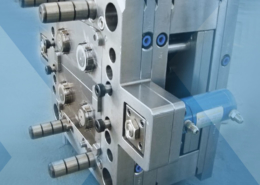
Moldex3D to preview next-gen plastic injection molding simulation software
Author:gly Date: 2024-09-30
By the end of 2021, countries around the world will begin a new wave of energy regulation. This gives the MIM industry a powerful business opportunity as a relatively energy-efficient manufacturing process. MIM is highly flexible and offers many advantages for small parts manufacturing, especially in comparison to processes with high energy consumption and a negative environmental impact, such as die casting, lost-wax casting (investment casting), traditional casting, forging, etc (Fig. 9).
Plastics Technology covers technical and business Information for Plastics Processors in Injection Molding, Extrusion, Blow Molding, Plastic Additives, Compounding, Plastic Materials, and Resin Pricing. About Us
Gifted with extraordinary technical know how and an authoritative yet plain English writing style, in this collection of articles Fattori offers his insights on a variety of molding-related topics that are bound to make your days on the production floor go a little bit better.
DUS Architects says this is the first time in the world that these kinds of XXL 3D prints are being shown in the public domain.
While prices moved up for three of the five commodity resins, there was potential for a flat trajectory for the rest of the third quarter.
Discover suppliers of these and more in our advertisers’ index and buyer’s guide, available in the back of PIM International.
Take a deep dive into all of the various aspects of part quoting to ensure you’ve got all the bases—as in costs—covered before preparing your customer’s quote for services.
technotrans says climate protection, energy efficiency and customization will be key discussion topics at PTXPO as it displays its protemp flow 6 ultrasonic eco and the teco cs 90t 9.1 TCUs.
HP’s Metal Jet has undergone significant refinement in the years since it was first unveiled in 2018. Now, by incorporating nearly the whole Bind...»
Prof Xuanhui Qu (Fig. 5) teaches Powder Metallurgy at the School of Materials Science and Engineering, within the University of Science and Technology Beijing. He is a Chinese-educated scholar who, since the beginning of his professorship in 1992, has trained over one hundred postgraduate students, many of whom are active in the MIM industry, including engineers, CTOs and CEOs. He allows students to guide their own work – something very admirable amid potentially rigid academic life. Today, he is the president of the MIM Association of the China Powder Metallurgy Alliance (CPMA), as well as the president of Powder Metallurgy Committee of the Chinese Society of Metals. He has served as Editor in Chief of the journal Powder Metallurgy Technology, the longest-running Chinese PM journal, since 2010.
Second quarter started with price hikes in PE and the four volume engineering resins, but relatively stable pricing was largely expected by the quarter’s end.
Mike Sepe has authored more than 25 ANTEC papers and more than 250 articles illustrating the importance of this interdisciplanary approach. In this collection, we present some of his best work during the years he has been contributing for Plastics Technology Magazine.
The Plastics Industry Association (PLASTICS) has released final figures for NPE2024: The Plastics Show (May 6-10; Orlando) that officially make it the largest ever NPE in several key metrics.
All these equipment innovations have been based on a desire for greater environmental protection, CO2 reduction, energy conservation, and safety. In addition to furnace technology, innovations have also been introduced that automate feedstock kneading and granulation, saving on labour costs.
Introduced by Zeiger and Spark Industries at the PTXPO, the nozzle is designed for maximum heat transfer and uniformity with a continuous taper for self cleaning.
The project is the first commercial spin-off resulting from the collaborations on the 3D Print Canal House, which is an initiative of DUS architects and partners. The production of the 3D prints has been done by Actual, an Amsterdam-based start-up that develops online customizing software for building elements linked to XL 3D printing. The façade has been developed due to to the close collaboration between the various parties: DUS (design), Actual (parametric development & 3D printing), Neptunus (temporary structures), TenTech (engineering), Henkel (material development), Philips (light), and Heijmans (construction and assembly).
Across the show, sustainability ruled in new materials technology, from polyolefins and engineering resins to biobased materials.
Successfully starting or restarting an injection molding machine is less about ticking boxes on a rote checklist and more about individually assessing each processing scenario and its unique variables.
