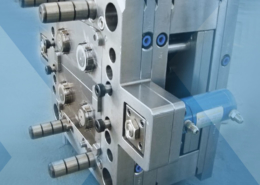
Merriott and Talisman team up to boost UK contract manufacturing - plastic injec
Author:gly Date: 2024-09-30
Any new materials also bring unknowns, especially in performance, and many bioresins may not perform as well as traditional materials in terms of product preservation, longevity, safety and other key metrics. These unknowns need to be addressed to achieve a successful bioresin adoption. Bioresins are not a straight replacement for PP and PE. Even within petrochemical based PE and PP, there is a wide variation in performance among the numerous grades. Make sure that the bioresin you’re choosing matches the requirements of the product that you’re bringing to market.
“We produce under cleanroom conditions in the process. Thus, when the mould is open, no grain of dust can get between the coating and the substrate surface. We thus achieve very low reject rates,” Luckner said.
Conduct an in-depth review of the application and the bioresin itself prior to any manufacturing. This review ensures the hot runner and controller are optimized for the specific application and bioresin. This should include optimizing the manifold design for consistent preparation of the bioresin.
This may require more frequent equipment inspection and maintenance to ensure consistent and predictable uptime. PLA can cause damage to not just the hot runner and the mold but the screw and barrel as well. Basically, anything that touches the melt needs to be stainless steel or have a nonreactive coating.
When planning to use bioresins, it’s important to note a few distinctions in related terminology and features. Biobased refers to the fact that biomaterials are used to create the resin. Biodegradable means the item will eventually breakdown in the natural environment. Not all biobased resins are biodegradable. Compostable means the material is biodegradable and breaks down within three to six months in an industrial composting facility, releasing nutrients and leaving no toxicity in the soil. Not all biobased and biodegradable materials are compostable.
Plastics Technology covers technical and business Information for Plastics Processors in Injection Molding, Extrusion, Blow Molding, Plastic Additives, Compounding, Plastic Materials, and Resin Pricing. About Us
One of the most frequent mistakes we see is people thinking because bioresins replace PP and PE, they process similarly to those resins. Bioresins are more thermally sensitive, and their process window is smaller, so running them requires equipment that’s designed to deal with those constraints.
Discover how artifical intelligence is revolutionizing plastics processing. Hear from industry experts on the future impact of AI on your operations and envision a fully interconnected plant.
The Plastics Industry Association (PLASTICS) has released final figures for NPE2024: The Plastics Show (May 6-10; Orlando) that officially make it the largest ever NPE in several key metrics.
Techniplas has used the ColorForm process for several years – although the manufacturer refers to it as “ColorFuse” technology. There are four ColorForm systems in Treuen and one in Rüti, Switzerland. An in-house technical center in Treuen also uses two further systems.
The pressure requirements for processing the bioresin need to be evaluated because viscosities for these materials can be very different from standard polyolefins. Determine if the machine and hot runner being used can generate adequate pressure to process the material. In general, Husky recommends machines that can achieve pressures of at least 28,000 to 32,000 psi.
To optimize the application, an in-depth review of the component and the bioresin should be conducted, including a cavity-fill analysis of the part design to verify all features are compatible with the rheology of the chosen bioresin. The bioresin supplier should be able to characterize flow characteristics, and ideally, the simulation will model the actual resin and not a substitute material. The need for a resin trial can also be evaluated — a step that is usually recommended for resins with limited performance data or in particularly challenging applications.
In this collection of content, we provide expert advice on welding from some of the leading authorities in the field, with tips on such matters as controls, as well as insights on how to solve common problems in welding.
What’s driving the growth in bioresin adoption? First are consumers who want to know that the product they purchased, as well as its packaging, is sustainable. Because bioresins are derived from relatively sustainable materials and can be engineered to biodegrade, many consumers feel bioresins are a more sustainable choice.
Demand for bioresins is growing in molded goods, particularly as a sustainability play to replace fossil-fuel based materials, but these materials are not a drop-in replacement for traditional materials. Molds and hot runners need to be optimized for these materials.
August 29-30 in Minneapolis all things injection molding and moldmaking will be happening at the Hyatt Regency — check out who’s speaking on what topics today.
