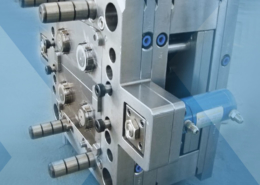
Metal Injection Molding in the consumer electronics and IT sectors - two part in
Author:gly Date: 2024-09-30
Gifted with extraordinary technical know how and an authoritative yet plain English writing style, in this collection of articles Fattori offers his insights on a variety of molding-related topics that are bound to make your days on the production floor go a little bit better.
Processors with sustainability goals or mandates have a number of ways to reach their goals. Biopolymers are among them.
However, re-stabilizing PCR products has, to date, attracted less attention than the larger challenges facing our recycling economy, such as improving recycler education and updating recycling facilities. In the U.S., for example, the recycling industry has invested, and continues to invest, in new technologies to improve the sortation and quality of recycled materials. These efforts should help make PCR content re-stabilization more effective.
In addition, Beaumont Technologies showed off its new Therma-flow software for “mapping” the moldability of materials (see March Keeping Up).
At the top of the list of new items from Milacron LLC is the Mold-Masters Summit Series premium hot-runner system. Nozzles and manifold have cast-in heaters surrounded by copper for good heat transfer, sandwiched between a stainless-steel core and sheath for chemical resistance. Aimed particularly at medical and personal-care applications, it boasts less than ± 5% thermal variation, important for running sensitive resins such as PC, COP, COC, PBT, and acetal. At the show, the Summit Series also ran Eastman’s Tritan copolyester in a 32-cavity mold for medical luers.
As demand for, and use of, PCR content continues to increase, there has been a renewed focus on the issue of polymer degradation. The properties of PCR content, such as melt flow, color and contamination, are directly related to proper stabilization—either upstream by plastics producers or downstream by recyclers and processors.
Ian Query is a technical specialist for the Special Additives division of Baerlocher USA. He has held this position since 2018, and is responsible for supporting downstream recycling and wood-plastic composite customers. Prior to joining Baerlocher, Query was a researcher for Nike’s Material Science Innovation team, focusing on material processing innovation and laboratory testing. He also has experience in PVC processing, serving on Emerald Kalama Chemical’s applications team, and performing research on PVC plasticizers. query.ian@baerlocher.com
While prices moved up for three of the five commodity resins, there was potential for a flat trajectory for the rest of the third quarter.
What’s more, Husky says Ultra Helix simplifies cold-half machining requirements to integrate the hot runner. That’s because “all the complexity is inside the nozzle,” according to Dave Morton, Husky v.p. Americas for hot runners and controllers. He also notes that new manufacturing technology guarantees stem-to-gate orifice concentricity, virtually eliminating mechanical wear on these components. Ultra Helix also boasts a highly consistent thermal profile, so molders don’t have to worry about altering the balance between cavities after changing a repleaceable heater.
Discover how artifical intelligence is revolutionizing plastics processing. Hear from industry experts on the future impact of AI on your operations and envision a fully interconnected plant.
HOT-RUNNER NEWS Alba Enterprises introduced to the U.S. triple-tip nozzles from Thermoplay of Italy that provide radially balanced filling of long, tubular parts such as syringe barrels .
ABOUT THE AUTHORS: Roberto Nunez, Ph.D., is business head of the Special Additives division of Baerlocher USA. He has held this position since 2017 and is responsible for managing P&L, sales, marketing, strategy development, innovation, and technical support for the division. Before joining Baerlocher USA, Nunez was a member of the Milliken Chemical executive leadership team for 12 years. baerlocher.com.
Chemical stabilizers can be incorporated during resin manufacturing, allowing the virgin material to be recycled several times. Also, stabilization can be added during PCR material filtration by recyclers, which involves melting and cleaning the resin to remove impurities that cause gels and black specks. Maintaining a constant level of stabilizers in your resin at every stage is key to optimal recycling.
Gifted with extraordinary technical know how and an authoritative yet plain English writing style, in this collection of articles Fattori offers his insights on a variety of molding-related topics that are bound to make your days on the production floor go a little bit better.
Second quarter started with price hikes in PE and the four volume engineering resins, but relatively stable pricing was largely expected by the quarter’s end.
In a time where sustainability is no longer just a buzzword, the food and beverage packaging industry is required to be at the forefront of this innovation. By adopting circular packaging processes and solutions, producers can meet regulatory requirements while also satisfying consumer demand and enhancing brand reputation. Join Husky to learn more about the broader implications of the circular economy — as well as how leading brands are leveraging this opportunity to reduce costs, increase design flexibility and boost product differentiation. Agenda: The cost and operational benefits of embracing circularity Key materials in circular packaging — including rPET and emerging bioplastics How to design a circular food and beverage package Strategies for selecting sustainable closures to future-proof packaging solutions Optimization and streamlining of production processes for enhanced efficiency How Husky Technologies can enable your sustainable success
In this three-part collection, veteran molder and moldmaker Jim Fattori brings to bear his 40+ years of on-the-job experience and provides molders his “from the trenches” perspective on on the why, where and how of venting injection molds. Take the trial-and-error out of the molding venting process.
The Plastics Industry Association (PLASTICS) has released final figures for NPE2024: The Plastics Show (May 6-10; Orlando) that officially make it the largest ever NPE in several key metrics.
Hasco America showed its newly improved Z3281 version of its Multimodule for mounting multiple nozzles in a round manifold block. It now accepts screw-in TechniShot series 20 nozzles for leak-free operation. Each nozzle’s temperature is individually controlled. Nozzle lengths run 50 to 125 mm, and pitch diameter is from 17 to 42 mm.
Across the show, sustainability ruled in new materials technology, from polyolefins and engineering resins to biobased materials.
Ultradent's entry of its Umbrella cheek retractor took home the awards for Technical Sophistication and Achievement in Economics and Efficiency at PTXPO.