Although MIM technology has only existed for around half a century, it has been promoted in Greater China since 1985. The fortuitous combination of the many events and circumstances presented here has resulted in the Chinese MIM industry accounting for half of the world’s production. What is clear is that well-funded R&D centres, connected to industry by high-profile ‘technology champions’, all operating within a defined strategic national framework, can result in what, by any standards, is a major success story.
The 2023 International Conference on Injection Moulding of Metals, Ceramics and Carbides (MIM2023), organised by the Metal Powder Industries Federa...»
Processors with sustainability goals or mandates have a number of ways to reach their goals. Biopolymers are among them.
I believe that we are all curious as to the reasons driving the rapid growth of the MIM industry in Greater China – including mainland China, Taiwan, Hong Kong, and Macau – in the last decade. Is success down to being in the right place at the right time, to a series of coincidences, or can individuals and governments, through strategic goals or individual efforts, drive the success of an industry? Here is my analysis.
How has the global Metal Injection Molding industry weathered the most turbulent years in recent history, and what has the impact been on MIM’s k...»
Sustainability continues to dominate new additives technology, but upping performance is also evident. Most of the new additives have been targeted to commodity resins and particularly polyolefins.
Learn about sustainable scrap reprocessing—this resource offers a deep dive into everything from granulator types and options, to service tips, videos and technical articles.
Join KraussMaffei for an insightful webinar designed for industry professionals, engineers and anyone interested in the manufacturing processes of PVC pipes. This session will provide a comprehensive understanding of the technology behind the production of high-quality PVC pipes: from raw material preparation to final product testing. Agenda: Introduction to PVC extrusion: overview of the basic principles of PVC pipe extrusion — including the process of melting and shaping PVC resin into pipe forms Equipment and machinery: detailed explanation of the key equipment involved — such as extruders, dies and cooling systems — and their roles in the extrusion process Process parameters: insight into the critical process parameters like temperature, pressure and cooling rates that influence the quality and consistency of the final PVC pipes Energy efficiency: examination of ways to save material and energy use when extruding PVC pipe products
In mainland China, there are two major triangular economic zones – the Pearl River and the Yangtze River deltas. Together, these are home to almost the entire capacity of Chinese manufacturing. Within the Pearl River Delta, the Greater Bay Area (GBA) represents nine cities from the Guangdong province, as well as the entirety of the Macau and Hong Kong regions (Fig. 1). This is the world’s most populous bay area – greater than San Francisco, New York, and Tokyo – and alone represents one of the largest economies in the world. The GBA hosts the greatest number of MIM plants in Greater China.
Multiple speakers at Molding 2023 will address the ways simulation can impact material substitution decisions, process profitability and simplification of mold design.
In this collection of articles, two of the industry’s foremost authorities on screw design — Jim Frankand and Mark Spalding — offer their sage advice on screw design...what works, what doesn’t, and what to look for when things start going wrong.
It’s all about sustainability and the circular economy, and it will be on display in Orlando across all the major processes. But there will be plenty to see in automation, AI and machine learning as well.
Exhibitors and presenters at the plastics show emphasized 3D printing as a complement and aid to more traditional production processes.
When Apple launched its new iPhone 13, we were very happy to see that parts produced by Metal Injection Molding still featured heavily. While the company’s requirements for MIM parts are very demanding across the board, this is especially the case in terms of part complexity, tolerances and appearance. It is in the latter – in a part’s aesthetic features – where the capabilities of MIM products can often be best demonstrated. Their excellent metallic appearance and surface finish, in addition to a variety of special capabilities unique to certain alloys, all available at a relatively quick production speed, are some of the key factors in MIM’s rise in popularity. And the technology’s progress shows little sign of slowing, with the new generation of folding smartphones relying on metal injection moulded hinges to deliver stable, long term performance.
While prices moved up for three of the five commodity resins, there was potential for a flat trajectory for the rest of the third quarter.
Hundreds of tons of demonstration products will be created this week. Commercial Plastics Recycling is striving to recycle ALL of it.