Bioresins come with unique and challenging physical properties that can make them difficult to incorporate into the injection molding process. For example, many bioresins are highly viscous and require high pressures to fill the mold cavities. They’re also prone to weepage and leakage. In terms of manufacturability, some bioresins are very temperature sensitive, so the manufacturing process must avoid exceeding temperatures above a certain threshold.
A sit-down with bioplastic producer Danimer Scientific showed me there are more possible answers to that question than I had previously thought.
In addition, it is best for the hot runner controller to be tied into the injection molding machine’s control. This is recommended because if the machine goes down for a predetermined amount of time without an operator, when the molder restarts the press, it’s best to have the controller automatically put the heat in standby on the hot runner to prevent material degradation during the idle.
Sustainability continues to dominate new additives technology, but upping performance is also evident. Most of the new additives have been targeted to commodity resins and particularly polyolefins.
Also, remember that the corrosiveness of the resin goes up almost exponentially as it degrades, making the ability to flush any degraded resin out important. Degraded bioresins will attack the steel components in the hot runner and can also damage the mold if injected.
In this three-part collection, veteran molder and moldmaker Jim Fattori brings to bear his 40+ years of on-the-job experience and provides molders his “from the trenches” perspective on on the why, where and how of venting injection molds. Take the trial-and-error out of the molding venting process.
Stainless steel hot runner systems, like this UltraMelt system designed by Husky Technologies, can resist the corrosive nature of some degraded bioresins. Photo Credit: Husky
In a time where sustainability is no longer just a buzzword, the food and beverage packaging industry is required to be at the forefront of this innovation. By adopting circular packaging processes and solutions, producers can meet regulatory requirements while also satisfying consumer demand and enhancing brand reputation. Join Husky to learn more about the broader implications of the circular economy — as well as how leading brands are leveraging this opportunity to reduce costs, increase design flexibility and boost product differentiation. Agenda: The cost and operational benefits of embracing circularity Key materials in circular packaging — including rPET and emerging bioplastics How to design a circular food and beverage package Strategies for selecting sustainable closures to future-proof packaging solutions Optimization and streamlining of production processes for enhanced efficiency How Husky Technologies can enable your sustainable success
Beyond Plastic and partners have created a certified biodegradable PHA compound that can be injection molded into 38-mm closures in a sub 6-second cycle from a multicavity hot runner tool.
Adding aPHA to PLA can boost a range of mechanical properties and expedite composting. Here are the details as well as processing guidelines for injection molding the blends.
"There, all necessary equipment is available on-site, and commissioning at the TechCenter was also completed on schedule – both for the injection moulding machine and for the PUR technology, that is, for the RimStar Flex with two MK 5-2K CCM mixing heads for simultaneous production of two components. This cannot be taken for granted under the current basic conditions determined by the pandemic," says Luckner.
Successfully starting or restarting an injection molding machine is less about ticking boxes on a rote checklist and more about individually assessing each processing scenario and its unique variables.
While the melting process does not provide perfect mixing, this study shows that mixing is indeed initiated during melting.
Despite price increase nominations going into second quarter, it appeared there was potential for generally flat pricing with the exception of a major downward correction for PP.
While the major correction in PP prices was finally underway, generally stable pricing was anticipated for the other four commodity resins.
Introduced by Zeiger and Spark Industries at the PTXPO, the nozzle is designed for maximum heat transfer and uniformity with a continuous taper for self cleaning.
The final driver is legislation. New legislation and regulations are placing pressure on manufacturers to reduce postconsumer waste and plastic pollution. In July 2021, for example, the European Commission implemented new laws that ban or restrict single-use products made from fossil-fuel-based polymers.
Across multiple industries and applications, bioresins have become increasingly popular alternatives to the traditional resins used in injection molding. The global market for bioresins has risen steadily over the years and is expected to continue that growth at an impressive rate. Over the next five years, the market is expected to double in size, with a compound annual growth rate (CAGR) of 17% in the U.S. and 13% in Europe.
Core Technology Molding turned to Mold-Masters E-Multi auxiliary injection unit to help it win a job and dramatically change its process.