August 29-30 in Minneapolis all things injection molding and moldmaking will be happening at the Hyatt Regency — check out who’s speaking on what topics today.
During the process of oxidative degradation, polymer chains change in different, negative ways. Polymers like HDPE and LLDPE tend to crosslink, raising melt viscosity and causing artifacts like gels. In polymers like PP, the oxidative degradation process results in chain scission, causing PP chains to be cleaved and melt viscosity to decrease. These changes in melt flow create issues with consistent melt processing. With the inclusion of a stabilizer package, changes to the polymer chains are mitigated and a more consistent melt flow can be expected.
Resin drying is a crucial, but often-misunderstood area. This collection includes details on why and what you need to dry, how to specify a dryer, and best practices.
Incoe announced the brand-new GSC mini valve-gate sequence controller. It’s a simple, low-cost device offering pneumatic, timer-based control of up to eight zones. Incoe also showed its compact HEM hydraulic cylinder for valve gates and a demonstration of the value of its SoftGate valve-gate speed controller. An Audi grille suffered from blistering of the chrome plating, caused by tiny air bubbles trapped under the surface of the ABS part. The problem was solved by controlled opening of the gates with SoftGate control.
The Summit Series can be supplied in valve-gate versions with servo-controlled pin actuators using compact stepper motors that allow for individual speed, time, and position control. Synchro Plate actuation of all pins (pneumatic, hydraulic, or servo) is also available. Summit Series valve gates come with a new extended ceramic valve disk for thermal insulation plus improved guidance and leakage resistance. Thermal-gate versions come with the ceramic EcoDisk for thermal insulation.
Exhibitors and presenters at the plastics show emphasized 3D printing as a complement and aid to more traditional production processes.
Osco Inc. showed its new mini valve-gate sequencer for up to eight zones. It’s pneumatic and time-based. Also new in the past year is the Quick Set mini hot half, a drop-in manifold with standard, off-the-shelf components. Osco also showed a hybrid application of its MGN Multiple Gate Nozzle. It combines two Osco systems: Its MGN multiple-gate nozzle body is used for the manifold, and the CVT-20 Series externally heated nozzles serve as the drops, instead of using nozzles embedded in the MGN manifold. This provides design flexibility and longer nozzle lengths for applications with close-pitch requirements.
Plastic Engineering & Technical Services brought out the EvenFlow variable-speed programmer for valve gates (see April Keeping Up for details). And Polyshot Corp. showed its new single-nozzle valve gates .
Plastics processors are finding applications for 3D printing around the plant and across the supply chain. Here are 8 examples to look for at NPE2024.
Learn about sustainable scrap reprocessing—this resource offers a deep dive into everything from granulator types and options, to service tips, videos and technical articles.
Resin drying is a crucial, but often-misunderstood area. This collection includes details on why and what you need to dry, how to specify a dryer, and best practices.
The aim of this presentation is to guide you through the factors and the numbers that will help you determine if a robot is a smart investment for your application. Agenda: Why are you considering automation? What problems are you trying to solve? How and why automation can help Crunch the numbers and determine the ROI
HANDY ITEMS FOR MOLD SHOPS ToolingDocs, PCIC Group’s mold-maintenance training specialists, has come out with its first line of hardware products for tool shops. These include toolroom benches with standardized design, developed to enable more efficient mold assembly and disassembly. Optional features include tool storage, water manifold and flowmeter, air manifold, and electrical hookups.
Mold-Masters’ new Summit Series premium hot-runner system is stainless steel with cast-in heaters embedded in copper. With valve or thermal gating, it’s aimed particularly at medical applications and boasts unusual thermal uniformity for trouble-free processing of sensitive resins.
In this collection, which is part one of a series representing some of John’s finest work, we present you with five articles that we think you will refer to time and again as you look to solve problems, cut cycle times and improve the quality of the parts you mold.
Multiple speakers at Molding 2023 will address the ways simulation can impact material substitution decisions, process profitability and simplification of mold design.
In this collection, which is part one of a series representing some of John’s finest work, we present you with five articles that we think you will refer to time and again as you look to solve problems, cut cycle times and improve the quality of the parts you mold.
When determining the best ejection option for a tool, molders must consider the ejector’s surface area, location and style.
technotrans says climate protection, energy efficiency and customization will be key discussion topics at PTXPO as it displays its protemp flow 6 ultrasonic eco and the teco cs 90t 9.1 TCUs.
Coverage of single-use plastics can be both misleading and demoralizing. Here are 10 tips for changing the perception of the plastics industry at your company and in your community.
As reported in March, MHT Mold & Hotrunner Technology showed off cavitation upgrade sets for Husky HyPET preform molds and new pre-engineered manifold systems for quick delivery and modest cost.
Synventive Molding Solutions introduced nuGate and hGate controls (pneumatic and hydraulic, respectively) for full control of valve-gate pin speed, acceleration, and stroke in both opening and closing. These complement its eGate electric version. Also reported in March was a new line of modular Plug’n Play actuators for valve gates that are pre-plumbed, prewired, and pretested. A third new product is SynCool 3 passive cooling for Synventive’s new hydraulic and pneumatic valve-gate actuators.
August 29-30 in Minneapolis all things injection molding and moldmaking will be happening at the Hyatt Regency — check out who’s speaking on what topics today.
Exhibitors and presenters at the plastics show emphasized 3D printing as a complement and aid to more traditional production processes.
Another passive cooling system for valve-gate actuators is the new SynCool3 from Synventive. The wavy aluminum conductor contacts the top plate or platen. No water cooling needed.
