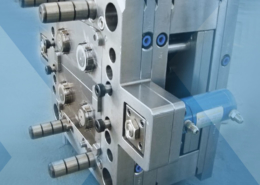
MIM used to produce hollow sphere reinforced aluminium matrix foam parts - injec
Author:gly Date: 2024-09-30
During in-mold labeling, a label is inserted into the thermoforming mold that shapes the product and forms a solid bond with the finished product. Shaping and decoration are performed in a single, efficient process.
In addition, the cup and label are made of polypropylene (PP), a mono-material construction that is very easy to recycle. Mono-material solutions also are possible with PET, Eisenhuber told PlasticsToday.
“At Greiner Packaging, we are committed to a circular economy and want to take a broad-based approach to making that happen,” Maurer added. “With our new T-IML cups using less material and being readily recyclable, they encapsulate exactly what we hoped to achieve.”
“We merged our cutting-edge tech to Huarong’s existing and functioning clamping unit, and the result is a compact, hassle-free, plug-and-play machine for Dry Molded Fiber manufacturing.”
Greiner Packaging has developed a technique for thermoforming cups with in-mold labels (IML) that requires less material, is lighter in weight, and is more recyclable than similar IML cups produced via injection molding.
When possible, Greinier Packaging tries to use recycled material, although the use of mechanically recycled material for food applications is limited because of strict approval criteria. Currently, only rPET meets those requirements.
IML typically is used in combination with injection molding technology. The thermoformed IML cups are more sustainable by several measures, according to Philipp Maurer, Key Account Manager at Greiner Packaging. Less plastic is required to produce thermoformed cups, which saves resources and makes the cups lighter and less costly to transfer. This requires fewer carbon dioxide emissions during transport.
“When we launched Dry Molded Fiber a few years ago, we did it with a great machine platform,” explains Sanna Fager, chief commercial officer at PulPac. “The PulPac Modula is still the best fit for producers with high volumes and a need for modularity. But one size doesn’t fit all, and we saw an opportunity to make Dry Molded Fiber approachable to even more packaging producers.
Approximately 100,000 injection moulding machines are produced every year, PulPac says, and many of them only produce single-use plastic. The PulPac Scala seeks to rectify this – bringing Dry Molded Fiber to customers and requiring a lower investment than the PulPac Modula while fitting into a 40-foot container.
PulPac is launching the PulPac Scala, a new machine platform combining its Mill-to-Web fibre unit with injection moulding technology, in the hopes of increasing the accessibility of Dry Molded Fiber worldwide.
Alongside its turnkey partner Huarong Group, PulPac is now releasing the compact, reportedly scalable Dry Molded Fiber machine platform. The fibre-forming technology claims to offer efficiency in resources, energy, and cost and hopes to overtake single-use plastic consumption globally.
“Its name is, of course, a play on words. Due to its low investment threshold, any producer who wants to gain market leverage in this new, exciting, and fast-growing market can start small and then scale up.”
After investing in a test mold, Greiner Packaging is able to manufacture 500-milliliter thermoformed IML (T-IML) cups with a diameter of 95 millimeters. By switching from injection molding to thermoforming, the cup’s weight was reduced from 15 to 11.4 grams, a 25% reduction, Eisenhuber said.
T- IML is an especially high-quality form of packaging decoration, the company said. Matte, rough, glossy, or soft-touch decorative effects can be applied, and the printed content is photo quality and “visually outstanding,” Maurer said. “IML packaging solutions are extremely effective at attracting consumers’ attention at the point of sale.
In addition, the sheet used in the thermoforming process to make the cup can be embedded with barrier properties, which can extend the shelf life of packaged food and help reduce food waste, according to Sebastian Eisenhuber, Global Product Group Manager.
SustainaPac LLC also joined PulPac’s licensee network and sought to use Dry Molded Fiber technology to produce single-use food service packaging products for the North American quick service restaurant market.
“Greiner Packaging offers various barrier solutions, which increase protection against oxygen or light and, thus, make food last longer,” Eisenhuber told PlasticsToday. “Our barrier solution of choice is a PP-EVOH-PP combination, which we call multi-barrier technology (MBT). It is hard to make a general statement about how barrier solutions will extend the shelf life of a product," Eisenhuber adds, “as this depends on many factors other than the packaging – such as the filling conditions and the type of filling itself.”
Greiner Packaging’s thermoformed cups with in-mold labels (IML) use less material, are lighter in weight, and easier to recycle than their injection molded counterparts.
The company will develop packaging solutions based on the individual needs of its customers to achieve the best protection for its customers’ goods, Eisenhuber said.
Greiner Packaging is a leading European manufacturer of plastic packaging in the food and nonfood sectors. Its two business units include Packaging and Assistec. The Packaging unit focuses on packaging solutions and the Assistec unit is dedicated to producing custom technical parts. Greiner Packaging employs a workforce of almost 4,900 at more than 30 locations in 19 countries worldwide. In 2020, the company generated annual sales revenue of €692 million ($783 million), including joint ventures, which represents approximately 35% of Greiner’s total sales.
Viktor Börjesson, PulPac’s chief partnerships officer, continues: “As the inventors of Dry Molded Fiber, our knowledge about the technology is unrivaled. Huarong brings 40 years of experience in building machines for the plastic industry.
Bruce Adams is an experienced content creator and trade publishing veteran who has written extensively about the plastics, automotive aftermarket, hospitality, tire, rubber, mining, and construction industries.
Earlier this year, Curt G. Joa, Inc. (JOA) worked with PulPac to bring the PulPac Modula production platform for Dry Molded Fiber to the North American market – aiming to meet growing demand for sustainable packaging solutions.
GETTING A QUOTE WITH LK-MOULD IS FREE AND SIMPLE.
FIND MORE OF OUR SERVICES:
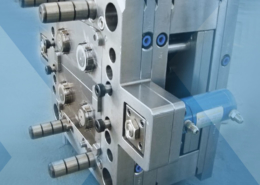
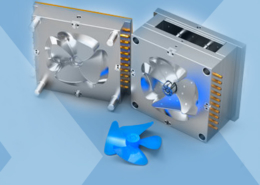
Plastic Molding

Rapid Prototyping
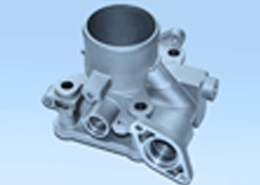
Pressure Die Casting
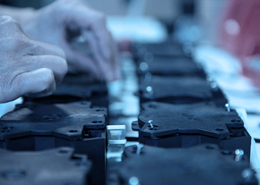
Parts Assembly
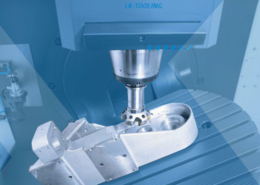