In most applications, high- and low-density polyethylene (HDPE, LDPE), polystyrene (PS) and PET can be replaced by polylactic acid (PLA). PLA is one of the first bioresins to be commercialized, and its feedstock options include corn or maize, tapioca and sugar cane.
Processors with sustainability goals or mandates have a number of ways to reach their goals. Biopolymers are among them.
This month’s resin pricing report includes PT’s quarterly check-in on select engineering resins, including nylon 6 and 66.
Learn about sustainable scrap reprocessing—this resource offers a deep dive into everything from granulator types and options, to service tips, videos and technical articles.
Husky is currently working with many of the bioresin suppliers to test and validate their materials, including new formulations as they go to market. In its lab, Husky has around 45 different molds with different part configurations to test an assortment of resins and help customers determine if a particular bioresin is right for a specific application. Compostability testing with the bioresin you’ve chosen is possible and required for commercializing a product with a compostability certification.
“Our customers, major OEMs from the automotive industry, place the highest demands on quality. There must be no defects larger than 0.2mm on the entire transparent component. With the MXW 1000 in combination with the RimStar Flex for PUR metering, we fully meet these requirements,” added Toni Luckner, process developer at Techniplas in Treuen.
Mixed in among thought leaders from leading suppliers to injection molders and mold makers at the 2023 Molding and MoldMaking conferences will be molders and toolmakers themselves.
Join Engel in exploring the future of battery molding technology. Discover advancements in thermoplastic composites for battery housings, innovative automation solutions and the latest in large-tonnage equipment designed for e-mobility — all with a focus on cost-efficient solutions. Agenda: Learn about cutting-edge thermoplastic composites for durable, sustainable and cost-efficient battery housings Explore advanced automation concepts for efficient and scalable production See the latest large-tonnage equipment and technology innovations for e-mobility solutions
Say “manufacturing automation” and thoughts immediately go to the shop floor and specialized production equipment, robotics and material handling systems. But there is another realm of possible automation — the front office.
Exhibitors and presenters at the plastics show emphasized 3D printing as a complement and aid to more traditional production processes.
This Knowledge Center provides an overview of the considerations needed to understand the purchase, operation, and maintenance of a process cooling system.
Additive technology creates air pockets in film during orientation, cutting down on the amount of resin needed while boosting opacity, mechanical properties and recyclability.
"ColorForm technology offers great potential for a lower CO₂ footprint in the production of components with a noble, multifunctional surface," said Michael Fuchs, global application owner surface and lightweight at KraussMaffei. By consolidating the process down into one step, the user saves time and resource on intermediate storage, painting, and reworking of components. By using a transparent polyurethane surface treatment, Techniplas can also achieve ‘depth effects’ on the final component. The company uses the MXW 1000 ColorForm system at its Treuen, Saxony site.
Bioresins — sometimes called bioplastics, biopolymers or biomaterials — refer to several categories of commercially available materials that can be used in injection molding and other processes. So, what makes these plastics “bio”? The materials are made in whole or in part from renewable biological resources. These biological resources can include corn or maize, potato starch, tapioca starch, vegetable oil, sugar cane starch and wood pulp or cellulose among other feedstocks.
While prices moved up for three of the five commodity resins, there was potential for a flat trajectory for the rest of the third quarter.
Ultradent's entry of its Umbrella cheek retractor took home the awards for Technical Sophistication and Achievement in Economics and Efficiency at PTXPO.
The performance characteristics to be expected, including in areas such as pressure drop; shear rate in the hot runner; shear rate at the gate; and the temperature increase as a result of that shear rate can be derived. For thermal uniformity, a Finite Element Analysis (FEA) is a good predictor of manifold temperature variation due to the design of the hot runner. By adjusting the design — including the number of heater zones, thermocouple placement, melt channel layout sinks and manifold profile — the designer can optimize the thermal uniformity of the manifold prior to manufacturing.
Individual tip control is highly recommended for bioresins, as it would be for all temperature-sensitive resins. Improved heat distribution is required to control any overshoot, and the controller should be designed specifically for low-variation, high-temperature control to eliminate overshoots, if possible.
Derived from a variety of sustainable feedstocks, bioresins can be processed in various ways to meet the needs of many applications. Photo Credit: Husky
Thousands of people visit our Supplier Guide every day to source equipment and materials. Get in front of them with a free company profile.
