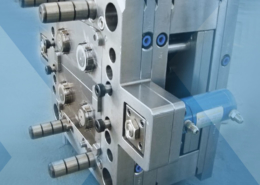
Mexico's manufacturing boom lures U.S. molders - injection mold makers
Author:gly Date: 2024-09-30
Depending on the production volume, multiple tools with up to sixteen mould cavities can be used, though the majority of tools have two to four mould cavities. “Hot runner technology is often used, but if heat transfer from the hot runner to the part is a problem for very small parts, we do not use this solution,” said Hermes.
Parmaco develops about thirty new MIM parts a year. The required injection moulding tools are designed and specified by the company’s own tool experts (Fig. 6) and then manufactured by external specialists. There are a number of qualified toolmakers in the vicinity who are commissioned with the production. Depending on the requirements of the tool, delivery time, and price, the best-suited toolmaker receives the order. “Minor tool repairs and maintenance work are done in-house, but in-house toolmaking is not economically viable,” shared Hermes.
“Apart from the higher accuracy requirements, there is no significant difference in the production of microMIM parts compared to traditional MIM parts. After injection moulding, they also go through the debinding and sintering processes. However, microMIM parts generally have to be ready for use after sintering, because reworking is usually no longer possible,” stated Breitenmoser.
A certified quality management system according to ISO 9001:2015 with periodical re-certifications is in place at Parmaco. High-precision measuring instruments are used to ensure the consistently high dimensional accuracy of tools and components (Fig. 4). In addition to dimensional inspection, metallographic inspection is also of great importance (Fig. 5).
Since the beginning of the industrialisation of MIM technology in the early 1990s, Parmaco Metal Injection Molding AG has maintained a leading position in the European MIM industry. This achievement of Georg Breitenmoser cannot be overestimated, particularly since the conditions for the production of metal components are particularly challenging in a high-wage country such as Switzerland. With great perseverance, innovation and commercial prudence, he has guided the company through all of the past market challenges. Parmaco’s team is determined to continue its success into the future.
And though the argument against masterbatch always is about these visual defects, little is said about scrap from paint lines, which can reportedly be more than 20%. Painting is not only more costly, and energy-intensive; it also generates very high levels of non-recyclable scrap.
As far as Additive Manufacturing processes are concerned, Parmaco is constantly investigating which technologies bring benefits to the company. Experience has already been gained with Binder Jetting and, in cooperation with the Swiss company Injex, injection moulds and MIM prototypes have been additively manufactured. This has enabled Parmaco to provide customers with prototypes of new MIM parts in the shortest possible time. “The surfaces of the prototypes produced in an additively manufactured injection mould were comparable to MIM series parts and significantly better than with Binder Jetting; however, the dimensional distribution was not always as good as conventional MIM tools,” stated Breitenmoser.
Ideally, parts will be ready for use by the customer after sintering, but this is not always the case. If a straightening process is necessary to comply with particularly tight dimensional tolerances which are not possible without reworking, this is carried out in-house. Other secondary processes such as machining, heat treatment, vibratory finishing, coating, etc. are carried out externally.
Parmaco successfully manufactures components for laparoscopy, a minimally invasive surgical procedure for abdominal operations. A laparoscope (a device with a built-in camera, light source, and rinsing and suction device) is inserted through a small opening in the abdomen and can be used to diagnose organs in the abdomen, or for surgery. The requirements for MIM parts for laparoscopes are extremely high in terms of geometrical complexity and dimensional accuracy. This and other fields of medical application are very attractive for Parmaco.
By international standards, Parmaco is not a company that wins customers through low prices; it is, after all, only through cost-covering prices that the company can pay Switzerland’s high wages to its employees. “As a technology-driven company, Parmaco makes every effort to push MIM technology to its limits and to extend those limits further,” said Hermes. “This builds trust with customers because they benefit from our technology, and they are willing to work closely together with Parmaco in the development of their products.”
Discover suppliers of these and more in our advertisers’ index and buyer’s guide, available in the back of PIM International.
In the case of new injection moulding tools, minor changes or adjustments may still have to be made after commissioning, for example in relation to the venting of the moulds or to manage burr formation. “In most cases, initial part dimensions correspond very well with the specification, at least if the tolerances are not exceptionally tight,” Breitenmoser explained. “However, we are usually operating at the limit of what is feasible with our dimensional tolerances. Since we are located in Switzerland, our strategy focuses on exceptional quality and tight tolerances. This is the only way we can justify Swiss prices.”
