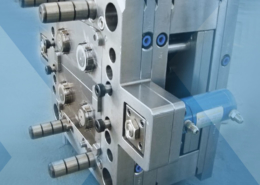
Milacron’s Mold-Masters completes facility expansion in China - milacron injecti
Author:gly Date: 2024-09-30
Additive Manufacturing technologies offer superior design possibilities compared to conventional manufacturing processes; however, residual stresses and the need for support structures add restrictions to the freedom of design when using AM technologies such as LB-PBF.
Maximilian Munsch, Matthias Schmidt-Lehr and Eric WyciskAmpower GmbH & Co. KG ZAL TechCenterHein-Sass-Weg 22 21129 Hamburg Germany
Prepreg co-molding compound by IDI Composites International and A&P Technology enables new geometries and levels of strength and resiliency for automotive, mobility.
Base Materials introduces a high-performance, toughened epoxy tooling board designed for thermoforming and vacuum forming processes, direct-to-part applications and more.
CW’s editors are tracking the latest trends and developments in tooling, from the basics to new developments. This collection, presented by Composites One, features four recent CW stories that detail a range of tooling technologies, processes and materials.
To minimise the influence of sintering temperature and other process-related factors on the mechanical properties, and to increase the comparability of processes, all specimens were additionally heat treated after sintering in identical cycles. All specimens were solution treated at 1040°C for 1 h in a vacuum. The 17-4PH specimens were additionally hardened to H1025 at 550°C for 4 h in atmosphere. Figs. 9-10 show the resulting hardness measurements. It is evident from these results that sinter-based AM technologies achieve values close to the requirements for metal injection moulded materials as defined in ISO 22068 for 316L, and exceed the standard value for H1025 hardened 17-4PH.
The production cost for the series production of the AM demonstration part (Fig. 1) has been calculated by the production speed in cm³/h and machine hourly rate for the respective AM system (Fig.12). Additional costs from any necessary mechanical post-processes as well as inspection efforts for quality assurance are excluded.
The future of Additive Manufacturing lies in part production at scale. Innovation must, therefore, focus on how to reduce part cost and improve per...»
For metal FDM systems, the cost for investment, maintenance and consumables is considerably lower. Focusing only on the build process, machine cost ranges between €60,000–100,000 resulting in hourly rates of €5–8.
Program will focus on sustainable, next-gen wing solutions, including in wing design and manufacturing and advancements in carbon fiber-reinforced composite materials.
CompositesWorld’s Tech Days: Design, Simulation and Testing Technologies for Next-Gen Composite Structures is designed to provide a multi-perspective view of the state of the art in design, simulation, failure analysis, digital twins, virtual testing and virtual inspection.
This session is designed to demonstrate the benefits of ultra polymers for aerospace applications with real case examples of Syensqo's polymer portfolio. Agenda: Introduction to ultra polymers (PAEK, PEKK, PEEK, PAI) key features Application of ultra polymers in aerospace: concrete examples Benefits of ultra polymers: enhanced performance, durability and cost-efficiency
As of today, there are at least eleven major metal Additive Manufacturing technologies. Each technology has its specific advantages and limitations regarding part design, mechanical properties and costs. This leads to ever more complex decisions when it comes to the choice of technology for a given application.
Analysis shows that LB-PBF production speed mainly depends on the number of lasers working in parallel in the build chamber. Based on the mentioned hourly rate, the resulting cost per volume varies between €1-3 per cm³ for stainless steel. For metal FDM, the layer thickness is the key factor to increase the build volume per time. By increasing this parameter, the production rate increases but also leads to a significant reduction in resolution and surface quality. As previously mentioned, the cost of feedstock also varies depending on the system. Taking these parameters into account, the resulting cost for stainless steel is estimated to be between €0.5 and €2.5 per cm³.
Binder Jetting is based on an MIT-developed technology which originally focused on sand casting forms. After its initial development, ExOne developed the first metal process based on Binder Jetting, with Höganäs’s Digital Metal following with its own system. Desktop Metal is currently publicising its binder jet-based Production System and, in September 2018, HP unveiled its first binder jet metal AM system.
We expect existing electron and laser beam PBF system manufacturers to further focus on demanding, high-end markets such as medical and aviation industry. The superior material properties and a high technology readiness level of PBF systems will also keep binder technologies at a distance in these high-end sectors. Mass markets such as automotive, however, will gradually shift their focus from LB-PBF to Binder Jetting. The prototyping and tooling market will quickly adapt to the cost potentials of metal FDM.
