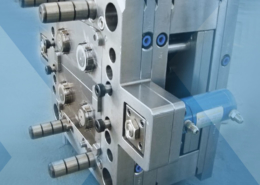
Molded-in-Color Parts Replace Metallic Paint on SUV Center Console Housing - abs
Author:gly Date: 2024-09-30
Until she retired in September 2021, Clare Goldsberry reported on the plastics industry for more than 30 years. In addition to the 10,000+ articles she has written, by her own estimation, she is the author of several books, including The Business of Injection Molding: How to succeed as a custom molder and Purchasing Injection Molds: A buyers guide. Goldsberry is a member of the Plastics Pioneers Association. She reflected on her long career in "Time to Say Good-Bye."
XLPE foam ducts boast several advantages compared to blow-molded, rigid PP ducts that are commonly used at present according to Illig. For example, ducts molded using XLPE foam (density of approximately 70 to 80 kg/m³ depending on the application) are not only substantially more lightweight than ducts made of solid PP (density of 900 kg/m³); among other properties they also possesses substantially lower heat conductivity and superior acoustic dampening behavior thanks to their foamed structure.
In twin-sheet thermoforming of cross-linked polyethylene (XLPE) foam, two sheets heated up to processing temperature are formed into half shells in the mold, supported by vacuum, and at the same time they are welded together on the outer contour. With the system developed by Illig; the formed parts are punched directly in the mold after the end of the cooling time. The upper mold half is equipped with extendible serrated knives. The lower mold half is equipped with grooves in which the knives interlock during punching. The punched out parts are secured by “holding bridges” and removed from the forming station. Upon removal from the thermoforming machine, only the joint areas of the air ducts have to be cut – just like blow-molded rigid ducts.
Lightweight and moreover flexible automotive air ducts are molded in sophisticated 3D geometries using XLPE foam and the thermoforming process on this Illig unit.
In the thermoforming process, XLPE sheet (thickness 3 to 4 mm) is supplied by two material roll stands and each material is heated up in the forming station to a surface temperature of up to 200 C. Subsequently the heater is rapidly removed from the forming station– in less than 3 seconds – in order to minimize cooling of the material prior to commencement of the forming process. Further, the servo drives for the upper and lower mold table are especially designed for rapid movement speeds of up to 500 mm/s, even for tools with a weight of up to 1 t per mold table.
In this way the foam’s lower heat conductivity minimizes condensation of water in the air duct after switching off the air conditioning system. High elasticity and good resilience of the ducts reportedly provide further benefits, such as ease of assembly and reduction of squeaking and rattling sounds even within a compact installation space.
A leading Spanish automotive supplier has put its third twin-sheet thermoforming line into operation for the manufacture of ducts for automobile air conditioning. The UAR 155g machine was supplied by Illig of Germany.
For moldmakers who wish they could simulate the molding process without having to build a prototype mold first, Sigmasoft software, designed for 3D injection molding process simulation, may be the answer. Using a completely 3D-approach and the integration of a highly developed thermal solver, the injection molding simulation software allows the calculation of multiple consecutive production cycles, considering the thermal interactions throughout all the components in the mold.
Sigma Plastic Services (Schaumburg, IL) highlighted this product at the recent NPE, where it says it was well received. The 3D-approach of Sigmasoft allows all the components in a mold, including all the thermal and physical properties of each one of them, to be reproduced. Therefore, the heat transfer process can be calculated between each one of the components.“In conventional injection molding software, a fixed mold temperature is defined, and the whole simulation is carried out under the assumption that this value remains constant over time,” explained Marco Thornagel, executive director of Sigma Engineering. “In reality, however, you have a very complex thermal process taking place within the mold: the steel is cooled with a tempering system, the mold is heated when the hot polymer melt enters the cavity and there is a loss of thermal energy towards the surrounding environment. All governed by the heat transfer properties of the materials present throughout the system: polymer melt, runner system, inserts, mold, isolation materials. Only when these complex interactions are considered, will the real production conditions be reproduced in the simulation. And our customers really appreciate that we already have 25 years of experience in how to make this kind of simulation, with a user friendly meshing algorithm,” observed Thornagel. To accurately simulate the production conditions, the heat transfer process taking place in reality must be exactly reproduced in the simulation. This includes the heat-up during the start-up of the machine, when the mold is heated from room temperature to its production conditions (typically between 60-120°C) by the tempering system. It also includes the warming up produced by the hot polymer melt over several consecutive pre-production cycles, as happens in actual run conditions. What differentiates Sigmasoft from other material flow software analysis is Sigmasoft’s ability to exactly reproduce processing conditions. The heat-up stage, as well as the thermal evolution of the mold over multiple consecutive production cycles. This accurate calculation predicts the real temperature in each location of the mold during production, producing a condition that more closely reflects reality for the polymer as it sets inside the cavity. This allows the software, for example, to predict how long the