The MXW 1000 was not just retrofitted for ColorForm technology. Its control system was also completely upgraded to KraussMaffei’s MC6 control system, and a new ORCA cooling system was installed. "The system performs a contact-free temperature measurement, which minimises maintenance. The technology allows us to control the twenty cooling circuits of the MXW precisely and thus makes a critical contribution to the high, uniform quality of the components," explained Luckner.
The corrosive properties of bioresins, particularly as they degrade, require melt-contact surfaces to use specialized coatings or be in stainless steel.
Join this webinar to explore the transformative benefits of retrofitting your existing injection molding machines (IMMs). Engel will guide you through upgrading your equipment to enhance monitoring, control and adaptability — all while integrating digital technologies. You'll learn about the latest trends in IMM retrofitting (including Euromap interfaces and plasticizing retrofits) and discover how to future-proof your machines for a competitive edge. With insights from industry experts, it'll walk you through the decision-making process, ensuring you make informed choices that drive your business forward. Agenda: Maximize the value of your current IMMs through strategic retrofitting Learn how to integrate digital technologies to enhance monitoring and control Explore the benefits of Euromap interfaces and plasticizing retrofits Understand how retrofitting can help meet new product demands and improve adaptability Discover how Engel can support your retrofitting needs, from free consultations to execution
Join Wittmann for an engaging webinar on the transformative impact of manufacturing execution systems (MES) in the plastic injection molding industry. Discover how MES enhances production efficiency, quality control and real-time monitoring while also reducing downtime. It will explore the integration of MES with existing systems, emphasizing compliance and traceability for automotive and medical sectors. Learn about the latest advancements in IoT and AI technologies and how they drive innovation and continuous improvement in MES. Agenda: Overview of MES benefits What is MES? Definition, role and brief history Historical perspective and evolution Longevity and analytics Connectivity: importance, standards and integration Advantages of MES: efficiency, real-time data, traceability and cost savings Emerging technologies: IoT and AI in MES
About the author: Sheldon Alexander is hot runners business manager for Husky. He has more than 20 years of global industry experience, traveling the world to help optimize injection molding applications for customers in more than 40 countries. Alexander has experience managing highly skilled teams across many functions in the injection molding value chain and holds several technical patents in the industry with specific expertise in hot runners. Contact: 905-951-5000; salexand@husky.co; www.husky.co
Resin drying is a crucial, but often-misunderstood area. This collection includes details on why and what you need to dry, how to specify a dryer, and best practices.
The partnership aims to bring together both companies’ technology platforms to produce FDCA from sustainable wood residues on an industrial scale.
In addition, the resin melt temperatures are relatively low and there is a comparatively low Delta T or difference between the melt and mold temperature. The next step is optimizing the hot runner and the controller for the bioresin, including using corrosive-resistant components and high-level melt management.
Multiple speakers at Molding 2023 will address the ways simulation can impact material substitution decisions, process profitability and simplification of mold design.
Join KraussMaffei for an insightful webinar designed for industry professionals, engineers and anyone interested in the manufacturing processes of PVC pipes. This session will provide a comprehensive understanding of the technology behind the production of high-quality PVC pipes: from raw material preparation to final product testing. Agenda: Introduction to PVC extrusion: overview of the basic principles of PVC pipe extrusion — including the process of melting and shaping PVC resin into pipe forms Equipment and machinery: detailed explanation of the key equipment involved — such as extruders, dies and cooling systems — and their roles in the extrusion process Process parameters: insight into the critical process parameters like temperature, pressure and cooling rates that influence the quality and consistency of the final PVC pipes Energy efficiency: examination of ways to save material and energy use when extruding PVC pipe products
“Our ColorForm system is used to produce parts using the injection compression moulding process, which are given a high-quality, transparent PUR surface for a special depth effect. Another line for the project is currently being commissioned,” said Luckner.
PE can be replaced with polyhydroxybutyrate (PHB) or polyhydroxyalkanoates (PHA), which are relatively newer resins on the market. These bioresins have more processing options and can offer compostability. PHA and PHB can be produced from corn; tapioca or potato starch; and vegetable oil. Many of the polypropylene (PP) parts molded today can be replaced with a cellulose resin made from wood pulp.