Increasingly, prototype and production-ready smart devices featuring thermoplastic composite cases and other components provide lightweight, optimized sustainable alternatives to metal.
Over the last 8 months, Archer Aviation has completed a total of 402 test flights with its composites-intensive aircraft, adding to key milestones.
Initial demonstration in furniture shows properties two to nine times higher than plywood, OOA molding for uniquely shaped components.
Reach a truly international audience that includes component manufacturers, end-users, industry suppliers, analysts, researchers and more.
Advanced Engineering is the UK’s largest annual gathering of engineering and manufacturing professionals. The event will help you to source new suppliers, network, build connections and learn about the latest industry developments all in one place. Get involved and exhibit alongside 400+ exhibitors offering solutions and products across all industries and sectors to help improve your productivity and inspire creativity. With over 9,000+ of your peers due to attend and ready to network with and inspire you, this is the event you can’t afford to miss!
CompositesWorld’s CW Tech Days: Infrastructure event offers a series of expert presentations on composite materials, processes and applications that should and will be considered for use in the infrastructure and construction markets.
Jetcam’s latest white paper explores the critical aspects of nesting in composites manufacturing, and strategies to balance material efficiency and kitting speed.
This collection features detail the current state of the industry and recent success stories across aerospace, automotive and rail applications.
The new space race is powered by metal Additive Manufacturing. In turn, the Additive Manufacturing of rocket engines is powered by advanced alloys....»
In the case of LB-PBF, metal Additive Manufacturing is characterised by high machine cost, low production speed and high material cost. Thus, not every part that is technically feasible is financially viable. Sinter-based metal AM technologies promise to change this and lower the cost for metal AM parts significantly.
This report is based on a forthcoming publicly available study that offers a detailed look into these new metal AM technologies. The full study will be available through www.am-power.de.
Reliable news and information on where and how fiber-reinforced composites are being applied — that’s just the start of what you get from our team here at CompositesWorld.
While Binder Jetting requires no supports during the build process, the sintering step may require additional supports to prevent deformation of the part. An alternative can be achieved by using ceramic ‘setters’ that hold the component in place and support areas that are prone to deform during sintering. This would require higher production volumes to amortise the associated costs.
Six U.S. companies have proven their recycling technologies for composites and rare earth elements, and will be supported for relevant scale demonstration and validation.
The composites-intensive VTOL platform is next expected to undergo a series of test flights in various conditions to validate its performance, safety and reliability, leading up to eventual certification.
Discover suppliers of these and more in our comprehensive advertisers’ index and buyer’s guide, available in the back of Metal AM magazine.
As of today, 17-4PH and 316L stainless steel are readily available for Binder Jetting and metal FDM technologies. Digital Metal also offers parts in titanium alloy Ti-6Al-4V. In principle, all known MIM alloys can be used for sinter-based AM technologies. Copper and carbide materials pose particularly interesting opportunities for future applications, since they have certain limitations in LB-PBF. On the other hand, aluminium alloys will remain challenging for the new Additive Manufacturing processes due to the difficulty of sintering aluminium.
Binder Jetting systems which offer comparable build envelopes in the range of edge lengths of 300 mm have similar investment cost covering only the part build process, excluding the debinding and sintering systems. Additionally, costs for consumables and maintenance have little impact in both technologies which results in similar machine hourly rates for Binder Jetting. Future Binder Jetting machines are expected to carry an even higher investment cost of around €1 million, excluding debinding and sintering, but promise a further increase in productivity.
CompositesWorld's Carbon Fiber conference offers you cutting-edge information and access to industry experts in streamlining manufacturing costs, market outlooks and forecasting, and more. You will make invaluable contacts as you meet and network with the industry's most innovative and influential leaders at Carbon Fiber. __PRESENT
The free to access Metal Additive Manufacturing magazine archive offers unparalleled insight into the world of metal Additive Manufacturing from a commercial and technological perspective through:
Tom Zozokos is the director of technology for advanced composites at Trelleborg Sealing Solutions, focused on developing solutions for a wide range of market segments using composites technology. He has worked for Trelleborg for the last 14 years in a variety of roles including: design engineering for thermoset composite products, new business development within thermoplastic injection molding technology, and global product management for bearings, bushings and guides. tom has a bachelor's degree from Princeton University in mechanical and aerospace engineering and currently lives in Chicago, Illinois.
The aim of the investigation has been to determine the technology readiness level of Binder Jetting and metal Fusion Deposition Modelling (FDM), as well as identify the potential and limitations of these technologies when compared to Metal Injection Moulding and LB-PBF. Whilst the complete report based on the investigation will give a more detailed look into these new metal AM technologies, this article presents key findings that will help guide prospective users to identify the right technology for a specific application.