Join Engel in exploring the future of battery molding technology. Discover advancements in thermoplastic composites for battery housings, innovative automation solutions and the latest in large-tonnage equipment designed for e-mobility — all with a focus on cost-efficient solutions. Agenda: Learn about cutting-edge thermoplastic composites for durable, sustainable and cost-efficient battery housings Explore advanced automation concepts for efficient and scalable production See the latest large-tonnage equipment and technology innovations for e-mobility solutions
While the melting process does not provide perfect mixing, this study shows that mixing is indeed initiated during melting.
This Knowledge Center provides an overview of the considerations needed to understand the purchase, operation, and maintenance of a process cooling system.
In this collection of content, we provide expert advice on welding from some of the leading authorities in the field, with tips on such matters as controls, as well as insights on how to solve common problems in welding.
Mixed in among thought leaders from leading suppliers to injection molders and mold makers at the 2023 Molding and MoldMaking conferences will be molders and toolmakers themselves.
Several new standardized mold components from Hasco America were reported in March Keeping Up, as were new components from DME, quick-change mold clamps from Lenzkes Clamping Tools, unscrewing devices from Superior Die Set Corp., and a rust preventive for molds from MetalRustGuard,, shown by DMS Components. New air poppet valves for part release were shown by Cumsa USA, as reported in February Keeping Up. New sensors with replaceable cables—or no cables at all—were introduced by Kistler.
Join Wittmann for an engaging webinar on the transformative impact of manufacturing execution systems (MES) in the plastic injection molding industry. Discover how MES enhances production efficiency, quality control and real-time monitoring while also reducing downtime. It will explore the integration of MES with existing systems, emphasizing compliance and traceability for automotive and medical sectors. Learn about the latest advancements in IoT and AI technologies and how they drive innovation and continuous improvement in MES. Agenda: Overview of MES benefits What is MES? Definition, role and brief history Historical perspective and evolution Longevity and analytics Connectivity: importance, standards and integration Advantages of MES: efficiency, real-time data, traceability and cost savings Emerging technologies: IoT and AI in MES
An unusual “variable-pitch” manifold (HPS III-FleX) with hinged arms, aimed at two-cavity prototype and short-run production, was brought to the U.S. by Ewikon Molding Technologies. Also shown was the MWB 100 mini fluidized-bed cleaning oven for nozzle tips (details on both in January Fakuma Close Up).
Despite price increase nominations going into second quarter, it appeared there was potential for generally flat pricing with the exception of a major downward correction for PP.
Mike Sepe has authored more than 25 ANTEC papers and more than 250 articles illustrating the importance of this interdisciplanary approach. In this collection, we present some of his best work during the years he has been contributing for Plastics Technology Magazine.
Mold maintenance is critical, and with this collection of content we’ve bundled some of the very best advice we’ve published on repairing, maintaining, evaluating and even hanging molds on injection molding machines.
Join KraussMaffei for an insightful webinar designed for industry professionals, engineers and anyone interested in the manufacturing processes of PVC pipes. This session will provide a comprehensive understanding of the technology behind the production of high-quality PVC pipes: from raw material preparation to final product testing. Agenda: Introduction to PVC extrusion: overview of the basic principles of PVC pipe extrusion — including the process of melting and shaping PVC resin into pipe forms Equipment and machinery: detailed explanation of the key equipment involved — such as extruders, dies and cooling systems — and their roles in the extrusion process Process parameters: insight into the critical process parameters like temperature, pressure and cooling rates that influence the quality and consistency of the final PVC pipes Energy efficiency: examination of ways to save material and energy use when extruding PVC pipe products
The Plastics Industry Association (PLASTICS) has released final figures for NPE2024: The Plastics Show (May 6-10; Orlando) that officially make it the largest ever NPE in several key metrics.
Plastics Technology covers technical and business Information for Plastics Processors in Injection Molding, Extrusion, Blow Molding, Plastic Additives, Compounding, Plastic Materials, and Resin Pricing. About Us
Plastics Technology’s Tech Days is back! Every Tuesday in October, a series of five online presentations will be given by industry supplier around the following topics: Injection Molding — New Technologies, Efficiencies Film Extrusion — New Technologies, Efficiencies Upstream/Downstream Operations Injection Molding — Sustainability Extrusion — Compounding Coming out of NPE2024, PT identified a variety of topics, technologies and trends that are driving and shaping the evolution of plastic products manufacturing — from recycling/recyclability and energy optimization to AI-based process control and automation implementation. PT Tech Days is designed to provide a robust, curated, accessible platform through which plastics professionals can explore these trends, have direct access to subject-matter experts and develop strategies for applying solutions in their operations.
SIMULATION & MOLDING ANALYSIS Besides the integration of valve-gate sequencing into Autodesk Moldflow, as noted above, other news in mold simulation includes a new Moldex 3D software release (R13.0) from CoreTech System of Taiwan and improved simulation of metal or ceramic powder injection molding (PIM) in Sigmasoft from Sigma Plastic Services. As reported in May Keeping Up, the software now predicts particle segregation in the mold.
• There’s also a new electric cylinder for use with all-electric machines. Another alternative to hydraulic actuation is high-pressure air.
Water flow and temperature monitoring is a new option for the Gammaflux G24 temperature controller. It’s a recommended safety feature to make sure that water and valve-gate seals are protected with adequate cooling.
The aim of this presentation is to guide you through the factors and the numbers that will help you determine if a robot is a smart investment for your application. Agenda: Why are you considering automation? What problems are you trying to solve? How and why automation can help Crunch the numbers and determine the ROI
In this collection of articles, two of the industry’s foremost authorities on screw design — Jim Frankand and Mark Spalding — offer their sage advice on screw design...what works, what doesn’t, and what to look for when things start going wrong.
Coverage of single-use plastics can be both misleading and demoralizing. Here are 10 tips for changing the perception of the plastics industry at your company and in your community.
• Also new are internally self-locking cylinders for the stationary side of the mold. More compact than competing units, the smallest holds 10 tons and the largest 70 tons, with air or hydraulic actuation.