When, how, what and why to automate — leading robotics suppliers and forward-thinking moldmakers will share their insights on automating manufacturing at collocated event.
Across the show, sustainability ruled in new materials technology, from polyolefins and engineering resins to biobased materials.
ColorForm is KraussMaffei’s combination of injection moulding technology and surface finishing with polyurethane in a single step. The technology is designed to make large-scale production of high-quality components more economical and sustainable.
Second quarter started with price hikes in PE and the four volume engineering resins, but relatively stable pricing was largely expected by the quarter’s end.
technotrans says climate protection, energy efficiency and customization will be key discussion topics at PTXPO as it displays its protemp flow 6 ultrasonic eco and the teco cs 90t 9.1 TCUs.
In this collection of articles, two of the industry’s foremost authorities on screw design — Jim Frankand and Mark Spalding — offer their sage advice on screw design...what works, what doesn’t, and what to look for when things start going wrong.
You need to pay attention to the inherent characteristics of biopolymers PHA/PLA materials when setting process parameters to realize better and more consistent outcomes.
Gifted with extraordinary technical know how and an authoritative yet plain English writing style, in this collection of articles Fattori offers his insights on a variety of molding-related topics that are bound to make your days on the production floor go a little bit better.
Equipment impact is another area where bioresins may not initially meet the same standards as traditional materials. Molten bioresins tend to be corrosive, especially in the case of PLA, which can compromise machinery and lead to quality issues, performance variation and even component failure.
Plastics Technology’s Tech Days is back! Every Tuesday in October, a series of five online presentations will be given by industry supplier around the following topics: Injection Molding — New Technologies, Efficiencies Film Extrusion — New Technologies, Efficiencies Upstream/Downstream Operations Injection Molding — Sustainability Extrusion — Compounding Coming out of NPE2024, PT identified a variety of topics, technologies and trends that are driving and shaping the evolution of plastic products manufacturing — from recycling/recyclability and energy optimization to AI-based process control and automation implementation. PT Tech Days is designed to provide a robust, curated, accessible platform through which plastics professionals can explore these trends, have direct access to subject-matter experts and develop strategies for applying solutions in their operations.
After successfully introducing a combined conference for moldmakers and injection molders in 2022, Plastics Technology and MoldMaking Technology are once again joining forces for a tooling/molding two-for-one.
Using ColorForm tech means Techniplas doesn’t need to transport and paint components, or invest in a painting plant. The finished components are also ready for installation when they’re discharged from the automated production cell, saving on buffer storage and drying.
Mold maintenance is critical, and with this collection of content we’ve bundled some of the very best advice we’ve published on repairing, maintaining, evaluating and even hanging molds on injection molding machines.
The aim of this presentation is to guide you through the factors and the numbers that will help you determine if a robot is a smart investment for your application. Agenda: Why are you considering automation? What problems are you trying to solve? How and why automation can help Crunch the numbers and determine the ROI
Weepage and leakage are also an issue. This is partly due to the material’s corrosive nature, but also its molecular structure tends to weep or leak. In the case of a valve-gate system where there are moving parts, weepage is possible. When there are moving parts like valves, stems and bushings, their design needs to take into consideration the possibility of weepage.
Across all process types, sustainability was a big theme at NPE2024. But there was plenty to see in automation and artificial intelligence as well.
(Left to right) - Peter Giessmann (KraussMaffei), Eric Jan Frijters (Techniplas), Philipp Strasser (KraussMaffei), Michael Fuchs (KraussMaffei), Rene Rudolf (Techniplas), Sarah Seidel (Techniplas)
The ColorForm process effectively works by combining injection moulding and polyurethane processing. The multi-component injection moulding procedure is the foundation of this process. After injection moulding of the thermoplastic mould base body, the body is flow-coated with polyurethane (PUR) or polyurea (PUA) as the surface material in a second cycle.
The second driver is environmental, social and governance (ESG) initiatives. Brands and molders are under increasing pressure to adopt an ESG strategy. Using bioresins for injection molded products and packaging can help organizations meet their ESG objectives and signal to consumers that they’re doing their part for the environment.
