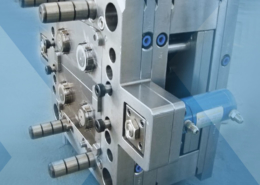
Motherson Sumi sets up wire harness unit in UAE - plastic molding for wire 1 2
Author:gly Date: 2024-09-30
Europe region is the fastest growing region in the plastic injection molding market. The cosmetics, pharmaceuticals, and home chemicals are some of the packaging applications in the Europe region. The consumables and electronics applications demand is predicted to be driven by rising demand for electronic appliances like laptops and cell phones, notably in the developed regions.
The high initial cost of injection molding machines is the primary growth constraint in the global plastic injection molding market. As petroleum products are raw materials for the plastic industry, the fluctuating nature of fuel prices limits market growth. Furthermore, growing concern about the negative environmental impact of plastics, as well as research into alternatives, will have a negative impact on the market.
The molded plastics have a wide range of uses in a variety of industries. The biggest demand generators are the automobile, electronics, and construction industries. As a result of the rise of these industries, plastic injection molding market’s share is steadily expanding.
He continued, “Our decision to move forward with Arburg was clearly based on our history of success using their machines. Their machines feature a sound mechanical design coupled with a very progressive control system.”
Injection molded plastics are used to make a variety of automotive parts, including wheel covers, enclosures, consoles, headlight housings, and interior parts. Their high tensile strength, chemical corrosion resistance, lightweight, durability, and high resistance to physical impact have encouraged manufacturers to replace metal parts in automotive design. The implementation of stringent vehicle emission regulations, as well as a greater emphasis on fuel efficiency, has increased demand for lightweight vehicles, propelling the plastic injection molding market in these regions. Furthermore, automotive manufacturers are effectively utilizing injection molded plastics because they provide improved recyclability, durability, abrasion resistance, vibration control, and strength. Injection molded plastics also allow manufacturers to reduce production costs, facilitate modular assembly, and improve vehicle exterior aerodynamics. Thus, increased emphasis on light weight materials to reduce fuel consumption is creating lucrative opportunities for the growth of plastic injection molding market during the forecast period.
Silcotech North America, a specialist in Liquid Silicone Rubber (LSR) injection moulding, has announced its expanding capacity with the purchase of two new injection moulding machine workcells.
“Twenty-five years ago, we set out to become a global leader of liquid silicone moulded parts. Having spent 17 years in a technical capacity with a world-renowned moulding machine manufacturer, injection moulding machines were part of my DNA,” he said.
Michael Maloney, Silcotech president, said that Arburg was chosen as the supplier of the new machines because of their long history of success providing machines for LSR applications.
The two new Arburg machines include a 110 US ton ALLROUNDER 470 A 1000 - 290 Comfort, and a 220 US ton ALLROUNDER 570 A 2000 - 400 Comfort. Both are all-electric machines specified with LIM/LSR moulding options as well as thermoplastic moulding capabilities. They will both be equipped with MULTILIFT SELECT 8 servo electric robotics for parts removal and manipulation. Delivery is scheduled for summer 2024.
Isolde Boettger, vice president and co-founder of Silcotech North America, said, “Michael’s technical experience, coupled with Arburg’s very solid and proven technology developments in LSR moulding technology, were superior when we made the decision to purchase our first two Arburg machines in 1998 when we started Silcotech North America. Looking back on our decision and evaluating the technology on a regular basis, it is clear Arburg was, and continues to be, the right decision for the competitive LSR space.”
“Silcotech’s business has seen growth in the 15% to 20% per year range over the past two years and the outlook is to keep that pace that in FY2024 and beyond,” said Morris.
Asia-Pacific is the largest segment for plastic injection molding market in terms of region. In developing countries of the Asia-Pacific region, rising infrastructure spending combined with rising automotive demand is expected to drive the market penetration. Due to the low labor costs in the Asia-Pacific nations such as Japan, China, and South Korea and major end use industries like automobile and electronics are driving the market growth.
Ottawa, Jan. 24, 2022 (GLOBE NEWSWIRE) -- The global plastic injection molding market size was worth at USD 167.2 billion in 2020. The plastic injection molding market is expected to be driven by rising demand for plastic components from various end use sectors such as packaging, automotive, household appliances, medical devices, and electrical and electronics. The injection molded technology has grown in importance in the mass manufacturing of difficult plastic shapes as a result of modern advancements to reduce the rate of defective production.
The plastic injection molding market is expanding due to rising demand for molded plastics in various end-user industries. The injection molding process enables the mass production of plastic goods with high efficiency and minimal resource waste. As a result, its market share is growing as a result of its low production costs and high reproducibility. Injection molded plastic has a wide range of applications in a variety of end-user industries. The automotive industry is also increasing its demand for lightweight and long-lasting objects to replace heavy metal parts. Similarly, the expansion of the packaging, construction, and pharmaceutical industries is increasing demand for injection molded plastics. Furthermore, technological advancements in molding technology will undoubtedly benefit the injection molding industry and fuel plastic injection molding market growth.
The new machines will be used to expand capacity at Silcotech's headquarters in Bolton, Ontario. They will be added to the existing fleet to handle growing business volume, and the new machines are sizes where increased capacity is needed, said Dan Morris, Business Development Manager at Silcotech.
Precedence Research is a worldwide market research and consulting organization. We give unmatched nature of offering to our customers present all around the globe across industry verticals. Precedence Research has expertise in giving deep-dive market insight along with market intelligence to our customers spread crosswise over various undertakings. We are obliged to serve our different client base present over the enterprises of medicinal services, healthcare, innovation, next-gen technologies, semi-conductors, chemicals, automotive, and aerospace & defense, among different ventures present globally.
“At that time there were only two significant players offering LIM options for their moulding machines – Arburg was one of them.”
You can place an order or ask any questions, please feel free to contact at sales@precedenceresearch.com | +1 9197 992 333
There are several other cost-effective methods that limit the use of injection molding. The plastic injection molding is a high-cost technology that limits the market growth even more. The emerging technologies like 3-dimensional (3D) printing are evolving all the time and can now create miniature things that are similar to injection molded ones. In the near future, further improvement in such technologies is projected to have a detrimental influence on demand for plastic injection molding products.
GETTING A QUOTE WITH LK-MOULD IS FREE AND SIMPLE.
FIND MORE OF OUR SERVICES:
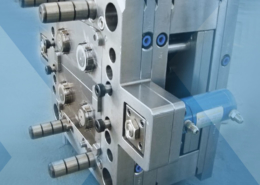
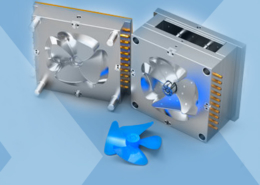
Plastic Molding

Rapid Prototyping
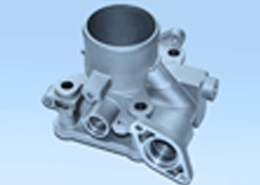
Pressure Die Casting
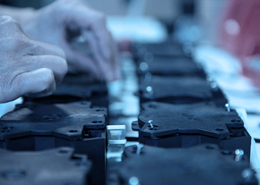
Parts Assembly
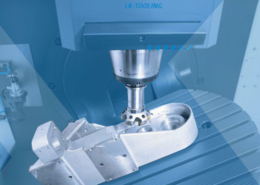