Discover how artifical intelligence is revolutionizing plastics processing. Hear from industry experts on the future impact of AI on your operations and envision a fully interconnected plant.
• A new waterproof connector plate plugs into all cylinders on a mold. Indicator lights show the position of each cylinder, solving the problem of identifying which cylinder is not in position and is holding up the cycle, without the need for a skilled electrician.
Take a deep dive into all of the various aspects of part quoting to ensure you’ve got all the bases—as in costs—covered before preparing your customer’s quote for services.
Learn about sustainable scrap reprocessing—this resource offers a deep dive into everything from granulator types and options, to service tips, videos and technical articles.
Gammaflux brought out two new options that can be added to its G24 temperature controller. The Water Flow Monitor uses dual-output flow and temperature sensors to ensure proper water flow throughout the mold. Adequate mold cooling is essential to protect water and valve-gate seals from overheating and potential leakage. And consistent cooling is equally critical to consistent part quality. The monitor supports 16 analog channels (eight dual-output sensors) and includes data-logging capability. An optional second module would double the number of channels monitored.
This month’s resin pricing report includes PT’s quarterly check-in on select engineering resins, including nylon 6 and 66.
Other new products include a mold light bar with magnetic mounting and color-coded magnetic status tags for molds to indicate whether they are awaiting maintenance, obsolete, or ready to run. ToolingDocs also offers a food/medical-grade mold grease, as well as the latest v6 of its MoldTrax mold-tracking software (see April Keeping Up).
In this collection of content, we provide expert advice on welding from some of the leading authorities in the field, with tips on such matters as controls, as well as insights on how to solve common problems in welding.
While the melting process does not provide perfect mixing, this study shows that mixing is indeed initiated during melting.
Due for release in the third or fourth quarter is a technology being developed by Milacron called SmartMold. It reportedly will be able to provide a wider range of information about a mold than has been available before—contactless wet-cycle counting, over-pressurization, overheating, over-tonnage, and abuse of the mold, such as slam closing. SmartMold will be able to communicate with the press, dryer, and chiller; and it will allow remote monitoring of the mold via “Cloud” reporting to automatically notify both the user and supplier of pending need for parts or service.
Across all process types, sustainability was a big theme at NPE2024. But there was plenty to see in automation and artificial intelligence as well.
Join this webinar to explore the transformative benefits of retrofitting your existing injection molding machines (IMMs). Engel will guide you through upgrading your equipment to enhance monitoring, control and adaptability — all while integrating digital technologies. You'll learn about the latest trends in IMM retrofitting (including Euromap interfaces and plasticizing retrofits) and discover how to future-proof your machines for a competitive edge. With insights from industry experts, it'll walk you through the decision-making process, ensuring you make informed choices that drive your business forward. Agenda: Maximize the value of your current IMMs through strategic retrofitting Learn how to integrate digital technologies to enhance monitoring and control Explore the benefits of Euromap interfaces and plasticizing retrofits Understand how retrofitting can help meet new product demands and improve adaptability Discover how Engel can support your retrofitting needs, from free consultations to execution
Ultradent's entry of its Umbrella cheek retractor took home the awards for Technical Sophistication and Achievement in Economics and Efficiency at PTXPO.
While prices moved up for three of the five commodity resins, there was potential for a flat trajectory for the rest of the third quarter.
Toshiba also molded parts in 3D printed cavities. What’s more, it used a six-axis robot to switch out plastic and steel cavities in a quick-change mold base.
Unlike SynCool 1 and 2, it uses no water-cooling plate and thereby both improves manifold temperature control and eliminates seal failures caused by clogged cooling circuits. This patent-pending system uses an aluminum heat conductor with a wavy geometry that contacts the top plate or platen. In addition, a titanium standoff inhibits thermal transfer to the cylinder (see photo). It’s aimed at polyolefin applications up to 250 C (482 F).
Say “manufacturing automation” and thoughts immediately go to the shop floor and specialized production equipment, robotics and material handling systems. But there is another realm of possible automation — the front office.
While the major correction in PP prices was finally underway, generally stable pricing was anticipated for the other four commodity resins.
If you’re interested in lightweight composites, IML, LSR, multi-shot, inmold assembly, barrier coinjection, micromolding, variotherm molding, foams, energy-saving presses, robots, hot runners, and tooling—they’re all here in force.
Two exhibitors demonstrated prototype or short-run molding with 3D-printed cavity inserts made of modified ABS using a Stratasys Polyjet machine. Such inserts are said to be durable enough for 500 shots, though cycles are relatively long, due to limited heat transfer. Milacron showed how cavities can be printed in 5 hr and then cleaned, inspected, and loaded into a quick-change DME MUD mold base, which was run in a 17-ton Roboshot all-electric press. Cycle time was around 100 sec.
Every time a polymer is heated, sheared or stressed during recycling, its original molecular structure can change. These changes affect physical properties such as impact and tensile strength. They also affect melt flow—a key factor in efficient throughput and the complete filling of a mold. Further, recycling can cause a material’s color to change, which can limit the applications in which PCR material is used. Other visual properties, such as gloss or clarity, can suffer as well.
MHS Hot Runner Solutions debuted a larger size of its Rheo-Pro Black Box pneumatic valve-gate actuator, which can process materials such as PEEK, LCP, PSU, PEI, and PPS at up to 450 C (842 F) in the hot runner and 200 C (392 F) in the mold without need of cooling. The initial smaller version was introduced at K 2013.
Hundreds of tons of demonstration products will be created this week. Commercial Plastics Recycling is striving to recycle ALL of it.
There’s no letup in development of sophisticated hot-runner nozzles and controls. Here’s news in these and other tooling products at the show.
In this collection of articles, two of the industry’s foremost authorities on screw design — Jim Frankand and Mark Spalding — offer their sage advice on screw design...what works, what doesn’t, and what to look for when things start going wrong.