Join Engel in exploring the future of battery molding technology. Discover advancements in thermoplastic composites for battery housings, innovative automation solutions and the latest in large-tonnage equipment designed for e-mobility — all with a focus on cost-efficient solutions. Agenda: Learn about cutting-edge thermoplastic composites for durable, sustainable and cost-efficient battery housings Explore advanced automation concepts for efficient and scalable production See the latest large-tonnage equipment and technology innovations for e-mobility solutions
One could be mistaken for thinking that the materials used by MIM today are based on quite long-established specifications such MPIF Standard 35. Don’t overlook the fact that, historically, industrial powder production had never been able to atomise high percentages of d50 < 15 µm fine powder. The production of MIM grade powders is as high as ever. At least ten powder manufacturers in China produce more than 2,500 tons of MIM powder a year – there is even one small factory with a single atomiser, yet it can also produce 250 tons of MIM powder a year. This easy sourcing of raw materials has therefore also been a major boost for MIM’s development.
After successfully introducing a combined conference for moldmakers and injection molders in 2022, Plastics Technology and MoldMaking Technology are once again joining forces for a tooling/molding two-for-one.
Mixed in among thought leaders from leading suppliers to injection molders and mold makers at the 2023 Molding and MoldMaking conferences will be molders and toolmakers themselves.
In this collection of content, we provide expert advice on welding from some of the leading authorities in the field, with tips on such matters as controls, as well as insights on how to solve common problems in welding.
Extensive MIM, CIM industry and sinter-based AM industry news, plus the following exclusive deep-dive articles and reports:
Mold maintenance is critical, and with this collection of content we’ve bundled some of the very best advice we’ve published on repairing, maintaining, evaluating and even hanging molds on injection molding machines.
In a time where sustainability is no longer just a buzzword, the food and beverage packaging industry is required to be at the forefront of this innovation. By adopting circular packaging processes and solutions, producers can meet regulatory requirements while also satisfying consumer demand and enhancing brand reputation. Join Husky to learn more about the broader implications of the circular economy — as well as how leading brands are leveraging this opportunity to reduce costs, increase design flexibility and boost product differentiation. Agenda: The cost and operational benefits of embracing circularity Key materials in circular packaging — including rPET and emerging bioplastics How to design a circular food and beverage package Strategies for selecting sustainable closures to future-proof packaging solutions Optimization and streamlining of production processes for enhanced efficiency How Husky Technologies can enable your sustainable success
Reach a truly international audience that includes component manufacturers, end-users, industry suppliers, analysts, researchers and more.
In this collection, which is part one of a series representing some of John’s finest work, we present you with five articles that we think you will refer to time and again as you look to solve problems, cut cycle times and improve the quality of the parts you mold.
Today, a record number of rapid tooling producers exist with the ability to complete a set of four-cavity moulds within seven days, in order to provide prototypes to customers. Perhaps this is the main reason why the MIM industry does not use additively manufactured rapid prototypes. Many tooling factories in Greater China already operate highly efficient and automated ‘lights out’ production – this is a real enabler of the fast delivery times offered by the MIM industry.
This month’s resin pricing report includes PT’s quarterly check-in on select engineering resins, including nylon 6 and 66.
The free-to-access PIM International magazine archive offers unparalleled insight into the world of MIM, CIM and sinter-based AM from a commercial and technological perspective through:
The rise of MIM technology can be viewed in parallel to the rise of smartphones. With perhaps the same global impact as the adoption of fire, smartphones have changed human civilisation. They allow unprecedented information transmission and clearer, more widespread communication than ever before. Of course, this universal electronic device needs to be strong, functional and aesthetically appealing. MIM products provided the necessary structural strength for this whilst having the desired aesthetically appealing appearance (Figs. 6–8).
Additive technology creates air pockets in film during orientation, cutting down on the amount of resin needed while boosting opacity, mechanical properties and recyclability.
Prof Shun-Tian Lin (Fig. 4) teaches in the Department of Mechanical Engineering, Taiwan University of Science and Technology. He returned to Taiwan from the United States in 1991 to promote the MIM of iron, stainless steel, copper and carbides, as well as ceramics. My master’s and PhD courses were guided by Prof Lin. His highest achievement is bridging the gap between PIM research and industry. Using his in-depth knowledge of a wide range of materials, he has guided many companies in Greater China to successfully integrate MIM and CIM technology into their products.
