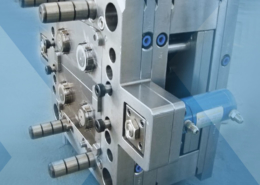
Molded-in-Color Parts Replace Metallic Paint on SUV Center Console Housing - mol
Author:gly Date: 2024-09-30
The LRTM concept uses vacuum pressure to hold the two halves of a closed mold together, while injecting resin at very low pressure — essentially a hybrid of RTM and vacuum infusion processing. One mold half, usually the lower or female half, is relatively rigid, while the matching counter mold half is thin and relatively flexible. Typically a manufacturer can use his existing open mold if it has a suitable edge flange for sealing and resin injection; the matching counter can be readily fabricated on the lower mold. Advantages of LRTM include its simplicity and very low cost, ability to produce parts with gel coated surfaces on both sides, and the potential for producing four or five times as many parts per day as open molding. LRTM part tolerances are tighter and part-to-part consistency is greater than open-molded parts, but LRTM does not achieve levels associated with traditional RTM. Fiber volumes also are less, on the order of 18 to 20 percent.
This sidebar to CW’s August 2024 feature article reviews this technology for more efficient composites manufacturing and why it aligns with Koridion active core molding.
The first project is underway to recover carbon fiber used in an A330-200 aircraft, which will then be regenerated for other end uses by HRC.
The Autoclave Scheduler is designed to increase autoclave throughput, save operational costs and energy, and contribute to sustainable composite manufacturing.
An on-demand mapping tool for anisotropic materials and polymer material fracture prediction model, i-Lupe, aims to help predict impact, crash behaviors.
This collection details the basics, challenges, and future of thermoplastic composites technology, with particular emphasis on their use for commercial aerospace primary structures.
MIT tooling, an RTM variation introduced about five years ago by Harper, incorporates multiple, identical, low-cost mold faces or skins, that can be quickly cycled in and out of the RTM mold press to increase productivity. While one skin is being injected and cured in the mold, others can be gel coated and loaded for the next cycle. Approximately 4 mm to 6 mm/0.158 inch to 0.25 inch thick, the skins can be composite, electroformed nickel, ceramic, elastomer or whatever material best suits the design. The system includes a heated hard tool base (which Harper calls a bolster), a matching upper counter mold, an offline "holding" bolster to support the MIT skins during demolding, and associated hardware.
Base Materials introduces a high-performance, toughened epoxy tooling board designed for thermoforming and vacuum forming processes, direct-to-part applications and more.
As the composites industry has matured, so has the tooling industry that underpins composites fabrication. But toolmakers perennially find themselves on the horns of a dilemma — clients demand quality tools that deliver dimensionally accurate, high-quality parts, but balk at the costs and lead times necessary to produce them.
And we haven't even begun to touch on the truly different tooling approaches available, such as soluble tooling from Advanced Ceramics Research Inc. (Tucson, Ariz., U.S.A.); a reusable ceramic material that changes from a liquid to a solid state to quickly form a tool, developed by 2Phase Technologies Inc. (Dayton, Nev., U.S.A.); Roctool SA (Le Bourget du Lac, France) rapid resistive heating and inductive heating molding concepts; a foamed carbon material from Touchstone Research Laboratory Ltd. (Triadelphia, W. Va., U.S.A.); and a new composite tooling concept soon to be introduced by Scion Industries LLC (Ft. Collins, Colo., U.S.A.).
Janicki Industries also produced the composite tools used by AAR Composites (Clearwater, Fla., U.S.A.) to make the bodies for the Las Vegas rapid transit monorail system, in Nevada. The E-glass/epoxy composite tools with steel backup structures incorporated details like window and door cutouts, which allowed net layups without the need for postcure cutting and finishing.
Whether you’re exploring new applications or seeking to gain a foothold in emerging markets, Carbon Fiber 2024 is where you’ll discover the insights and connections needed to shape your business strategy. Register now.
Low-melt polyaryletherketone (LMPAEK) unidirectional tapes provide outstanding thermal and fire protection, demonstrating their effectiveness through rigorous testing. These tapes are fire, smoke and toxicity compliant with FAR25.853 and meet OSU Heat Release Rate standards. The tapes were tested under ISO 2685/AC 20-135 Change 1, meeting the fireproof criteria. Additionally, they met UL 2596 requirements for battery thermal runaway tests. These tapes are crucial for high-temperature applications showcasing their resilience and safety in both aerospace and automotive applications. Part of a broader range that includes films and compounds, Victrex LMPAEK materials are valued for their excellent processability and weldability. They offer versatile solutions for complex needs beyond traditional structural parts, such as: thermal runaway and lightning strike protection, heat sinking, and intricate bracketry. Victrex LMPAEK materials facilitate automation and high-rate production while addressing performance and sustainability challenges. With reduced environmental impact, lower weight and cost-efficiency, they meet the evolving demands of the transportation industry and support innovative design solutions. Agenda: Introduction to LMPAEK ecosystem, highlighting unidirectional tapes Thermal and fire protection performance: applications and benefits Material forms and processability Sustainability and efficiency Conclusion and future innovations
Prepreg co-molding compound by IDI Composites International and A&P Technology enables new geometries and levels of strength and resiliency for automotive, mobility.
