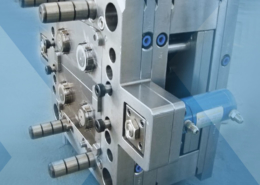
Mitsubishi Chemical to launch Freeform Injection Molding services across
Author:gly Date: 2024-09-30
Previous efforts in motorsports tooling would often include the production of a foam master model followed by a composite mold to be used only to make a limited number of parts. After their use, both the foam master and composite mold would be discarded. Combating this, Airtech’s team of experts has created a sustainable approach for producing 3D printed composite mold tools – made from an energy-intensive, engineering-grade, recyclable thermoplastic. This approach removes the need for a master mold and saves time, energy, and waste.
I mean variable geometry extrusion: As example (Flashing light warning!;P) https://inv.bp.projectsegfau.lt/watch?v=VRC59iJjOwk
3D printing and mass production shouldn’t be in one sentence. Unless we combine efficient industrial warm/hot extrusion with robotic arm. Why extrude just one layer if you can extrude entire surface in liquid and/or conveyor belt?
Airtech will also display its Aircraft Fairing Vacuum Trimming Fixture, 3D printed using Dahltram C-250GF, in the JEC Innovation Planet Mobility area, in Hall 6. As a partner of the EmpowerAX project, Airtech won the JEC Award 2024 in the ‘Aerospace Processes’ category. As part of a team of AM experts, the company used its expertise in material consultation and supply of short fiber-reinforced, high-performance polymer Dahltram I-350CF to realize this project. The EmpowerAX Demo Part realized by DLR and the other 12 partners will be displayed at Weber’s booth #P138 in hall 5.
He has some good points but it’s a very hard “3D printing is the only future and you’re a morno if you think otherwise” vibe.
This is what there print farm looks like. They should change the picture https://static.wixstatic.com/media/fc79c8_7357ffbb11134fbf92d74c6c3ff2c47e~mv2.jpg/v1/fill/w_2592,h_1728,al_c,q_90/fc79c8_7357ffbb11134fbf92d74c6c3ff2c47e~mv2.webp
Partners printing live with Airtech materials at JEC include Belotti, printing with Dahltram C-250CF 6G61; Caracol, printing with Dahltram C-250CF – 5L116; CEAD, printing with Dahltram C-250CF – 5Q58; CMS, printing with Dahltram C-150CF – 5N58; Multiax, printing with Dahltram T-100GF – 5M88; and Thermwood, printing with Dahltram I-350 – 6P52.
I often points he made incisive as we often don’t design with 3d printing in mind. But you don’t make any valid argument against his opinion except that his degree. George, you can do better than that. This isn’t YouTube comments.
We’ll take a wild guess and say that right now, within arm’s length of wherever you’re reading this, there’s something that was produced by injection molding. Look around; it’s there someplace, and whatever it is, thousands or perhaps millions of other identical artifacts were produced along with it, all by squeezing hot plastic into intricately machined metal tools.
This obviously has his bias in 3d printing. But how is it got to do with his degree. Having it doesn’t make this opinions valid or vice versa.
By using our website and services, you expressly agree to the placement of our performance, functionality and advertising cookies. Learn more
I’m sorry – but this guy is 99.99% sales man – the HAD writer setting this up is being taken for a ride. THe guy owns a huge print farm, and all his videos on youtube have this weird/angry/aggressive vibe about how his way of designing things are so much better for the world, and you must adapt to his ways or else..(his way just happens to be better for 3d printing – surprise, surprise) While you have him chatting, please ask where he got his engineering degree – he likes to dodge that question, but claim he is one.
In collaboration with Oak Ridge National Lab (ORNL), Airtech utilized its advanced 3D printing materials and techniques, and grinding and reprocessing capabilities, to bring The Brumos Collection’s vision to life. The result was the production of a new high-temperature mold for a carbon-fiber aerodynamic splitter that diverts air under the car – increasing aerodynamic downforce.
Fun fact: The head picture is from Prusa’s farm in Prague, Czechia: https://stock.adobe.com/it/images/prusa-research-3d-printing-farm-in-prague-czech-republic/301117847 I thought Slant 3D use their own, not Prusa :-)
1,346 polymer and metal AM companies and 143 end-users. Consumer products AM generated $2.6 billion in 2023. Segment expected to grow to $28 billion by 2033 at 26.8% CAGR. This new market study fro...