Resin drying is a crucial, but often-misunderstood area. This collection includes details on why and what you need to dry, how to specify a dryer, and best practices.
The COVID-19 pandemic, the US/China semiconductor trade war, and the wider semiconductor crisis led to reduced smartphone production, resulting in a reduction in the demand for MIM parts for this application. This resulting spare capacity led to an immediate production shift in Greater China. Small smartphone parts were replaced by components for domestic products, often larger in size. This shift was in part possible thanks to the low cost of Chinese MIM powders. This, combined with low domestic transport costs, has allowed raw materials and products to be produced nearer the point of demand, without the need for international shipping. The MIM industry in Greater China has, in this instance, proven itself resilient.
Join this webinar to explore the transformative benefits of retrofitting your existing injection molding machines (IMMs). Engel will guide you through upgrading your equipment to enhance monitoring, control and adaptability — all while integrating digital technologies. You'll learn about the latest trends in IMM retrofitting (including Euromap interfaces and plasticizing retrofits) and discover how to future-proof your machines for a competitive edge. With insights from industry experts, it'll walk you through the decision-making process, ensuring you make informed choices that drive your business forward. Agenda: Maximize the value of your current IMMs through strategic retrofitting Learn how to integrate digital technologies to enhance monitoring and control Explore the benefits of Euromap interfaces and plasticizing retrofits Understand how retrofitting can help meet new product demands and improve adaptability Discover how Engel can support your retrofitting needs, from free consultations to execution
When, how, what and why to automate — leading robotics suppliers and forward-thinking moldmakers will share their insights on automating manufacturing at collocated event.
This Knowledge Center provides an overview of the considerations needed to understand the purchase, operation, and maintenance of a process cooling system.
Prof Kuen-Shyang Hwang (Fig. 3) teaches in the Department of Materials Science and Engineering, Taiwan University. He returned to Taiwan in 1988 from the United States, where he began his MIM research. All of Prof Hwang’s teachings and research are related to PM and MIM, an area in which he has mentored many students, many of whom are now in the MIM industry. Among these is Dr Y C Lu, Professor Hwang’s first PhD graduate, of Taiwan Powder Technology Co., Ltd. (TPT). TPT was the first company in Asia to produce MIM 3C products on a large-scale production order.
Ultradent's entry of its Umbrella cheek retractor took home the awards for Technical Sophistication and Achievement in Economics and Efficiency at PTXPO.
Formnext Chicago is an industrial additive manufacturing expo taking place April 8-10, 2025 at McCormick Place in Chicago, Illinois. Formnext Chicago is the second in a series of Formnext events in the U.S. being produced by Mesago Messe Frankfurt, AMT – The Association For Manufacturing Technology, and Gardner Business Media (our publisher).
While the major correction in PP prices was finally underway, generally stable pricing was anticipated for the other four commodity resins.
Join Wittmann for an engaging webinar on the transformative impact of manufacturing execution systems (MES) in the plastic injection molding industry. Discover how MES enhances production efficiency, quality control and real-time monitoring while also reducing downtime. It will explore the integration of MES with existing systems, emphasizing compliance and traceability for automotive and medical sectors. Learn about the latest advancements in IoT and AI technologies and how they drive innovation and continuous improvement in MES. Agenda: Overview of MES benefits What is MES? Definition, role and brief history Historical perspective and evolution Longevity and analytics Connectivity: importance, standards and integration Advantages of MES: efficiency, real-time data, traceability and cost savings Emerging technologies: IoT and AI in MES
Despite price increase nominations going into second quarter, it appeared there was potential for generally flat pricing with the exception of a major downward correction for PP.
The aim of this presentation is to guide you through the factors and the numbers that will help you determine if a robot is a smart investment for your application. Agenda: Why are you considering automation? What problems are you trying to solve? How and why automation can help Crunch the numbers and determine the ROI
In life, some things develop naturally, and some are helped along by luck. The successful development of industrial technology also needs coincidence. These are some of the ‘coincidences’ that I believe had an impact on the development of MIM in China.