Six U.S. companies have proven their recycling technologies for composites and rare earth elements, and will be supported for relevant scale demonstration and validation.
RTM methods have multiplied over the past 15 years, as manufacturers have recognized the benefits of the process. A two-part, machined RTM mold delivers a smooth surface finish on both sides of the part and can produce complex, detailed, near-net shapes at a high rate with minimal post-production trimming. The fact that the resin is delivered under pressure with the mold halves clamped together (or held together in a press) means parts are consistent, repeatable, dimensionally stable and well-consolidated, with high fiber content (50 to 70 percent) and excellent void control (usually less than 0.2 percent). For high-performance parts made with higher-viscosity toughened resins, molds are usually heated (accomplished with heated oil galleys) and resin injection pressure is controlled with a meter/mix injection machine. Raw material costs are generally less than those for hand layup because dry preforms are used rather than traditional prepregs. Cycle time can range from two to three hours — shorter than typical autoclave cure cycles.
"The clients we work with whose parts must meet various certifications – UL, FAA, and MIL-spec, among others – need to have a 'real' part to test against their real-world challenges. RPM facilitates that by getting testable parts into the field quickly," said David Brantner, Chief Executive Officer of Alpine Advanced Materials. "Think of companies bidding for military or aerospace contracts – it's powerful to have data that backs up whether your components actually work."
Even for suppliers of more traditional metallic tooling, cost-effectiveness sometimes can be secured through changes in customer relationships, says van den Berg of ATS. "How can we reduce tooling costs? Get the tooling supplier into the process early on," he states. "We and other tooling houses have invested in engineering expertise, including CATIA5. We can do tooling design more cost-effectively than the OEMs."
Over the last 8 months, Archer Aviation has completed a total of 402 test flights with its composites-intensive aircraft, adding to key milestones.
Some aerospace part allowables, however, simply cannot be met with LRTM or MIT, and more traditional tooling is sometimes the best answer. Plastech also has designed, built and supplied highly accurate composite RTM tools with steel backup structure for projects like the ASRAAM missile manufactured for the U.K. Ministry of Defence by MBDA UK Ltd. (formerly Matra BAE Dynamics), as well as matched metal RTM molds for other high-rate production parts.
Kennametal will cover the influence of different composite materials characteristics on drilling performance and how to optimize the process. Agenda: Who is Kennametal? Hole making challenges in composite materials Innovations for hole making applications Upcoming events and academic partnerships
In 2018, Teijin broke ground on a facility that is reportedly the largest capacity carbon fiber line currently in existence. The line has been fully functional for nearly two years and has plenty of room for expansion.
Validation of 80-100% tensile strength and comparability to injection molding via Voxelfill extrusion process was achieved through plastic and fiber-filled test series.
Celebrating National Composites Week 2024, CW looks at how composites are being used to provide the next generation of energy.
During this webinar, the audience will be introduced to a variety of fiber composite technologies — as well as the machines and equipment — from short fibers to continuous fibers, from thermoset to thermoplastic, as well as the according process technology, including a special focus on long-fiber injection (LFI) and structural composite spray (SCS). Focus markets include automotive, aviation and AAM, transportation, and construction. This webinar will provide a detailed overview of according application examples. Agenda: Long fiber injection (LFI) Structural composite spray (SCS) Resin transfer molding (RTM), wet compression molding, etc. Pultrusion FiberForm
An overview of ASTM Standard Guide D8509, and its coupon-level mechanical testing of design properties for analyzing composite bolted joints.
CompositesWorld’s Tech Days: Design, Simulation and Testing Technologies for Next-Gen Composite Structures is designed to provide a multi-perspective view of the state of the art in design, simulation, failure analysis, digital twins, virtual testing and virtual inspection.
A report on the demand for hydrogen as an energy source and the role composites might play in the transport and storage of hydrogen.
"Obviously, when you're making a 40m long part, autoclave cure isn't an option," says Ridgard. "With the ZPREG material, during cure, the dry areas between the resin strips provide escape paths for the air, which results in very low porosity and, consequently, much better surface finish."
Prepreg co-molding compound by IDI Composites International and A&P Technology enables new geometries and levels of strength and resiliency for automotive, mobility.
Alpine's flagship nanocomposite material HX5® offers the strength of aluminum at half the weight with environmental and thermal performance to withstand the harshest environments. HX5 can be formed into complex shapes and easily coated without sacrificing strength, performance or aesthetics. From prototypes to full-scale injection molding production, HX5 is an ideal alternative to the cost and production challenges associated with aluminum. For more information, visit www.alpineadvancedmaterials.com.
An integrated software approach has also helped Apex Machine Tool Co. (Farmington, Conn., U.S.A.) reduce tooling development costs. The company employs Unigraphics Solutions from EDS (Maryland Heights, Mo., U.S.A.), a system that allows Apex to design, draft and machine an entire tooling project for true concurrent engineering. For a recent project, a customer's composite propeller design — also developed using Unigraphics — was readily downloaded into Apex's system, and engineers from both companies were able to collaborate on mold design throughout the process, for an on-time tool delivery and reduced cost. Apex has used its design expertise to develop unique break-apart mandrels for more efficient tooling designs, says Apex's composite designer Rich Walton.