In these sessions, experts will discuss the emerging hydrogen economy and the opportunities for composites in this lucrative space.
The typical investment for a twin laser LB-PBF system is around €500,000 and the depreciation and consumables add up to an average hourly machine rate of €30-40. Single laser systems are at the lower end of this range while the newest quad laser systems cost up to €55 per hour.
Gabriel Benarroch is a product sales engineer at Trelleborg Sealing Solutions in Albany. He has a dual bachelor’s degree in aeronautical engineering and mechanical engineering from Rensselaer Polytechnic Institute. He has six years of experience at Trelleborg working with aerospace customers on novel automated fiber placement applications.
Classification of the different melting/fusion technologies can be accomplished by distinguishing the material deposition method (direct or powder bed) and the energy source:
The technology map shown in Fig. 2 aims to classify these different metal AM technologies whilst taking the ISO/ASTM 52900 standard into account. Most of the processes can be classified into melting or binder-based sintering technologies. While sintering always comes with a binder component and a two-step manufacturing process, melting technologies use powder or wire in a single-step process to directly produce the part.
How the predictive tool “CZone” is applied to simulate the axial crushing response of composites, providing valuable insights into their use for motorsport applications.
Thermoplastics for Large Structures, experts explored the materials and processing technologies that are enabling the transition to large-part manufacturing.
The ITHEC 2024 will take place from the 9 to 10 October 2024 in Bremen, Germany. At the 7th International Conference, more than 300 participants from around the world will be presenting and discussing newest scientific results, meet leading international specialists, share their expertise and start business co-operations in the field of thermoplastic composite technologies. The international exhibition will feature 40+ exhibitors showcasing all steps of the supply-chain. Be it materials, machines, testing, processes, or solutions. By combining the exhibition and the conference ITHEC is further fostering the inter-connectivity between science and industry.
Recoat temperature, part orientation and bead geometry are some key design variables to consider for a successful and reliable large-format additive manufacturing (LFAM) process.
Stephen Heinz, vice president of R&I for Syensqo delivered an inspirational keynote at SAMPE 2024, highlighting the significant role of composite materials in emerging technologies and encouraging broader collaboration within the manufacturing community.
Another important factor in metal Additive Manufacturing is the surface quality, as high accuracy and low surface roughness might make additional mechanical post processing unnecessary. In this regard the surface finish of parts made by LB-PBF is often compared to the surface quality of cast parts. While functional surfaces must be post-processed, free form surfaces can be kept as-built or simply sand blasted. In MIM, as-sintered quality usually fulfils the requirements for functional surfaces. The surface roughness, as well as the repeatability of dimensional accuracy, allows the production of highly precise parts without mechanical post-processing. If all the functional surfaces cannot be achieved in the moulding process, it is common to process the parts in the green state. Milling operations are significantly easier while the part is unsintered and the same holds for sinter-based AM parts.
Production speed in Binder Jetting is calculated from the total build job time and packing density. The packing density reflects the sum of all part volumes referred to the complete build envelope. Packing density is typically 10% for mixed build jobs with different parts and 30% for optimised stackable parts in a large volume production. Build times are between twenty and forty hours. Considering the claimed improvements in the technology in the next few years, the build envelope will increase while the total build time reduces to ten hours thanks to single pass jetting. With the systems available today, the cost of a build with stainless steel is between €0.5 and €1 per cm³.
The composites industry is increasingly recognizing the imperative of sustainability in its operations. As demand for lightweight and durable materials rises across various sectors, such as automotive, aerospace, and construction, there is a growing awareness of the environmental impact associated with traditional composite manufacturing processes.
American Bureau of Shipping (ABS) certifies use of jointly developed CFRP repair technique on FPSO and FSO industrial systems, addressing traditional steel restoration challenges.
Whether you’re exploring new applications or seeking to gain a foothold in emerging markets, Carbon Fiber 2024 is where you’ll discover the insights and connections needed to shape your business strategy. Register now.
A combination of Airtech’s 3D printing materials and Ascent’s production capabilities aim to support increased use of composite additive tooling in spaces like defense and aerospace.
Recoat temperature, part orientation and bead geometry are some key design variables to consider for a successful and reliable large-format additive manufacturing (LFAM) process.
UK-based Wayland Additive is convinced that, when it comes to metal Additive Manufacturing, Electron Beam Powder Bed Fusion (PBF-EB) has a bright f...»