For a medium-sized company, employing about sixty people, Parmaco has a relatively large product development department. This consists of eight employees who take care of the introduction of new parts, as well as the automation and optimisation of the production process. Around forty employees work in production, quality assurance, and maintenance, while the rest work in sales and administration. The plant has a production area of about 4,000 m2 (Fig. 1).
Compared to other MIM producers, Parmaco manufactures relatively small parts. According to Breitenmoser, the average part weight is 6 g. The smallest parts weigh significantly less than 0.05 g.“With our sales activities, we are targeting the market leaders in the industries we supply,” said Breitenmoser. Parmaco sees itself as one of the market leaders in MIM technology and the company’s management sees that market leaders in end-user sectors appreciate Parmaco’s superior technology.
In more than thirty years of MIM manufacturing, Parmaco has learned to effectively master its own processes. Through the extensive documentation of process parameters and quality checks, the foundation has been laid for reliable process monitoring. This makes it possible to detect deviations from ‘safe’ values at an early stage and to take countermeasures. As part of a development project, Parmaco is investigating opportunities for the use of Artificial Intelligence (AI) in order to derive new process insights. The ambition is to further improve product quality through the huge amounts of data collected over decades.
Transitioning from paint to the use of MIC with Smartbatch FX helps manufacturers in the automotive, appliance, consumer goods and other industries create attractive, durable parts at reduced cost. PolyOne’s metallic-effect masterbatches can be incorporated into pre-colored compounds or dosed at a molding machine.
For many years, Breitenmoser has also been actively involved in the EPMA and the German MIM Expertenkreis. These organisations offer a forum for an exchange between the participating organisations and also provide suggestions for development projects that benefit the entire MIM industry. Parmaco sees high value in these networking activities.
Extensive MIM, CIM industry and sinter-based AM industry news, plus the following exclusive deep-dive articles and reports:
Another innovation for prototyping is the use of additively manufactured tool inserts made of a material that can be removed in solvent. Parmaco’s feedstock is injected into these tool inserts, then the entire tool insert is ejected. The tool insert is then dissolved in the solvent. What remains is the green MIM part, which is further processed using the usual technology. According to Breitenmoser, quite good surface qualities can be achieved if the tool inserts are manufactured with a very low build rate of around 10 μm per layer. “This process is ideally suited to prototyping microMIM parts, primarily because it is – at first – unnecessary to worry about ejecting the part from a mould,” said Breitenmoser.
Reach a truly international audience that includes component manufacturers, end-users, industry suppliers, analysts, researchers and more.
“Typically, you do not want a bunch of holes or sharp curves in a part if you intend to use metallic-effect masterbatch. Too often, a mold is made for molding of parts that will be painted, and then — when it is time for a facelift — the OEM decides it wants to save some money and shift from paint to masterbatch. However, without investing in a new mold, the existing mold design often makes it very difficult for masterbatch to be successfully used.
Transitioning from paint to masterbatch for metallic-effect parts is not new, but it is nowhere near as widespread as one would expect according to some auto industry observers. Inertia — We’ve always done it that way — and legacy investment in paint lines, supports the continued use of paint.
However, he believes that there are limits to these measures. “If you want good quality, you should not overdo the savings,” Breitenmoser said. This applies to both the consumption of process gases and to energy consumption.
Parmaco is a specialist in the production of microMIM parts, a term that Breitenmoser described as applying to “parts that weigh less than 1 g and also have particularly fine features. Such parts are also associated with particularly high dimensional accuracy requirements, and microMIM offers a proven route to meet these requirements. Of course, this also places particularly high demands on the precision of the injection moulding tools.”
Parmaco’s debinding and sintering is done in a batch process (Fig. 2). Debinding is divided into two sub-steps. Firstly, the parts are debound in a special solvent. Secondly, the residual binder is thermally removed in a reducing atmosphere before sintering. Hermes emphasised that the maintenance and servicing – especially of the sintering furnaces – is of paramount importance, because the more carefully the equipment is maintained, the more durable and reliable it is.
The key to molding good parts is for OEMs to decide, very early on, that a part will be colored with molded-in color masterbatch; that decision will then support the development of a mold and part suitable for masterbatch.
Stephen has been with PlasticsToday and its preceding publications Modern Plastics and Injection Molding since 1992, throughout this time based in the Asia Pacific region, including stints in Japan, Australia, and his current location Singapore. His current beat focuses on automotive. Stephen is an avid folding bicycle rider, often taking his bike on overseas business trips, and is a proud dachshund owner.