The alternating dry and resin-impregnated strips means that 50 percent of the ZPREG material is dry, which gives it excellent drape and formability for layup. The resin is allowed to bleed through on one side of the prepreg, which gives it a slight tack. The ZPREG resin system has a broad processing window, ranging from 65°C/150°F to 150°C/302°F under a vacuum bag, but can produce tools capable of making parts that cure at 177°C/350°F.
The composites industry is increasingly recognizing the imperative of sustainability in its operations. As demand for lightweight and durable materials rises across various sectors, such as automotive, aerospace, and construction, there is a growing awareness of the environmental impact associated with traditional composite manufacturing processes.
"We've proven that with peripheral injection, you can inject resin four times faster than with a single inlet," he states. "But, pressure is the killer — if you over pressurize, you will simply warp the lighter, upper counter mold and end up with a too-thick component, which can exotherm and wreck the tooling."
Stephen Heinz, vice president of R&I for Syensqo delivered an inspirational keynote at SAMPE 2024, highlighting the significant role of composite materials in emerging technologies and encouraging broader collaboration within the manufacturing community.
Initial demonstration in furniture shows properties two to nine times higher than plywood, OOA molding for uniquely shaped components.
HPC's January/February 2001 issue (p. 20), reported that epoxy-based modeling pastes were being used not only for models, but inexpensive tools, as well. One example was The Boeing Co.'s (Chicago, Ill., U.S.A.) low-cost tooling for composites (LCTC) system. LCTC employs Vantico's (East Lansing, Mich., U.S.A.) Ren RP4040 syntactic epoxy tooling paste patties, which are pressed into a machined aluminum honeycomb substructure, and then cured and machined to final contour. Formglas (Toronto, Ontario, Canada) has since perfected the concept, proving that LCTC molds can be quickly fabricated directly from CAD data and autoclave cured for multiple part runs, with significantly lower lead times and cost. "It's the perfect tool for rapid prototyping of new structures or short-run operations," says Formglas technician Steven Burke.
Prepreg co-molding compound by IDI Composites International and A&P Technology enables new geometries and levels of strength and resiliency for automotive, mobility.
Especially in aerospace, new cost-saving tooling ideas are often stymied by the potential high cost of a part failure. Nevertheless, over the past five years, more cost-effective tooling innovations have proliferated, as vacuum and resin transfer molding (RTM) methods have been adapted for higher-performance applications. Traditional aerospace tooling is changing to take advantage of high-production-rate processing methods and new materials, while preserving part quality.
Given the countless possibilities for the design and fabrication of composite parts, the industry is counting on new innovations in the tooling to realize those parts. "People are looking for alternatives to aluminum, steel and titanium materials, particularly in the aerostructures industry, where the properties of composites bring so many advantages," says van den Berg. "The tooling industry will benefit from that."
Performing regular maintenance of the layup tool for successful sealing and release is required to reduce the risk of part adherence.
Filling the gap between a 3D printed part, which can get a client close in shape but is limited by mechanical performance, and an injection molded part, which provides form and function but requires investment in tooling, RPM delivers production-level components at a relatively low cost ideal for low volume testing. Giving product designers the chance to fully prove a part before committing to a steel mold, RPM also allows for design iterations that make testing more dynamic.
The Marservis PROeco is a mass transportation marine vessel using Bcomp natural fiber for interior parts in place of standard materials.
Advanced Composites Group (ACG, Tulsa, Okla., U.S.A. and Heanor, Derbyshire, U.K.) points to its new ZPREG prepreg material as a means of making composite tooling more cost-effective. ZPREG, originally developed for making parts, consists of two layers of reinforcement enclosing the resin. Rather than a continuous layer, the resin is applied in approximately 12.5 mm/0.5-inch wide strips, with dry strips between. But, says ACG's aerospace sector manager Chris Ridgard, it can be used to make high-temperature composite tooling with an excellent surface finish without an autoclave. The company recently completed a 40m/130-ft long wind turbine blade tool in carbon fiber/epoxy ZPREG.
Reliable news and information on where and how fiber-reinforced composites are being applied — that’s just the start of what you get from our team here at CompositesWorld.
CompositesWorld's Carbon Fiber conference offers you cutting-edge information and access to industry experts in streamlining manufacturing costs, market outlooks and forecasting, and more. You will make invaluable contacts as you meet and network with the industry's most innovative and influential leaders at Carbon Fiber. __PRESENT
The composites industry plays a crucial role in developing lightweight and durable materials for a range of applications, including those critical to national defense. One key focus area is the development of advanced structural materials and manufacturing technologies that support next-generation space, missile and aircraft systems for the U.S. Department of Defense (DOD). ARC Technologies LLC (ARC), a division of Hexcel Corporation, based in Amesbury, Massachusetts, is a provider of advanced composites structures, specialty materials and other unique products that provide the U.S. Department of Defense with advanced capabilities to protect service members while in harm’s way. This team’s specialty is to understand a specific need from a program office, PEO, platform manufacturer or other offices within the DOD. With that understanding, the team can design a solution, develop a prototype for test and evaluation, perform extensive in-house testing — including electromagnetic, environmental and structural testing — and then partner with the customer through platform evaluation. The Hexcel Amesbury division has a team of engineers on staff, including mechanical, chemical, electrical and research and development specialists that can provide design, testing and manufacturing capabilities to service customer requirements from concept through production. This presentation will illustrate capabilities in advanced composites and other specialty materials structures, focusing on the Hexcel Amesbury team's niche in electromagnetic signature reduction and other unique capabilities.