This study analysed the arithmetic average surface roughness in the as-sintered state by tactile measurement. The values were obtained by measuring the specimens’ surfaces in the zx- and xy-plane. The mean value of both measurements allows a technology comparison. However, especially for metal FDM, the surface roughness depends significantly on the build direction (Fig. 11).
During this webinar, the audience will be introduced to a variety of fiber composite technologies — as well as the machines and equipment — from short fibers to continuous fibers, from thermoset to thermoplastic, as well as the according process technology, including a special focus on long-fiber injection (LFI) and structural composite spray (SCS). Focus markets include automotive, aviation and AAM, transportation, and construction. This webinar will provide a detailed overview of according application examples. Agenda: Long fiber injection (LFI) Structural composite spray (SCS) Resin transfer molding (RTM), wet compression molding, etc. Pultrusion FiberForm
Herone, Spiral RTC, Teijin Carbon Europe and Collins Aerospace Almere recycle A350 thermoplastic composite clips/cleats waste into rods for the all-thermoplastic composite Multifunctional Fuselage Demonstrator’s crown.
Metal AM magazine, published quarterly in digital and print formats, is read by a rapidly expanding international audience.
Metal FDM uses wire, MIM feedstock or rods as the base material (Fig. 6). This raw material feedstock is a compound of metal powder and polymer binder. While the machine principle is very similar to polymer FDM systems, the key difference lies in the extrusion nozzle, which has specific characteristics for applying the metal-loaded feedstock.
Formnext Chicago is an industrial additive manufacturing expo taking place April 8-10, 2025 at McCormick Place in Chicago, Illinois. Formnext Chicago is the second in a series of Formnext events in the U.S. being produced by Mesago Messe Frankfurt, AMT – The Association For Manufacturing Technology, and Gardner Business Media (our publisher).
The AM supply chain is bound to experience changes with the adoption of these emerging technologies. Starting with material feedstock, today’s metal powder suppliers face new markets in Binder Jetting and metal FDM technologies. However, both technologies will have different requirements for their products.
Comparing the production speed proves to be challenging. While LB-PBF and FDM systems can be quantified by their build rate (volume over time in cm³/h), the build rate of Binder Jetting processes largely depends on the packing density. Build jobs of the same height usually take the same amount of total build time independently from the aggregated part volume.
Foundational research discusses the current carbon fiber recycling landscape in Utah, and evaluates potential strategies and policies that could enhance this sustainable practice in the region.
The JEC Forum DACH is a business meetings event organised by JEC The JEC Forum DACH is organised on October 22 and 23, 2024 by JEC, in partnership with the AVK, gathering the composite materials community from the DACH Region (Germany, Austria and Switzerland).
Thousands of people visit our Supplier Guide every day to source equipment and materials. Get in front of them with a free company profile.
Material availability and performance is a key enabling factor for new Additive Manufacturing applications. At the moment only LB-PBF offers a wide range of materials, with alloys based on aluminium, titanium, nickel, steel and precious metals, as well as other materials in development such as magnesium. In theory, any weldable material can be processed by LB-PBF. A multitude of publications on the mechanical properties of all these alloys means that engineers can be confident in their expected characteristics and ultimately results in a higher acceptance of LB-PBF over less-researched technologies.
The composite tubes white paper explores some of the considerations for specifying composite tubes, such as mechanical properties, maintenance requirements and more.
Whether you’re exploring new applications or seeking to gain a foothold in emerging markets, Carbon Fiber 2024 is where you’ll discover the insights and connections needed to shape your business strategy. Register now.
Prepreg co-molding compound by IDI Composites International and A&P Technology enables new geometries and levels of strength and resiliency for automotive, mobility.
The first project is underway to recover carbon fiber used in an A330-200 aircraft, which will then be regenerated for other end uses by HRC.
At Ampower we expect the main impact for Binder Jetting to be seen in the higher production volume applications as, for example, seen in the automotive industry. Metal FDM technology will enable applications in the machine industry, especially when it comes to low production volumes, prototypes or jigs and tools. Due to the high requirements on material properties, we expect it to be unlikely that aviation and implant manufacturers will adopt sinter-based AM technologies for highly loaded parts.
In addition to providing extensive industry news coverage, Metal AM magazine is known for exclusive, in-depth articles and technical reports.
The Marservis PROeco is a mass transportation marine vessel using Bcomp natural fiber for interior parts in place of standard materials.
Sinter-based metal AM technologies can be classified into metal FDM and Binder Jetting processes. Both are currently available from several system manufacturers. While Binder Jetting has its roots in the Additive Manufacturing of sand cores, metal FDM is based on conventional FDM technology.
