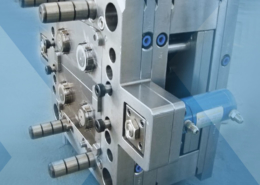
Industrial Injection Molding: Revolutionizing Manufacturing Processes
Author:gly Date: 2024-06-08
Industrial injection molding stands at the forefront of modern manufacturing, revolutionizing the production of intricate plastic components across diverse industries. This article aims to delve into the intricacies of industrial injection molding, exploring its mechanisms, applications, innovations, and environmental implications.
Understanding the Process
Industrial injection molding involves the transformation of raw plastic materials into complex shapes through the application of heat and pressure. The process begins with the feeding of plastic pellets into a heated barrel, where they are melted and mixed. The molten plastic is then injected into a mold cavity under high pressure, where it cools and solidifies into the desired shape.
This process offers unparalleled precision and efficiency, allowing for the mass production of intricate components with minimal waste. From automotive parts to medical devices, industrial injection molding has become indispensable in various sectors.
Advancements in Material Science
The evolution of industrial injection molding has been closely tied to advancements in material science. Engineers and researchers continually explore new materials with enhanced properties, such as strength, flexibility, and heat resistance, to meet the demands of modern applications.
Biodegradable polymers, reinforced composites, and high-performance thermoplastics are just a few examples of materials pushing the boundaries of industrial injection molding. These innovations not only improve product performance but also address sustainability concerns by reducing environmental impact.
Precision Engineering and Design
The success of industrial injection molding relies heavily on precision engineering and design. Mold designers utilize advanced software and simulation tools to optimize mold geometries, cooling systems, and gating configurations, ensuring uniformity and consistency in the final products.
Furthermore, the integration of automation and robotics streamlines the manufacturing process, increasing productivity and reducing labor costs. With computer-controlled systems overseeing every stage, from material preparation to quality inspection, manufacturers can achieve unparalleled levels of efficiency and reliability.
Quality Control and Assurance
Maintaining stringent quality control standards is paramount in industrial injection molding. Real-time monitoring systems track key parameters, such as temperature, pressure, and cycle times, to detect any deviations or defects during production.
Additionally, comprehensive testing protocols, including dimensional analysis, mechanical testing, and visual inspection, validate the integrity of the molded components. By identifying and rectifying issues early in the process, manufacturers can uphold quality standards and meet customer expectations consistently.
Environmental Sustainability
As the global focus on environmental sustainability intensifies, industrial injection molding plays a pivotal role in reducing waste and energy consumption. Recycling initiatives, waste minimization strategies, and eco-friendly materials contribute to a more sustainable manufacturing ecosystem.
Furthermore, advancements in energy-efficient machinery and processes help minimize the carbon footprint of industrial injection molding operations. By embracing green technologies and practices, manufacturers can mitigate environmental impact while maintaining competitiveness in the market.
Challenges and Future Outlook
Despite its numerous benefits, industrial injection molding faces several challenges, including rising material costs, geopolitical uncertainties, and regulatory pressures. Additionally, the complexity of molding high-performance materials poses technical and logistical challenges for manufacturers.
Looking ahead, the future of industrial injection molding lies in innovation and collaboration across disciplines. Research into advanced materials, additive manufacturing techniques, and intelligent automation holds the key to unlocking new possibilities and driving industry growth.
In conclusion, industrial injection molding stands as a cornerstone of modern manufacturing, driving innovation, efficiency, and sustainability across diverse industries. By embracing technological advancements and fostering collaboration, the industry can navigate challenges and pave the way for a brighter, more resilient future.
GETTING A QUOTE WITH LK-MOULD IS FREE AND SIMPLE.
FIND MORE OF OUR SERVICES:
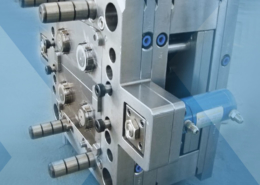
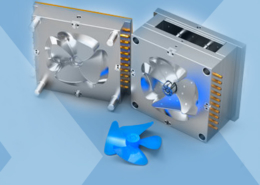
Plastic Molding

Rapid Prototyping
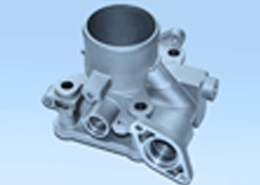
Pressure Die Casting
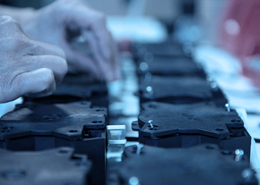
Parts Assembly
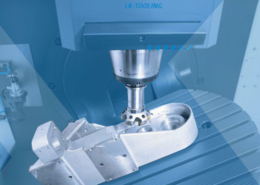