American Bureau of Shipping (ABS) certifies use of jointly developed CFRP repair technique on FPSO and FSO industrial systems, addressing traditional steel restoration challenges.
Cevotec, a tank manufacturer, Roth Composite Machinery and Cikoni, have undertaken a comprehensive project to explore and demonstrate the impact of dome reinforcements using FPP technology for composite tanks.
Formnext Chicago is an industrial additive manufacturing expo taking place April 8-10, 2025 at McCormick Place in Chicago, Illinois. Formnext Chicago is the second in a series of Formnext events in the U.S. being produced by Mesago Messe Frankfurt, AMT – The Association For Manufacturing Technology, and Gardner Business Media (our publisher).
Aerospace manufacturer joins forces with composite materials company to achieve sustainable manufacturing practices that overcome traditional composite layup tooling.
"The clients we work with whose parts must meet various certifications – UL, FAA, and MIL-spec, among others – need to have a 'real' part to test against their real-world challenges. RPM facilitates that by getting testable parts into the field quickly," said David Brantner, Chief Executive Officer of Alpine Advanced Materials. "Think of companies bidding for military or aerospace contracts – it's powerful to have data that backs up whether your components actually work."
During this CW Tech Days event, sponsored by Composites One, experts will offer presentations to review and evaluate the composite materials, processes and applications that should and will be considered for use in the infrastructure and construction markets.
Closed mold processes have many advantages over open molding. In this knowledge center, learn the basics and vital tools needed to produce parts accurately.
Advanced Engineering is the UK’s largest annual gathering of engineering and manufacturing professionals. The event will help you to source new suppliers, network, build connections and learn about the latest industry developments all in one place. Get involved and exhibit alongside 400+ exhibitors offering solutions and products across all industries and sectors to help improve your productivity and inspire creativity. With over 9,000+ of your peers due to attend and ready to network with and inspire you, this is the event you can’t afford to miss!
"With DRIV, manufacturers can produce larger and more intricate parts, with higher fabric content and high viscosity resin," says Petrovich. The method can be applied to any type of liquid molding, including vacuum-assisted resin transfer molding (VARTM) and other infusion processes.
CompositesWorld is the source for reliable news and information on what’s happening in fiber-reinforced composites manufacturing. About Us
A big advantage with RTM is part consolidation — the ability to produce a complex component as a single molded composite part rather than an assembly of multiple parts typically required in metal. Radius Engineering Inc. (Salt Lake City, Utah, U.S.A.), involved with RTM tooling development since the mid-1980s, recently molded a prototype carbon composite wing flap that will replace a multipiece aluminum assembly on the Bombardier CRJ aircraft. Because the flap can be RTM'd as a single component, it is cost-competitive with the aluminum version, and the part's excellent surface accepts paint without the need for additional surface treatment.
Using RPM, Alpine clients can additively manufacture a tool cavity injection mold, a negative of the designed part, then create the prototype using the dramatically cheaper mold. Once produced, the mold is dissolved away, leaving an injection molded prototype with fiber alignment for strength and without the surface finish issues of 3D printing. Additionally, with separable components, RPM allows for two-part tools that can be used repeatedly for low volumes that also convey both form and function equivalent to that of a standard steel tool. Alpine is known for both HX5 and its advanced design for manufacturing services, helping companies evolve to use new materials and methods in designing superior parts and components.
Recoat temperature, part orientation and bead geometry are some key design variables to consider for a successful and reliable large-format additive manufacturing (LFAM) process.
The ITHEC 2024 will take place from the 9 to 10 October 2024 in Bremen, Germany. At the 7th International Conference, more than 300 participants from around the world will be presenting and discussing newest scientific results, meet leading international specialists, share their expertise and start business co-operations in the field of thermoplastic composite technologies. The international exhibition will feature 40+ exhibitors showcasing all steps of the supply-chain. Be it materials, machines, testing, processes, or solutions. By combining the exhibition and the conference ITHEC is further fostering the inter-connectivity between science and industry.
"The design freedom Alpine can now offer their clients with Addifab Freeform Injection Molding opens the way to faster, cheaper, and greener product development," said Carsten Jarfelt, Chief Commercial Officer of Addifab in the USA. "Our technology supports product development with economical prototype tooling, cutting an average of 85 percent off the price a first functional component, and can make it faster than ever before."
Suppliers of thermoplastics and carbon fiber chime in regarding PEEK vs. PEKK, and now PAEK, as well as in-situ consolidation — the supply chain for thermoplastic tape composites continues to evolve.
CW’s editors are tracking the latest trends and developments in tooling, from the basics to new developments. This collection, presented by Composites One, features four recent CW stories that detail a range of tooling technologies, processes and materials.
The DOMMINIO project combines AFP with 3D printed gyroid cores, embedded SHM sensors and smart materials for induction-driven disassembly of parts at end of life.