polymer remains in a fluid condition so that post-pressure can be applied, or where the thermally induced deformation will most likely compromise part quality. At NPE, PlasticsToday sat down with Christof Heisser, president of Sigma Plastic Services Inc., who explained, “Because no other software program can really simulate the actual molding conditions, mold designers throw it over the wall and the molder has to deal with it. It becomes a matter of trial and error. Yet, you can actually simulate in the virtual world for accurate, real-world results. We create the part, the cooling lines, and material temperatures to simulate actual molding conditions.”Another advantage of multi-cycle simulation, said the company, is the ability to calculate how many production cycles are required for the mold to achieve cyclic equilibrium—and thus consistent quality conditions over a production run. Therefore, the number of parts required before the actual production begins can be more accurately predicted. The system can be optimized to minimize the number of pre-production parts that are required. Another benefit is the ability to compare the efficiency of different tempering systems to understand how to achieve equilibrium more quickly or how to consume less energy. “Typically with other software programs, you can’t simulate the mold from the process side,” Heisser explains. “Usually these types of programs have only been used on the design side to make assumptions about the mold, but you can only look at the part because they are not capable of capturing the entire process. “Even those programs that can come close can only simulate certain aspects of the process, not what happens in the real production world. We’re the only one that can simulate every detail of the hot runner system, the needles, channels, etc. We go into that detail that is critical to every aspect of the molding process.” Heisser noted that the big issue for Sigma is that the minute someone says “simulation” they say moldmakers believe there is nothing applicable to them. “What we offer in Sigmasoft is virtual molding processing development,” he stated. “We simulate every volume of all the different components and assign properties to each of the components.”Because Sigma comes from the metal casting world – it’s a division of Magma Foundry Technolgies Inc. – Sigma has developed huge data bases of heat transfer data. Matt Proske, Applications Manager for Sigma Plastics Services, said, “We need to have temperature dependent physical properties of plastics and metal to know how it flows and solidifies. We spent 30 years measuring all these properties for metal properties at Magma, so if you leave the mold open and it gets too cold, you’ll see that in the simulation.“If you ask a molder how much a role mold temperature plays in the molding process, they’ll say ‘a lot.’ If you don’t know the mold temperature—the thermal gradient inside the mold, because the rate of heat transfer is driven by that temperature differential—if in a simulation you don’t have the mold temperature—you have to calculate it, and you can’t possibly get the right information,” Proske added. “With Sigmasoft, you can go through the entire cycle—from mold close to mold open—and all the heat transfer is calculated. By the end of first cycle the mold has a temperature—a thermal gradient—and some heat is released from the material to the mold steel. During the second cycle, the steel starts out the same temperature as it had at the end of the first cycle.”Heisser said that while this requires a lot of calculations it’s not a problem because that’s what the computer does. The solid model of the parts that the tool shop has already is loaded into the program, along with the starting temperature of the cooling medium, the cycle time and the injection temperature of the plastic. “The molder doesn’t have to sit there for days like in traditional simulation, and make or fix meshes,” said Heisser. “Just press a button and the computer prepares the entire simulation. You just decide the same things you’d decide as if you were actually processing the part.” Certainly processing knowledge is needed but Heisser said this is a tool that can be put in the engineering department of a molder. “You don’t need an analyst, you just need people who understand the process rather than people who know how to run simulation,” he stressed. “Other tools need finite element meshing specialists. We made a simulation tool—a virtual mold/process development tool for engineers.”
For moldmakers who wish they could simulate the molding process without having to build a prototype mold first, Sigmasoft software, designed for 3D injection molding process simulation, may be the answer. Using a completely 3D-approach and the integration of a highly developed thermal solver, the injection molding simulation software allows the calculation of multiple consecutive production cycles, considering the thermal interactions throughout all the components in the mold. The accuracy of the entire simulation is thus dramatically increased.
A further benefit provided by thermoforming with twin-sheet technology versus extrusion blow molding is that multiple parts of differing dimensions and geometries can be manufactured simultaneously by utilizing a large-area tool (the UAR 155g features a forming area of up to 1450 x 1200 mm). This capability also has implication in terms of cycle time per air duct, which is naturally shorter. On these accounts, air ducts made of foam are cost competitive when compared with rigid PP blow-molded ducts– manufacturing costs per duct are in fact comparable.
GETTING A QUOTE WITH LK-MOULD IS FREE AND SIMPLE.
FIND MORE OF OUR SERVICES:
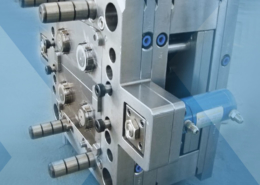
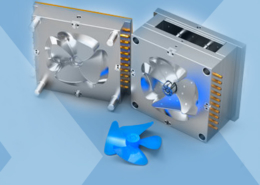
Plastic Molding

Rapid Prototyping
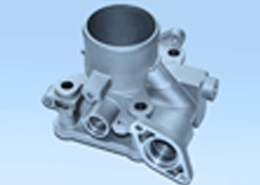
Pressure Die Casting
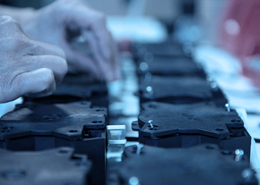
Parts Assembly
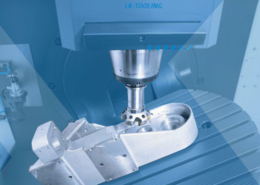