Low-melt polyaryletherketone (LMPAEK) unidirectional tapes provide outstanding thermal and fire protection, demonstrating their effectiveness through rigorous testing. These tapes are fire, smoke and toxicity compliant with FAR25.853 and meet OSU Heat Release Rate standards. The tapes were tested under ISO 2685/AC 20-135 Change 1, meeting the fireproof criteria. Additionally, they met UL 2596 requirements for battery thermal runaway tests. These tapes are crucial for high-temperature applications showcasing their resilience and safety in both aerospace and automotive applications. Part of a broader range that includes films and compounds, Victrex LMPAEK materials are valued for their excellent processability and weldability. They offer versatile solutions for complex needs beyond traditional structural parts, such as: thermal runaway and lightning strike protection, heat sinking, and intricate bracketry. Victrex LMPAEK materials facilitate automation and high-rate production while addressing performance and sustainability challenges. With reduced environmental impact, lower weight and cost-efficiency, they meet the evolving demands of the transportation industry and support innovative design solutions. Agenda: Introduction to LMPAEK ecosystem, highlighting unidirectional tapes Thermal and fire protection performance: applications and benefits Material forms and processability Sustainability and efficiency Conclusion and future innovations
Component manufacturers now have more options than ever when it comes to choosing the right technology for their application. However, this choice also challenges engineers to develop knowledge of several different production technologies. In the past few years, casting and forging engineers have had to adopt and develop knowledge about LB-PBF. Now, the technologies of Binder Jetting and metal FDM offer an even wider choice. More than ever, the knowledge about possibilities, limitations and characteristics of the different manufacturing technologies becomes a crucial factor for engineers of tomorrow. Fig. 13 shows a technology map to support the choice of technology based on manufacturing volume and part complexity.
A report on the demand for hydrogen as an energy source and the role composites might play in the transport and storage of hydrogen.
Aerospace manufacturer joins forces with composite materials company to achieve sustainable manufacturing practices that overcome traditional composite layup tooling.
Knowing the fundamentals for reading drawings — including master ply tables, ply definition diagrams and more — lays a foundation for proper composite design evaluation.
How the predictive tool “CZone” is applied to simulate the axial crushing response of composites, providing valuable insights into their use for motorsport applications.
Together with a number of industry partners, Ampower is currently evaluating whether these sinter-based metal AM technologies can live up to expectations and become a serious competitor to LB-PBF. The industrial partners for this investigation are Alliance MIM, DB Fahrzeuginstandhaltung GmbH, C. Illies & Co. Handelsgesellschaft mbH, Lufthansa Technik AG, citim GmbH, Porsche AG, SLM Solutions Group AG and Yxlon International GmbH.
Cevotec, a tank manufacturer, Roth Composite Machinery and Cikoni, have undertaken a comprehensive project to explore and demonstrate the impact of dome reinforcements using FPP technology for composite tanks.
The technology principle is still based on the original MIT patents, which refer to a powder bed of sand or metal powder on which binder is locally applied. This fluid binder solidifies by applying heat (Fig. 7). A slightly different approach is described by 3DEO. Here, the binder is applied on the complete powder bed area followed by a milling process of the hardened layer with multiple machining spindles to create the contour of the part in each layer.
Prepreg co-molding compound by IDI Composites International and A&P Technology enables new geometries and levels of strength and resiliency for automotive, mobility.
For density analysis, six sections of each technology were analysed by light microscopy. The analysis includes micrographs from several Binder Jetting and metal FDM system manufacturers as well as MIM and LB-PBF specimens. The results show significant differences in pore size, shape and distribution between the technologies (Fig. 8). For all sinter-based technologies, the most likely cause of this is the different debinding and sintering strategies and not the specific Additive Manufacturing mechanism. It is worth mentioning that the density of all analysed MIM samples exceeds the standard MIM as-sintered density range of 95–97%. This however is unsurprising, as the selected supplier targets demanding applications with high performance requirements.
For metal FDM the feedstock consists of wire, granulate or rods made of metal powder and polymer binder compound. Here, the cost of binder is already included. However, the spread in feedstock cost is significant. While granulates are based on conventional MIM feedstocks and range between €15–18 per kg for 316L, filaments such as BASF’s Ultrafuse 316LX are priced at around €200 per kg. However, similar metal filaments are also sold from other suppliers for €100 per kg. While Binder Jetting and granulate based metal FDM are leading to massive cost reduction on material, other metal FDM technologies result in even higher feedstock pricing than LB-PBF.