Don't miss any new issue of PIM International, and stay up to date with the latest industry news. Sign up to our fortnightly newsletter.
In Parmaco’s early days, components for defence applications were of great importance and, to this day, Parmaco manufactures parts for this industry, but applications in the growing lock, sensor and medical device industries have become much more important. Minimally invasive surgical devices are often single use and the quantities consumed are highly-suited to MIM.
In the early days, Parmaco primarily produced low-alloy Fe-Ni MIM parts. This group of materials still makes up a considerable percentage of production, as many parts run for years, sometimes decades. Newer projects are predominantly produced with high-alloy steels. Parts made of nickel-base alloys and heavy metal alloys are also in production, but to a lesser extent. “We are able to offer the full range of available MIM materials and our development department has the expertise to develop special materials in a short period of time, if this is required by customers,” said Breitenmoser.
To provide customers with additional information on making the switch from paint to molded-in-color parts, PolyOne has created an eBook titled, “Trend Report: Efficient Manufacturing And Molded-In Color.”
Life Cycle Assessments (LCA) are used to determine the consumption of gases, water and electrical energy in the company as well as the amount of waste in order to identify potential savings. Currently, the Fraunhofer IFAM institute in Bremen is developing standards for LCAs on behalf of the European Powder Metallurgy Association (EPMA) so that uniform methods for assessing sustainability can be applied in PM and other industries, enabling comparable results. In addition to the consumption values of the company’s own operations, the CO2 footprints of the raw materials used must also be included in the calculation. For Breitenmoser, it is essential that such methods are internationally applicable and provide meaningful comparative values.
A key driver of innovation is the need to reduce the time it takes to prototype a new MIM part. Parmaco has introduced special prototype injection moulds that have a modular design. The cavities for these prototypes are incorporated into prefabricated tool inserts, thereby enabling prototypes to be produced in only a few weeks. Such tools allow Parmaco to economically manufacture even small batches of MIM parts with what is described as a “tried-and-tested” technology.
Sustainability and climate protection are high on Parmaco’s agenda. Breitenmoser ensures that measures are taken to both protect the environment and save on costs, whilst expecting politicians to also work to ensure that the wider industry is encouraged to take measures to protect the environment. As an example, he cites the CO2 tax, which rewards companies that reduce their emissions of climate-damaging gases. Reductions in electricity consumption are also an issue. Next year, Parmaco plans to install solar panels on all roofs of company buildings, thereby generating around 25% of the energy it needs sustainably. It should, of course, be noted that around 60% of Switzerland’s electricity comes from hydro-power, with a further 29% coming from nuclear.
From the very start, Parmaco has produced its feedstock in-house. The binder technology used has, of course, evolved over the decades, but the recognition of the value of having control over feedstock production remains. Breitenmoser appreciates the flexibility of in-house feedstock production for a number of reasons: on the one hand, binder compositions can be quickly adjusted if the moulds for particularly thin-walled parts are difficult to fill, or if other filling problems arise such as sink marks or voids; on the other hand, the binder composition can be adjusted if a part requires a particularly high green strength.
“When developing new parts, very close cooperation with the customer is essential,” added Breitenmoser. “We need to understand what functions and characteristics the customer wants the part to have so that we can optimise the design for the MIM process. It may even be possible to integrate the functions of two or more parts into one MIM part.” In addition, MIM can often provide added value that customers who are not so familiar with the process are often unaware of. For example, markings, labels or company logos can be integrated into the tool. “Our goal is to always create added value in dialogue with the customer through MIM production,” stated Hermes.
“It is in our DNA to never stand still. Even if a part is already being mass-produced, there are always opportunities to further optimise production – be it automation, furnace process control, a better understanding of the scientific background – and to convert the results into stable, safe processes,” explained Breitenmoser.
PolyOne recently collaborated with a leading global automotive OEM and its injection molder to eliminate paint from a new vehicle’s interior.
The 4th Workshop on Sinter-based Additive Manufacturing, organised by Fraunhofer IFAM, in Bremen, Germany, took place from September 13-14 2023. It...»
