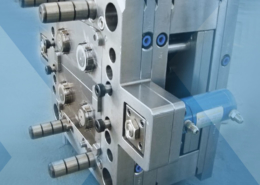
The Fascination of Double Shot Molding
Author:gly Date: 2024-06-08
Double shot molding, a captivating process in the realm of plastic injection molding, has garnered widespread attention for its unique capabilities and applications. This innovative technique involves injecting two different materials into a single mold, consecutively or simultaneously, to create a single, integrated component with distinct layers or colors. As the demand for intricate, multi-material products continues to rise across various industries, the significance of double shot molding becomes increasingly apparent.
Understanding Double Shot Molding
Introduction to the Process
Double shot molding, also known as two-shot molding or dual-shot molding, revolutionizes traditional injection molding by enabling the seamless integration of multiple materials or colors in a single manufacturing cycle. Unlike conventional methods that require secondary operations or assemblies to achieve similar results, double shot molding streamlines the production process, reduces costs, and enhances product aesthetics and functionality.
Key Components and Equipment
The success of double shot molding hinges upon precision-engineered molds, specialized injection molding machines equipped with multiple barrels or rotating platens, and advanced control systems. These components work in tandem to ensure precise material placement, temperature control, and cycle synchronization, thereby facilitating the seamless fusion of different materials into cohesive, high-quality parts.
Material Selection and Compatibility
One of the critical considerations in double shot molding is the selection of compatible materials with complementary properties, such as adhesion, thermal expansion, and shrinkage. By carefully choosing the appropriate resin formulations and optimizing processing parameters, manufacturers can mitigate potential challenges associated with material bonding, warpage, or delamination, thereby ensuring the structural integrity and durability of the final product.
Advantages and Applications
Enhanced Design Flexibility
Double shot molding offers unparalleled design freedom, allowing engineers to integrate multiple functionalities, textures, and colors within a single component. This versatility enables the creation of complex geometries, ergonomic features, and decorative elements that would be impractical or impossible to achieve using traditional manufacturing methods, thereby unlocking new opportunities for product innovation and differentiation.
Improved Product Performance
By combining materials with complementary properties, such as rigidity and elasticity or transparency and opacity, double shot molding enables the production of components with enhanced performance characteristics. For instance, automotive manufacturers leverage this technology to create weather-resistant exterior trims with soft-touch grips or transparent lenses with integrated sealing gaskets, thereby enhancing both aesthetics and functionality.
Streamlined Manufacturing Process
Double shot molding eliminates the need for secondary operations, such as painting, assembly, or bonding, thereby reducing production lead times, labor costs, and material waste. Moreover, by consolidating multiple components into a single integrated part, manufacturers can simplify supply chain logistics, minimize inventory management, and improve overall production efficiency, resulting in significant cost savings and competitive advantages.
Challenges and Considerations
Tooling Complexity and Cost
The design and fabrication of double shot molds entail greater complexity and precision compared to conventional molds, due to the need for intricate parting lines, gating systems, and cavity configurations. As a result, tooling costs and lead times may be higher, particularly for low-volume or custom applications, necessitating careful evaluation of the cost-benefit trade-offs and scalability considerations.
Material Compatibility and Processing Parameters
Achieving optimal material compatibility and adhesion poses a significant challenge in double shot molding, especially when combining dissimilar resins or additives with varying rheological properties. Fine-tuning processing parameters, such as injection pressures, temperatures, and cycle times, is essential to ensure proper material fusion, minimize defects, and maximize part quality and consistency.
Quality Assurance and Validation
Maintaining stringent quality standards and ensuring regulatory compliance are paramount in double shot molding, given the complexity of multi-material components and the potential for defects or inconsistencies. Robust process monitoring, inspection, and validation protocols, including dimensional analysis, visual inspection, and mechanical testing, are essential to detect and mitigate defects early in the production process, thereby minimizing scrap rates and customer returns.
Conclusion
In conclusion, double shot molding represents a groundbreaking advancement in plastic injection molding technology, offering unparalleled design flexibility, enhanced product performance, and streamlined manufacturing processes. By leveraging the unique capabilities of this innovative technique, manufacturers can unlock new opportunities for product differentiation, cost optimization, and market expansion across diverse industries. However, addressing the inherent challenges and complexities associated with material selection, tooling design, and quality assurance is essential to maximize the benefits of double shot molding and ensure long-term success in today's competitive marketplace. As the demand for multi-material components continues to grow, ongoing research and development efforts aimed at refining process capabilities, expanding material options, and improving quality control methodologies will be crucial for driving innovation and driving the adoption of double shot molding in the years to come.
GETTING A QUOTE WITH LK-MOULD IS FREE AND SIMPLE.
FIND MORE OF OUR SERVICES:
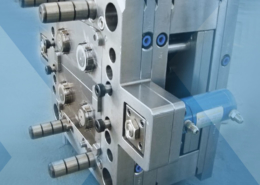
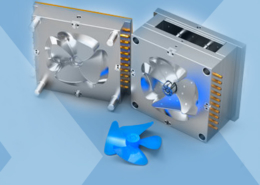
Plastic Molding

Rapid Prototyping
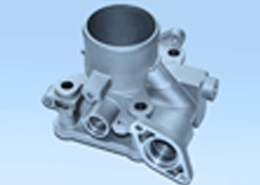
Pressure Die Casting
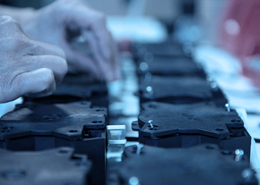
Parts Assembly
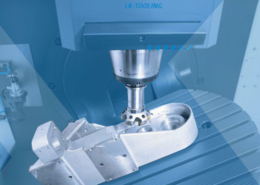