HRSflow of Italy announced that its Flexflow servo-electric valve-gate system has been integrated into Autodesk Moldflow simulation software. Moldflow now can simulate the gradual opening and closing of nozzles, which are individually programmable for speed, force, and position. Flexflow is aimed at large, thin-wall automotive parts.
Additive technology creates air pockets in film during orientation, cutting down on the amount of resin needed while boosting opacity, mechanical properties and recyclability.
One argument against using PCR content is the potential impact on high-speed injection molding, blow molding and extrusion processes. PCR material with poor melt flow can slow throughput. The addition of a stabilizer can help prevent this issue.
Introduced by Zeiger and Spark Industries at the PTXPO, the nozzle is designed for maximum heat transfer and uniformity with a continuous taper for self cleaning.
Plastics Technology covers technical and business Information for Plastics Processors in Injection Molding, Extrusion, Blow Molding, Plastic Additives, Compounding, Plastic Materials, and Resin Pricing. About Us
A third new development from Männer is the MCN-P valve-gate nozzle for thin-wall packaging molded at high injection pressures and speeds. In lengths of 79 to 404 mm (vs. a max. of 304 mm previously), it has a screw-on tip and boasts an improved temperature profile, a highly wear-resistant design, and an additional guiding ring for the pin under the nozzle tip for superior gate quality.
When a resin is made by a polymer producer, its structure is highly controlled to provide excellent consistency in physical and visual properties. It is also often accompanied by a base level of stabilizer blends, which allow these properties to remain unaffected by the harsh process conditions the resin will be subjected to during its conversion to the final product.
• A primary antioxidant, which is active in the processed article. These antioxidants prevent auto-oxidation by capturing oxygen-centered free radicals that propagate the degradation chain reaction.
Successfully starting or restarting an injection molding machine is less about ticking boxes on a rote checklist and more about individually assessing each processing scenario and its unique variables.
• V450CM compact heavy-duty cylinders have a new option whereby mechanical switches are built into the cylinder. They send a signal to the machine so that it knows their position. These units withstand temperatures up to 320 F and pressures up to 6500 psi.
However, the recycling industry is demonstrating stronger support for the use of stabilizers. Chemical stabilizers help advance four important goals of the Association of Plastic Recyclers (APR) to improve the plastics circular economy: increasing supply, enhancing quality, expanding demand and communicating value. Stabilization expands potential uses for PCR content, due to the material’s higher quality vs. degraded resin, and enables more content to be reused for higher-value applications.
Other hot-runner news from Milacron includes a newly optimized dual-gate solution for the Mold-Masters Melt Cube. It feeds long, hollow parts like pipettes and syringe barrels from two sides. Previously, each Melt Cube contained one nozzle for each part, but now it contains two nozzles facing in opposite directions. Lower capital investment is said to result.
Despite price increase nominations going into second quarter, it appeared there was potential for generally flat pricing with the exception of a major downward correction for PP.
MOLDS & COMPONENTS Interesting news for PET preform molders was Husky’s self-cleaning mold. As reported in our May show Close Up, controlled flashing of the neck-ring area cleans up mold deposits in one cycle, saving hundreds of hours of maintenance per year.
• A secondary antioxidant, which works during the melt phase. It destroys hydroperoxides generated during the melt, which would otherwise destroy the primary antioxidant. Secondary antioxidants also help to delay the formation of quinones, a color-changing biproduct that forms when primary antioxidants are consumed.
However, Husky’s big news in controls was the Altanium servo control, which Husky calls “the first integrated temperature and servo controller.” It controls all servo axes in the mold—not just valve gates, but also collapsible cores, slides, unscrewing, stack rotation, and coining motions.
Some recyclers use stabilization technology to improve the quality of their PCR material or to meet customer requests, while others do not—either because their customers are not asking for stabilized PCR content or to avoid adding costs to their product in a market with slim profit margins.
Core Technology Molding turned to Mold-Masters E-Multi auxiliary injection unit to help it win a job and dramatically change its process.
The second new G24 option is a machine-mount bracket to move the controller off the floor, saving floorspace, and especially useful in cleanrooms.
In a time where sustainability is no longer just a buzzword, the food and beverage packaging industry is required to be at the forefront of this innovation. By adopting circular packaging processes and solutions, producers can meet regulatory requirements while also satisfying consumer demand and enhancing brand reputation. Join Husky to learn more about the broader implications of the circular economy — as well as how leading brands are leveraging this opportunity to reduce costs, increase design flexibility and boost product differentiation. Agenda: The cost and operational benefits of embracing circularity Key materials in circular packaging — including rPET and emerging bioplastics How to design a circular food and beverage package Strategies for selecting sustainable closures to future-proof packaging solutions Optimization and streamlining of production processes for enhanced efficiency How Husky Technologies can enable your sustainable success
MHS Hot Runner Solutions debuted a larger size of its Rheo-Pro Black Box pneumatic valve-gate actuator, which can process materials such as PEEK, LCP, PSU, PEI, and PPS at up to 450 C (842 F) in the hot runner and 200 C (392 F) in the mold without water cooling.
One concern about the use of stabilizers is the potential contamination effects they may have on recyclability. As to be expected, many stakeholders are cautious about contaminating the recycle stream, and industry groups are continuously working to provide practical guidelines. However, additives are becoming an increasingly valuable tool for users of recycled material. Many additives can be used at reasonable levels during resin production while still permitting the material to be recyclable. These additives include stabilizers, nucleating agents, lubricants and impact modifiers.
When, how, what and why to automate — leading robotics suppliers and forward-thinking moldmakers will share their insights on automating manufacturing at collocated event.
This month’s resin pricing report includes PT’s quarterly check-in on select engineering resins, including nylon 6 and 66.
