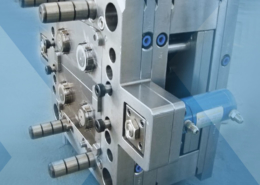
Mold Shuttle System Can Double Injection Molding Capacity - multi mold plastics
Author:gly Date: 2024-09-30
The alumina powder and binders were mixed in a kneader for 1 h at 180°C with powder loading of 47, 50, and 52 vol.%. Viscosity measurements were performed on the feedstock compounds obtained to investigate their rheological behaviour. The authors stated that it was possible to select the powder loading and binder composition according to the viscosity of the sample. In particular, PP has higher strength and lower viscosity than LDPE and HDPE, which they suggest gives it advantages when used to produce artificial bone material from alumina.
Leveraging a strong history in developing novel reverse logistics strategies, Ultra-Poly collects the used bumper covers directly from auto body shops, where they have been removed from vehicles and stripped of any usable connected components. The program offers a strong value to the shops, including;
End-of-life car bumpers are converted into a raw material that is used in the production of new chassis vibration- and noise-attenuation components.
The resulting material offers strong value to converters and brand owners as well, including a consistent high-quality material with a balance of stiffness and toughness, and certified 100% post-consumer content.
Discover suppliers of these and more in our advertisers’ index and buyer’s guide, available in the back of PIM International.
Industry integrity – the used fascia are completely destroyed in the process and cannot be repaired and make their way back into the supply stream, which presents significant quality issues.
Extensive MIM, CIM industry and sinter-based AM industry news, plus the following exclusive deep-dive articles and reports:
Don't miss any new issue of PIM International, and stay up to date with the latest industry news. Sign up to our fortnightly newsletter.
“This is a groundbreaking program that will help advance the automotive industry closer to achieving the standards of a circular economy,” said Kevin Cronin, vice president of sustainability and R&D at Ultra-Poly. “Sustainability is in the DNA of Ultra-Poly. Our commitment and expertise in improving the sustainability of the plastics industry is evident throughout our business model and we look forward to all that we can achieve with this innovative program.”
The free-to-access PIM International magazine archive offers unparalleled insight into the world of MIM, CIM and sinter-based AM from a commercial and technological perspective through:
Reach a truly international audience that includes component manufacturers, end-users, industry suppliers, analysts, researchers and more.
Autoneum North America Inc. Vice President of Product Development and Engineering, Dan Moler, added: “With the increasing challenge of OEMs to require more and more recycled content, this product delivers on that challenge, enabling us to become more sustainable as a company by reducing our carbon footprint and engineering a product from the ground up with end-of-life recycling in mind to ultimately reach the end goal of a circular economy. Everyone benefits — body shops, recyclers, automotive part manufacturers, OEMs and, most importantly, the environment.”
As a member of the Plastics Industry Association, the company was one of several that worked on the End-of-Life Vehicle (ELV) project, which sought to determine if the fascia material could be recovered for use in new fascia. Ultimately, this was deemed not viable, primarily because of surface finish issues. However, Ultra-Poly saw potential for the material in other polypropylene compounds as well as in non-appearance applications in the automotive and other industrial markets.
The recycled material is now available to be sampled and used by any automotive manufacturer or supplier for other potential programs.
The authors used alumina (Al2O3) powder, to which was added the binder comprising polyacetal (POM) and polyolefin (PO), three types of polypropylene (PP) with different melt flow rates, low-density polyethylene (LDPE) and high-density polyethylene (HDPE)), paraffin wax (PW), fatty acid amide, and an antioxidant. POM and PO acted as the backbone polymers. Powder loading and binder composition are shown in Table 1.
Bioceramics is a class of materials that have found use as artificial bone materials for repairing or replacing damaged bone tissue because of their excellent biocompatibility and mechanical properties. Bioceramics can also directly interact with the surrounding tissue, either supporting tissue growth or inducing new tissue regeneration. In many biomedical applications, bioceramics such as alumina must often be fabricated to a specific and often complex shape such as artificial hip joints, artificial knee joints, bone screws, maxillofacial reconstruction, dental implants, etc. Alumina oxide is a bioinert material with excellent biocompatibility and mechanical properties, but its high hardness and brittleness make it difficult and costly to machine to the highly complex and precision shapes often required in artificial bone replacements.