While the melting process does not provide perfect mixing, this study shows that mixing is indeed initiated during melting.
Greater China has a lot of plastic injection moulding companies, meaning there are also quite a few corresponding injection moulding tooling factories. Although the tooling used for MIM and plastic injection moulding are different, a ‘general’ injection moulding tooling factory may still have experience manufacturing some sets of MIM tools. Moreover, these factories can quickly learn the specific manufacturing expertise needed for MIM tools, and expand production.
While many people still don’t know MIM by name, its products have followed people into their smartphones, cars and domestic appliances. MIM technology is a multi-step combination of traditional industrial technologies. Each step requires careful learning, observation, recording and operation. Due to its unique human resources and the nature of business in Greater China, the MIM industry has been able to adapt itself into just what its customers need.
Don't miss any new issue of PIM International, and stay up to date with the latest industry news. Sign up to our fortnightly newsletter.
With the support of these R&D programmes, great progress has been made in basic research, from alloy selection, to binder design, fundamental process research and so on. The success of this basic research has established a substantial foundation for the rapid development of China’s MIM industry.
The Leadership of the Council of the European Union is conducted on a rotating schedule, meaning each country holds the presidency for six months at a time. The Netherlands took over on Jan. 1, 2016 and needed a place to hold the European meetings for the next six months. The group decided to use innovative resources in constructing the building for the meetings.
Of course, it is not always ‘plain sailing’: equipment manufacturers are working day and night, both to fulfil equipment orders and develop new equipment, and many MIM factories use the current intermittent power supply situation to complete customer orders – including the author himself, as I write this manuscript. Welcome to Greater China and its MIM family!
August 29-30 in Minneapolis all things injection molding and moldmaking will be happening at the Hyatt Regency — check out who’s speaking on what topics today.
Thousands of people visit our Supplier Guide every day to source equipment and materials. Get in front of them with a free company profile.
Core Technology Molding turned to Mold-Masters E-Multi auxiliary injection unit to help it win a job and dramatically change its process.
Plastics Technology’s Tech Days is back! Every Tuesday in October, a series of five online presentations will be given by industry supplier around the following topics: Injection Molding — New Technologies, Efficiencies Film Extrusion — New Technologies, Efficiencies Upstream/Downstream Operations Injection Molding — Sustainability Extrusion — Compounding Coming out of NPE2024, PT identified a variety of topics, technologies and trends that are driving and shaping the evolution of plastic products manufacturing — from recycling/recyclability and energy optimization to AI-based process control and automation implementation. PT Tech Days is designed to provide a robust, curated, accessible platform through which plastics professionals can explore these trends, have direct access to subject-matter experts and develop strategies for applying solutions in their operations.
The localisation of MIM equipment production began in about 2011 and hasn’t stopped since. More than five generations of batch vacuum sintering and debinding furnaces were developed in only a decade. The invention of oxalic acid catalytic debinding by Shenzhen SinterZone technology Co., Ltd. in 2014 was a big step towards reducing the environmental impact of the MIM debinding process. Ningbo HIPER Vacuum Technology Co., Ltd. advanced its batch vacuum sintering furnace technology to six-zone temperature control. Continuous sintering furnaces have also been manufactured for five years by Hiper and SinterZone.
In early 2008 in China, a severe winter blizzard paralysed transportation and affected hundreds of millions of people preparing to return home for the Chinese New Year. The weather also worsened the ongoing economic depression at that time, as workers were left unable to return to their workplaces. Following this crisis, the Chinese government began to focus on the improvement and construction of the country’s transportation infrastructure – power networks, communications, roads, railways, and water supply. After ten years of construction, the foundations of the relevant transportation systems had been transformed. Connected with this, the MIM industry found the opportunity to benefit not only from increased government funding, leading to rapid adoption by a variety of sectors, but it also directly benefited from the new, faster, more efficient transportation networks.
The GBA is also home to a leading manufacturing innovation city: Shenzhen. While the region faces increasing competition for low-cost manufacturing from Southeast Asian countries such as India and Vietnam, as well as in rapid research and development for innovative electronics from Europe, the United States, and Japan, the industry here naturally aims to keep its name relevant through its MIM technology capabilities. With the ability to meet the needs of a large number of orders in a short amount of time, it slots into place with the product development and mass-production methods already established in the GBA.