"The mandrels were designed so that closing the tool would force them into their final position and overcome the natural bulk of the inner braids," explains Emmanuel Pons, Radius Engineering's project manager. "Because of details shaped into the leading edge, the first mandrel was split to prevent any locking of the tooling."
Thermoplastics for Large Structures, experts explored the materials and processing technologies that are enabling the transition to large-part manufacturing.
CW Tech Days are virtual events dedicated to the topics impacting the composites industry today. Access past event recordings and register for upcoming Tech Days.
Janicki is trying to perfect a composite tooling system fabricated by resin infusing multiple plies of dry carbon fiber tooling fabric on a pattern to create a solid laminate approximately 19-mm/0.75-inch thick. A backup structure is attached and the entire assembly is postcured at 177°C/350°F. During the postcure, the tool moves due to resin shrinkage and "spring" — a change in the curvature of a thick laminate placed on a contour or radius. Rather than attempt to constrain the movement, the company machines the cured face to final tolerance. By using infusion to create the tool, air is forced out, resulting in less tool porosity and, therefore, a better surface finish. Janicki reports that while still under development, the method is rapid and cost-effective, and will provide aerospace-grade tools that are lighter than metallic tools, with faster thermal transfer rates and the same CTE as the parts currently being produced.
The composite tubes white paper explores some of the considerations for specifying composite tubes, such as mechanical properties, maintenance requirements and more.
CompositesWorld’s CW Tech Days: Infrastructure event offers a series of expert presentations on composite materials, processes and applications that should and will be considered for use in the infrastructure and construction markets.
Long an advocate of cost-effective, low-hassle composite tooling, John Janicki, president of Janicki Industries (Sedro Woolley, Wash., U.S.A.), points out that, particularly for prototyping, the requirements of the tool (temperature performance, accuracy) must be reduced to keep tooling costs in line. "Our customers who are bidding on major programs like the Joint Strike Fighter are interested in new tooling technology, but in the end, most go for the tried and true, which often ends up being metallic tooling like Invar," states Janicki. "They all recognize the problems with Invar — like the cost, the lead times, the thermal mass, and the requirements for support infrastructure to move the tools around. One of the beauties of composite tooling is that it can accommodate any part shape — it opens up new opportunities for designers."
Explore the technologies, materials and strategies used by composites manufacturers working in the evolving space market.
Source: FormglasRen RP4040 tooling compound patties are applied to a machined aluminum honeycomb core block backup structure.
Foundational research discusses the current carbon fiber recycling landscape in Utah, and evaluates potential strategies and policies that could enhance this sustainable practice in the region.
"By working together with the part designers, you can develop a tool that can be modified later if changes are needed, which saves tremendous cost. Second, once the tool and part size are defined, the toolmaker can buy the tooling materials ahead of time, essentially sharing some of the cost risk with the customer, so that as soon as the CAD data is released, we can start milling," he explains.
Thousands of people visit our Supplier Guide every day to source equipment and materials. Get in front of them with a free company profile.
During the last decade, NCTM has introduced several RTM molding innovations to make the process more affordable and predictable for a variety of part sizes and shapes. A notable project was a modular RTM tool suite for customer GDATP — DeLand Operations (formerly Intellitec, DeLand, Fla., U.S.A.), used to produce carbon fiber/epoxy stiffener frames and bulkheads for the Apache AH-64A helicopter fuselage (see "Focus on Design," HPC January 2002, p. 40). The modular premise, borrowed from injection molding, involves a common mold base with interchangeable cavity inserts. The inserts allow production of different part shapes from the same mold, says GDATP's RTM program manager Dan Davenport. For the Apache, thirteen different frame components were produced from just two modular aluminum RTM molds, one of which was fabricated by NCTM. The insert tooling strategy cost 70 percent less than creating individual molds for each part, which enabled the development project to meet its non-recurring cost budget.
Recoat temperature, part orientation and bead geometry are some key design variables to consider for a successful and reliable large-format additive manufacturing (LFAM) process.
Additionally, stitch-bonded non-crimp fabrics (NCFs) provide manufacturers and asset owners even more ways to gain a competitive advantage with products built specifically for the environments and loading conditions in which they will be utilized. Join Vectorply Corporation and Creative Composites Group (CCG) for this in-depth webinar detailing the process of engineering NCFs to build composite parts that will stand the test of time. Unlike steel, concrete and wood, composite NCFs can be optimized utilizing various fiber types, architectures and substrates to achieve the specific goals of their application efficiently. High corrosion resistance, strength and stiffness, and longevity can all be accomplished with custom-designed laminates for these heavily abused applications. Vectorply Vice President of Engineering Trevor Gundberg and Creative Composites Group Chief Sales Officer Dustin Troutman will share their industry-leading expertise on the process of laminate design and part production. Attendees can expect to learn when to use composite NCFs in their production process and the wide range of fiber-reinforced plastic (FRP) composites that Creative Composites Group produces for the industrial and infrastructure markets. Whether you want to learn more about utilizing NCFs in your production process or why CCG’s extensive product line may be the choice for your project, this webinar is the place learn the process and how to take the next steps. Agenda: Distinct advantages of non-crimp fabrics versus alternative materials How to design laminates for specific processes such as pultrusion and infusion Real-world success spotlights of NCFs in industrial applications
"Traditional liquid molding relies on uncontrolled resin flooding, with single point, edge-of-part venting," says DRIV inventor Petrovich. "Unfortunately, this type of approach tends to result in dry spots. Manufacturers increase injection pressure to improve wetout, but this can cause fabric movement and mold deflection." Further, says Petrovich, mold mass and clamping pressure are increased, all of which tend to limit the size and complexity of RTM parts. With the DRIV concept, pockets are machined into the inner mold surface; the pockets, either circular or oval-shaped depending on the part, contain small holes drilled through the mold thickness. Tiny vented inserts with serrated edges are then placed in the pockets as dictated by the part geometry. Air can vent through the insert into the pocket and out of the mold, but the serrations prevent resin flow. Or, says Petrovich, the serrations can be machined larger to allow telltale resin flow in a particular segment of the part. The inserts and pockets are designed so that no witness marks are created in the part.
