Some services are Bureau Veritas, SGS, MTS or contact a testing laboratory. Even in Canada, most labs have a prop 65 testing protocol.
Is it blow molding or roto molding?I always assumed roto and then they IP the squeaker and either insert mold it or assemble it post.
Looking at this for a client and I’ve searched the internet. Any kid or pet toy that has a hollow center made out of soft durometer material. I figure it’s some sort of a blow molding process. Some toys have open ends on them but I wouldnt think you could pull a core out of it without ripping the material. Help anyone?
Editor in chief of PlasticsToday since 2015, Norbert Sparrow has more than 30 years of editorial experience in business-to-business media. He studied journalism at the Centre Universitaire d'Etudes du Journalisme in Strasbourg, France, where he earned a master's degree.
@ralphzoontjens could you please re-post the link to the video of how squeakers are made? The link you posted previously no longer works. If anyone reading this can help with the link or has a similar video they can share it would be greatly appreciated!
Vinyl/PVC toys like bath toys and the cheapest dog toys are usually rotocast in a bank of molds that get filled with liquid, pelletized or powdered raw materials. This goes in to a furnace, spins real fast and then comes out to cool off, the toys are ripped out of small opening in the mold which creates a sloppy area on the part and its usually trimmed and filled in with a molded plug that would house the squeaker. This can also be done in a slush casting process using a vinyl plastisol. In some cases you might rotocast liquid RTV materials. Most of these materials are not highly durable.
Thermosets or vulcanates like natural rubber can be compression molded, injection molded, or compression/injection molded. Same process as above but natural rubber has a higher stress/strain than most TPE so you can pull enormous mandrels out of tiny holes. And when it comes to elastomeric materials natural rubber is incredibly durable
Haven’t done any squeeky toys myself, but for the dog toys I’m thinking of, I would have assumed blow molding since usually there is a good smooth finish and an obvious clamp mark for a gas injection point, plus the smaller size and surface finish.
I’ve always used roto casting too, with spray ops for any deco. Like Ray mentions, you really need to watch out for some of those materials, especially including Phthalates, which are commonly used to soften material used in roto casting.
Blow molding is a good technique for molding these toys but mostly if the product has to have a relatively strong and lightweight outer shell. It also has a cycle time at least 10x faster than rotational molding. But the advantages of rotomolding are that it works for more types of polymers including soft PUs, tooling costs are much lower, and it is easy to experiment with production parameters. That is the reason why these toys are often rotationally molded.
"Our acquisition of Schnipke was driven by a focused strategy to deepen our capabilities, capacity, and technical superiority across the entire manufacturing process for medical device components,” said Vinc Ellerbrock, president and CEO of Atalys. “The addition of Schnipke adds two manufacturing sites for scalable growth, broadens our geographic presence and reach, enables us to serve a wider array of customers, and significantly augments our technical capabilities,” said Ellerbrock.
I recommend vinyl because it looks great and can be downcycled into flooring. You can look into extrusion blow molding TPE or EVA but it will likely require some R&D before the factory gets it right.
Earlier this week, another medical injection molder made news when Total Molding Services announced that it has been acquired by Haartz Family Holdings, changing its name to Moldgenix in the process.
Founded in 1967, Schnipke has established a reputation for building tools in-house and designing and engineering molds that meet the medical device industry's stringent requirements for precision at extremely tight tolerances, said the news release. The company claims on its website that it can mold within tolerances of +/-0.001 inches and as small as 0.02 grams in weight. Even smaller dimensions can be accommodated upon customer request.
You answered your own question, it’s blow molding. Soft elastomer materials are pretty easy to yank tools out of, especially if the material is still warm. Theres also collapsing cores and other options.
In February, Atalys announced that it is tripling the size of its existing facility in the Dominican Republic from 15,000 to 47,000 square feet through the addition of a new 32,000-square-foot building. The company said that the new building will be dedicated to manual assembly with complementary injection molding, pad printing, tool repair, and warehousing. The existing facility will become the company's primary plastics processing site focused on cleanroom injection molding as well as secondary operations such as testing and packaging.
But I admit I could be wrong and just basing those assumption on samples I saw long ago. Never touched either process in my line of work.
on my first trip to China i saw a part from my company that was 8" in diameter with a .4" wall thickness that was molded over a steel core that was pulled out of a 1.5" opening in the part. The part had nearly a 10 minute cycle time, two cavity mold, when the parts came out 1 worker would pick up the core and part, and hang it from a fixture while two dudes with bulging biceps used tire spoons to wrestle that part off the mandrel. At this point there have been millions sold.
Thanks guys. I wish there was a video of this process. Normally I can just youtube any manufacturing question and see it on youtube or on old clips of “how things are made”. I’m curious if they use a rotomolded process, they must do multiples of them and I envision they put these molds or mold (with multiple cavities) on a rotating 2-3 axis mechanism.
In addition to its headquarters in Rochester, Atalys has manufacturing facilities in Asheboro, NC, and the Dominican Republic. The New York and North Carolina plants have multiple Class 8 cleanrooms for molding and assembly on site; the Santo Domingo site in the Dominican Republic offers cleanroom assembly and automation. The company said it adheres to scientific molding principles and is equipped with presses ranging in size from “near micro molding” to 1,400 tons.
Latex is slush cast or slipcast just like ceramic in plaster molds. slightly more durable than vinyl depending on how you measure but with a much shorter lifespan.
As an aside to the manufacturing of the outer, if you’re looking for it to make any noise you can have some fun playing with different bellow sizes and different reeds for a great range of sounds! And they don’t all need to be reeds, they can be compression and even things that you bend that make unusual sounds! Great fun to play around with, really makes you feel like a kid!
GETTING A QUOTE WITH LK-MOULD IS FREE AND SIMPLE.
FIND MORE OF OUR SERVICES:
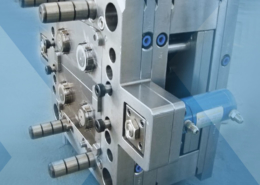
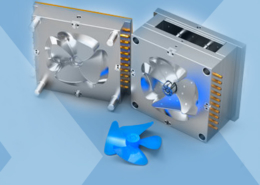
Plastic Molding

Rapid Prototyping
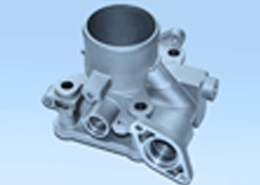
Pressure Die Casting
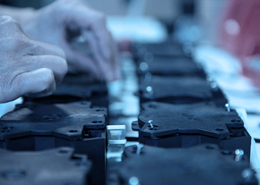
Parts Assembly
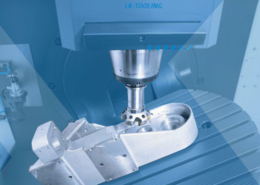