The printed patterns build up from large to small and round to square and depict the variety and community of the EU countries. Every seating element is parametrically designed and fits perfectly within each alcove. They are prototypes developed especially for the EU presidency, and printed locally with the XXL 3D printer of the 3D Print Canal House in Amsterdam. This life-size printer can print elements up to 2 x 2 x 3.5 meters. The prints are made of a specially developed bioplastic and the seating surfaces are filled with a light-colored concrete. The bioplastic can be shredded and reprinted after the presidency is over.
The entrance façade, designed by Amsterdam-based DUS Architects, consists of unique 3D printed elements made of bioplastic that the company says can be fully recycled after the presidency is over. The entrance of the building is partially constructed with shaped sails that refer to the historical sailing ships that used to be built in this area. This creates alcoves, which house EU-blue colored 3D-printed benches.
The dissemination of knowledge is crucial when considering whether a new technology can be adopted by a region. I joined the MIM industry in 1991, one afternoon during the first week of my master’s degree, and, after thirty years in the field, I have come up with a list of the three most respected educators from Greater China who have played a key role in nurturing and developing the talent that enabled the industry’s success.
In this three-part collection, veteran molder and moldmaker Jim Fattori brings to bear his 40+ years of on-the-job experience and provides molders his “from the trenches” perspective on on the why, where and how of venting injection molds. Take the trial-and-error out of the molding venting process.
A technical session, comprising three papers, at the Euro PM2021 Virtual Congress, organised by the European Powder Metallurgy Association (EPMA) a...»
Across all process types, sustainability was a big theme at NPE2024. But there was plenty to see in automation and artificial intelligence as well.
As early as 1996, MIM was identified as one of the key technologies for the future of China’s manufacturing industry. MIM research and development programmes have been continuously supported by government programmes such as the National Natural Science Foundation of China (NSFC), the National High-Tech R&D Program of China (863 Program), the National Basic Research Program of China (973 Program), and the National Key Research and Development Program of China, to name just a few.
Discover how artifical intelligence is revolutionizing plastics processing. Hear from industry experts on the future impact of AI on your operations and envision a fully interconnected plant.
In terms of technical contribution, Prof Hwang was the one who advocated ASTM F75 alloys for smartphones; this alloy has since been used in the camera frames of over 500 million smartphones since 2016. He has published two textbooks, Powder Metallurgy (3rd ed.) and Metal Injection Molding (2nd ed.), both of which are widely used in industry and academia. However, he has often said that, while we can record our knowledge in such books, we should better appreciate the real-world skills, know-how and experiences which are key to making things happen and keeping the MIM industry strong and vibrant.
Say “manufacturing automation” and thoughts immediately go to the shop floor and specialized production equipment, robotics and material handling systems. But there is another realm of possible automation — the front office.
GETTING A QUOTE WITH LK-MOULD IS FREE AND SIMPLE.
FIND MORE OF OUR SERVICES:
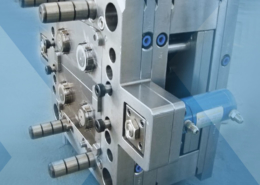
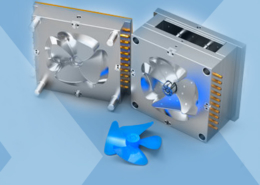
Plastic Molding

Rapid Prototyping
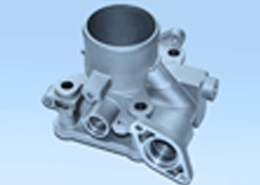
Pressure Die Casting
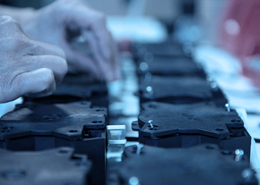
Parts Assembly
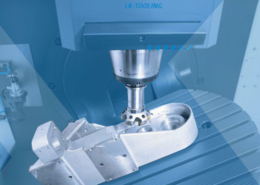