Directed resin injection and venting (DRIV) technology is another recent RTM tooling development from NCTM. In the DRIV tool, strategically placed mold inserts function as vents, allowing entrapped air to escape from the preform in a sequenced manner, which facilitates resin flow and wetout throughout the part cavity.
The JEC Forum DACH is a business meetings event organised by JEC The JEC Forum DACH is organised on October 22 and 23, 2024 by JEC, in partnership with the AVK, gathering the composite materials community from the DACH Region (Germany, Austria and Switzerland).
UCAR Composites Inc. (Irvine, Calif., U.S.A.) is another traditional aerospace tooling supplier that has streamlined its operation and reduced tooling lead times and costs with an innovative software approach. The company uses an integrated software management tool called VISUAL Enterprise from Lilly Software Assoc. Inc. (Hampton, N.H., U.S.A.) that combines manufacturing and quality functions for substantially reduced overhead expenses. The program tracks and prioritizes each tooling projection, estimated delivery times and production schedules, as well as quality issues for ISO 9000 compliance.
The composites-intensive VTOL platform is next expected to undergo a series of test flights in various conditions to validate its performance, safety and reliability, leading up to eventual certification.
In the Automated Composites Knowledge Center, CGTech brings you vital information about all things automated composites.
A recent challenge was the tool set for manufacturer North American Bus Industries Inc. (NABI, Woodland Hills, Calif., U.S.A.), which fabricates a 45-ft long, two-axle, low-floor monocoque bus structure with no separate metal chassis. Axles and suspension components attach directly to the CompoBus composite body. To get the necessary stiffness, the bus body had to be made almost entirely as a one-piece construction. Janicki produced a six-piece carbon fiber/epoxy composite tool that bolts together for layup and resin infusion, but disassembles for storage.
EU project will develop bio-based, repairable and recyclable vitrimer composites and advanced sensors for highly reliable, sustainable wind blades.
New aircraft is expected to deliver wind turbine blades from 105 meters up to expand the reach of wind energy and achieve global climate goals.
The relatively high cost of matched metal molds is usually justified only for high production runs, small parts or well-funded projects. But toolmakers are striving to overcome cost issues with innovations like modular tooling, removable inserts that can be configured for multiple parts, and alternative materials and approaches that reduce capital investment. For example, one tooling manufacturer, Dangar Engineering & Manufacturing Inc. (Newbury Park, Calif., U.S.A.), has developed a multipart automated RTM tooling concept with molds that slide on rails to eliminate mold handling. "We need a fast production method to compete against aluminum," says Dangar's president Dan Woods.
CompPair and Composite Recycling introduce a roof scoop made of recycled fibers to an eco-efficient rally buggy, which channels airflow to the engine for optimal, sustainable performance.
"The implementation of VISUAL Manufacturing helped get our scheduling and job costing under control," says UCAR's Bill Kansky, vice president of finance. "It has also helped meet our customers' demanding specifications and increased on-time deliveries to 98 percent."
How the predictive tool “CZone” is applied to simulate the axial crushing response of composites, providing valuable insights into their use for motorsport applications.
For many applications, two-part RTM molds for liquid molding aren't the solution because of part size, materials or performance requirements. Tooling for complex aerospace parts has always required precision design and careful material selection because of technical issues, such as durability, CTE mismatch and tool movement during cure), that are beyond the obvious hurdles of cost and lead time. The standard approach has always been the "model-to-mold" route, starting with a certified master, often an intermediate "splash" or reverse mold, then the actual production mold and rate tools — all requiring a lot of time, materials and floor space. But toolmakers are pushing ahead to innovate in this arena, as well, with digital master patterns, new and more affordable materials, software changes and paradigm shifts in relationships with customers.
Increasingly, prototype and production-ready smart devices featuring thermoplastic composite cases and other components provide lightweight, optimized sustainable alternatives to metal.
"It's a belt-plus-suspenders approach that reduces risk," he explains. "The inserts help you ensure complete wetout — they can either be manually operated or controlled by computer in a defined sequence that facilitates the resin front." The DRIV RTM concept was used successfully by Lockheed Martin to mold a demonstration vertical stabilizer part for the Joint Strike Fighter (JSF) aircraft program. The part's venting layout was actually modeled by the University of Delaware's Center for Composite Materials, which demonstrated that the vent inserts improved the resin flow front geometry. With better wetout at lower injection pressure, less material was needed for the mold itself, which reduced overall tooling cost. Clamping pressure requirements also were lower.