For this study, stainless steel alloys 316L and 17-4PH were chosen to determine the material characteristics. These alloys are commonly available for the LB-PBF, MIM, metal FDM and Binder Jetting processes and therefore offer the best property comparisons. The obtained results are based on over fifty specimens from eight different system suppliers. The complete test program includes tensile testing, hardness and surface roughness measurements as well as micrograph and µCT analysis.
Celebrating National Composites Week 2024, CW looks at how composites are being used to provide the next generation of energy.
Performing regular maintenance of the layup tool for successful sealing and release is required to reduce the risk of part adherence.
Thermoplastic material systems have been used in aerospace for decades. Their use and adoption continues to grow and Trelleborg has been on the leading edge of development for many of these systems. In this webinar, Trelleborg will be presenting a range of topics from the use of in-situ, automated fiber placement of thermoplastics prepreg for structural and functional products to complex injection molding of thermoplastic interior pieces. It will explore some of the benefits these products provide and the potential for future growth and development.
As a technology, Additive Manufacturing can look back on a history of over thirty years. Beginning primarily as a prototyping technology, it has over the last five years gained tremendous momentum for the production of functional parts in a wide range of industrial applications. For many highly demanding applications, Laser Powder Bed Fusion (LB-PBF) has become the dominant Additive Manufacturing technology. However, with the development of metal AM technologies that rely on a sintering process as a final production step, this may be about to change. The technology of fundamental importance to the development of these new processes is Metal Injection Moulding (MIM), hence frequent references to ‘MIM-like’ AM processes.
Kennametal is a particularly interesting company when it comes to the adoption of Additive Manufacturing. It is a dynamic global producer of toolin...»
An overview of ASTM Standard Guide D8509, and its coupon-level mechanical testing of design properties for analyzing composite bolted joints.
Kennametal will cover the influence of different composite materials characteristics on drilling performance and how to optimize the process. Agenda: Who is Kennametal? Hole making challenges in composite materials Innovations for hole making applications Upcoming events and academic partnerships
Arris presents mechanical testing results of an Arris-designed natural fiber thermoplastic composite in comparison to similarly produced glass and carbon fiber-based materials.
CW Tech Days are virtual events dedicated to the topics impacting the composites industry today. Access past event recordings and register for upcoming Tech Days.
The Marservis PROeco is a mass transportation marine vessel using Bcomp natural fiber for interior parts in place of standard materials.
An on-demand mapping tool for anisotropic materials and polymer material fracture prediction model, i-Lupe, aims to help predict impact, crash behaviors.
EU project will develop bio-based, repairable and recyclable vitrimer composites and advanced sensors for highly reliable, sustainable wind blades.
During this CW Tech Days event, sponsored by Composites One, experts will offer presentations to review and evaluate the composite materials, processes and applications that should and will be considered for use in the infrastructure and construction markets.
Explore the technologies, materials and strategies used by composites manufacturers working in the evolving space market.
New aircraft is expected to deliver wind turbine blades from 105 meters up to expand the reach of wind energy and achieve global climate goals.
Regarding part size, MIM parts are characterised by rather small component dimensions of typically 50 mm or smaller. The reason for this limitation lies in the debinding and sintering process. From a practical point of view, debinding limits the maximum material thickness to 5–10 mm. Exceeding this value increases the debinding time exponentially or makes complete debinding impossible. Additionally, sintering requires temperatures close to the material melting point, which can cause deformation when large masses or geometric complexity exist. During the sintering phase, the part undergoes the most significant shrinkage and a suitable surface is therefore required to allow this movement.
To reduce complexity, some sinter-based metal AM technology vendors use a one-step thermal debinding and sintering process. For components with wall thicknesses of up to 3-4 mm, this takes about sixteen hours in a typical furnace with a volume of 50,000 cm³. The hourly rate for a thermal debinding and sintering furnace ranges between €13 and €23, with the lower estimate being for a typical debinding operation and the higher figure representative of a typical sintering operation. This figure is based on a calculation that includes utilities and consumables such as electricity, process gas, the cost of a standard furnace with deprecation over five years with an annual run time of 6,000 hours, and furnace maintenance. Excluded from the calculations are labour, infrastructure and overheads, etc. Assuming a packing density of 10%, the cost for thermal debinding and sintering is estimated at €0.08 per cm³. In contrast, the cost for catalytic debinding and sintering adds up to about €0.28 per cm³.
The cost for metal powder suitable for LB-PBF ranges from €40 to €400 per kg, depending on the alloy. For stainless steel, the cost is at the lower end, between €40 and €80 per kg. As with LB-PBF, current Binder Jetting technologies use spherical powder particles; however, many of the new technologies, such as that of Desktop Metal, use conventional MIM powders. Since the cost for stainless steel MIM powder such as 17-4PH is only €5–10 per kg, this offers great potential for reducing material cost by 80–90%, although the cost of the binder material must also be added.