Join KraussMaffei for an insightful webinar designed for industry professionals, engineers and anyone interested in the manufacturing processes of PVC pipes. This session will provide a comprehensive understanding of the technology behind the production of high-quality PVC pipes: from raw material preparation to final product testing. Agenda: Introduction to PVC extrusion: overview of the basic principles of PVC pipe extrusion — including the process of melting and shaping PVC resin into pipe forms Equipment and machinery: detailed explanation of the key equipment involved — such as extruders, dies and cooling systems — and their roles in the extrusion process Process parameters: insight into the critical process parameters like temperature, pressure and cooling rates that influence the quality and consistency of the final PVC pipes Energy efficiency: examination of ways to save material and energy use when extruding PVC pipe products
technotrans says climate protection, energy efficiency and customization will be key discussion topics at PTXPO as it displays its protemp flow 6 ultrasonic eco and the teco cs 90t 9.1 TCUs.
For instance, the American Association of State Highway and Transportation Officials (AASHTO) adopted new specifications to account for possible failure modes of corrugated HDPE pipes that incorporate recycled content. The new specifications now include a requirement for a minimum length of oxidative induction time, a measure of the level of stabilization present in a resin. The Association recognized that polymer stability was needed to prevent chemical failure in these pipes, or else the use of recycled HDPE would be a liability. Adding stabilizers helps HDPE recyclers meet these stringent requirements and encourages the use of recycled HDPE in drainage pipes by enabling long lifespans.
Across the show, sustainability ruled in new materials technology, from polyolefins and engineering resins to biobased materials.
Second quarter started with price hikes in PE and the four volume engineering resins, but relatively stable pricing was largely expected by the quarter’s end.
Chemical stabilizers can prevent or minimize these undesirable effects. They can optimize melt flow for better processing, preserve physical properties that support better application performance, and prevent or minimize oxidative degradation that can lead to cracking and failure.
Also new from Männer is its smallest Slimline nozzle yet for engineering resins, with 8 mm diam. and 16 mm pitch. (This size was already available for polyolefins.) Improved temperature profile allows these small nozzles to be up to 164 mm long.
After successfully introducing a combined conference for moldmakers and injection molders in 2022, Plastics Technology and MoldMaking Technology are once again joining forces for a tooling/molding two-for-one.
Männer’s new Edgeline valve-gate nozzles are for side injection of long, narrow, tubular parts like syringe barrels. Available with one, two, and four drops per nozzle, they allow for compact, high-cavitation layouts.
New line of toolroom products from ToolingDocs includes standardized mold-repair benches with optional utilities and mold-storage space, as well as magnetic mold-status tags and a light bar.
Also, Husky’s new Unify pre-assembled manifold system signals the company’s re-entry into automotive technical parts—i.e., precision molding of engineering resins.
These humble but essential fasteners used in injection molds are known by various names and used for a number of purposes.
Mold maintenance is critical, and with this collection of content we’ve bundled some of the very best advice we’ve published on repairing, maintaining, evaluating and even hanging molds on injection molding machines.
The properties of PCR content, such as melt flow, color and contamination, are directly related to proper stabilization.
Across all process types, sustainability was a big theme at NPE2024. But there was plenty to see in automation and artificial intelligence as well.
Say “manufacturing automation” and thoughts immediately go to the shop floor and specialized production equipment, robotics and material handling systems. But there is another realm of possible automation — the front office.
In controls, Husky presented the latest enhancements to its Altanium Matrix2, a high-end system for high-cavitation molds (up to 254 zones). Measurement and control accuracy are said to be even better than before, while new H-Series circuit cards provide more features in a smaller footprint. Added safety features enhance diagnostics and fault mitigation.
Core Technology Molding turned to Mold-Masters E-Multi auxiliary injection unit to help it win a job and dramatically change its process.
Thousands of people visit our Supplier Guide every day to source equipment and materials. Get in front of them with a free company profile.
Join Wittmann for an engaging webinar on the transformative impact of manufacturing execution systems (MES) in the plastic injection molding industry. Discover how MES enhances production efficiency, quality control and real-time monitoring while also reducing downtime. It will explore the integration of MES with existing systems, emphasizing compliance and traceability for automotive and medical sectors. Learn about the latest advancements in IoT and AI technologies and how they drive innovation and continuous improvement in MES. Agenda: Overview of MES benefits What is MES? Definition, role and brief history Historical perspective and evolution Longevity and analytics Connectivity: importance, standards and integration Advantages of MES: efficiency, real-time data, traceability and cost savings Emerging technologies: IoT and AI in MES
This Knowledge Center provides an overview of the considerations needed to understand the purchase, operation, and maintenance of a process cooling system.
While these infrastructure improvements are critical, PCR material stabilization is also vital to enable the plastics industry to produce the high-quality PCR material needed to meet brands’ requirements. Effective stabilization can:
The series comes in three sizes—femto, pico, and centi. Manifolds use iFlow technology—curved flow channels rather than straight gun-drilled passages. Full hot halves come with a special coating on valve-pin front ends for corrosion resistance and durability.
When, how, what and why to automate — leading robotics suppliers and forward-thinking moldmakers will share their insights on automating manufacturing at collocated event.
Join Engel in exploring the future of battery molding technology. Discover advancements in thermoplastic composites for battery housings, innovative automation solutions and the latest in large-tonnage equipment designed for e-mobility — all with a focus on cost-efficient solutions. Agenda: Learn about cutting-edge thermoplastic composites for durable, sustainable and cost-efficient battery housings Explore advanced automation concepts for efficient and scalable production See the latest large-tonnage equipment and technology innovations for e-mobility solutions
Thousands of people visit our Supplier Guide every day to source equipment and materials. Get in front of them with a free company profile.
Multiple speakers at Molding 2023 will address the ways simulation can impact material substitution decisions, process profitability and simplification of mold design.