Mike Sepe has authored more than 25 ANTEC papers and more than 250 articles illustrating the importance of this interdisciplanary approach. In this collection, we present some of his best work during the years he has been contributing for Plastics Technology Magazine.
The RimStar Flex ColorForm reaction process machine, which was designed specifically for this process, and the mixing head, feed the surface material (PUR/PUA) directly into the cavity. “RimStar systems take up very little space and meter even small amounts precisely and at a high cycle frequency,” said Philipp Strasser, global application owner, RPM and automotive at KraussMaffei.
If a color change will be required, the channels must be sized so the shear rates are on the high side, which results in proper scrubbing of the melt channels, expediting color switchovers. With these inputs and using the output from several software packages, the optimum geometry for the melt channel, including its layout and channel diameter, can be determined.
A new system has recently been put into operation, for which Techniplas used an existing MXW 1000 injection moulding machine from KraussMaffei as the basis. Techniplas had the MXW retrofitted at its manufacturer's main factory in Munich's Allach neighborhood.
Ensuring the manifold design is optimized for bioresin includes applying geometrically balanced channels so the melt traveling from the sprue bushing to every cavity, whether there are two or 96, experiences the same, if not similar, rheology profiles.
In processing, the pre-sealed bag is ideally opened and loaded directly into the dryer. The bag should not be left open for an excessive amount of time, and users shouldn’t drain the resin from the dryer after it has been dried and leave it out. Errors in drying and handling can have a particular impact on mechanical performance.
Take a deep dive into all of the various aspects of part quoting to ensure you’ve got all the bases—as in costs—covered before preparing your customer’s quote for services.
In this collection, which is part one of a series representing some of John’s finest work, we present you with five articles that we think you will refer to time and again as you look to solve problems, cut cycle times and improve the quality of the parts you mold.
While prices moved up for three of the five commodity resins, there was potential for a flat trajectory for the rest of the third quarter.
Here are processing guidelines aimed at both getting the PHA resin into the process without degrading it, and reducing residence time at melt temperatures.
Bioresin preparation includes drying to a moisture content of less than 250 parts per million (ppm) to prevent viscosity impacts and resin degradation. Bioresins are usually supplied in foil-lined bags or bags that are dried to less than 400 ppm in moisture. These resins should not be exposed to atmospheric conditions after drying.
Formnext Chicago is an industrial additive manufacturing expo taking place April 8-10, 2025 at McCormick Place in Chicago, Illinois. Formnext Chicago is the second in a series of Formnext events in the U.S. being produced by Mesago Messe Frankfurt, AMT – The Association For Manufacturing Technology, and Gardner Business Media (our publisher).
Remembering that the melt channel size and distance covered helps determine the shear rates, molders should consider and optimize these for low pressure, reduced shear and minimal residence time, bearing in mind that the smaller the channel, the higher the shear rate and the lower the residence time. The counterpoint to that setting profile is pressure drop. Molders need to ensure that for some specific bioresins, the channel is not too small and there isn’t too much pressure drop, which could prevent the parts from filling. Each manifold should be engineered specifically to the application and then balanced between pressure drop, shear rate and residence time requirements.
GETTING A QUOTE WITH LK-MOULD IS FREE AND SIMPLE.
FIND MORE OF OUR SERVICES:
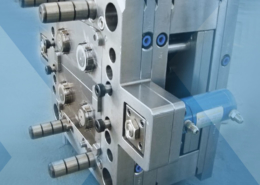
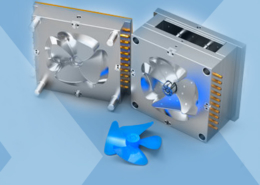
Plastic Molding

Rapid Prototyping
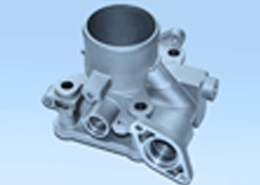
Pressure Die Casting
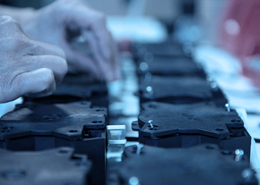
Parts Assembly
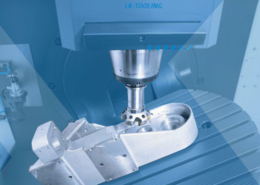