Herone, Spiral RTC, Teijin Carbon Europe and Collins Aerospace Almere recycle A350 thermoplastic composite clips/cleats waste into rods for the all-thermoplastic composite Multifunctional Fuselage Demonstrator’s crown.
A combination of Airtech’s 3D printing materials and Ascent’s production capabilities aim to support increased use of composite additive tooling in spaces like defense and aerospace.
In these sessions, experts will discuss the emerging hydrogen economy and the opportunities for composites in this lucrative space.
Continuous fiber-reinforced thermoplastic composite targets full circularity in aircraft interior applications, with FST, impact resistance and toughness features.
That sentiment is echoed by all the companies interviewed for this article, from aerospace tooling suppliers to general industry moldmakers. "The bitterness of poor quality remains long after the sweetness of low price is forgotten," states Remco van den Berg, director of sales at Advanced Tooling Systems (ATS, Almelo, The Netherlands).
DALLAS, Aug. 25, 2022 /PRNewswire/ -- Alpine Advanced Materials has introduced Rapid Prototype Molding (RPM) using Addifab's proprietary resin system and Nexa3D's printers to give clients a more rapid tool manufacturing solution that provides a functional and testable part at a fraction of the cost. Complementing Alpine's suite of high-performance engineered materials and advanced design services, RPM Freeform Injection Molding delivers complex injection molded parts more quickly and affordably than when using standard steel molds.
"We're not in the business of asking our customers to take big risks," says Rich Petrovich, president of North Coast Tool and Mold Corp. (NCTM, Cleveland, Ohio, U.S.A.). "Innovations are good, but they have to be proven."
About Alpine Advanced Materials Alpine Advanced Materials is a leading expert in the design and manufacture of custom-engineered parts for the world's most demanding aerospace, defense, energy, space, and outdoor applications. With experience across multiple industries, a collaborative approach, and deep expertise in designing for manufacturing, Alpine delivers the future of innovation.
Alan Harper, managing director of Plastech Thermoset Tectonics Ltd. (Gunnislake, Cornwall, U.K.) envisions low-cost, low-risk automated RTM systems for general and industrial molders making 500 to 2,000 parts per year, without the capital investment in heavy matched metal tools and associated tool manipulation infrastructure.
This collection features detail the current state of the industry and recent success stories across aerospace, automotive and rail applications.
How the predictive tool “CZone” is applied to simulate the axial crushing response of composites, providing valuable insights into their use for motorsport applications.
Powered by an 85% air/15% pure polyimide aerogel, Blueshift’s novel material system protects structures during transient thermal events from -200°C to beyond 2400°C for rockets, battery boxes and more.
ATS recently completed a tool set for Airbus Industrie that includes 64 tools for the A380 wing spoilers. The set includes 32 upper and lower skin layup tools in tooling steel, with 16 associated assembly jigs. Van den Berg reports that ATS is experimenting with new adjustable tools with thin face sheets made with Invar plate stock.
"The production cycle is nearly three times faster with MIT than with a single mold, leading to a much quicker capital investment payback period, and obviously much less expense than multiple sets of RTM tools," explains Harper. Hot molds often play havoc with gel coat, but the fact that a cool MIT insert can be gel coated offline and placed in the heated bolster means the mold base can maintain its temperature, eliminating cooling time delays. The MIT process has been used successfully on fairly large — up to 23m2/240 ft2 — general molding parts using vacuum lifting frames to facilitate lifting the skins.
Explore the cutting-edge composites industry, as experts delve into the materials, tooling, and manufacturing hurdles of meeting the demands of the promising advanced air mobility (AAM) market. Join us at CW Tech Days to unlock the future of efficient composites fabrication operations.
Source: Radius EngineeringThe top of the RTM mold is lifted away from the molded flap. Note that the mold weight requires lifting infrastructure.
Analyzing structural resonance of the aircraft under various loads becomes a critical step in obtaining flight certification.
Knowing the fundamentals for reading drawings — including master ply tables, ply definition diagrams and more — lays a foundation for proper composite design evaluation.
Resin is injected at a pressure of 1 to 2 psi. Harper says the process works on the principle of peripheral injection, in which the resin is introduced around the periphery of the mold, between the edge of the part reinforcement and the inner pressure gasket, rather than at a single central injection inlet. Harper stresses that pressure control is critical, and that resin flow must be carefully controlled with a meter/mix machine and a pressure sensing and control device, such as Plastech's cost-effective Mould Pressure Guard (MPG) sensor or updated PV Sensor system, which allow precise machine pressure control in the millibar range.
"One of the biggest barriers in transitioning to advanced materials is the weighty cost and time commitment required to test actual parts. Too often, the prospect of paying for a prototype that will cost tens of thousands of dollars stops innovation dead in its tracks," added Brantner. "With RPM, we allow our clients across aerospace, defense, unmanned aerial vehicles, space and outdoor to more easily tap into the power of new material and design technology for dramatically less time and money."