The major limit of binder technologies will remain in the part size and complexity limitations of the sintering process. Here, manufacturers of sintering equipment and toll sintering operations will experience a significant growth in interest in their products and services. Furthermore, we expect that many conventional MIM producers will integrate sinter-based AM technologies into their portfolio.
Analyzing structural resonance of the aircraft under various loads becomes a critical step in obtaining flight certification.
This sidebar to CW’s August 2024 feature article reviews this technology for more efficient composites manufacturing and why it aligns with Koridion active core molding.
CompositesWorld is the source for reliable news and information on what’s happening in fiber-reinforced composites manufacturing. About Us
All these MIM restrictions also apply to sinter-based metal AM technologies. With dimensional distortion during sintering difficult to predict, one of the major advantages of Additive Manufacturing – the ability to deliver very low volumes or one-off parts – is negated. Developing a sinter-based process for complex parts requires several test loops to control any distortion during sintering. This limits these AM technologies to either simple part geometries or trial and error loops for complex parts.
Binder Jetting and metal FDM printing processes are always followed by an additional debinding and sintering process. The costs for this largely depends on the specific debinding and sintering technology used by the system supplier. In MIM, catalytic debinding and sintering processes dominate, thanks to their high productivity and good process control. On the other hand, the catalytic process requires a high level of equipment investment, process knowledge and the use of hazardous consumables such as nitric acid.
In the Automated Composites Knowledge Center, CGTech brings you vital information about all things automated composites.
With AIM3D, Desktop Metal, EVO-Tech and Markforged, four major suppliers are currently offering metal FDM printing systems. Their business models vary as they each cover different aspects of the vertical value chain. While Markforged offers proprietary material solutions and debinding/sintering solutions alongside their AM system, AIM3D and EVO-Tech use metal filament and MIM feedstock that is readily available on the market from established suppliers, such as BASF. Furthermore, they use common debinding and sintering process equipment offered by a number of tried and tested MIM furnace manufacturers.
This collection details the basics, challenges, and future of thermoplastic composites technology, with particular emphasis on their use for commercial aerospace primary structures.
Conventional Powder Injection Moulding (PIM) technologies, incorporating the use of a metal or ceramic powder, mixed with a polymer binder and then a debinding and sintering step, are firmly established in today’s manufacturing environments and have a far longer history in industrial applications than Additive Manufacturing. Dating back to the late 1930s and early 1940s, the precursor to what we now know as Ceramic Injection Moulding (CIM) used ceramic powder and a binder to manufacture products such as spark plug bodies. In the 1970s the technology was significantly enhanced with new, more capable binders, and the use of metal powders was investigated. This work led to the birth of Metal Injection Moulding, for which the first patent was filed in 1976. The early cost of MIM parts, however, was extremely high and the process more complex in comparison to competing casting technologies. The subsequent development of more sophisticated binder materials and debinding processes brought improved process stability and easier access to the technology, leading to strong global growth. Today, total global sales of metal injection moulded parts are valued at over €2 billion, with a compound annual growth rate of between 10 and 20%. MIM applications are dominated by complex components for consumer electronics, medical devices, orthodontic applications, firearms, automotive components, watches, jewellery and power tools. Part sizes typically vary between 5–50 mm, however some are in the micro size range and weigh just 0.02 g, whilst others can weigh more than 500 g. The MIM process is based on three steps (Fig. 3):
Additionally, stitch-bonded non-crimp fabrics (NCFs) provide manufacturers and asset owners even more ways to gain a competitive advantage with products built specifically for the environments and loading conditions in which they will be utilized. Join Vectorply Corporation and Creative Composites Group (CCG) for this in-depth webinar detailing the process of engineering NCFs to build composite parts that will stand the test of time. Unlike steel, concrete and wood, composite NCFs can be optimized utilizing various fiber types, architectures and substrates to achieve the specific goals of their application efficiently. High corrosion resistance, strength and stiffness, and longevity can all be accomplished with custom-designed laminates for these heavily abused applications. Vectorply Vice President of Engineering Trevor Gundberg and Creative Composites Group Chief Sales Officer Dustin Troutman will share their industry-leading expertise on the process of laminate design and part production. Attendees can expect to learn when to use composite NCFs in their production process and the wide range of fiber-reinforced plastic (FRP) composites that Creative Composites Group produces for the industrial and infrastructure markets. Whether you want to learn more about utilizing NCFs in your production process or why CCG’s extensive product line may be the choice for your project, this webinar is the place learn the process and how to take the next steps. Agenda: Distinct advantages of non-crimp fabrics versus alternative materials How to design laminates for specific processes such as pultrusion and infusion Real-world success spotlights of NCFs in industrial applications
Trelleborg will present a range of topics from the use of in-situ, automated fiber placement of thermoplastics prepreg for structural and functional products to complex injection molding of thermoplastic interior pieces.