Edgeline is a new generation of valve-gate nozzles for side injection from Männer of Germany. It’s aimed at long, narrow, tubular parts like syringe barrels. The valve pins move at right angles to the mold parting line. It’s available with one, two, and four drops per nozzle, allowing for compact, high-cavitation layouts (see photo). Multi-drop nozzles have a single pneumatically actuated pin to open and close all gates simultaneously, though temperatures are individually controlled. Edgeline is said to perform well with resins such as COP, COC, PMMA, PC, and TPE.
Processors with sustainability goals or mandates have a number of ways to reach their goals. Biopolymers are among them.
After successfully introducing a combined conference for moldmakers and injection molders in 2022, Plastics Technology and MoldMaking Technology are once again joining forces for a tooling/molding two-for-one.
Additive technology creates air pockets in film during orientation, cutting down on the amount of resin needed while boosting opacity, mechanical properties and recyclability.
Introduced by Zeiger and Spark Industries at the PTXPO, the nozzle is designed for maximum heat transfer and uniformity with a continuous taper for self cleaning.
Successfully starting or restarting an injection molding machine is less about ticking boxes on a rote checklist and more about individually assessing each processing scenario and its unique variables.
Yudo of Korea recently began using fusion bonding to manufacture complete hot halves. This approach combines two separate plates and allows for polishing the flow channels in both plates so there are no dead spots, which facilitates quicker color changes. Similarly, Yudo has begun using brazing to produce core and cavity inserts by bonding two pieces. This enables cooling channels to be introduced in places that would not be possible with conventional gun-drilled channels.
There’s a lot more to these humble but essential mold components than you might suspect. Following the author’s tips could save much time, money and frustration.
Despite countervailing forces such as lower virgin resin prices, strong demand continues for post-consumer recycled (PCR) content in applications such as packaging, pipe and furniture. One reason is the commitment by major brands to address consumer demands for sustainable products and packaging. Also, there are new regulations that encourage the reuse of plastics to support circularity. For instance, in 2022, the UK will introduce a Plastic Packaging Tax to incentivize the incorporation of recycled plastic. Also, the Council of the European Union (EU) adopted a directive in 2019 that introduces upcoming restrictions on certain single-use plastic products. It includes targets for plastic bottles to contain at least 25% recycled content by 2025 and 30% by 2030.
Plastics Technology’s Tech Days is back! Every Tuesday in October, a series of five online presentations will be given by industry supplier around the following topics: Injection Molding — New Technologies, Efficiencies Film Extrusion — New Technologies, Efficiencies Upstream/Downstream Operations Injection Molding — Sustainability Extrusion — Compounding Coming out of NPE2024, PT identified a variety of topics, technologies and trends that are driving and shaping the evolution of plastic products manufacturing — from recycling/recyclability and energy optimization to AI-based process control and automation implementation. PT Tech Days is designed to provide a robust, curated, accessible platform through which plastics professionals can explore these trends, have direct access to subject-matter experts and develop strategies for applying solutions in their operations.
St. Joseph Plastics grew from a simple grinding operation and now pursues growing markets in recycled PP, food-grade recycled materials, and customized post-industrial and post-consumer compounds.
Although not new, Mitsubishi Heavy Industries demonstrated an interesting technique called Sequential Cavity Separation (SCS), which uses valve gates in a family mold to inject two similar or different parts in sequence. This “shared tonnage” approach uses less clamp force than if both parts were injected simultaneously. At the show, a 720-ton ME2+ all-electric machine molded 16-in.-diam. PC relish trays using no more than 400 tons of force for a job that would normally require 900 tons. SCS can permit independent injection profiles for each cavity. And even if both parts are identical, SCS can be valuable for weight-critical applications, such as fan blades, because separate injection provides tighter shot control for each part, according to MHI.
I conclude this three-part examination of real-world problems and solutions involving hot runners by focusing on heaters, thermocouples, and controls. Part 3 of 3.
From hot runners to self-cleaning PET preform molds to 3D-printed plastic cavity inserts, there was plenty of cutting-edge tooling technology on display at NPE2015 in Orlando, Fla., in March. In hot runners, key themes were data storage in the “cloud,” individual adjustability of valve-gate opening and closing, and multi-tip nozzles for molding long, thin, tubular products such as medical pipettes and syringes. Valve-gate actuators without water cooling also made debuts. Here is additional news on these topics, supplementing what has been published in previous issues.
Formnext Chicago is an industrial additive manufacturing expo taking place April 8-10, 2025 at McCormick Place in Chicago, Illinois. Formnext Chicago is the second in a series of Formnext events in the U.S. being produced by Mesago Messe Frankfurt, AMT – The Association For Manufacturing Technology, and Gardner Business Media (our publisher).
Husky’s new Ultra Helix servo-actuated valve-gate nozzle reportedly offers the least gate vestige, the longest operating life, and easier mold integration than ever before
Heitec of Germany, represented in North America by Technoject Machinery Corp., showcased a new two-drop valve-gate system with linear electricVisio-NV-Drive, which can delay valve-opening time by adjustable increments of 0.01 sec and can set valve-pin end position in increments of 0.01 mm.
The main new hot-runner product of Husky Injection Molding Systems was the Ultra Helix nozzle. This servo-actuated valve gate reportedly permits direct gating parts with a gate vestige so slight as to be “often unmeasurable,” according to the company, which also claims that “this level of gate quality lasts for millions of cycles—longer than any other valve gate currently available.” Husky says tests show the median gate vestige is 0.0 mm in 65% of parts and the maximum vestige is less than on 85% of parts molded with other valve gates, including earlier Husky models. Nozzles should need no replacement parts for more than 5 million cycles, Husky asserts.
