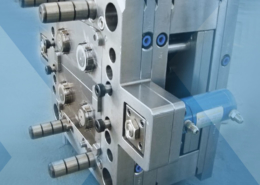
Micro Injection Molded Plastic Market Size Report, 2024-2032 - automotive plasti
Author:gly Date: 2024-09-30
The pilot plant has been equipped 11 injection moulding machines with clamping forces of between 65t and 420t, two of which are equipped for two-component injection moulding with clamping forces of 120t and 200t, respectively. It also features project-specific assembly units such as joining machines, bonding units or ultrasound welding systems.
Synchronous lifting of the load-bearing core and stripping of the molded part saves time, mold costs, and installation space.
Braunform initially designed an eight-cavity pilot mold for testing purposes, which ultimately led to a 32-cavity production mold. Synchronized mechanical movements in combination with a horizontal part made it possible to perform direct injection via a valve gate.
Even at this early pre-production stage, the pilot production unit complies with large-scale quality standards so that the acquired production intelligence can be applied directly to large-scale production processes at any Gerresheimer facility, the company says.
"With more than 25 years of experience in the field of medical technology and production in cleanrooms, we are proud to further support our medical technology customers in the safe and effective production of their plastic articles," said Joachim Stiller, general manager of Braunform GmbH.
Cleanroom Technology keeps decision-makers worldwide updated on contamination control via digital, live, and print platforms. Our articles span the cleanroom lifecycle, from design to maintenance, including monitoring and compliance. Editors deliver breaking news, product launches, and innovations, and also commission exclusives on technical trends from industry experts
German medical molding specialist Braunform combined two technologies developed in-house to reduce cycle times and optimize quality.
Medical molding specialist Braunform GmbH will showcase at Fakuma next month how a combination of two technologies developed in-house enabled a mold design and process that optimized the production of insulin pen housings.
Braunform developed the Med Mold concept to ensure the safe use of injection molds in cleanrooms, based on a quarter century of experience in cleanroom production. Specifically developed for medical and pharmaceutical applications, Med Mold has been part of the company’s standard operations since 2010.
Quality is optimized because the horizontal positioning reduces flash formation compared with slider molds. The vertical arrangement also improves gate quality.
A Management Execution System (MES) guarantees efficient, fast and cost-efficient production processes. Automated quality checks are integrated into the process, while an end-to-end tracking system for individual subassemblies or batches ensures that all products comply with the required quality standards for pharmaceutical and medical technology products.
In the company’s proprietary Lift&Strip² technology, movement is initiated by the machine’s ejector, which lifts and strips the part simultaneously. A movable forced guidance system, the stripping mechanism moves synchronously with the mold opening. Previously, when the mold opened, stripping was actuated by a separate drive. This drive is no longer required and the two processes have been combined into one. This innovation reduces cycle times and increases efficiency, said Braunform.
In the initial phase, the production area will be 420m2 in size, with plans to expand this to 1,400m2 in 2016. It will include a 400m2 ISO Class 8 cleanroom to the DIN EN ISO 14644 standard, while integrated laminar flow hoods create an ISO Class 7 cleanroom environment in the injection moulding area. A gantry crane inside the cleanroom allows for fast and easy mould changes, the company says.
The pilot plant delivers laboratory prototypes, clinical test samples and small-scale production batches at any project stage. Potential weak points can be spotted at an early stage, optimised during the active project, and the acquired insights applied to large-scale production. Similarly, all intelligence gathered during the mould engineering and automation processes can be applied directly to the construction of moulds and technical equipment for large-scale production. The development and project teams supervise the entire product creation process right through to series production.
Gerresheimer Medical Plastic Systems has installed a small-scale pilot production unit at its Technical Competence Centre in Wackersdorf, Germany.
Editor in chief of PlasticsToday since 2015, Norbert Sparrow has more than 30 years of editorial experience in business-to-business media. He studied journalism at the Centre Universitaire d'Etudes du Journalisme in Strasbourg, France, where he earned a master's degree.
Gating options are optimized by enabling a horizontal lengthwise positioning of the parts. Side-gate applications can be avoided and conventional valve gate applications can be implemented.
The control of the entire production process, including order management, production planning and scheduling, mould service, injection moulding/assembly, quality management and freight management, complies with the standards of large-scale production processes.
Braunform will exhibit at booth 5207 in hall A5 at Fakuma. The international trade show for plastics processing returns to Friedrichshafen, Germany, on Oct. 15 to 19, 2024.
GETTING A QUOTE WITH LK-MOULD IS FREE AND SIMPLE.
FIND MORE OF OUR SERVICES:
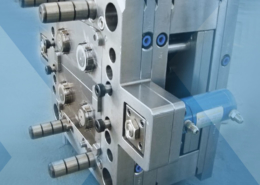
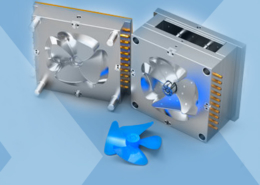
Plastic Molding

Rapid Prototyping
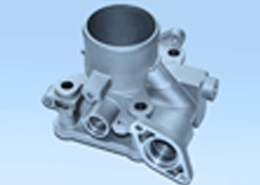
Pressure Die Casting
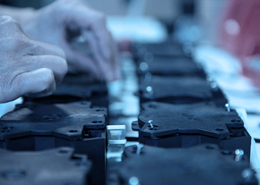
Parts Assembly
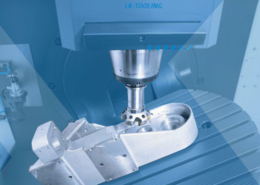