Program will focus on sustainable, next-gen wing solutions, including in wing design and manufacturing and advancements in carbon fiber-reinforced composite materials.
Whether you’re exploring new applications or seeking to gain a foothold in emerging markets, Carbon Fiber 2024 is where you’ll discover the insights and connections needed to shape your business strategy. Register now.
Van den Berg points to the automotive industry as a model for what is starting to occur in aerospace and other industries. Typically the OEM shifts responsibility for supplying parts to the first-tier suppliers. For example, Mercedes designs a "marketing model" — a new convertible, for example — as a 3-D surface, and leaves the details of how the various parts will be tooled and assembled up to the suppliers. In order to meet the hard deadline for producing parts, the supplier and tool designer must work in concert, in a process van den Berg feels is truly "concurrent engineering."
This session is designed to demonstrate the benefits of ultra polymers for aerospace applications with real case examples of Syensqo's polymer portfolio. Agenda: Introduction to ultra polymers (PAEK, PEKK, PEEK, PAI) key features Application of ultra polymers in aerospace: concrete examples Benefits of ultra polymers: enhanced performance, durability and cost-efficiency
Radius achieved good wetout using a single resin inlet at the center of the tool's leading edge and a single vacuum port at the center of the rear, injecting standard Hexcel RTM 6 epoxy resin at 100 psi. The tool featured a resin distribution "weir" that causes resin to flow along the tool's entire front edge, so that the part is impregnated across the broadest possible front, with the resin path proceeding from the leading edge to the trailing edge.
"More economical molding methods are needed if the composite industry is to stay competitive with steel, aluminum and thermoformed plastic parts," says Harper. His firm has developed several innovations, including Multiple Insert Tooling (MIT) RTM, and has helped popularize a process known as Light RTM (LRTM), providing training, tool design and ancillary accessories and equipment.
Radius manufactured the prototypes and the parts required for part certification; the actual production rate should be about 200 parts per year. The reduction in part count translated to cost savings that have offset the cost of the tooling development. The innovative tooling design was recognized as the award winner in the "Air Transport" category at the recent JEC Composites Show in Paris (April 1-3).
Arris presents mechanical testing results of an Arris-designed natural fiber thermoplastic composite in comparison to similarly produced glass and carbon fiber-based materials.
The Ren RP4040 material has a CTE roughly equivalent to aluminum with thermal transfer rates comparable to carbon/epoxy prepreg tooling, in contrast to some other products like tooling boards. In addition, even after cure, it can be rebonded and remachined, to easily accommodate design changes or mold repair. A sealant compatible with the epoxy resin system used in the part is required to ensure vacuum integrity. Burke says the LCTC system can save as much as 70 percent in overall mold material and fabrication time, compared to traditional methods.
Tier-1 aerostructures manufacturer Spirit AeroSystems developed an out-of-autoclave (OOA), one-shot resin infusion process to reduce weight, labor and fasteners for a multi-spar aircraft torque box.
Jetcam’s latest white paper explores the critical aspects of nesting in composites manufacturing, and strategies to balance material efficiency and kitting speed.
The tool, made with vacuum-cast and anodized M1 aluminum mold plate, has a top and bottom half with outer molding line (OML) machined into each half. Anodized aluminum was selected for its surface hardness and its low specific heat and high conductivity, which permits faster heating than steel. It also has good vacuum integrity and can withstand RTM resin injection pressures. The mold includes an inner set of six aluminum mandrels fixtured together at their ends to control their positions relative to each other and to the OML. The 3.6m/11.7-ft long by 0.6m/2.3-ft wide part was designed so that braided sock preforms, supplied by A&P Technology Inc. (Cincinnati, Ohio, U.S.A.), could be fitted over each mandrel to form the flap's internal spar webs. Above and below the spars, tackified carbon fabric from HexcelHexcel Composites (Dublin, Calif., U.S.A.) forms the upper and lower skins. The approximately ten-fold difference in coefficient of thermal expansion (CTE) between the aluminum mold and mandrels and the carbon part is actually a design benefit — aluminum's much greater shrinkage makes it easy to remove the mandrels after cool down.
GETTING A QUOTE WITH LK-MOULD IS FREE AND SIMPLE.
FIND MORE OF OUR SERVICES:
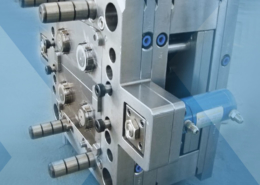
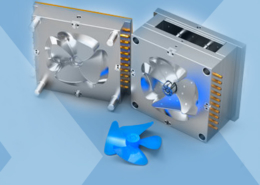
Plastic Molding

Rapid Prototyping
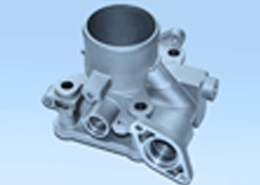
Pressure Die Casting
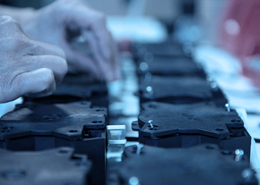
Parts Assembly
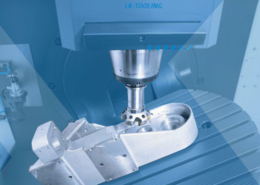