Two recent award winning MIM parts that demonstrate the technology’s capabilities for net-shape high-volume production are shown in Figs. 4-5. Based on the recent success of sintering technologies in general, and MIM in particular, several companies have developed sinter-based metal AM technologies. These new AM technologies share steps 2 and 3 with Metal Injection Moulding. However, the forming of the green part uses the layer-on-layer manufacturing principle of Additive Manufacturing instead of injection into a mould. Nevertheless, the actual material deposition method used to create the green part can vary greatly from company to company.
Don't miss any new issue of Metal AM magazine, and get the latest industry news. Sign up to our twice weekly newsletter.
This report will focus on the hardness measurements and density analysis, which represents a major quality factor for metal parts. A high material density is paramount for good material characteristics such as tensile strength and fatigue behaviour. Also, with design restrictions in mind, a certain density is required for all components which carry fluids or gases. In these applications, low density leads to the need to increase wall thicknesses to achieve the necessary impermeability of the part.
Ampower is a leading consultancy in the field of industrial Additive Manufacturing. The company advises its clients on strategic decisions by developing and analysing market scenarios as well as compiling technology studies. On operational level, Ampower supports the introduction of Additive Manufacturing through targeted training program as well as identification and development of components suitable for production. Further services include the setup of quality management and support in qualification of internal and external machine capacity. The company is based in Hamburg, Germany.
Eco-friendly natural fiber range of decking, cladding, fencing, railing options ensure durable and long-lasting structures.
Explore the cutting-edge composites industry, as experts delve into the materials, tooling, and manufacturing hurdles of meeting the demands of the promising advanced air mobility (AAM) market. Join us at CW Tech Days to unlock the future of efficient composites fabrication operations.
Our audience includes component manufacturers, end-users, materials and equipment suppliers, analysts, researchers and more.
Closed mold processes have many advantages over open molding. In this knowledge center, learn the basics and vital tools needed to produce parts accurately.
Composites using graphene is not a new concept — but what is new is that the industry now recognizes "graphene" as an actual family of materials with different properties and promise. A new and exciting form of graphene is made from reclaimed methane, which uses new technologies to create green carbon materials. While showing great sustainability promise, functionalization is needed to unlock graphene's full range of properties for the next generation of composites to make these carbon materials useful. In this webinar, graphene manufacturer Mito Material Solutions will discuss how to bring functionalization and multifunctionality to these new "green" graphenes to enable a stronger, more robust and sustainable world.
Sinter-based AM processes require a debinding and sintering step and therefore all have heat in common as the main energy source. They are also classified by the material deposition method and further distinguished by the type of feedstock:
Udita Menon is a project engineer on the aerospace business development team. Her goal is to bridge the global technology and resources of Trelleborg to provide new solutions to the customer base. She has been with Trelleborg for five years, previously working in the roles of quality engineer and project manager. Her education is in mechanical engineering and she is currently based in Denver, Colorado.
GETTING A QUOTE WITH LK-MOULD IS FREE AND SIMPLE.
FIND MORE OF OUR SERVICES:
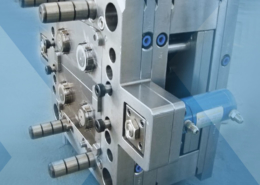
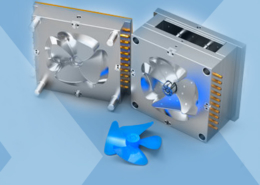
Plastic Molding

Rapid Prototyping
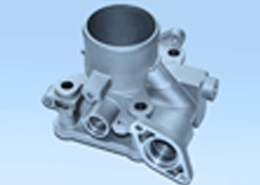
Pressure Die Casting
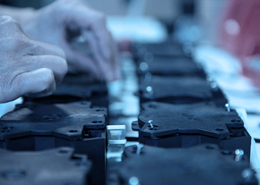
Parts Assembly
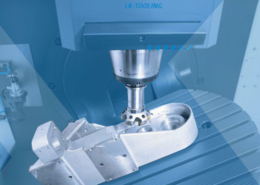