The small town of Fischingen, in eastern Switzerland, is home to one of Europe’s longest established manufacturers of MIM parts. In 1992, Georg Breitenmoser acquired a technology licence from the process pioneer, Parmatech Corporation, based in Petaluma, California, USA, and founded Parmaco Metal Injection Molding AG. The company is still Switzerland’s leading MIM producer and, to this day, Breitenmoser steers the fortune of the company as the sole owner and president of the board of directors, though he handed over management responsibility for daily operations to Kai Hermes, Parmaco’s General Manager, in 2020.
Some examples of Parmaco’s MIM products are shown in Figs. 7-11. Applications range from a sensor housing (Fig. 7) to laparoscopic instruments (Fig. 8 and Fig. 9) and robotic devices in medical technology (Fig. 10 and Fig. 11). All of the parts shown have extremely tight tolerances. These strict tolerance specifications ensure the highest precision and reliability of surgical instruments and other assemblies. After manufacturing, most parts are subjected to heat treatment to optimise surface properties and increase surface hardness.
The potential of sinter-based Additive Manufacturing for industrial production, along with the diversity of the processes that are being developed,...»
Computer simulations are used in tool design with the aim of achieving the required dimensional accuracy in as few iteration steps as possible (Fig. 6). As far as furnaces are concerned, reliance has, so far, been placed on empirically determined temperature profiles. The work on the simulation of furnace processes is known, but has not yet been applied in practice.
PolyOne recently collaborated with a leading global automotive OEM and its injection molder to eliminate paint from a new vehicle’s interior. To support the transition to molded-in-color (MIC) parts, PolyOne provided metallic-effect Smartbatch FX masterbatch colorants for two PC/ABS side panels on the center console of a compact SUV now entering commercial production. The parts (two; one on each side of the center console) are C-shaped, 35-cm long, and at their widest point 11-cm wide.
The industry’s challenges, in light of COVID-19 and an uncertain economy, could open the door much wider to greater use of metallic-effect masterbatches, as these significantly lower cost per part. The challenge with masterbatch remains molding parts that do not have visual defects such as flow or weld lines.
Paint adds a great surface finish to automobile parts, but painting always adds cost, time, and additional logistics requirements according to PolyOne. By using Smartbatch FX metallic masterbatches, the molder was able to produce parts ready for assembly with no secondary processing required. Suitable for standard injection molding machinery, Smartbatch FX reduces the cost per part by 30 percent or more compared to painted parts. Lowered energy requirements versus painting and the reduction of VOCs also make this masterbatch a more environmentally sustainable solution.
“Many car parts are painted, not just metal and thermoplastic exterior parts, but also thermoplastic parts in a vehicle’s interior,” notes Gary Fielding, vice president and general manager, Color and Additives EMEA at PolyOne. “We have successfully helped carmakers transition from paint to MIC for many exterior applications such as skid plates and trims. This recent project is a significant step forward in reducing the cost to manufacture highly visible interior applications.”
Metal Injection Moulding is one of the most capable manufacturing processes for small precision components, yet it is also one of the least well kn...»
Wherever it is possible and economically viable, production is automated. Green parts are removed from the injection moulding machine by pick-and-place robots or six-axis robots and placed on trays for further processing (Fig. 3).
The free-to-access PIM International magazine archive offers unparalleled insight into the world of MIM, CIM and sinter-based AM from a commercial and technological perspective through:
This is a story from what once looked like the edge of the metal Additive Manufacturing universe. A decade ago, the idea of a Metal Injection Moldi...»
GETTING A QUOTE WITH LK-MOULD IS FREE AND SIMPLE.
FIND MORE OF OUR SERVICES:
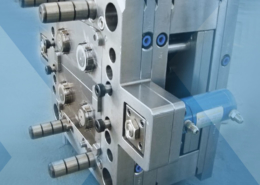
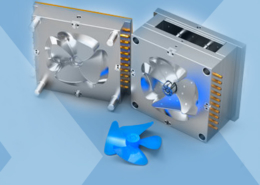
Plastic Molding

Rapid Prototyping
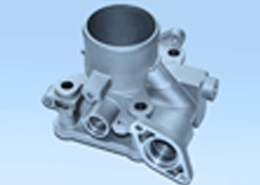
Pressure Die Casting
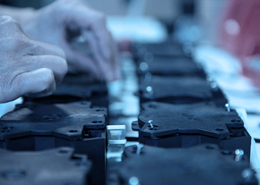
Parts Assembly
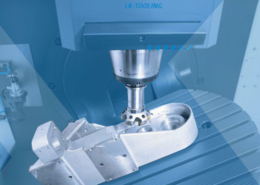