Stabilizer packages can support the current version of the resin while enhancing future uses. One example is post-consumer HDPE bottles that are sorted, ground, washed, dried and then extruded into a fractional-melt pellet. To increase the flow of fractional-melt HDPE, metal stearates such as calcium stearate and zinc stearate that have lubricative properties can be used. These additives have the added benefit of being great acid scavengers, helping to protect stabilizer systems and prevent equipment corrosion.
As reported in our March preview, Athena Controls showed off a new version of its Bedros controller with eight to 64 zones and “Cloud”-enabled software. Also reported in March was new Cloud-based software for Ion and Pulse controllers from Fast Heat . Wireless remote access to controllers and ability to predict failures before they happen are key features. Also new are CableXChecker and MoldXChecker, special diagnostic devices that quickly identify bad cables and thermocouple or heater short circuits, respectively, before the mold goes into the press.
In this three-part collection, veteran molder and moldmaker Jim Fattori brings to bear his 40+ years of on-the-job experience and provides molders his “from the trenches” perspective on on the why, where and how of venting injection molds. Take the trial-and-error out of the molding venting process.
• An antacid that will neutralize leftover catalyst residuals from polymer production. These residuals can negatively affect color and physical properties.
Tests with a seven-drop rear spoiler tool outfitted with additional pressure sensors verified the Moldflow prediction that gradual valve opening and closing produced lower and more homogeneous packing pressure than in conventional “cascade” hot-runner molding. The part was 4-mm-thick TPV with 20% talc. Benefits included better surface appearance, lower stress and warpage, and up to 20% lower clamp-force requirement. To demonstrate the value of Flexflow, HRSflow has installed spoiler tools for demonstrations at its sites in Italy, China, and Grand Rapids, Mich.
Mike Sepe has authored more than 25 ANTEC papers and more than 250 articles illustrating the importance of this interdisciplanary approach. In this collection, we present some of his best work during the years he has been contributing for Plastics Technology Magazine.
While prices moved up for three of the five commodity resins, there was potential for a flat trajectory for the rest of the third quarter.
An important benefit of stabilizing PCR content is expanded application possibilities. With effective stabilization, PCR material can be used in higher-value applications rather than downcycled into low-value parts.
Other news in nozzles from Husky includes adaptation of the Ultra Side Gate, introduced at NPE 2012, for stack molds. The angled tip helps more customers move away from cold runners, Husky says.
Often, the base stabilizer package is only sufficient for a single use and is depleted within the first use of the polymer. With an insufficient level of stabilizer in the polymer, harsh conditions during recycling can more aggressively degrade the material and damage its properties.
Formnext Chicago is an industrial additive manufacturing expo taking place April 8-10, 2025 at McCormick Place in Chicago, Illinois. Formnext Chicago is the second in a series of Formnext events in the U.S. being produced by Mesago Messe Frankfurt, AMT – The Association For Manufacturing Technology, and Gardner Business Media (our publisher).
While the major correction in PP prices was finally underway, generally stable pricing was anticipated for the other four commodity resins.
Join this webinar to explore the transformative benefits of retrofitting your existing injection molding machines (IMMs). Engel will guide you through upgrading your equipment to enhance monitoring, control and adaptability — all while integrating digital technologies. You'll learn about the latest trends in IMM retrofitting (including Euromap interfaces and plasticizing retrofits) and discover how to future-proof your machines for a competitive edge. With insights from industry experts, it'll walk you through the decision-making process, ensuring you make informed choices that drive your business forward. Agenda: Maximize the value of your current IMMs through strategic retrofitting Learn how to integrate digital technologies to enhance monitoring and control Explore the benefits of Euromap interfaces and plasticizing retrofits Understand how retrofitting can help meet new product demands and improve adaptability Discover how Engel can support your retrofitting needs, from free consultations to execution
Take a deep dive into all of the various aspects of part quoting to ensure you’ve got all the bases—as in costs—covered before preparing your customer’s quote for services.
New from Progressive Components and its sister company Roehr Tool Corp. are tiny Dove Tail (DT) collapsible cores (7-10 mm I.D.) to permit releasing very small threads and undercuts in caps, connectors, and medical parts. Also new is that Z-Series alignment locks are now guaranteed for the life of the mold.
Mixed in among thought leaders from leading suppliers to injection molders and mold makers at the 2023 Molding and MoldMaking conferences will be molders and toolmakers themselves.
Sustainability continues to dominate new additives technology, but upping performance is also evident. Most of the new additives have been targeted to commodity resins and particularly polyolefins.
While prices moved up for three of the five commodity resins, there was potential for a flat trajectory for the rest of the third quarter.
Sustainability continues to dominate new additives technology, but upping performance is also evident. Most of the new additives have been targeted to commodity resins and particularly polyolefins.
GETTING A QUOTE WITH LK-MOULD IS FREE AND SIMPLE.
FIND MORE OF OUR SERVICES:
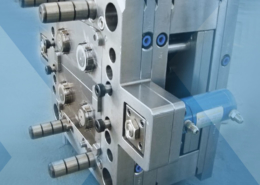
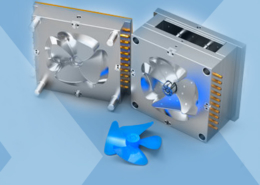
Plastic Molding

Rapid Prototyping
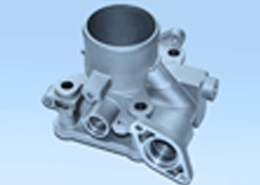
Pressure Die Casting
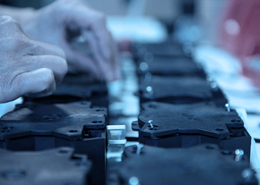
Parts Assembly
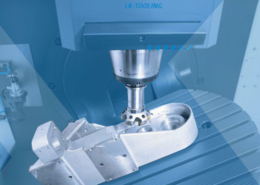