The new mold successfully produced an improved splitter – generating more downforce and giving the car better traction and stability to navigate the mountain’s sharp turns, at more than 140mph. All of this was done at a fraction of the cost, with a fraction of the environmental impact.
In November 2023, at Formnext, the company launched the new Dahltram T-100GF resin, its first recycled grade thermoplastic polymer resin for pellet-fed, large-scale 3D printing.
But does that mean that medium-sized runs of parts are out of luck? Not at all! Gabe Bentz, founder and CEO of Slant 3D, is passionate about filling the manufacturing void where injection molding is prohibitive, either by virtue of start-up costs or because the part design is just not possible to manufacture. His massive print farms are busy day in and day out cranking out parts for customers that otherwise couldn’t be made. So if you’ve ever wondered what it takes to run a print farm, and what kinds of design considerations make a part a candidate for mass production by 3D printing, drop by the chat and we’ll see what he has to tell us.
When you visit any web site, it may store or retrieve information on your browser, mostly in the form of cookies. Control your personal Cookie Services here.
Airtech will continue to develop, test, and validate future sustainable solutions to expand the performance envelope for additively manufactured tools – both from an innovative design perspective as well as to improve the mechanical performance of the Dahltram resin system to increase the appeal of 3D printing compared to traditional tooling approaches.
Our Hack Chats are live community events in the Hackaday.io Hack Chat group messaging. This week we’ll be sitting down on Wednesday, August 23 at 12:00 PM Pacific time. If time zones have you tied up, we have a handy time zone converter.
NEWS FLASH! CEO of 3D printing company says 3D printing is a good way to do things! More on this shocking and unprecedented revelation at 11!
Airtech Advanced Material Group has recently played a pivotal role in enhancing the Brumos Collection’s Porsche GT2 RS Clubsport for 2023’s Pikes Peak International Hill Climb race. In support of this program, it provided all essential materials – leveraging its technical expertise and design support. Thanks to the company’s multiple cross-industry partnerships – and its Dahltram C-250CF Polycarbonate, carbon fiber-reinforced material made from recycled tooling waste – it has demonstrated the circular lifecycle capabilities for 3D printed tooling. The Brumos Racing mold will be on display at this year’s JEC, at booth #G41 in hall 5.
It’s HAD – the comments are worse :) But you’re trying to conflate the two topics I mentioned – I never said there was a connection – that mistake is on you.
It’s not much of an overstatement to say that, for good or for ill, the world is made from injection-molded plastic. But not every product can support the often considerable up-front costs associated with injection molding. The tooling needed is often remarkably complicated and correspondingly expensive, and running the machines that actually do the molding is expensive and highly specialized. Unless you’re committed to making a lot of parts, injection molding might just be out of your league.
The result of this development was an exciting race at the Pikes Peak International Hill Climb where The Brumos Collection and their esteemed driver, David Donohue, raced to the top of Pikes Peak in a record-breaking 9:18:053 – securing the win in his class (time attack 1). This win is a prime example of the potential of 3D printing to enable a circular economy in which materials from a variety of clean energy applications are reused multiple times over – with enhanced efficiency and performance.
GETTING A QUOTE WITH LK-MOULD IS FREE AND SIMPLE.
FIND MORE OF OUR SERVICES:
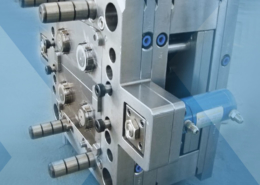
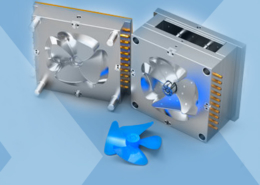
Plastic Molding

Rapid Prototyping
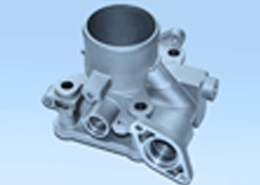
Pressure Die Casting
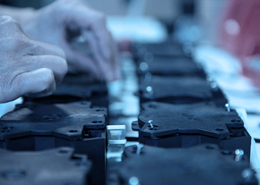
Parts Assembly
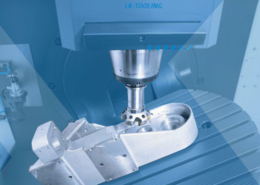