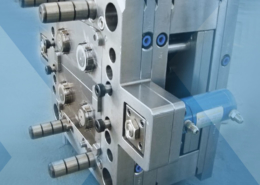
Metal Injection Molding (MIM) Market Analysis 2024-2032: - industrial injection
Author:gly Date: 2024-09-30
Röhm commissioned an acrylic resin (PMMA) plant of undisclosed capacity in Shanghai, China, in October 2023. China is the largest market for PMMA in the world. Röhm’s Plexiglass finds use in automotive lighting, appliance, and building and construction applications, and demand growth is such that Röhm COO Hans-Peter Hauck says another PMMA plant was due to start production in Worms, Germany, at the end of 2023.
Normally, this would require a very high level of injection pressure – at the expense of energy requirements and mould wear. This is why injection compression moulding is used for this application. Compared to classic injection moulding, this process requires significantly less injection pressure and it is possible to work with mould temperatures of 20 instead of 12 degrees Celsius. The special "Next Cycle IML" label can be completely separated from the PP of the cup during recycling, so that the product can be recycled by type after use. In contrast to thermoforming, no pre-produced foils are used and no stamping waste is produced.
Stephen has been with PlasticsToday and its preceding publications Modern Plastics and Injection Molding since 1992, throughout this time based in the Asia Pacific region, including stints in Japan, Australia, and his current location Singapore. His current beat focuses on automotive. Stephen is an avid folding bicycle rider, often taking his bike on overseas business trips, and a proud dachshund owner.
One of the world’s largest acrylonitrile-butadiene-styrene (ABS) plants was officially opened in November 2023 in Ningbo, China. The 600,000-tonnes/year site is a joint venture of Sinopec and Ineos Styrolution. This facility will produce high-end Terluran ABS grades that advance the design and functionality of many applications across numerous industry sectors, including automotive, electronics, household, healthcare, and toys/sports/leisure for the rapidly growing domestic market in China
Demand for medium- and high-modulus carbon fibers is rising in Europe, driven by a push toward a net-zero society. This growth is mainly due to higher build rates for commercial aircrafts (secondary structures and engines), as well as centrifuges for energy production, satellites, and high-end automobiles.
The exhibit uses a 4-cavity mould from Brink to produce thin-walled IML round cups from polypropylene (PP) using compression moulding at an injection pressure of just 23,000 psi (1,600 bar). For process monitoring, the mould is equipped with six high-resolution inductive position measuring and embossing sensors. Four moulded parts, each weighing 10.4 grams and with a wall thickness of only 0.37 millimetres, are produced in a cycle time of 3.95 seconds. The plastic has a biomass footprint and ISCC-certified. Also integrated into the production cell is a side-entry robot from Brink that inserts the labels, removes the finished cups and stacks them on a conveyor belt.
An electric Allrounder 720 A in the "Ultimate" performance variant demonstrates at NPE 2024 that high-quality injection moulding technology can be an alternative to thermoforming. The exhibit uses injection compression moulding to produce thin-walled IML cups that can be easily recycled after use.
Plastics may be coming under fire from all quarters, but that’s not stopping suppliers from expanding capacity for key resins and reinforcing materials serving major end-use industries such as automotive, appliances, E&E, and other sectors. Several key recent announcements follow.
In this particularly resource-saving application for the packaging industry, special emphasis was placed on energy efficiency and on a part design that saves materials. Thanks to the all-electric packaging machine in combination with injection compression moulding, the energy footprint is improved by 20 per cent with a significant reduction in part weight from 13 to 10.4 grams. Meanwhile, the flowpath/wall thickness ratio is 380:1.
The directly driven high-performance machine with a clamping force of 2,900 kN is equipped with a size 1300 injection unit that is specifically optimised for high performance. Thanks to high-precision servo motors from Arburg's sister company AMKmotion, very high injection volume flows and injection speeds of up to 400 millimetres per second can be achieved.
Toray Industries Inc. is expanding French subsidiary Toray Carbon Fibers Europe S.A.’s production facilities for regular to medium- and high-modulus carbon fibers. This move will increase annual capacity at the Abidos plant in southwest France from 5,000 to 6,000 tonnes/year. Production is expected to start in 2025.
In September 2023, ExxonMobil inaugurated its 400,000-tonnes/year Vistamaxx propylene-based elastomer plant in Baytown, TX, effectively more than doubling its overall capacity for the resin. The plant can also manufacture Exact ethylene-based elastomers that are widely used in impact modification for automotive compounds and solar module encapsulation. Vistamaxx itself is widely used in hygiene applications, construction materials such as roof membranes, and as a recycling additive.
GETTING A QUOTE WITH LK-MOULD IS FREE AND SIMPLE.
FIND MORE OF OUR SERVICES:
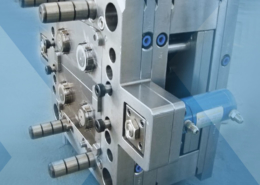
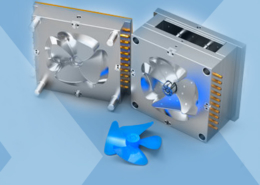
Plastic Molding

Rapid Prototyping
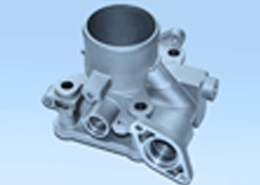
Pressure Die Casting
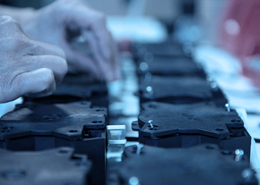
Parts Assembly
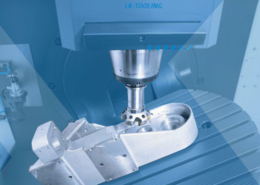