Research at the Department of Mechanical Systems Engineering, Tokyo Metropolitan University, Japan, has been focused on Ceramic Injection Moulding to produce alumina artificial bone material and, in particular, the research has investigated the effects of CIM conditions, such as alumina powder loading and binder composition and content in the CIM feedstock, in order to control the porosity, grain size and mechanical properties of the sintered CIM alumina material. A paper by T Osada, Y Nagai, and S Kobayashi, recently published in Open Ceramics (Vol. 13, 2023, 100328, 7pp) entitled: ‘Fabrication and mechanical characterization of biocompatible oxide ceramic parts by injection molding’, outlined the results of their research. The authors stated that it is possible to control the density of CIM alumina parts by controlling the binder components and amount of binder added, or adjusting the powder loading. Even if the obtained bending strength of the CIM alumina parts decreased slightly with increasing porosity, they stated it was still found to be sufficient for use as artificial bone material.
Porosity of the sintered CIM alumina parts could be modified by changing the powder loading and porosity could also be increased when needed by increasing the backbone polymer content. Higher powder loading was found to show larger grain sizes in sintered alumina, whereas parts with lower powder loading showed smaller grain size and higher porosity. Bending tests showed fracture occurring along the grain boundaries. The bending strengths of the CIM alumina specimens showed that they were sufficient for use as artificial bone material.
The authors reported that the higher viscosity of PP, which has the higher bending strength, makes this binder more suitable when the green CIM parts need to be machined before sintering. The bending strength of LDPE specimens increased with increasing POM and LDPE content. The authors suggested that the molecular weight or content of the backbone polymer affected the strength of green CIM alumina compacts.
There has been a significant increase over the past fifty years in the number of elderly people in the global population, which in turn has led to the need to raise awareness of osteoporosis caused by ageing and the growing demand for artificial bone materials as bones become more fragile and fracture and require to be repaired or replaced.
Ultra-Poly, one of America's largest plastics recyclers, has announced a first-of-its-kind bumper recycling program, that involves the collection and reprocessing of damaged automotive bumpers into a new raw material for use in an auto component. Ultra-Poly collaborated with Tier 1 Autoneum North America to develop a product that uses the recycled bumper material as a rigid backing substrate for a fibrous layer, creating a composite used in vibration and noise attenuation in a chassis component. The material is listed in the International Material Data System (IMDS).
The alumina feedstock was injection moulded into tensile bar shaped specimens. It was established that the optimum conditions for CIM of the alumina feedstock are 50–52 vol.% powder loading or 30–40 mass% in POM/PP and POM/PE in the binder composition. Bending strength was measured on both the green and sintered CIM alumina parts. Fig. 1 shows the relationship between relative density and bending strength in sintered samples, depending on the effect of powder loading, and Fig. 2 shows the same relationship, depending on the different binder compositions used.
Ceramic Injection Moulding is a manufacturing process which can meet many of the requirements for complex geometries and high precision alumina components for artificial bone materials and, where necessary, the alumina parts can be easily machined to the required shape in the green state after injection moulding and prior to sintering. This can result in low-cost custom-made alumina artificial bone structures that match the exact shape of the defective bone being replaced. The CIM alumina parts can also be produced with some porosity to allow cell ingrowth and tissue regeneration.
GETTING A QUOTE WITH LK-MOULD IS FREE AND SIMPLE.
FIND MORE OF OUR SERVICES:
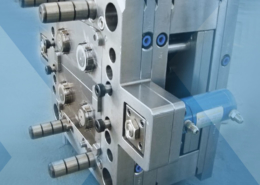
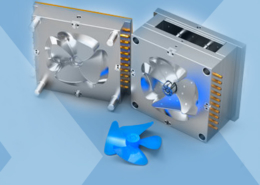
Plastic Molding

Rapid Prototyping
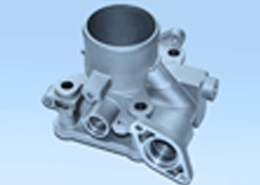
Pressure Die Casting
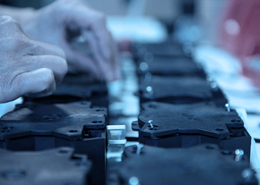
Parts Assembly
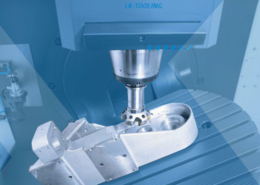